Punyo: A Leap Forward in Soft Robotics
Punyo: A Leap Forward in Soft Robotics
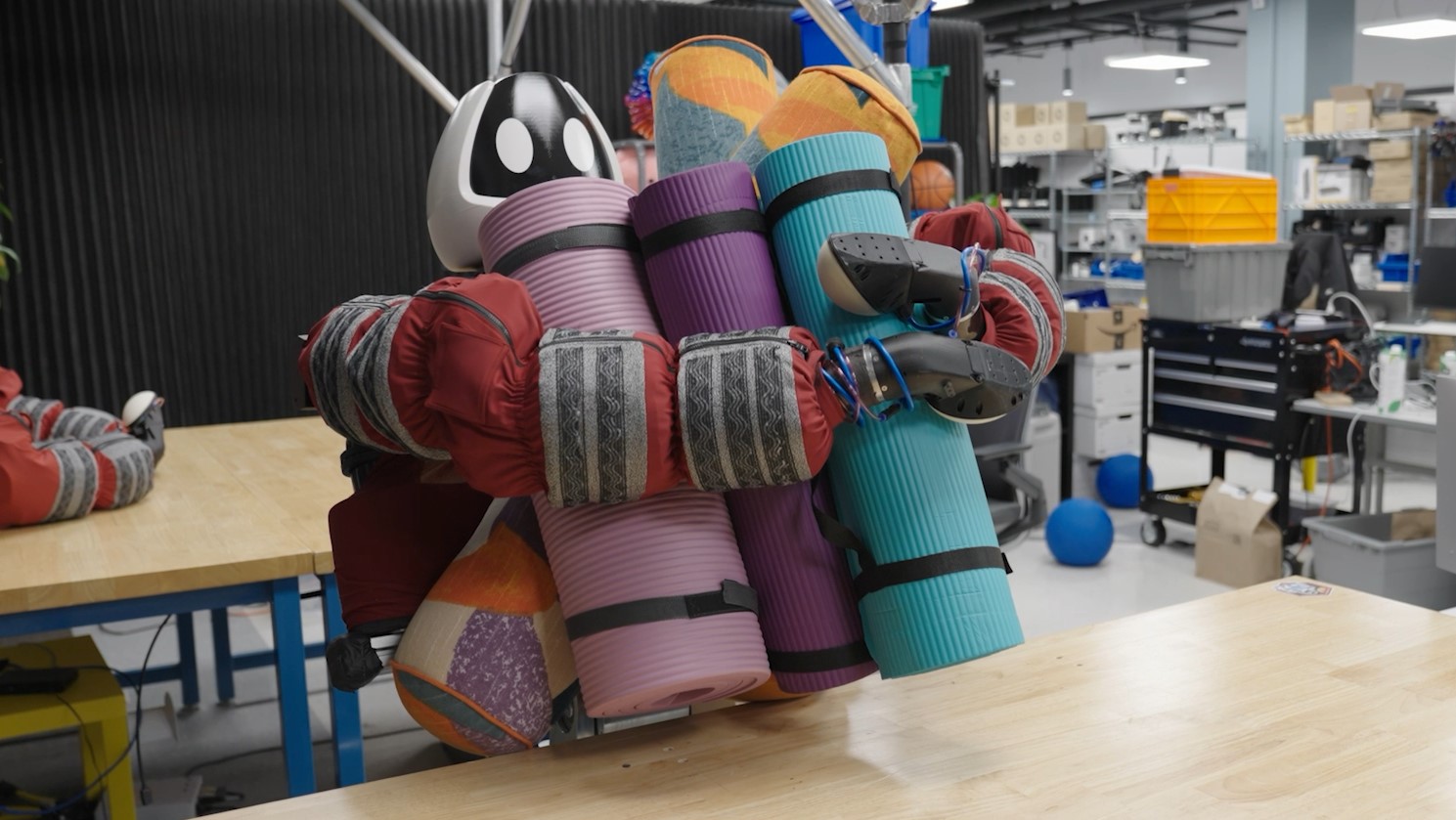
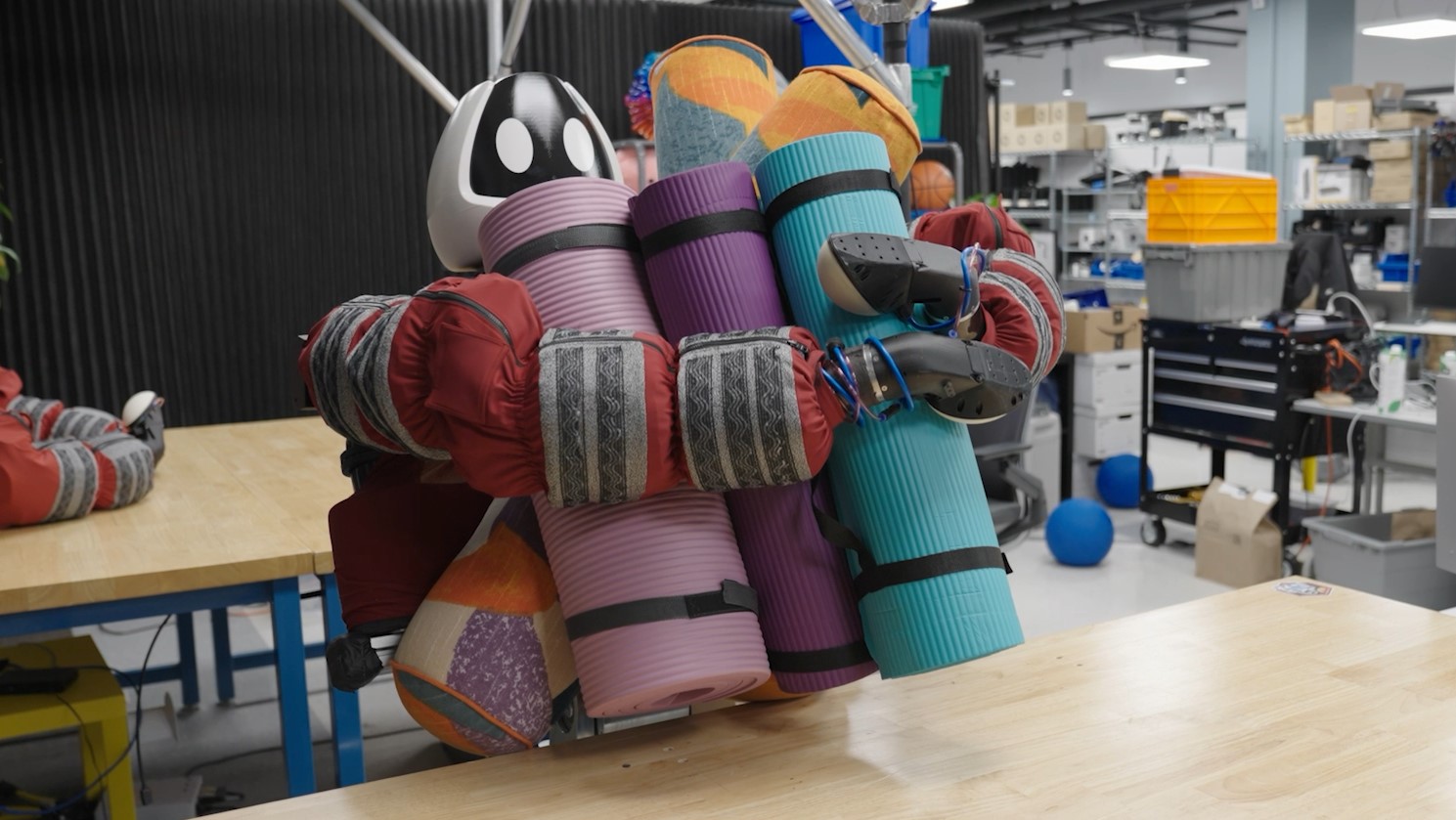
Toyota Research Institute’s Punyo soft robot is an innovation in whole-body manipulation research.
Soft robotics are developed from highly flexible materials, allowing for movements and actions that mimic biological systems more closely than traditional rigid robots.
Toyota Research Institute (TRI) has been at the forefront of this technology with its development of the soft robot, Punyo, which represents a leap forward in soft robotics by emphasizing safe interaction and efficient manipulation capabilities.
Unlike conventional robots, which rely on rigid components, Punyo utilizes soft, flexible materials that can adapt to the shape and contours of the objects it interacts with. This adaptability ensures a gentle touch, reducing the risk of damage to both the robot and the items it handles.
“We’re developing robotic capabilities that amplify rather than replace people and we’re on a mission to help with everyday tasks that require more than just our hands and fingertips,” said Alex Alspach, a tech lead with Toyota Research Institute’s Punyo Whole-Body Manipulation team in Cambridge, Mass. “Traditionally, robots for manipulation—think factory robots, or the arms of most humanoids we’ve seen lately—are intended to make contact only with their hands/grippers, and this is generally inefficient. Therefore, the surfaces of their arms are generally built with slick metal or plastic surfaces.”
More for You: From Minifig to Walking Mini-Robot
But this can lead to dangerous situations for some of these robots, should their arms accidentally contact an object or they can’t sense the item, he explained. And should these types of robots intentionally make contact or grasp a surface, forces are high at the rigid points of contact and their grasp would likely be unstable and slip due to the lack of friction.
Punyo does things differently by utilizing its whole body to carry and manipulate. “This allows it to do more than it could by grasping with only outstretched hands,” Alspach said. “It is a lightweight, low-cost solution to challenges faced by other designs. Its compliance, friction, and willingness to make a lot of contact result in stable grasps with evenly distributed forces and its tactile sensing allows these forces to be controlled and informative.”
But the systems TRI is developing can augment any traditional robot, transforming it into a soft, contact sensing robot arm, he added.
Punyo doesn’t have the same joints or arm lengths as a human, but its high-level structure (two arms, a chest, and a waist) and the use of its whole body’s worth of actuators and compliant surfaces to lift objects efficiently and capably are inspired by the way people put their bodies to use. This contrasts with traditional heavy lifting robots that require huge motors and gearboxes to lift objects at their grippers.
“It’s wise to take inspiration from the human build on this. We are strong enough to perform most everyday tasks with our hands, but when a big, heavy object comes around, we get creative with how we wrap our arms, position it against our body, lean back, lift with our legs, etc.” Alspach explained. “Unlocking a robot’s chest, arms, and other body surfaces for manipulation is mechanically advantageous. Coupled with compliance and friction, a robot can hold and manipulate large objects with less energy, increasing payload and battery life and enabling lighter, lower-cost systems.”
Become a Member: How to Join ASME
The development of soft robots like Punyo has broad implications for society. In healthcare, they could provide support to elderly or disabled individuals, enhancing their quality of life. In industrial settings, they could take on roles that are hazardous to humans, such as handling toxic substances or performing tasks in dangerous environments.
While Punyo is a research platform, its focus is on solving key problems that may lead to capable, general, interactive, and safe domestic robots. It’s suited for the home, but with its adaptable technologies it may augment robot manipulators in workplaces, factories, construction sites, and elsewhere.
The real world is full of complex environments full of clutter, tight spaces, moving people, and new objects. Robots cannot be programmed to have a perfect, canned method to deal with every unique task they will come up against, so they must be adaptive, reactive, and able to learn.
“With Punyo, we are developing hardware and algorithms that enable truly capable robots to help with large, heavy, and unwieldy items,” Alspach said. “Our team—who are experts in soft robotics, contact-rich planning and learning, tactile sensing, and human-robot interaction—are dedicated to a future where robots and people collaborate safely, productively, and happily side by side. Our latest achievements with Punyo are an important step in making this a reality.”
Jim Romeo is a technology writer in Chesapeake, Va.
Toyota Research Institute (TRI) has been at the forefront of this technology with its development of the soft robot, Punyo, which represents a leap forward in soft robotics by emphasizing safe interaction and efficient manipulation capabilities.
Unlike conventional robots, which rely on rigid components, Punyo utilizes soft, flexible materials that can adapt to the shape and contours of the objects it interacts with. This adaptability ensures a gentle touch, reducing the risk of damage to both the robot and the items it handles.
“We’re developing robotic capabilities that amplify rather than replace people and we’re on a mission to help with everyday tasks that require more than just our hands and fingertips,” said Alex Alspach, a tech lead with Toyota Research Institute’s Punyo Whole-Body Manipulation team in Cambridge, Mass. “Traditionally, robots for manipulation—think factory robots, or the arms of most humanoids we’ve seen lately—are intended to make contact only with their hands/grippers, and this is generally inefficient. Therefore, the surfaces of their arms are generally built with slick metal or plastic surfaces.”
More for You: From Minifig to Walking Mini-Robot
But this can lead to dangerous situations for some of these robots, should their arms accidentally contact an object or they can’t sense the item, he explained. And should these types of robots intentionally make contact or grasp a surface, forces are high at the rigid points of contact and their grasp would likely be unstable and slip due to the lack of friction.
Punyo does things differently by utilizing its whole body to carry and manipulate. “This allows it to do more than it could by grasping with only outstretched hands,” Alspach said. “It is a lightweight, low-cost solution to challenges faced by other designs. Its compliance, friction, and willingness to make a lot of contact result in stable grasps with evenly distributed forces and its tactile sensing allows these forces to be controlled and informative.”
But the systems TRI is developing can augment any traditional robot, transforming it into a soft, contact sensing robot arm, he added.
Punyo doesn’t have the same joints or arm lengths as a human, but its high-level structure (two arms, a chest, and a waist) and the use of its whole body’s worth of actuators and compliant surfaces to lift objects efficiently and capably are inspired by the way people put their bodies to use. This contrasts with traditional heavy lifting robots that require huge motors and gearboxes to lift objects at their grippers.
“It’s wise to take inspiration from the human build on this. We are strong enough to perform most everyday tasks with our hands, but when a big, heavy object comes around, we get creative with how we wrap our arms, position it against our body, lean back, lift with our legs, etc.” Alspach explained. “Unlocking a robot’s chest, arms, and other body surfaces for manipulation is mechanically advantageous. Coupled with compliance and friction, a robot can hold and manipulate large objects with less energy, increasing payload and battery life and enabling lighter, lower-cost systems.”
Become a Member: How to Join ASME
The development of soft robots like Punyo has broad implications for society. In healthcare, they could provide support to elderly or disabled individuals, enhancing their quality of life. In industrial settings, they could take on roles that are hazardous to humans, such as handling toxic substances or performing tasks in dangerous environments.
While Punyo is a research platform, its focus is on solving key problems that may lead to capable, general, interactive, and safe domestic robots. It’s suited for the home, but with its adaptable technologies it may augment robot manipulators in workplaces, factories, construction sites, and elsewhere.
The real world is full of complex environments full of clutter, tight spaces, moving people, and new objects. Robots cannot be programmed to have a perfect, canned method to deal with every unique task they will come up against, so they must be adaptive, reactive, and able to learn.
“With Punyo, we are developing hardware and algorithms that enable truly capable robots to help with large, heavy, and unwieldy items,” Alspach said. “Our team—who are experts in soft robotics, contact-rich planning and learning, tactile sensing, and human-robot interaction—are dedicated to a future where robots and people collaborate safely, productively, and happily side by side. Our latest achievements with Punyo are an important step in making this a reality.”
Jim Romeo is a technology writer in Chesapeake, Va.