International Gas Turbine Institute (IGTI)
Dedicated to supporting the international exchange and development of information to improve the design, application, manufacture, operation and maintenance, and environmental impact of all types of gas turbines, turbomachinery and related equipment.
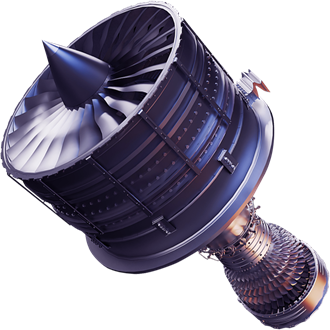
Executive Committee
Caroline Marchmont, Chair
Ansaldo Energia
Douglas Hofer, Past Chair
Southwest Research Institute
Jacqueline O'Connor, Vice-Chair, Operations Department
The Pennsylvania State University
Sina Stapelfeldt, Vice-Chair, Professional Development Department
Imperial College London
Susan Scofield, Vice-Chair, Strategy Department
Siemens-Energy
Extended Leadership Team
Ricardo Martinez-Botas, Turbo Expo Committee Head (Operations Department)
Imperial College London
Jaroslaw Szwedowicz, Associated Events Committee Head (Operations Department)
Siemens Energy AG
Liping Wang, Technical Committees Head (Operations Department)
GE Aerospace
Richard Dennis, Finance & Performance Committee Head (Operations Department)
Retired
Vassilios Pachidis, Peer Review & Publications Committee Head, Operations Deparment)
Cranfield University
Doug Nagy, Honors and Awards Committee Head (Professional Engagement Department)
Retired
Cis De Maesschalck, Marketing & Technical Communications Committee Head (Professional Engagement Department)
Rolls Royce
Dimitra Eirini Diamantidou, Early Career Committee Head (Professional Engagement Department)
MTU Aero Engines
Mike Koenig, Professional Development Committee Head (Professional Engagement Department)
Siemens-Energy
Richard Sandberg, ASME Outreach Committee Head (Strategy Department)
University of Melbourne
Natalie Smith, IGTI Outreach Committee Head (Strategy Department)
Southwest Research Institute
Peter Stuttaford, External Outreach Committee Head (Strategy Department)
Thomassen Energy
Laura Herrera, Senior TEC Operations Manager
ASME
The IGTI Division Executive Committee is structured into three departments dedicated to serving the gas turbine community. These departments encompass in total twelve committees that cover all aspects of the division's activities.
OPERATIONS DEPARTMENT The Operations Department delivers networking opportunities and disseminates knowledge through Turbo Expo and associated events. It drives technical excellence through support of the technical committees and maintaining high standards in all publications through the peer review processes while ensuring financial goals are achieved in all IGTI departments.
PROFESSIONAL ENGAGEMENT DEPARTMENT The Professional Engagement Department strives to create and serve a thriving global community of gas turbine professionals and enthusiasts. It is committed to attracting and maintaining a diverse membership, to engaging and developing members through all stages of their careers, and to recognising technical excellence and outstanding contributions to the community.
STRATEGY DEPARTMENT The Outreach Department identifies and develops strategic topics that are not yet in an operational format within IGTI. This team works to curate and prototype next generation concepts based on what is needed or anticipated in our Technical Community. Ideation is done through connecting and working with critical networks within IGTI, other ASME Groups, government agencies and international think tanks.
The IGTI's vision is to be the world's leader and champion of innovative gas turbines and related energy systems to power a sustainable way of life.
Global Gas Turbine News
The Global Gas Turbine News (GGTN) is published quarterly inside ASME's Mechanical Engineering magazine. The GGTN provides technical content as well as updates on industry and ASME IGTI events.
If you are an ASME member, you automatically receive Mechanical Engineering as part of your membership. For single-issue reprints of Mechanical Engineering or to subscribe, call 1-800-THE ASME.
GGTN issues:
April 2025 / May 2025
December 2024 / January 2025
August 2024 / September 2024
April 2024 / May 2024
December 2023 / January 2024
August 2023 / September 2023
April 2023 / May 2023
December 2022 / January 2023
August 2022 / September 2022
April 2022 / May 2022
December 2021 / January 2022
October 2021 / November 2021
April 2021 / May 2021
February 2021 / March 2021
December 2020 / January 2021
September 2020
May 2020
March 2020
December 2019
Please email ahmedh@asme.org if interested in an older issue.
Meet the GGTN Editorial Committee
Tamy Guimarães
Assistant Professor of Mechanical Engineering
The Pennsylvania State University
Chair
Lorenzo Mazzei, PhD
R&D Programs Manager
Ergon Research, Italy
Member
Uma Maheshwar
Chief Consulting Engineer
GE Aerospace Engineering-India
Member
Lee S. Langston
Professor Emeritus
University of Connecticut
Member
Angela Serra
Senior Technical Emissions Advisor
Baker Hughes
Member
Keun Ryu
Associate Professor
Hanyang University, South Korea
Member
Lance L. Smith
Senior Technical Fellow
RTS Technology Research Center (RTRC)
Member
Manfred Klein
Energy Consultant
MA Klein & Assoc.
Member
Hafsa Ahmed
Coordinator, Conferences & Exhibitions
ASME
IGTI Liaison
A special thanks to previous members for their time and dedication:
Jeffrey M. Cohen
RTX Technology Research Center
Anton Streit
Siemens Energy
Cis De Maesschalck, PhD
Rolls-Royce plc
James D. Heidmann, PhD
NASA Glenn Research Center
About
The International Gas Turbine Institute (IGTI) is a Group of The American Society of Mechanical Engineers (ASME) under the ASME Gas Turbine Technology Group. ASME helps the global engineering community develop solutions to real world challenges. Founded in 1880, ASME is a not-for-profit professional organization that enables collaboration, knowledge sharing and skill development across all engineering disciplines, while promoting the vital role of the engineer in society. ASME codes and standards, publications, conferences, continuing education and professional development programs provide a foundation for advancing technical knowledge and a safer world.
IGTI's Mission Statement
To advance safe, clean, reliable, and affordable gas turbine and related energy system technologies by:
Building a diverse global technical community for knowledge sharing and collaboration.
Inspiring and developing engineers, scientists, and technologists.
Promoting innovation and thought leadership across academia, government, and industry.
IGTI Vision Statement
To be the world’s leader and champion of innovative gas turbines and related energy systems to power a sustainable way of life..
Membership
The International Gas Turbine Institute has no formal individual or corporate members. Individuals interested in participating in the International Gas Turbine Institute should become members of ASME. Upon joining ASME, new members are asked to select specific areas of interest. Upon selection of gas turbines (technical interest #22), new ASME members will regularly receive the Global Gas Turbine News, the official newsletter of IGTI, as well as regular mailings from both IGTI and ASME, and are eligible for a discounted subscription to either the Journal of Engineering for Gas Turbines and Power or the Journal of Turbomachinery.
ASME membership qualifies individuals for substantial cost discounts on both IGTI and ASME programs and products.
ASME IGTI Committees
The heart of the ASME International Gas Turbine Institute is its highly successful committee structure. ASME IGTI's Committees provide regular ongoing forums for program development and technical exchange, addressing all areas of technical expertise related to gas turbines, turbomachinery and related equipment.
The Committees organize the high quality paper and panel sessions for the annual conferences sponsored by ASME IGTI. Committee members consist of leading engineers in close contact with the latest developments in turbomachinery equipment, improvements in techniques, and introductions of new practices. They bring such developments to the annual ASME TURBO EXPO where these activities may be reported, discussed freely, and their benefits shared by the entire turbomachinery community.
Over 30 countries are represented by the Committee membership, derived from academic, government, and industrial affiliations.
All ASME IGTI Committees support their individual missions with the following activities:
- Monitoring current issues and trends in gas turbines, turbomachinery, and related equipment, and organizing related sessions for the TURBO EXPO or other related programs. Committee members assist in this process by suggesting session topics, presenting papers, participating on panel discussions, and acting as Session Chair or Vice Chair.
- Supporting the ASME IGTI Review process, which assures quality peer reviewed published paper presentations. Committee members assist in this by coordinating peer reviews according to the ASME IGTI guidelines, communicating needed revisions to the author, reviewing papers, and assisting the Journal editors.
- Encouraging cooperation with other professional societies who share common interests. ASME has cooperative agreements with many engineering societies throughout the world. Although ASME membership is not required to join an ASME IGTI Committee, it is recommended. ASME membership is required to serve as Committee Chair or Vice Chair.
- Actively working to expand the membership to maintain the breadth and depth of experience necessary to address the Committee's focused area of interest. The most valued benefit of being an active Committee member is the opportunity to interact with an international membership of leading professionals in the turbomachinery industry.
- Recognizing technical accomplishments by nominating papers for ASME and Committee awards. Several highly-respected awards are presented annually at the ASME TURBO EXPO.
If you are interested in becoming involved in one or more of the Committees, simply contact the related Chair. The Committees differ slightly in their membership requirements, but in most cases it would be helpful to provide a letter of interest, a resume, and (if appropriate) a letter of support from your employer. Attend a Committee meeting. Committee meetings are open to all interested persons. Each Committee differs on the frequency and location of their meetings. However, all of the Committees meet at the annual ASME TURBO EXPO.
- Aircraft Engine Committee
- Ceramics Committee
- Coal, Biomass & Alternative Fuels Committee
- Combustion, Fuels & Emissions Committee
- Controls, Diagnostics & Instrumentation Committee
- Cycle Innovations Committee
- Education Committee
- Electric Power Committee
- Energy Storage
- Fans and Blowers Committee
- Heat Transfer Committee
- Industrial & Cogeneration Committee
- Manufacturing Materials & Metallurgy Committee
- Microturbines, Turbochargers & Small Turbomachines Committee
- Oil & Gas Applications Committee
- Steam Turbine Committee
- Structures & Dynamics Committee
- Student Advisory Committee
- Supercritical CO2 Committee
- Turbomachinery Committee
- Wind Energy Committee
Honors & Awards
- The ASME R. Tom Sawyer Award
- The ASME Gas Turbine Award
- The ASME IGTI Scholar Award
- The ASME IGTI John P. Davis Award
- The ASME IGTI Aircraft Engine Technology Award
- The ASME IGTI Industrial Gas Turbine Technology Award
- ASME IGTI Dilip R. Ballal Early Career Award
- ASME IGTI Committee Best Paper Awards
- Turbo Expo Early Career Engineer Travel Award
- ASME IGTI Student Scholarship Program
- The ASME IGTI Student Advisory Committee Travel Award
IGTI Division Events
ASME 2025 Turbo Expo Conference
June 16 – 20, 2025
Renasant Convention Center
Memphis, Tennessee USA
The technical program and exhibits will be held at the Renasant Convention Convention Center
Past Events
ASME 2024 Turbo Expo ConferenceJune 24 - 28, 2024
ExCeL London
London, England
ASME 2023 Turbo Expo Conference
June 26 – 30, 2023
Hynes Convention Center
Boston, Massachusetts, USA
ASME 2021 AMRGT Symposium (Advanced Manufacturing & Repair for Gas Turbines)
Virtual Event: October 5 – 8, 2021
Presentation Abstract Submission Deadline Date: May 25, 2021
ASME 2021 Gas Turbine India Conference
Virtual Event: December 2 – 3, 2021
Abstract Submission Deadline Date: May 10, 2021
Journals
GT Journals Promote Exchange of Technical Knowledge
The Journal of Turbomachinery and the Journal of Engineering for Gas Turbines and Power are the ASME quarterly publications focused on disseminating gas turbine technical information of permanent interest.
The Journal of Turbomachinery publishes the best technical papers worldwide that further the technology of turbomachinery related to gas turbine engines. Subject matter scope includes the fluid dynamics and heat transfer aspects of turbomachine design and performance advancement.
Covering a broad spectrum of practical topics of interest to the gas turbine and power industry, the Journal of Engineering for Gas Turbines and Power presents archival quality research in stationary, vehicular, and aircraft power systems applications.
Please click here if you are interested in submitting your work for publication in one of these journals.
Webinars: Technical
Open to everyone-students, professionals, and enthusiasts alike-these webinars bring together leading industry experts and distinguished academics to share valuable insights into the latest advancements and real-world
applications in the field of turbomachinery. Each seminar is structured in an engaging one-hour format, featuring a 40-minute in-depth technical presentation followed by a 20-minute interactive Q&A session, providing participants with the opportunity to actively engage, ask questions, and exchange ideas.
The series will cover a broad spectrum of critical and emerging topics, including combustion, turbomachinery performance optimization, artificial intelligence and machine learning (AI/ML) applications, computational fluid dynamics (CFD), and more.
Registration is complimentary and open to all. Do not miss this opportunity. Register today to attend these inspiring talks!
Webinars On Demand
Astrid Walle
Siemens-Energy
As CFD advances through the development of new methods, high-performance computing (HPC), and multidisciplinary approaches, the integration of AI and ML is paving the way for innovative solutions and enhanced efficiencies. We will explore various methodologies for applying ML in CFD applications, including design, surrogate modeling, and geometric deep learning.
We will discuss the requirements for successful implementation, emphasizing the importance of automated process chains, data models, and data management strategies.
Astrid Walle
Astrid is a mechanical engineer with a PhD in CFD and more than a decade of experience in applied fluid mechanics. She has held several positions in gas turbine R&D and AI development at Siemens Energy, Vattenfall and Rolls Royce. Following her professional determination to bring AI and Data Science into engineering she ran her own business and worked as a Product Manager in a software startup before she rejoined Siemens Energy to establish the usage of data from the very beginning in product development.
Complimentary Webinar: Turbomachinery CFD: Perspectives on Interactions
Prof. L. He
Statutory Chair of Computational Aerothermal Engineering
Department of Engineering Science
University of Oxford
Computational fluid dynamics has become indispensable to modern turbomachinery development. Challenges (& opportunities) in turbomachinery CFD arise in a multi-physics multi-components interactive environment for aerodynamic performance, machine durability and structural integrity. A primary issue of interest is: How can we identify, predict and understand relevant interactions to influence turbomachinery designs? A perhaps less-often asked question may be: if and how can we leverage distinctive turbomachinery characteristics in Turbomachinery-CFD method development (e.g. achieving the same modelling fidelity & solution accuracy at a much faster speed to accelerate design iterations)?
This webinar will start with a brief overview of some fundamentals and major past milestones. We will then look at a few aero-thermal-dynamic interaction case examples of our previous research efforts on:
- Bladerow/stage interaction
- Shape design-Flow control interaction
- Aerodynamics-Aeroelasticity interaction
- Aerodynamics-Heat transfer/Cooling interaction
Prof. Li He (Ph.D. Cambridge, 1990) holds the Statutory Chair of Computational Aerothermal Engineering at Oxford University. He had been the head of Osney Laboratory (now known as 'Oxford Thermofluids Institute'), the acting director of the Rolls-Royce University Technology Centre (UTC) in Heat Transfer, and the Oxford Codirector of UK EPSRC Center of Doctoral Training (CDT) in Gas Turbine Aerodynamics. Professor He's research interest is primarily in CFD methods development & application for multi-physics and multi-component interactive turbomachinery design and analysis. Having served as an associate editor for ASME Journal of Turbomachinery, a guest editor for Applied Thermal Engineering and International Journal fo CFD, he is an associate editor for Aeronautical Journal and the Editor-in-Chief for Journal of GPPS. Professor He is Fellow ASME, Fellow of Roya Aeronautical Society (FRAeS), and Chartered Engineer (CEng).
Complimentary Webinar: The Role of Hydrogen Combustion in Decarbonizing Future Civil Aviation
Dr. Xiaoxiao Sun
Lecturer
Cranfield University
Hydrogen is now considered one of the ultimate solutions for decarbonizing the aviation industry. Without radical changes to gas turbine engines, emission targets can be achieved by burning hydrogen smartly in the combustion chamber. Hydrogen combustion research is of particular interest, as the very different thermochemical properties of hydrogen lead to distinct combustion characteristics, presenting both challenges and opportunities for applying new energy-efficient and low-emissions technologies.
This webinar will provide detailed insights into the current progress in gas turbine hydrogen combustion research, as well as a roadmap for maturing hydrogen combustion technologies and integrating them into aircraft.
Complimentary Webinar: Combustors for Future Energy and Propulsion Needs
Tim Lieuwen
Regents' Professor and Executive Director, Strategic Energy Institute
Georgia Institute of Technology
Global energy and propulsion systems are evolving rapidly with the push towards decarbonization. Within these evolving systems, the role of gas turbines to meet societal energy, reliability, and propulsion needs are evolving significantly in some ways, and staying the same in others. The combustor is a critical component in the gas turbine, which serves as the ultimate source of energy for the cycle, the source of its emissions, and that influences overall system operational boundaries and performance. The purpose of this talk is to provide a tutorial review of combustion science and technology, explain current R&D needs, and discuss the role of combustion systems in a decarbonizing society.
Complimentary Webinar: Application of Machine Learning to Turbomachinery Design
Dr. Akin Keskin
Vice President for Digital in Business Aviation
Rolls Royce
Dr. Ricardo Paiva
Specialist, Development Engineering Software
Rolls Royce
The latest developments in the world of machine learning and AI have brought about incredible opportunities for synergy with the simulation world. Various developments have been made in terms of applying these techniques to develop better products at a faster pace. From classical statistics-based models to deep neural networks, this lecture will give a flavour of applications of automated model creation for the purposes of turbomachinery design.
Dr. Akin Keskin
Akin is an experienced engineer and senior manager in the field of Simulation and Modelling with a degree in Aerospace Engineering and a doctoral degree in Mechanical Engineering. He joined Rolls-Royce in 2001 and has since led various research and capability development projects. In 2015 he was appointed to the Rolls-Royce Engineering Fellowship to drive the development of Design Systems and Methodologies. Currently he is the Vice President for Digital in Business Aviation and responsible for the digital strategy across engineering and services. Akin is an active member of the AIAA and ASME with more than 50 publications, is regular keynote speaker and panellist at various international conferences and workshops, and a member of the IGTI Executive Committee.
Dr. Ricardo Paiva
Ricardo is an Aerospace Engineer by training and through his doctoral research focused on the development of numerical methods and optimisation strategies in the engineering simulation world. Having worked for Rolls-Royce since 2011 he took on various roles from component designer to software developer, always with the underlying goal of simplifying design processes through code, be it via leveraging automation techniques and/or machine learning algorithms. At the moment, he serves as a specialist in the development of Rolls-Royce engineering software used to predict “time on wing” (life) for aircraft engines.
Complimentary Webinar! Register Today!
Demetrios Lefas, PH.D.
University of Cambridge
Nature of Transonic Compressor Flow and its Design Implications
A key problem in transonic compressor and fan design is that although a 3D description of the flow is necessary to correctly capture the shock, accounting for it during the sectional detailed design is difficult because the key driving design parameters are still poorly understood. In this webinar, it is shown that for inlet relative Mach numbers between 0.85 to 1.20, the pressure rise across the shock is purely a function of the 3D streamtube area at the throat at over the inlet area A1. This finding is based on three key transonic flow features, discussed in detail within this seminar, being present together across a wide range of more than 2000 representative transonic compressor and fan designs published online (https://whittle.digital/).
The second half of the webinar discusses the implications of this newfound clarity to practical transonic rotor design. First, it outlines the important preliminary geometric design parameters set prior to the detailed design phase and then describes a simple and efficient physics-based method for designing optimal transonic multistage compressor rotors. The key to this novel method is that the spanwise variation of At /A1, is extracted directly from the 3D CFD. The spanwise distribution of the area ratio is then adjusted iteratively to 'aerodynamically balance' the shock structure across the blade span.
This simplified design process will be shown, through representative rotor redesign examples, to achieve highly satisfactory results whilst providing a physically intuitive way of understanding how the design was improved. Hence, it is of great practical utility and valuable learning for any compressor or fan designer.
Complimentary On-Demand Webinar
Exploring Additive Manufacturing for Advancing Turbine Cooling, Dr. Karen A. Thole
Commercial aviation is responsible for between 2.0 and 2.5 percent of the total global CO2 emissions of which 90 percent comes from large single-aisle and twin-aisle aircraft. With the exception of fully electric, the majority of the future aviation propulsion systems will use a gas turbine as the power plant. In response to the International Civil Aviation Organization’s pledge to support an aspirational net zero aviation goal by 2050, the pace at which gas turbines are developed must hasten. While increasing turbine efficiencies is key to reducing carbon emissions, this must be balanced with component life, which is set by operational temperatures. Recent advances in the field of additive manufacturing (AM) have opened up possibilities to evaluate new features for cooling turbine airfoils with a much more rapid turnaround relative to conventional casting. The opportunity is to exploit the use of additive manufacturing in re-thinking cooling schemes for components while considering the inherent effects of the metal additive process. This talk will also provide insights on various challenges associated with additively manufacturing components.
Dr. Karen A. Thole is a Distinguished Professor in the Department of Mechanical Engineering at The Pennsylvania State University. Dr. Thole’s expertise is heat transfer, additive manufacturing, and instrumentation development. She directs the Steady Thermal Aero Research (START) Lab where experimental and computational studies are conducted to advance aviation sustainability and power generation through highly efficient turbines. She is a Fellow of ASME, AIAA and the Royal Aeronautical Society. She has been a member of several National Academy of Engineering studies; has served on NASA advisory committees; and is a member of the Department of Air Force Scientific Advisory Board. Her work has been recognized by ASME’s R. Tom Sawyer, George Westinghouse Gold, Edwin F. Church and Heat Transfer Memorial Awards. From AIAA, she has been awarded AIAA’s Air Breathing Propulsion and Thermophysics Awards. Dr. Thole received her BSME and MSME from the University of Illinois and her PhD from the University of Texas.
Complimentary On-Demand Webinar
Accelerating Turbomachinery Design: The Role of High-Fidelity Simulation and Machine Learning, by Richard Sandberg
To accelerate the deployment of cleaner energy and propulsion technologies, their development time and costs need to be considerably reduced. A key enabler for this is stronger reliance on computational fluid dynamics (CFD) for the design of turbomachinery components because CFD predictions with sufficient reliability can reduce the number of costly and time-consuming laboratory experiments and test campaigns. First-principles based simulations are most accurate and have the potential to elucidate mechanisms that can be exploited for further efficiency gains. Their excessive computational cost, however, preclude their use in a design context and therefore modelling is required. Unfortunately, the inaccuracies introduced by RANS- or URANS-based CFD modelling approaches can limit the impact CFD can have on technology development.
This presentation will present state-of-the-art high-fidelity simulations of bladed turbomachinery components, harnessing the power of the latest GPU-accelerated supercomputing systems. It will include discussion of cases with fully resolved realistic roughness and show how physical insight relevant to designers has been extracted. The talk will also introduce some of the inherent turbulence modelling errors and how those can be addressed with a novel machine-learning approach that can use both high-fidelity and sparse experimental data. It will be shown that closure models developed using the gene-expression programming approach, which are interpretable and easily implementable into CFD solvers, outperform traditional models both for the cases they were trained on and for cases not seen before.
Richard is Chair Professor of Computational Mechanics in the Department of Mechanical Engineering at the University of Melbourne. He also leads the Power Generation and Transport Program of the Melbourne Energy Institute.
His main interests are in (i) high-fidelity simulation of transitional and turbulent flows to gain physical understanding of flow and noise generation mechanisms, (ii) pursuing novel machine-learning approaches to help assess and improve low-order models (e.g. RANS) that can be employed in an industrial context.
He received his PhD in 2004 in Aerospace Engineering at the University of Arizona and prior to joining the University of Melbourne, he was a Professor of Fluid Dynamics and Aeroacoustics in the Aerodynamics and Flight Mechanics research group at the University of Southampton and headed the UK Turbulence Consortium (www.turbulence.ac.uk). He was awarded a veski innovation fellowship in July 2015 entitled: "Impacting Industry by enabling a step-change in simulation fidelity for flow and noise problems" and has been granted an Australian Research Council Future Fellowship for 2020-2024 to work on integrating high-fidelity simulation and machine-learning based turbulence modelling. He is an editor for Flow, Turbulence and Combustion and the Journal of Turbomachinery and is part of the ASME Gas Turbine Technology Group.