Researchers to Create a Digital Library for Aircraft Parts
Researchers to Create a Digital Library for Aircraft Parts
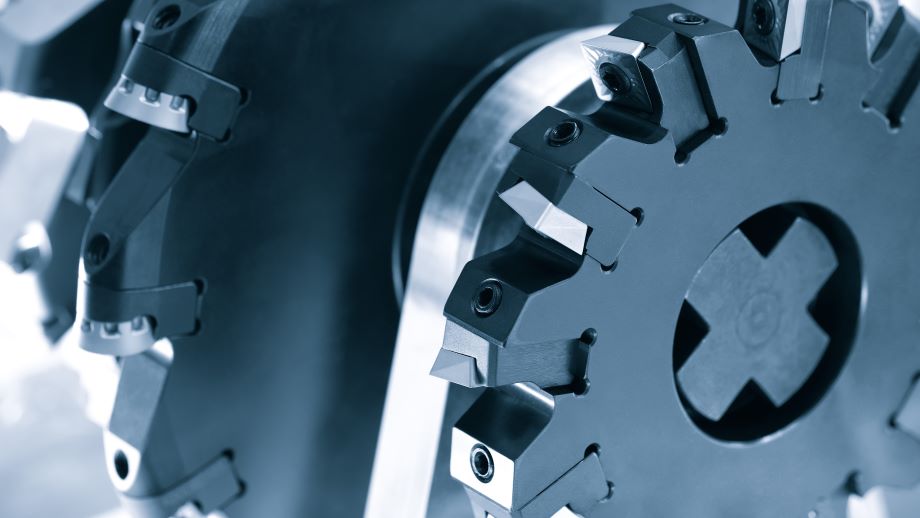
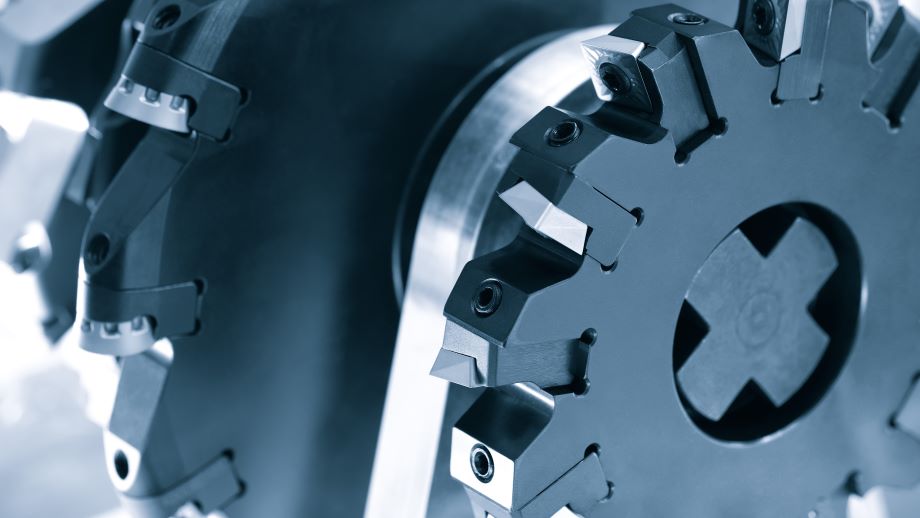
Advanced technologies and methods could improve the maintenance and readiness of older aircraft fleets.
Aircraft can have surprisingly long lives. For instance, the 58 B-52 bombers operated by the U.S. Air Force were all built prior to 1963. While the manufacturer of the B-52, Boeing, is still in existence, consolidation in the industry makes finding parts from the original equipment manufacturer a problem.
Researchers at the University of Oklahoma recently received a grant to address the challenges of maintaining aging aircraft. Their research aims to develop advanced technologies and methods to improve the sustainment and readiness of older aircraft fleets.
This initiative is part of a broader effort to enhance the safety, performance, and longevity of military and commercial aircraft through innovative engineering solutions. The project will focus on new diagnostic tools, materials, and maintenance practices that enable fabrication of critical spares and parts to ensure these aircraft remain operational and cost-effective for extended periods.
Reverse or shape engineering (SE) entails recapturing a part’s geometry and material to reproduce a product’s original functionality and preparing it for downstream applications. It is required when an industrial part either partly or fully ceases to function as intended during service. This is especially essential when there is little or no technical data available to guide replacement fabrication. The entire SE process must be made faster, cheaper and better.
Selected for You: New 3D Printing Method Cuts Material Development Time in Half
“The measurement process obtains data through laser scanning systems and coordinate measurement systems, scanning a variety of parts ranging from small components to larger assemblies,” said Shivakumar Raman, David Ross Boyd Professor and director of the School of Industrial and Systems Engineering at the University of Oklahoma in Norman. “Scans of an object result in the collection of large-point cloud data sets used to reconstruct a digital model of the object. The resulting digital model will then drive downstream applications such as prototype fabrication, re-engineering, materials characterization, structural finite-element analysis and simulation.”
Raman is leading the initiative to capture the shape of these critical parts.
“Many airplanes, especially military and commercial, were designed in the 1950s and 1960s, and their parts go out of production,” Raman said. “The original equipment manufacturer does not want to sell those parts, or the parts no longer exist. Sometimes, the original manufacturer is no longer in business. Components can’t be around forever.”
For instance, the Boeing 747 has over 1 million parts and warehouses simply lack the capacity to store every airplane component because of spatial constraints. “The demand fluctuates unpredictably,” Raman said. “You might require a part every three years, every 30 years, or not at all. Hence, stockpiling becomes impractical.”
As Raman explains, equipment limitations hinder widespread engagement in this area. To delve deeper into this subject, understanding equipment constraints is crucial.
More Advanced Manufacturing: Equipment Makes 5 Paralympic Sports Possible
“We have several scanners that provide different levels of precision and accuracy, that include coordinate measuring machines, laser radar scanners, scan arms, and stereoscopy/photogrammetry/interferometry/structured light equipment,” Raman said. “Measurement and part conformance verification are the primary functions of these equipment. They often procure the data that must be suitably converted and input into CAD systems. We are unique in the sense that we have a complete array of such equipment that can reverse engineer most mechanical parts used in industry.”
Discover the Benefits of ASME Membership
“True democratization of manufacturing will involve collaboration across and within small companies with complementary expertise and capabilities,” Raman said.
More than 75 percent of US manufacturing is performed by small manufacturers with 20 employees or less and are limited to specific capabilities and expertise. Raman said critical gaps present among small manufacturers can be alleviated by collaboration to produce a robust supply ecosystem. Entire supply chains can be ‘leaned out’ and optimized to deliver “faster, cheaper, better” solutions.
“Our recent research has investigated these topics including the establishment of robust and resilient supply chains of small and large manufacturers with able support from university research teams,” he says. “Quality is central to delivery!”
Jim Romeo is a technology writer in Chesapeake, Va.
Researchers at the University of Oklahoma recently received a grant to address the challenges of maintaining aging aircraft. Their research aims to develop advanced technologies and methods to improve the sustainment and readiness of older aircraft fleets.
This initiative is part of a broader effort to enhance the safety, performance, and longevity of military and commercial aircraft through innovative engineering solutions. The project will focus on new diagnostic tools, materials, and maintenance practices that enable fabrication of critical spares and parts to ensure these aircraft remain operational and cost-effective for extended periods.
Reverse or shape engineering (SE) entails recapturing a part’s geometry and material to reproduce a product’s original functionality and preparing it for downstream applications. It is required when an industrial part either partly or fully ceases to function as intended during service. This is especially essential when there is little or no technical data available to guide replacement fabrication. The entire SE process must be made faster, cheaper and better.
Selected for You: New 3D Printing Method Cuts Material Development Time in Half
“The measurement process obtains data through laser scanning systems and coordinate measurement systems, scanning a variety of parts ranging from small components to larger assemblies,” said Shivakumar Raman, David Ross Boyd Professor and director of the School of Industrial and Systems Engineering at the University of Oklahoma in Norman. “Scans of an object result in the collection of large-point cloud data sets used to reconstruct a digital model of the object. The resulting digital model will then drive downstream applications such as prototype fabrication, re-engineering, materials characterization, structural finite-element analysis and simulation.”
Raman is leading the initiative to capture the shape of these critical parts.
Endurance flying
Advanced computer technologies allow for digitized models of products to exist in shared repositories for use by third parties and customers. In Raman’s vision, once the parts for an aircraft are digitized and stored in this sort of library, companies will be able to manufacture scanned objects in needed quantities.“Many airplanes, especially military and commercial, were designed in the 1950s and 1960s, and their parts go out of production,” Raman said. “The original equipment manufacturer does not want to sell those parts, or the parts no longer exist. Sometimes, the original manufacturer is no longer in business. Components can’t be around forever.”
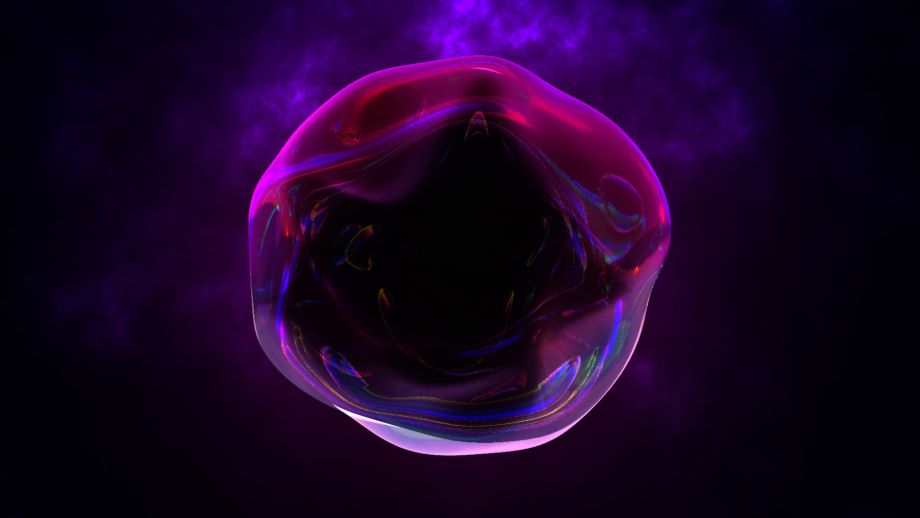
For instance, the Boeing 747 has over 1 million parts and warehouses simply lack the capacity to store every airplane component because of spatial constraints. “The demand fluctuates unpredictably,” Raman said. “You might require a part every three years, every 30 years, or not at all. Hence, stockpiling becomes impractical.”
As Raman explains, equipment limitations hinder widespread engagement in this area. To delve deeper into this subject, understanding equipment constraints is crucial.
More Advanced Manufacturing: Equipment Makes 5 Paralympic Sports Possible
“We have several scanners that provide different levels of precision and accuracy, that include coordinate measuring machines, laser radar scanners, scan arms, and stereoscopy/photogrammetry/interferometry/structured light equipment,” Raman said. “Measurement and part conformance verification are the primary functions of these equipment. They often procure the data that must be suitably converted and input into CAD systems. We are unique in the sense that we have a complete array of such equipment that can reverse engineer most mechanical parts used in industry.”
A new frontier for parts support
The ability to scan, identify geometries, and utilizing shape engineering to define a product for fabrication opens a new frontier for parts supportability in an environment that not only relies on the availability of such parts, but preserves the finite and accurate specifications of the part, Raman said. Once these methods become commonplace, aircraft owners will not be dependent on original manufacturers to supply parts. Instead, the part may be reverse engineered and able to be fabricated organically rather than relying on an outside vendor.Discover the Benefits of ASME Membership
“True democratization of manufacturing will involve collaboration across and within small companies with complementary expertise and capabilities,” Raman said.
More than 75 percent of US manufacturing is performed by small manufacturers with 20 employees or less and are limited to specific capabilities and expertise. Raman said critical gaps present among small manufacturers can be alleviated by collaboration to produce a robust supply ecosystem. Entire supply chains can be ‘leaned out’ and optimized to deliver “faster, cheaper, better” solutions.
“Our recent research has investigated these topics including the establishment of robust and resilient supply chains of small and large manufacturers with able support from university research teams,” he says. “Quality is central to delivery!”
Jim Romeo is a technology writer in Chesapeake, Va.