Advanced Thermal Interface Materials for Electronic Assemblies
Advanced Thermal Interface Materials for Electronic Assemblies
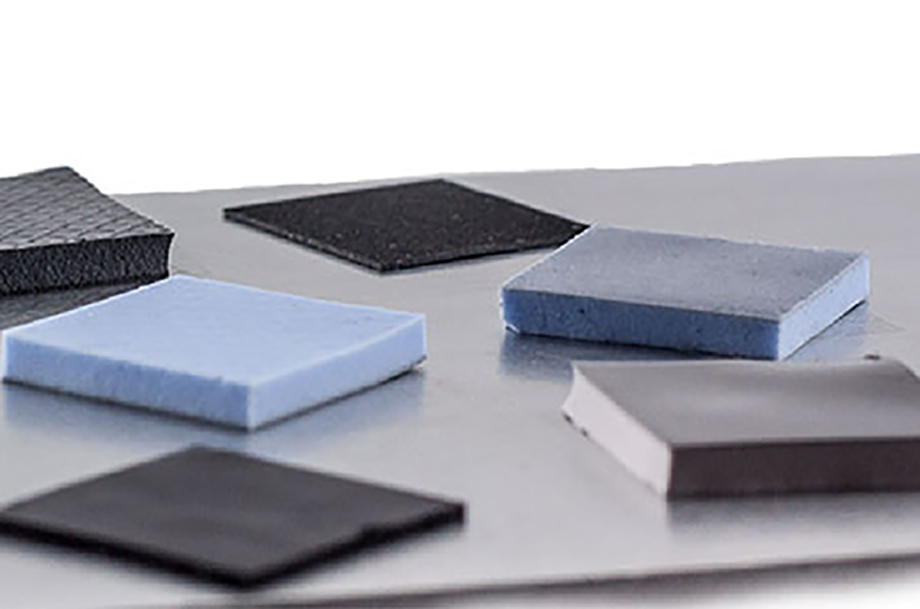
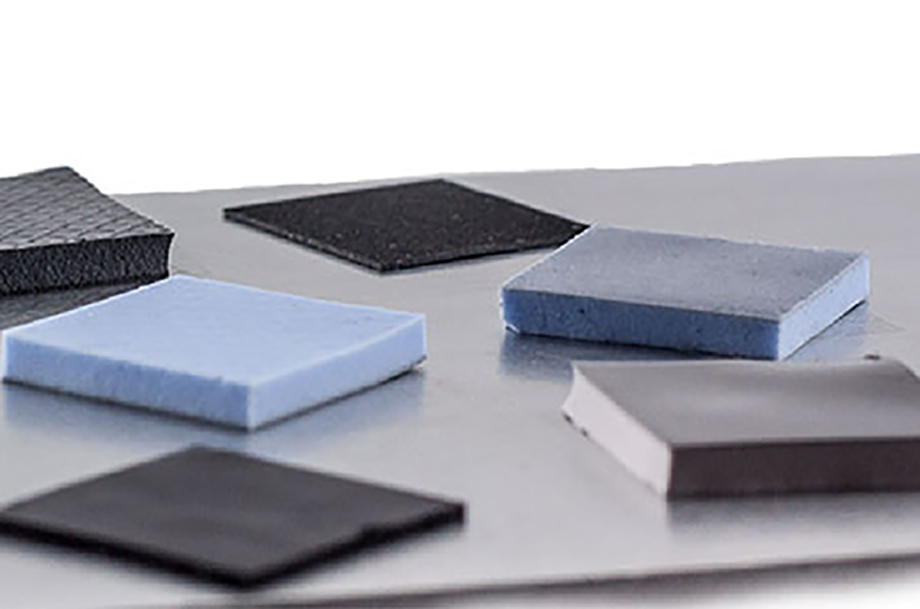
As electronic devices draw more power and miniaturize, engineers need to learn how to design effective thermal management systems.
Overheating is a critical concern for next-generation electronics across most major industries. Moore’s law states that the number of transistors on integrated circuit chips doubles every two years. With increased computing power and higher transistor density comes greater thermal loads and an increased need for more efficient, more effective thermal management.
In addition to innovations for improved performance, many electronic component manufacturing trends have also focused on device miniaturization, which further complicates high-performance cooling. Thermal management is often considered last in the design cycle, even though one of the leading causes of product performance issues is overheating. Heat is attributed as the cause of electronic component failure 55 percent of the time. Design engineers are best equipped to address the thermal limitations of advanced electronic components by leveraging the capabilities of carefully selected thermal interface materials (TIM).
TIMs play a vital role in addressing the thermal limitations of new electronic assembly designs. They provide improved thermal contact between heat-generating devices and cooling components, effectively helping to increase power capacity and reliability while also reducing the cost of the finished assembly. The ideal material conforms to mating surfaces, wets out across the substrate, and maintains a minimal thickness.
Thermal interface materials are a crucial part of any thermal management solution. Since it’s physically a small portion of most applications, it’s an easy component to overlook. But thermal interface material can make or break a device and its associated product.
These materials remove air gaps and aid in optimized heat transfer to improve cooling and improve the reliability of the application significantly. As a passive solution used for conductive cooling, they offer highly reliable, thin heat spreading. Utilized within an assembly, they improve reliability and offer increased functionality to thermal solutions.
TIMs combine thermal properties with mechanical characteristics into a single electrically isolated product. They can be constructed out of many materials such as wax, grease, and graphite, but they are primarily made from polymer materials such as silicone or rubber.
Recommended for You: Five Key Trends in Industrial Connectivity
For example, the TIMs manufactured by 3M’s Electronic Materials Solutions division consists of mostly acrylic and silicone thermal interface pads. These types of TIMs are typically die-cut by converters like Boyd. These materials are available with fillers in a range of thicknesses, dielectric strengths, and thermal conductivities. They help improve device assembly time, reduce weight and extend component life. TIMs can also be designed with exceptional peel strengths, virtually eliminating the need for mechanical fastens, and each product is engineered to address specific application requirements.
Thermally conductive acrylic interface pads provide higher levels of conductivity than comparable products on the market. These materials are durable, highly conformable, have excellent wet-out characteristics, and offer substantial cost savings compared to silicone materials. Reported thermal conductivity is tested in accordance with ASTM D5470 test methods.
Proper material selection is critical to the performance and functionality of the final thermal solution. Interface pads are highly conformable, slightly tacky acrylic elastomer filled with thermally conductive ceramic particles. It improves handling and forms an effective heat path when bonding irregular IC surfaces and electric vehicle batteries to heat spreaders and heat sinks. Like the 3M Thermally Conductive Acrylic Interface Pad 5571, some pads are available in roll format for use in rotary die-cut conversions. The soft-compliant acrylic interface pad allows for pressure relaxation, helping prevent high-pressure zones when joining non-flat IC surfaces and heat spreading blocks.
Thermally conductive interface tape is made of acrylic polymer pressure-sensitive adhesive tape with a thin PET carrier. The tape has a rated thermal conductivity of 1.5 W/mK, excellent dielectric properties, and good substrate compatibility. The tapes can be cut to multiple thicknesses for bonding or joining a range of different surfaces.
A different type of pad material is silicone, which addresses the requirements of high-temperature applications. These materials exhibit excellent dielectric properties and are available with up to 4.9 W/ mK with thermal conductivities. 3M’s Thermally Conductive Silicone Interface Pad 5516, for example, is a highly conformable, slightly tacky silicone elastomer pad with a rated thermal conductivity of 3.1 W/mK. The soft silicone pad is conformable at low pressures. It provides high-temperature resistance and good dielectric properties providing an effective heat transfer path between heat-generating components and heat sinks, heat spreaders, or other cooling devices.
Excess heat is the most prevalent cause of product failure, decreased efficiency, lower reliability, and substandard performance. To overcome the thermal limitations of next-generation electronics, design engineers require advanced materials and highly customized solutions.
TIMs benefit electronic assemblies in two primary ways. Their heat spreading properties help reduce heat density and accumulation at the heat source. Excessive heat is one of the common causes for degrading in electronics. Minimizing heat source temperatures in electronic assemblies helps extend their lifetime usage. TIMs also help eliminate the air gap between the heat source and the thermal solution with a more conductive material. Heat will accumulate less by reducing this interface resistance,
Many engineers focus more on heat sink design but often forget to consider how heat gets from the heat source to the heat sink. Even the smoothest surface has some level of surface roughness. The roughness of two surfaces in contact with each other creates air pockets. Since air is a good thermal insulator, air pockets from mating surface roughness impede heat transfer from one surface to another.
You May Also Like: Advancing Battery Technology for Modern Innovations
This is where using thermal interface material comes in. TIMs replace most of these air pockets with a material optimized for better thermal conductivity. By using thermal interface material, we increase how much heat is transferred away from the heat source and into the heat sink.
In the diagram shown here, dark blue represents thermal interface material. Most of the light blue air pockets have been eliminated and replaced with a more conductive material. Heat is now efficiently conducting across the entire surface. This improves heat transfer away from the heat source significantly. It’s nearly impossible to remove 100 percent of the air in most cases, so there are still small air pockets in little nooks and crannies. However, thermal performance is vastly improved with the use of thermal interface materials.
TIMs provide highly effective thermal solutions that reduce assembly time, improve yield rates and extend component life at the lowest total cost of ownership. Overheating is one of the leading causes of electronic product failure, and to overcome the thermal limitations of next-generation electronics, design engineers require advanced materials and highly customized solutions.
Magnus Tedestedt is vice president of engineered materials at Boyd Corporation.
In addition to innovations for improved performance, many electronic component manufacturing trends have also focused on device miniaturization, which further complicates high-performance cooling. Thermal management is often considered last in the design cycle, even though one of the leading causes of product performance issues is overheating. Heat is attributed as the cause of electronic component failure 55 percent of the time. Design engineers are best equipped to address the thermal limitations of advanced electronic components by leveraging the capabilities of carefully selected thermal interface materials (TIM).
TIMs play a vital role in addressing the thermal limitations of new electronic assembly designs. They provide improved thermal contact between heat-generating devices and cooling components, effectively helping to increase power capacity and reliability while also reducing the cost of the finished assembly. The ideal material conforms to mating surfaces, wets out across the substrate, and maintains a minimal thickness.
TIMs Increase Device Reliability
Thermal interface materials are a crucial part of any thermal management solution. Since it’s physically a small portion of most applications, it’s an easy component to overlook. But thermal interface material can make or break a device and its associated product.
These materials remove air gaps and aid in optimized heat transfer to improve cooling and improve the reliability of the application significantly. As a passive solution used for conductive cooling, they offer highly reliable, thin heat spreading. Utilized within an assembly, they improve reliability and offer increased functionality to thermal solutions.
TIMs combine thermal properties with mechanical characteristics into a single electrically isolated product. They can be constructed out of many materials such as wax, grease, and graphite, but they are primarily made from polymer materials such as silicone or rubber.
Recommended for You: Five Key Trends in Industrial Connectivity
For example, the TIMs manufactured by 3M’s Electronic Materials Solutions division consists of mostly acrylic and silicone thermal interface pads. These types of TIMs are typically die-cut by converters like Boyd. These materials are available with fillers in a range of thicknesses, dielectric strengths, and thermal conductivities. They help improve device assembly time, reduce weight and extend component life. TIMs can also be designed with exceptional peel strengths, virtually eliminating the need for mechanical fastens, and each product is engineered to address specific application requirements.
Thermally conductive acrylic interface pads provide higher levels of conductivity than comparable products on the market. These materials are durable, highly conformable, have excellent wet-out characteristics, and offer substantial cost savings compared to silicone materials. Reported thermal conductivity is tested in accordance with ASTM D5470 test methods.
Different Interface Materials for Different Applications
Proper material selection is critical to the performance and functionality of the final thermal solution. Interface pads are highly conformable, slightly tacky acrylic elastomer filled with thermally conductive ceramic particles. It improves handling and forms an effective heat path when bonding irregular IC surfaces and electric vehicle batteries to heat spreaders and heat sinks. Like the 3M Thermally Conductive Acrylic Interface Pad 5571, some pads are available in roll format for use in rotary die-cut conversions. The soft-compliant acrylic interface pad allows for pressure relaxation, helping prevent high-pressure zones when joining non-flat IC surfaces and heat spreading blocks.
Thermally conductive interface tape is made of acrylic polymer pressure-sensitive adhesive tape with a thin PET carrier. The tape has a rated thermal conductivity of 1.5 W/mK, excellent dielectric properties, and good substrate compatibility. The tapes can be cut to multiple thicknesses for bonding or joining a range of different surfaces.
A different type of pad material is silicone, which addresses the requirements of high-temperature applications. These materials exhibit excellent dielectric properties and are available with up to 4.9 W/ mK with thermal conductivities. 3M’s Thermally Conductive Silicone Interface Pad 5516, for example, is a highly conformable, slightly tacky silicone elastomer pad with a rated thermal conductivity of 3.1 W/mK. The soft silicone pad is conformable at low pressures. It provides high-temperature resistance and good dielectric properties providing an effective heat transfer path between heat-generating components and heat sinks, heat spreaders, or other cooling devices.
The Benefits of TIMs in Electronic Assemblies
Excess heat is the most prevalent cause of product failure, decreased efficiency, lower reliability, and substandard performance. To overcome the thermal limitations of next-generation electronics, design engineers require advanced materials and highly customized solutions.
TIMs benefit electronic assemblies in two primary ways. Their heat spreading properties help reduce heat density and accumulation at the heat source. Excessive heat is one of the common causes for degrading in electronics. Minimizing heat source temperatures in electronic assemblies helps extend their lifetime usage. TIMs also help eliminate the air gap between the heat source and the thermal solution with a more conductive material. Heat will accumulate less by reducing this interface resistance,
Many engineers focus more on heat sink design but often forget to consider how heat gets from the heat source to the heat sink. Even the smoothest surface has some level of surface roughness. The roughness of two surfaces in contact with each other creates air pockets. Since air is a good thermal insulator, air pockets from mating surface roughness impede heat transfer from one surface to another.
You May Also Like: Advancing Battery Technology for Modern Innovations
This is where using thermal interface material comes in. TIMs replace most of these air pockets with a material optimized for better thermal conductivity. By using thermal interface material, we increase how much heat is transferred away from the heat source and into the heat sink.
In the diagram shown here, dark blue represents thermal interface material. Most of the light blue air pockets have been eliminated and replaced with a more conductive material. Heat is now efficiently conducting across the entire surface. This improves heat transfer away from the heat source significantly. It’s nearly impossible to remove 100 percent of the air in most cases, so there are still small air pockets in little nooks and crannies. However, thermal performance is vastly improved with the use of thermal interface materials.
TIMs provide highly effective thermal solutions that reduce assembly time, improve yield rates and extend component life at the lowest total cost of ownership. Overheating is one of the leading causes of electronic product failure, and to overcome the thermal limitations of next-generation electronics, design engineers require advanced materials and highly customized solutions.
Magnus Tedestedt is vice president of engineered materials at Boyd Corporation.