Six-Armed Robot Stickbug Works as a Precision Pollinator
Six-Armed Robot Stickbug Works as a Precision Pollinator
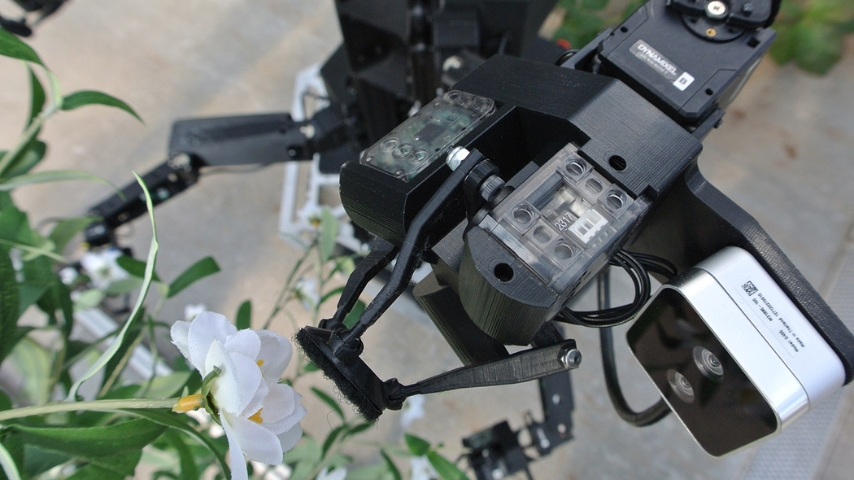
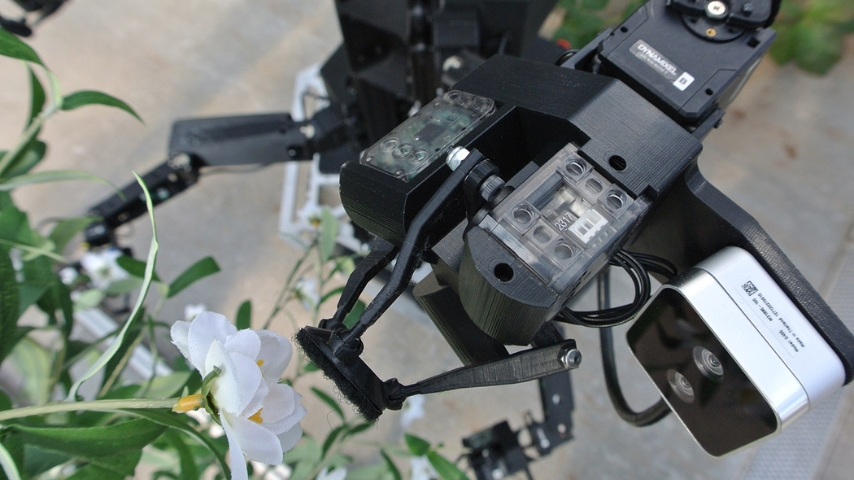
With six arms, a Kiwi drive, and custom detectors designed for contact-based pollination, the precision Stickbug reaches flowers growing above the greenhouse floor while navigating narrow plant rows.
With the ability to navigate narrow rows and reach up to plants extending several feet above workers’ heads, West Virgina University (WVU) researchers introduce the newest iteration of their precision pollinator. This impressive “Stickbug” robot plies six arms, employs a Kiwi drive, and uses custom detectors and classifiers allowing it to use its precision, felt-tipped end-effector for contact-based pollination.
“This is a precision pollinator robot that we hope will help offset the effects of a decreasing population of natural pollinators,” explained Yu Gu professor, Department of Mechanical and Aerospace Engineering at WVU in Morgantown, W.Va. In its paper “Design of Stickbug: a Six-Armed Precision Pollination Robot,” the team of scientists point toward evidence of a shrinking population of diverse wild natural pollinators as motivation for the system. It hopes that the robot will not only work as a pollinator but give the industry the added capability of global flower mapping that will eventually help predict fruit production and improve health monitoring of crops.
Gu’s passion of improving robots’ ability to function in increasingly complex environments and situations is a natural for this work. Humans can work alongside natural pollinators, for example, and manipulate the flora of brambles (blackberries and raspberries). But the flowers are abundant on the plant and form in tight clusters making hand pollination “very time-consuming and impractical,” Gu said.
The flowers of brambles are individually different and the challenge that the robot must overcome—using vision algorithms that can properly recognize them and associate them—is not a trivial problem. Its earlier system—Bramblebee—used mapping, visual perception, path planning, motion control, and manipulation techniques to pollinate efficiently. The latest robot builds on that 2018 version and can now attempt over 1.5 pollinations per minute with a 50 percent success rate. It is working on getter quicker than human pollinators and more precise than Bramblebee.
The current iteration of the robot works in and around its mapped environment. It has many degrees of freedom with multiple joints. It can recognize certain plant flora and “knows how to move its arm towards those flowers,” Gu said.
“We are trying to build a fully autonomous system,” he explained. The current multi-agent approach is made up of arms that are each standalone and able to function separately. The drive base is also a separate agent, Gu explained. The overall system is made of several sub-robots, each with its own sensors and decision-making abilities.
Discover the Benefits of ASME Membership
Unlike natural pollinators, which inherently have a preference for specific plant flora, the robotic pollinators will be able to accommodate different environments and tasks. Moreover, they can work in indoor agriculture, such as greenhouses, and eventually they will be able to accomplish other gardening responsibilities such as flower thinning and gathering critical crop data.
While many love to talk about what his Stickbug robot is capable of, most notably pollinating continually, without having to stop for breaks, Gu wanted to make sure people understood that he can easily tell you what it cannot do. “It cannot produce honey,” Gu explained, with a smile. He emphasized that the robot is set up to “help” not “replace” the current wild pollinators and a human workforce by working in environments not suitable for natural pollinators.
The robot has a good memory, Gu explained. Stickbug can roughly remember which flowers are where and collects a lot of information on individual flora. The robot is set up to work well in controlled environments with specific plants. “Many plants rely on insects, because they are the type of plant that need physical manipulation,” he said. “We look at those crops that rely on contact-based pollination.”
What’s the biggest challenges to getting Stickbug out there on the floor of greenhouses across the United States? “We have a bunch of obstacles,” Gu admitted. One of the most difficult is how delicate plants and their flowers are and the gentle operation of spreading pollen. The operation is challenging even for human pollinators.
“And even when we do get the system working, we have to think about if it is efficient and effective,” he said. And cost is an important consideration. “This second-generation pollinator is being made with a focus on making a low-cost system.”
More for You: Why Animals Are Still Faster Than Robots
And Gu makes the point that an affordable robot that is effective and reliable, still needs to be used correctly by end-users and acceptable to industry workers and buyers. “Growers will need to work alongside a machine,” he explained. “And that is a barrier that we need to think about.” In fact, human-robot interaction is a part of the team’s work.
And will growers of the future work increasingly in greenhouses, high tunnels, and vertical indoor hydroponic farms? “The future is hard to predict,” Gu admitted. And added that the robot will provide a supplementary capability no matter what direction the industry decides to go.
Gu describes his work as a possible “Plan B.” In case this current trend of insect shortage continues, and the world does not have enough insects for outdoor pollination, “we would need some solutions in our pocket,” he concluded.
Cathy Cecere is membership content program manager.
“This is a precision pollinator robot that we hope will help offset the effects of a decreasing population of natural pollinators,” explained Yu Gu professor, Department of Mechanical and Aerospace Engineering at WVU in Morgantown, W.Va. In its paper “Design of Stickbug: a Six-Armed Precision Pollination Robot,” the team of scientists point toward evidence of a shrinking population of diverse wild natural pollinators as motivation for the system. It hopes that the robot will not only work as a pollinator but give the industry the added capability of global flower mapping that will eventually help predict fruit production and improve health monitoring of crops.
Gu’s passion of improving robots’ ability to function in increasingly complex environments and situations is a natural for this work. Humans can work alongside natural pollinators, for example, and manipulate the flora of brambles (blackberries and raspberries). But the flowers are abundant on the plant and form in tight clusters making hand pollination “very time-consuming and impractical,” Gu said.
The flowers of brambles are individually different and the challenge that the robot must overcome—using vision algorithms that can properly recognize them and associate them—is not a trivial problem. Its earlier system—Bramblebee—used mapping, visual perception, path planning, motion control, and manipulation techniques to pollinate efficiently. The latest robot builds on that 2018 version and can now attempt over 1.5 pollinations per minute with a 50 percent success rate. It is working on getter quicker than human pollinators and more precise than Bramblebee.
Autonomous pollination
The current iteration of the robot works in and around its mapped environment. It has many degrees of freedom with multiple joints. It can recognize certain plant flora and “knows how to move its arm towards those flowers,” Gu said.
“We are trying to build a fully autonomous system,” he explained. The current multi-agent approach is made up of arms that are each standalone and able to function separately. The drive base is also a separate agent, Gu explained. The overall system is made of several sub-robots, each with its own sensors and decision-making abilities.
Discover the Benefits of ASME Membership
Unlike natural pollinators, which inherently have a preference for specific plant flora, the robotic pollinators will be able to accommodate different environments and tasks. Moreover, they can work in indoor agriculture, such as greenhouses, and eventually they will be able to accomplish other gardening responsibilities such as flower thinning and gathering critical crop data.
While many love to talk about what his Stickbug robot is capable of, most notably pollinating continually, without having to stop for breaks, Gu wanted to make sure people understood that he can easily tell you what it cannot do. “It cannot produce honey,” Gu explained, with a smile. He emphasized that the robot is set up to “help” not “replace” the current wild pollinators and a human workforce by working in environments not suitable for natural pollinators.
The robot has a good memory, Gu explained. Stickbug can roughly remember which flowers are where and collects a lot of information on individual flora. The robot is set up to work well in controlled environments with specific plants. “Many plants rely on insects, because they are the type of plant that need physical manipulation,” he said. “We look at those crops that rely on contact-based pollination.”
Commercialization
What’s the biggest challenges to getting Stickbug out there on the floor of greenhouses across the United States? “We have a bunch of obstacles,” Gu admitted. One of the most difficult is how delicate plants and their flowers are and the gentle operation of spreading pollen. The operation is challenging even for human pollinators.
“And even when we do get the system working, we have to think about if it is efficient and effective,” he said. And cost is an important consideration. “This second-generation pollinator is being made with a focus on making a low-cost system.”
More for You: Why Animals Are Still Faster Than Robots
And Gu makes the point that an affordable robot that is effective and reliable, still needs to be used correctly by end-users and acceptable to industry workers and buyers. “Growers will need to work alongside a machine,” he explained. “And that is a barrier that we need to think about.” In fact, human-robot interaction is a part of the team’s work.
And will growers of the future work increasingly in greenhouses, high tunnels, and vertical indoor hydroponic farms? “The future is hard to predict,” Gu admitted. And added that the robot will provide a supplementary capability no matter what direction the industry decides to go.
Gu describes his work as a possible “Plan B.” In case this current trend of insect shortage continues, and the world does not have enough insects for outdoor pollination, “we would need some solutions in our pocket,” he concluded.
Cathy Cecere is membership content program manager.