7 Benefits of Lightweighting
7 Benefits of Lightweighting
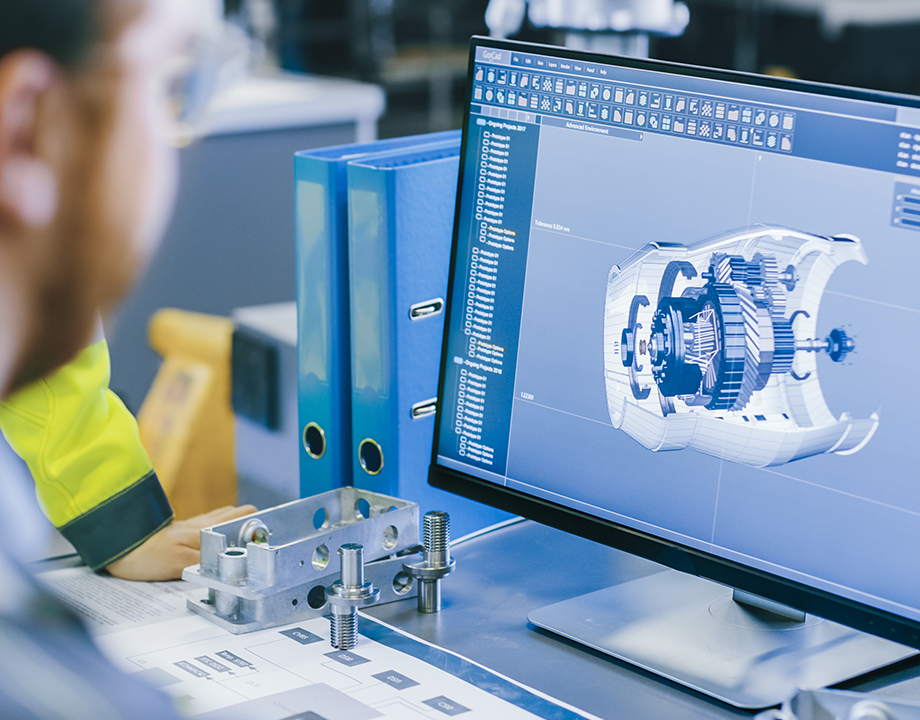
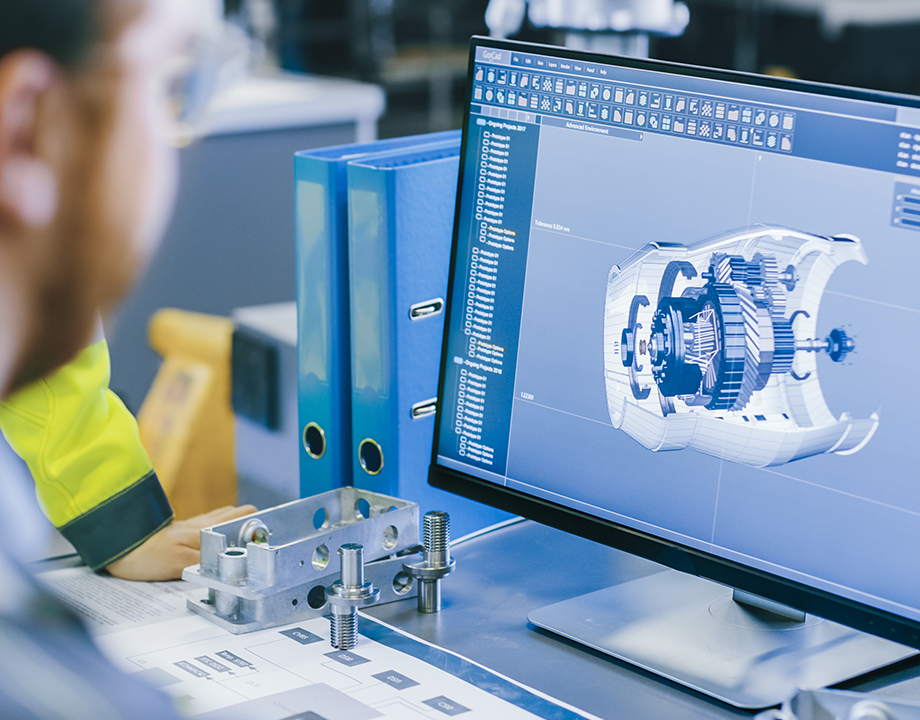
Lightweighting can improve performance while saving money and material waste.
Besides improved performance, another reason engineers turn to lightweighting is that it saves money by reducing the amount of material waste. More than 40% of manufacturing costs are related to materials; a more efficient design that uses less material reduces costs, improves product performance, and speeds up production.
Here are seven ways that lightweighting benefits manufacturing and design.
1. Reduced manufacturing costs
Lighter-weight parts typically require less material, which reduces overall material and manufacturing costs. If 40 percent of manufacturing costs are materials-related, this means that a 10 percent reduction in weight lowers manufacturing costs by 4 percent, demonstrating that a slight decrease in the amount of material used in a design can reduce manufacturing costs significantly.
More for You: Combining Parts Simplifies Assembly, Improves Quality
2. Sustainability
By using fewer materials, lightweighting plays a key role in making manufacturing processes more sustainable by reducing carbon dioxide emissions, the consumption of natural resources, and the amount of waste that is sent to landfills. All of that saved energy and reduce a company’s carbon footprint.
3. Improved performance
Lightweight components typically offer performance advantages. For example, using lighter materials in auto manufacturing improves vehicle maneuverability, acceleration, and durability. In aviation, the Boeing 787 was designed to be 20% lighter, which increased fuel economy by 10 percent to 12 percent. In the consumer space, sports equipment made from carbon composites has improved strength-to-weight ratios and are lighter weight and easier to use, reducing fatigue.
4. Material savings
Lighter-weight parts typically use less materials by volume, leading to cost savings. This is especially true for more expensive materials that are highly engineered or delicate/sensitive, such as bioresorbables. With the current material shortages and unpredictable supply chains, lightweighting helps conserve inventories of these expensive materials. Additive manufacturing too, is very effective for creating lighter-weight designs that conserve these materials.
Reader’s Choice: 3D Printing Goes Mobile
5. Expanded material options
The weight of standard materials can often limit how a particular product or component can be designed. However, lightweighting (latticing, for example) can expand the range of materials that can be used for that given application, which may even have better chemical and/or mechanical properties for that application. For example, compared to steel, composite materials can have outstanding heat and chemical resistance properties, yet still be lighter weight, stronger, and more flexible.
6. Metal to plastic conversion
Plastic parts typically weigh up to 50% less than their metal counterparts; as a result, more manufacturers are shifting from metal to plastic parts to save money and be more competitive. Engineers have more than 25,000 engineering-grade plastics from which to choose. Such a huge variety makes it easier to select or create custom-blended plastics for specific applications, such as lightweighting. Metal parts often require secondary steps such as painting and finishing. Because they already come in a variety of colors, textures, and surfaces, plastics can eliminate the need for secondary operations.
7. Consumer safety
Lightweighting can also contribute to consumer safety. Many solid components provide more of their desired characteristics than is required. for example, a component could be 100 times as stiff as it needs to be. The elimination of material via lightweighting could, for instance, decrease the same part’s stiffness to 25 times what is required or even less, making that part less dangerous in high-impact situations.
Editor’s Pick: Printing Across Barriers with Sound
Adopting lightweighting as a key tool for generative design can improve part performance, reduce wear and tear, and make operations more efficient and cost-effective. Extremely complex lattice structures that reduce weight can be made using additive manufacturing that cannot be achieved using sophisticated CNC machining equipment.
Perhaps the most exciting part of lightweighting is the design freedom it provides engineers. They can think beyond what they have been taught about design complexity, geometry, and material science.
The continued advancement of additive manufacturing technologies and materials will allow them to design increasingly complex lightweight solutions for an ever-expanding variety of commercial and industrial applications that improve product performance and longevity. The combination of advanced manufacturing technologies such as 3D printing with generative design software can lead to an exciting array of new lightweighting opportunities.
Mark Crawford is a science and technology writer in Corrales, N.M.