Bacterial Additive Makes Plastic More Sustainable
Bacterial Additive Makes Plastic More Sustainable
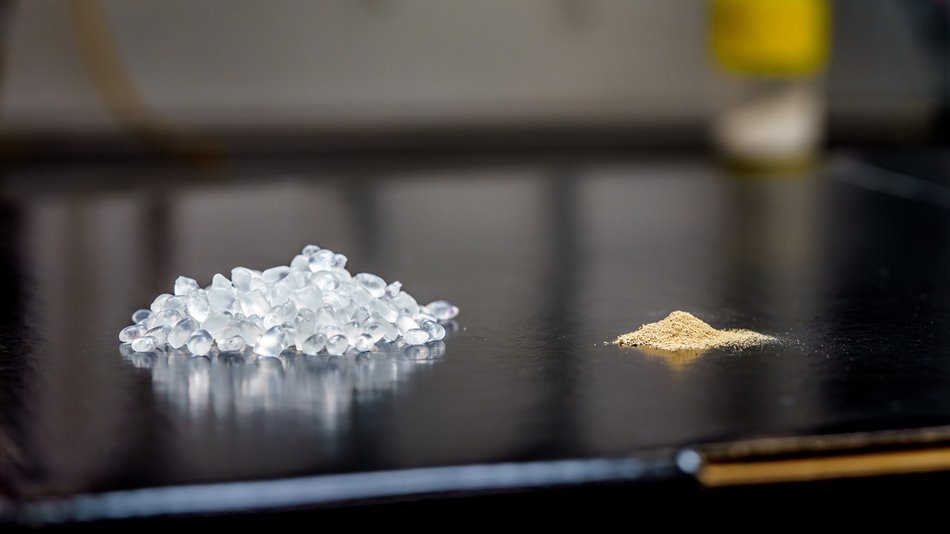
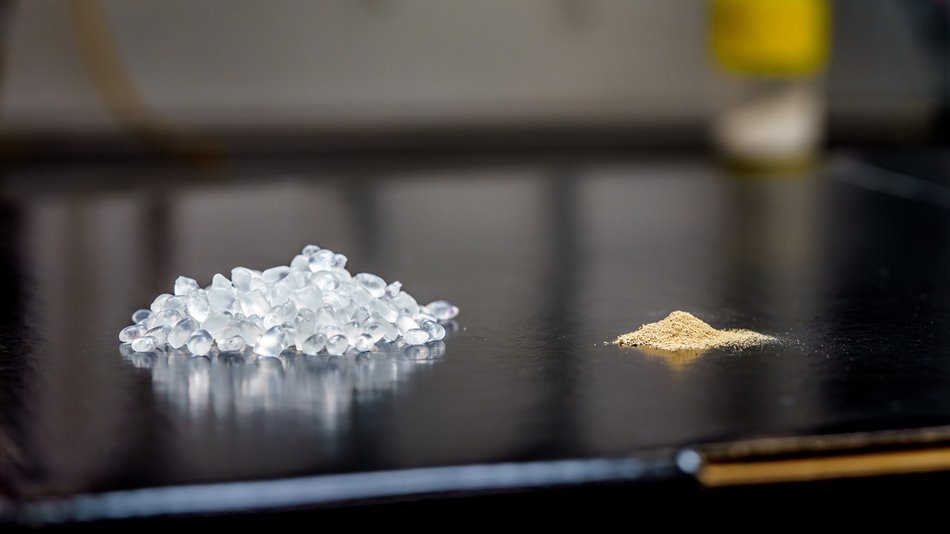
Engineers found that mixing bacterial spores into polyurethane can enable it to break down in a landfill.
Researchers have recently announced the development of a hybrid engineered living plastic material capable of self-digestion in a compost environment. Engineered living materials, a relatively new field, combines synthetics and biological materials to create products that change their shape or properties in response to environmental stimuli.
“We incorporated bacterial spores into polyurethanes with the intent that once the spores woke up and started germinating, they would use the polymers as a food source to make the polyurethanes biodegradable,” explained Jonathan Pokorski, a professor of nanoengineering at the University of California San Diego (UC San Diego) Jacobs School of Engineering.
The research team included members from UC San Diego, the New Materials Institute at the University of Georgia in Athens, and BASF’s Thermoplastic Polyurethane Research Group.
Hundreds of types of plastic exist, each with different chemical compositions, uses, and manufacturing processes. Despite consumer participation, less than 10 percent of global plastic waste is recycled and roughly 12 percent incinerated, leaving nearly 80 percent destined for landfills. Thermoplastic polyurethanes (TPU), commonly used in footwear, sporting goods, and cell phone cases, ranked as the sixth most common plastic produced worldwide. But only 0.3 percent of TPUs are recycled in the US, even though they fell under category seven of the recycling code for "other" plastics.
Anticipating their hybrid plastic would likely end up in a landfill rather than a recycling facility, researchers mimicked a compost environment to test the degradation of their hybrid plastic material.
Discover the Benefits of ASME Membership
“The plastic on its own isn't a good enough food source to wake up the bacteria spores. You can soak the polymers in water, or in a salt solution and nothing really happens. They need a little bit of extra juice to get them going,” Pokorski said.
Using adaptive laboratory evolution, the research team adapted the bacteria to withstand higher temperatures during plastic production. They placed B. subtilis cultures in a cylindrical tube and heat-shocked by immersing the tubes in boiling water for varying lengths of time. The resulting dormant B. subtilis spores, now capable of withstanding temperatures up to 275 °F (135 °C) for 15 minutes, were dried into a powder and added to melted thermoplastic polyurethanes, in a concentration up to 0.5 percent by weight, before extrusion.
Thermoplastic polyurethanes offered the potential to integrate well with bacterial spores, which added strength to the final plastic product.
More on This Topic: Catalyzing a Solution for Plastic Waste
“The hope was that the spores would act like rebar does in concrete to reinforce the polymer, which turns out they did,” Pokorski said. Evaluations of the B. subtilis thermoplastic polyurethane (BC TPU) showed an increase in toughness up to 30 percent.
“When we put the plastic (BC TPU) into the sterile compost, we knew that the only thing that was going to serve as a source of degradation was the spores in the polymer,” Pokorski said.
The compost and B. subtilis thermoplastic polyurethane were incubated at 98 °F (37 °C) and 45-to-55 percent relative humidity to mimic a home compost setup. After five months, the team observed as much as 90 percent degradation.
The manufacturing workflow for incorporating B. subtilis powder into plastic is relatively simple, no more complex than adding dye to color the plastic. Heat treating the bacteria spores and turning them into a powder can be done in large volumes for minimal cost. With only 0.5 percentw/w required to create a biodegradable plastic product, the bacteria are an affordable additive.
Selected for You: More Plastics May Be Recycled with Plasma
This collaborative effort by researchers harnessed the capabilities of B. subtilis spores, adapted to withstand high temperatures, and created a hybrid engineered living plastic product. The simplicity and cost-effectiveness of incorporating bacterial spores into thermoplastic polyurethanes make this approach highly feasible for large-scale production. The resulting material’s enhanced toughness and biodegradability further underscore its practical applications.
The project’s success also opened doors for future research and development. By experimenting with different bacteria and plastic materials, scientists could tailor biodegradability to specific environmental conditions and manufacturing requirements. This breakthrough not only provided a viable solution for reducing plastic waste but also sets the stage for ongoing innovation in the field of engineered living materials, paving the way for a more sustainable future.
Nicole Imeson is a technology writer in Calgary, Alta.
“We incorporated bacterial spores into polyurethanes with the intent that once the spores woke up and started germinating, they would use the polymers as a food source to make the polyurethanes biodegradable,” explained Jonathan Pokorski, a professor of nanoengineering at the University of California San Diego (UC San Diego) Jacobs School of Engineering.
The research team included members from UC San Diego, the New Materials Institute at the University of Georgia in Athens, and BASF’s Thermoplastic Polyurethane Research Group.
Hundreds of types of plastic exist, each with different chemical compositions, uses, and manufacturing processes. Despite consumer participation, less than 10 percent of global plastic waste is recycled and roughly 12 percent incinerated, leaving nearly 80 percent destined for landfills. Thermoplastic polyurethanes (TPU), commonly used in footwear, sporting goods, and cell phone cases, ranked as the sixth most common plastic produced worldwide. But only 0.3 percent of TPUs are recycled in the US, even though they fell under category seven of the recycling code for "other" plastics.
Anticipating their hybrid plastic would likely end up in a landfill rather than a recycling facility, researchers mimicked a compost environment to test the degradation of their hybrid plastic material.
Discover the Benefits of ASME Membership
“The plastic on its own isn't a good enough food source to wake up the bacteria spores. You can soak the polymers in water, or in a salt solution and nothing really happens. They need a little bit of extra juice to get them going,” Pokorski said.
Evolution in the lab
The manufacturing process of thermoplastic polyurethanes, like many other plastic products, melted the plastic and extruded it through a dye to form the desired part. Researchers chose thermoplastic polyurethanes for lower manufacturing temperatures—roughly 275 °F (135 °C)—and easier degradation potential compared to some other plastics. Bacillus subtilis, a garden-variety bacteria found in probiotics and bio fertilizer, survives in a dormant state for several years but only resists heat to 212 °F (100 °C).Using adaptive laboratory evolution, the research team adapted the bacteria to withstand higher temperatures during plastic production. They placed B. subtilis cultures in a cylindrical tube and heat-shocked by immersing the tubes in boiling water for varying lengths of time. The resulting dormant B. subtilis spores, now capable of withstanding temperatures up to 275 °F (135 °C) for 15 minutes, were dried into a powder and added to melted thermoplastic polyurethanes, in a concentration up to 0.5 percent by weight, before extrusion.
Thermoplastic polyurethanes offered the potential to integrate well with bacterial spores, which added strength to the final plastic product.
More on This Topic: Catalyzing a Solution for Plastic Waste
“The hope was that the spores would act like rebar does in concrete to reinforce the polymer, which turns out they did,” Pokorski said. Evaluations of the B. subtilis thermoplastic polyurethane (BC TPU) showed an increase in toughness up to 30 percent.
Experimental tests
To see how well BC TPU decomposes, researchers collected four- to five-month-old raw compost—consisting of food waste, forest residue, and livestock manure from the University of Georgia and Athens-Clarke County Solid Waste Compost Facility. They then passed the compost through a sieve to remove large particles and dried the remaining compost into a fine powder and sterilized it. Ensuring sterile compost was critical to confirm that B. subtilis alone degraded the plastic without help from other bacteria.“When we put the plastic (BC TPU) into the sterile compost, we knew that the only thing that was going to serve as a source of degradation was the spores in the polymer,” Pokorski said.
The compost and B. subtilis thermoplastic polyurethane were incubated at 98 °F (37 °C) and 45-to-55 percent relative humidity to mimic a home compost setup. After five months, the team observed as much as 90 percent degradation.
The manufacturing workflow for incorporating B. subtilis powder into plastic is relatively simple, no more complex than adding dye to color the plastic. Heat treating the bacteria spores and turning them into a powder can be done in large volumes for minimal cost. With only 0.5 percentw/w required to create a biodegradable plastic product, the bacteria are an affordable additive.
Selected for You: More Plastics May Be Recycled with Plasma
This collaborative effort by researchers harnessed the capabilities of B. subtilis spores, adapted to withstand high temperatures, and created a hybrid engineered living plastic product. The simplicity and cost-effectiveness of incorporating bacterial spores into thermoplastic polyurethanes make this approach highly feasible for large-scale production. The resulting material’s enhanced toughness and biodegradability further underscore its practical applications.
The project’s success also opened doors for future research and development. By experimenting with different bacteria and plastic materials, scientists could tailor biodegradability to specific environmental conditions and manufacturing requirements. This breakthrough not only provided a viable solution for reducing plastic waste but also sets the stage for ongoing innovation in the field of engineered living materials, paving the way for a more sustainable future.
Nicole Imeson is a technology writer in Calgary, Alta.
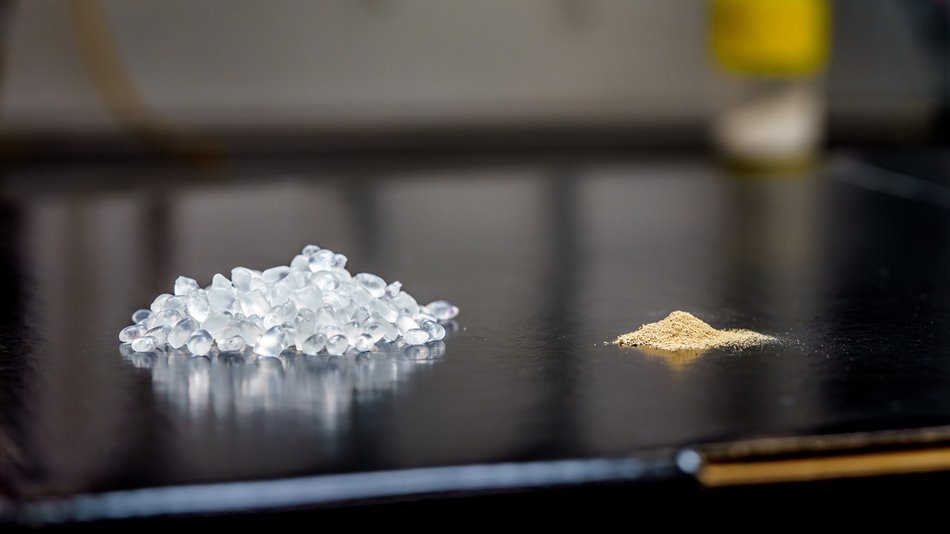
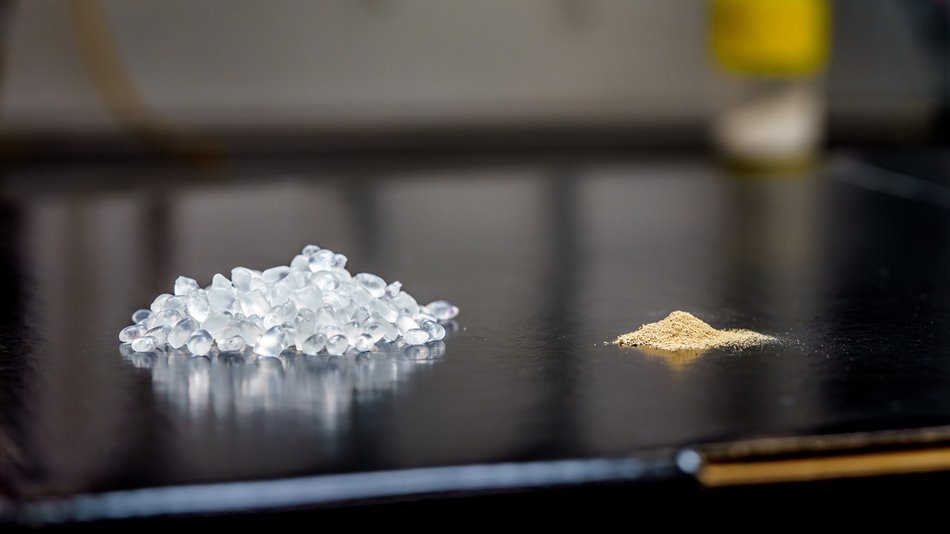