7 Top Applications of Lasers in Manufacturing
7 Top Applications of Lasers in Manufacturing
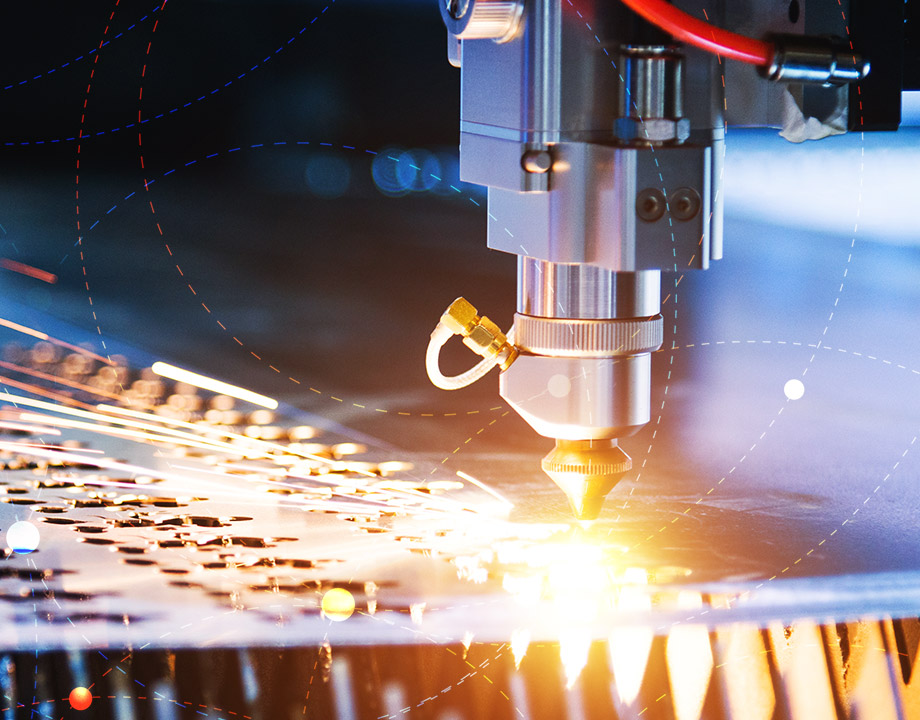
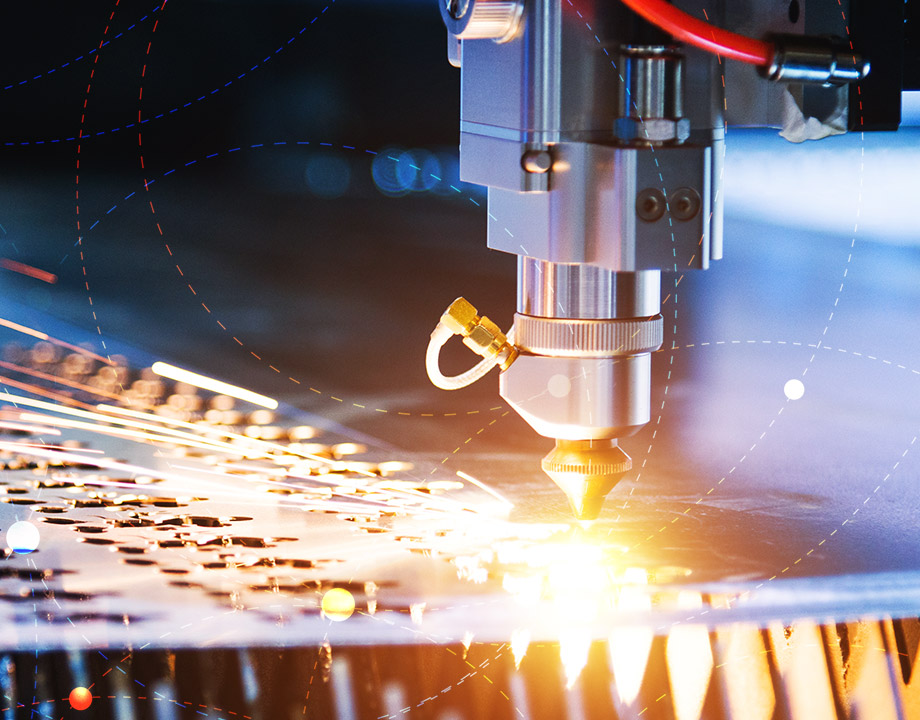
Lasers are one of the most widely used tools in manufacturing and can create fine features that are difficult or impossible to make using traditional machining equipment.
This story was updated on 1/31/2023.
Lasers are one of the most widely used tools in manufacturing today, especially as additive manufacturing and Industry 4.0 allow engineers to create more complex features and product designs that require tight tolerances. Laser machining can create fine features that are difficult or impossible to make using traditional machining equipment, and laser cuts are super-clean with no burrs or heat effects on the surrounding material—thereby eliminating the need for some secondary finishing steps.
Laser processes are becoming the go-to manufacturing technologies for medical device manufacturers as they design smaller and more advanced products. Keep reading to learn about seven top applications for lasers in manufacturing.
1. Laser Marking
Lasers are increasingly used to imprint unique identification (UID) numbers on parts and products, which allow them to be easily traced in the event of a recall. Laser markings are highly durable and, for medical devices, can withstand many cycles of sterilization. Both human-readable and barcode information, including lot and batch codes and even design histories, can be laser-marked on products with flat or curved part geometries.
2. Surface Texturing
Lasers can create textures or patterned microstructures on the surfaces of components or products that improve physical performance, such as wear rates, grip, optical properties, and load capacity. Laser micro-texturing can create roughness on medical implants that make it easier for new tissue or bone to take hold and grow into the new implant, and patterns with features as small as 10 µm can be produced with very high depth resolution.
Recommended for You: 9 Materials Discoveries that could Transform Manufacturing
3. Laser Ablation
This subtractive machining method essentially vaporizes material with great precision using a laser beam. Pulse length, wavelength, and intensity are adjusted according to the material being processed. Ablation is especially useful for machining sensitive materials such as nanomaterials, or superconductive materials, because the non-contact method does not change the structure of the material or damage its surface with abrasion or heat.
4. Laser Drilling
Lasers are incredibly accurate at drilling micron-sized holes in a wide range of materials, including metals, polymers, and ceramics.
“Many of today’s manufactured parts call for microscopic features that can only be created with laser drilling,” said Matt Nipper, director of engineering for Laser Light Technologies, which has since been acquired by Spectrum Plastics. “Very small, complex features can be produced in a variety of materials, with methods such as direct write, trepanning, and mask projection, with no heat effects or material damage.”
5. Laser Cutting
Similar to laser drilling, laser cutting relies on a focused laser beam to ablate material, straight cut, or cut patterns to very precise depths in the material or component. Ultrafast lasers are typically used for various types of metals and polymers because they cut clean edges and do not create heat-affected zones.
Lasers can cut a wide variety of materials, including aluminum, titanium, and steel, with micron-level tolerances.
You May Also Like: 8 Ways 3D Printing is Helping to Fight Coronavirus
6. Laser Welding
This process is especially effective for products with complex geometries or dissimilar materials that are difficult to join together. Depending on the product, laser welding can be the best joining process compared to gluing or soldering, especially for connecting metals and plastics. It also creates strong, high-precision welds that can be as small as 0.004 inches and provide repeatable quality.
7. Wire Stripping
Wire stripping removes sections of insulation or shielding from wires and cables to provide electrical contact points and make the wire ready for termination.
“Laser wire stripping is a fast process that provides excellent precision and process control and eliminates contact with the wire, allowing for the processing of delicate wire gauges greater than 32 AWG,” said Nipper. “Insulation can be removed to within a 0.005-inch tolerance. Stripping can be programmed to ablate insulation at any point along the wire, enabling high-precision mid-span removals.”
New Laser Applications
Lasers are key pieces of equipment for Industry 4.0, and researchers are continuing to learn how to use them more effectively in manufacturing processes, including faster speeds.
For example, in 2018, the National Institute of Standards and Technology (NIST) built a laser that pulses 100 times faster than conventional ultrafast lasers (pulses that last quadrillionths of a second). Additionally, scientists in Germany are experimenting with integrating tiny lasers directly in silicon chips to increase processing speed.
Another area of research is using artificial intelligence (AI) to create smart lasers that “understand” the material being processed and when the process is finished. German machine manufacturer TRUMPF is developing a laser system that uses AI to determine the best welding points for creating copper coils for the automotive industry.
As more companies embrace Industry 4.0.—including AI, sensor technologies, and additive manufacturing—lasers will have an ever-expanding role in modern manufacturing.
Mark Crawford is a technology writer based in Corrales, N.M.
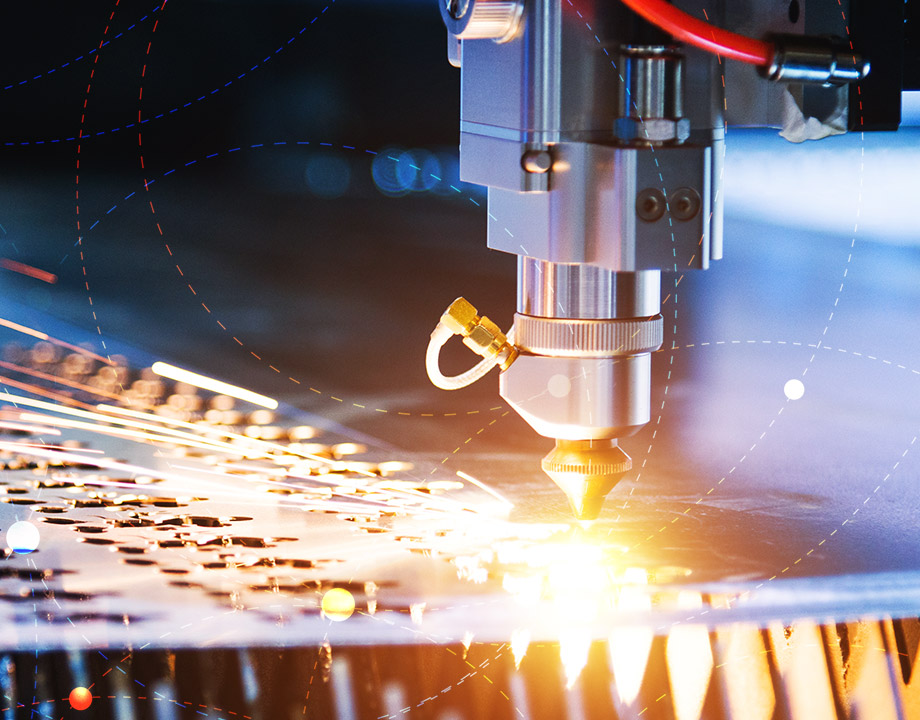
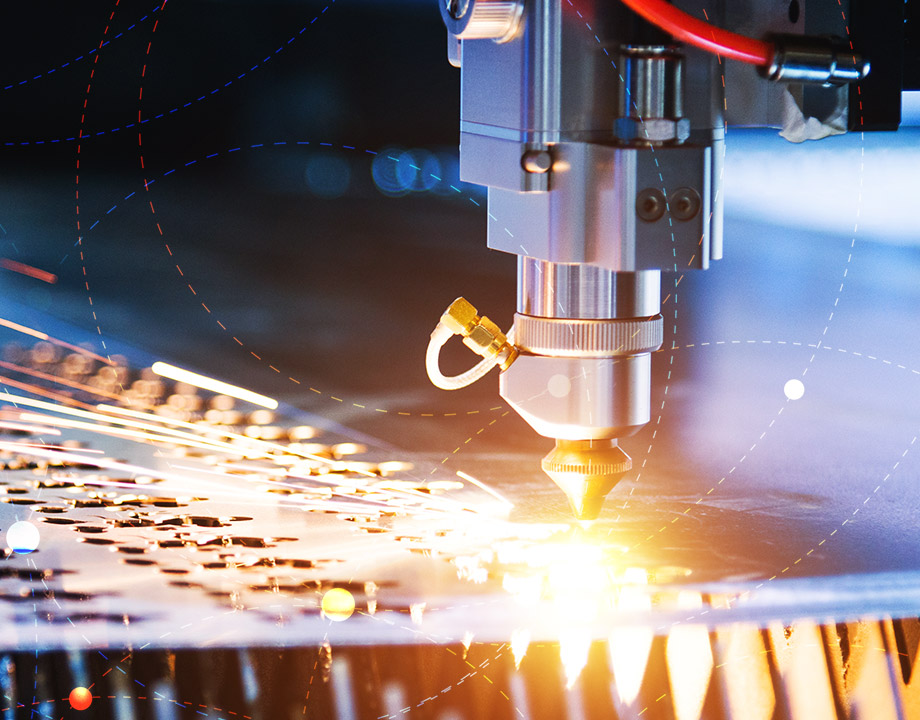