Catalyzing a Solution for Plastic Waste
Catalyzing a Solution for Plastic Waste
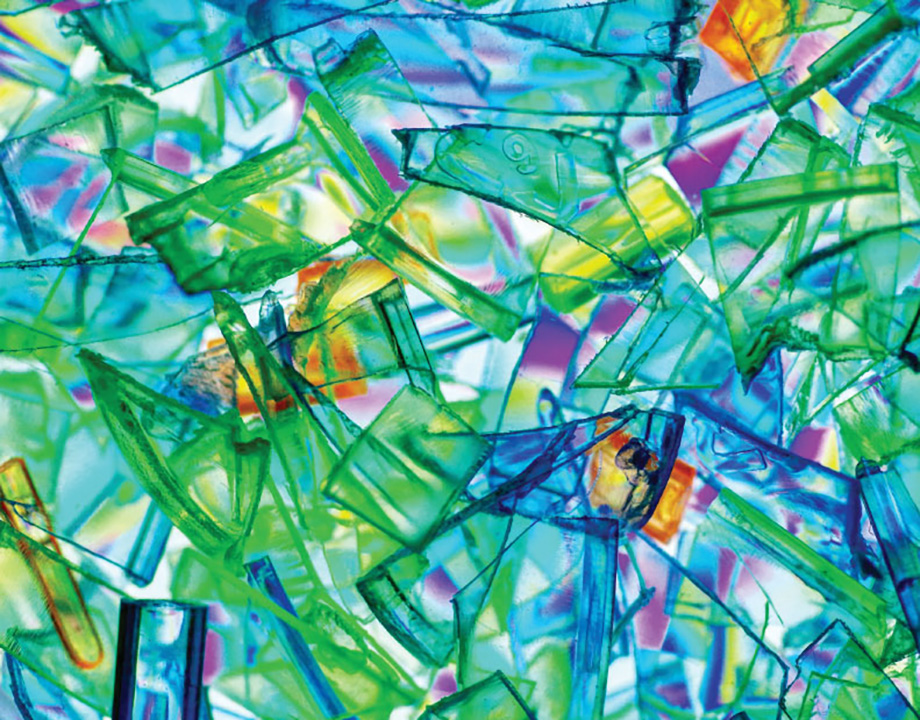
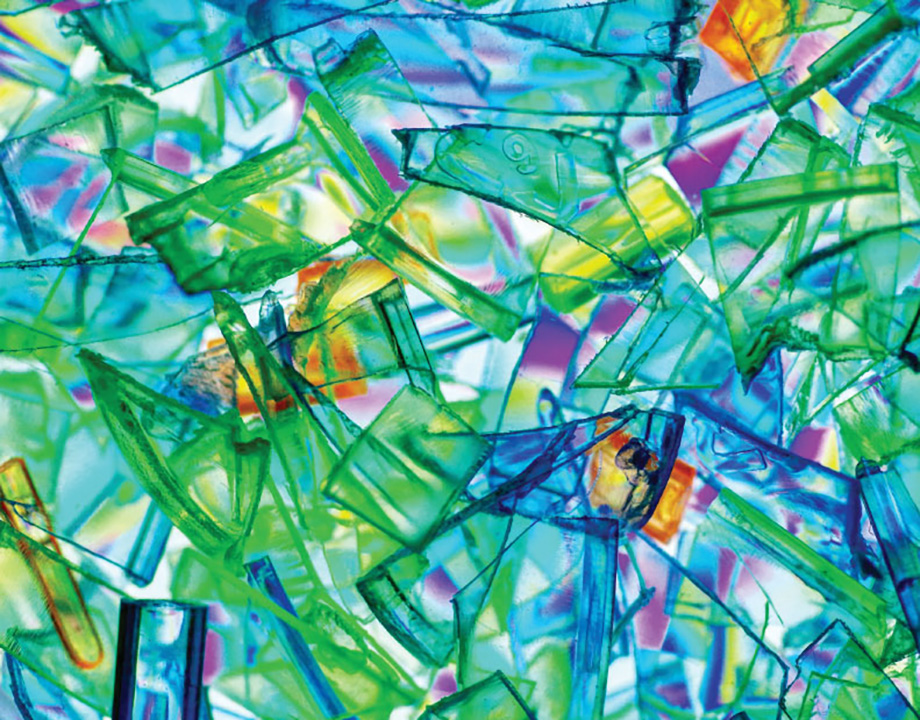
Chemical recycling can divert plastics from the environment and landfills and create new and valuable products that displace virgin materials.
Plastics are an incredible class of materials. Engineers and chemists start with simple hydrocarbon chains and manipulate them to produce new substances with properties difficult to find in nature. From high-strength Kevlar and low-friction Teflon to humble styrene foam, plastics are integral to the modern world. Furthermore, studies have shown that society’s use of plastic in some applications that traditionally used metal or glass has resulted in reduced environmental impacts.
Plastic is manufactured as a direct result of demand by businesses and consumers. Because plastics are produced in large volumes—an October 2020 paper in Science Advances estimated global production in 2016 to be 422 million tons—management of plastic waste and litter is becoming a serious problem. The same October 2020 paper estimated that the United States produced 42 million tons of plastic waste in 2016, or 130 kg per capita. While some of that waste is recycled or combusted with energy recovery, the Environmental Protection Agency reports that around three-quarters of plastic waste is simply buried in landfills; an unknown fraction escapes into the wider environment and is washed into the oceans.
Policymakers are reviewing proposals to minimize plastic waste and litter, from bans on single-use plastic bags to deposits on plastic beverage bottles. Often, the policy solution is to step up recycling. It is important for policymakers to understand, however, that traditional mechanical recycling will not by itself achieve the time-restricted goals set by most municipalities and environmental organizations.
According to a 2017 study that some colleagues and I published in Waste and Biomass Valorization, even in an ideal scenario where a municipal recycling center receives an uncontaminated polypropylene (PP) and high-density polyethylene (HDPE) stream, the best recycling rate will be 73 percent due to technology inefficiencies. In a real-world illustration of the limits of recycling, New York has one of the best curbside collection and citizen participation rates in the United States for plastic recovery but still achieves a recycling rate of only 48 percent of plastic placed in the blue bins. These are just two of many examples which clearly indicate mechanical recycling cannot be expected to manage all the plastics which enter the waste stream.
To meet the ambitious targets ahead of us, all possible processes and technologies must be considered to ensure end-of-life plastics are not disposed in landfills. A set of technologies worth investigating are some relatively new ones that repurpose used plastics into new products, including new plastics, industrial products, and transportation fuels.
Technologies that break down used plastics into their chemical building blocks to create new products are broadly referred to as “chemical recycling” and complement current mechanical recycling efforts. In addition to creating new products, these technologies keep these plastic materials circulating within the existing infrastructure and economy. The process of breaking down the plastics into their building blocks is basically reversing the assembly process. This can help to decontaminate some plastics, making their recycling more valuable.
More about Materials: Making a Greener Catalyst
There has been much public discourse about the promise, merit, and drawbacks of chemical recycling—however, it can only be fully understood through careful analysis of the results from scientific studies. Some organizations are concerned that the promise of chemical recycling is a myth and may actually exacerbate environmental impacts. The body of knowledge and evidence developed by engineers, scientists, and practitioners demonstrates that these concerns not supported.
What most people think of as plastic recycling is mechanical recycling. Mechanical processes, such as grinding, regranulating, and compounding, are used to reprocess the materials; the polymers stay intact. This works well for specific resins and forms like bottles and containers (think of resin identification code numbers 1 and 2), and it is well-suited to produce plastics for new durable uses such as pipe, railroad ties, lawn furniture, and pallets.
However, other plastics (such as multi-layer food packaging) are difficult to sort and impossible to process in today’s mechanical recycling facilities. When those streams are processed through a mechanical recycling facility, a huge amount of waste is generated at the end of the process, and this would typically be landfilled or combusted for energy.
Chemical recycling offers an alternative for those waste streams and offers a second life for the plastic as a renewed useful end product. In chemical recycling, the plastic material undergoes a set of changes at the molecular level that affects the polymer structure. The processes are varied; such as decomposition of mixed plastics into fuels via pyrolysis and other processes, depolymerization of single polymers into their monomers and raw materials, or the repolymerization of decomposed polymers to produce essentially virgin materials. Although processes such as repolymerization are technically challenging, they are achievable, and since they use “waste” plastics as the feedstock, the processes simultaneously reduce the use of petrochemicals and divert used plastics from the environment.
Among the end products for chemical recycling processes are feedstocks for new plastics, which can be utilized in a multitude of plastic manufacturing applications; chemicals such as methanol found in windshield wiper fluid; and valuable products such as wax that can be utilized in roofing and candles. The recycled plastics can also be converted into fuels for jets, diesel trucks, heating units, and any other machine that consumes petroleum-derived fuels.
Neither mechanical recycling or chemical recycling is “better” than the other; instead, each has a unique use-case depending on the plastic waste stream and the output needed. For instance, it is challenging to use mechanically recycled plastics in food-contact applications and packaging, whereas chemical recycling allows for added purification making waste plastics suitable for food contact.
Green Technology: 5 Ways to Make Roads More Sustainable
Chemical recycling does require an energy input and is competing against the plastics industry with ready access to raw petrochemicals. Many observers will bring up economics: Is chemical recycling a viable business? It is, as long as the business model contains three important elements. The first two are a suitable technology and access to an untapped waste stream of used plastics—both of which exist. There are quite a few examples of chemical recycling technologies that have been deployed economically in various industrial processes, including the production of industrial waxes, and more processes continue to come online.
The third element is more uncertain: Is there a demand for the end products of the process at a price that covers all costs? That third element is rapidly developing as today’s business climate demands materials made from recycled content to help meet sustainability goals. Mechanical recycling will allow for a portion of that demand to be met, but not all. Remaking plastics from used plastics (repolymerization) will help businesses to meet their recycled content goals and to reduce their dependence on virgin material.
Today’s chemical recycling businesses vary in their maturity, but all have demonstrated practical viability. Recent studies have demonstrated great opportunities for chemical recycling, both at home and abroad. For example, a 2019 report by the Closed Loop Partners, an organization that invests in the development of the circular economy, found there is tremendous demand for the products of chemical recycling. So, while many chemical recycling companies are young, they are maturing quickly as the growth in demand for their outputs continues.
As is common with relatively new technologies, especially ones involving industrial processes, there is some skepticism concerning chemical recycling beyond its economic viability. Specifically, environmental factors are often raised when assessing chemical recycling, with the statement that the advantages over other forms of recycling or disposal are actually a form of what is called “greenwashing.”
Greenwashing refers to efforts to obscure environmental realities by painting a misleading picture. In this instance, the charge is that the term “chemical recycling” uses an environmentally friendly term (recycling) to describe a polluting industrial process. In this instance, however, the chemicals actually are being recycled—there is no sleight of hand in the description—although the term doesn’t fully describe the wide variety of technologies, processes, and end products involved. It is a term that differentiates the technology from the more widely known recycling processes that use mechanical technologies to recycle used plastics. Others use the terms “advanced recycling and recovery” or “transformational technologies” interchangeably with chemical recycling; it’s all the same.
Another issue that many cite is that converting used plastics into fuel damages the environment. Converting plastics to fuel is just one of the processes defined by chemical recycling. Since plastics contain a certain inherent energy the capturing and usage of that energy is environmentally beneficial compared to the alternative of landfilling. The process allows the energy captured in the original petroleum and natural gas hydrocarbons to have two uses: first as the plastic product, and then fuel. Therefore, converting used plastics into valuable transportation fuels reduces the need to extract natural resources to create “virgin” fuels and avoids the associated environmental impacts.
Effectively, this process takes back the inherent energy that was used to make the product and repurposes it in a beneficial use.
Emissions release is an important facet of fuel production from plastics. Yet, all facilities (manufacturing facilities, restaurants, factories, homes, hospitals, government offices, and more) produce emissions. Chemical recycling is a manufacturing process: raw materials (waste plastics) are processed to make new products. Like all manufacturing processes, there is a potential for emissions, so the process is monitored and controlled to ensure emissions are below the U.S. EPA and state regulatory limits. These processes are monitored not only by the manufacturer, but also by state and federal authorities.
Interestingly, emissions from facilities that use a common chemical recycling technology (pyrolysis) were typically found to be lower compared to many industrial and commercial facilities, such as food manufacturing, hospitals, and universities. Pyrolysis results in a non-hazardous solid byproduct that can be managed similarly to other solid waste, resulting in waste reduction of approximately 90 percent.
Another important consideration about chemical recycling is that it allows for avoidance of emissions that would be generated if new plastic material or fuels needed to be manufactured from extraction of natural resources.
(The production of fuels from chemicals should not be confused with incineration of plastics. Incineration refers to destroying waste materials by burning, without any provision for recovering energy or materials. This is a separate process. There are facilities that can recover the energy and materials through combustion called waste-to-energy [WTE].)
Editor's Choice: How Are Robots Helping Us to Recycle Better
It is important not to make broad assumptions about chemical recycling technologies, processes, costs, efficiencies, and environmental profiles. Each technology is different and has advantages and challenges just as mechanical recycling does. Instead, keep in mind that the ultimate goal is to ensure that plastics are properly collected and managed after they have gone through their useful life.
Plastic manufacturers produce materials to meet customers’ demands. They can easily produce plastics from virgin feedstocks or renewed plastic feedstocks that result from chemical recycling. Many of these manufacturers have committed to increase the amount of recycled plastics they use, to meet their customers’ demands and sustainability pledges. These companies also realize that mechanical recycling is useful but obviously cannot handle all the plastic waste. So, these companies promote chemical recycling to complement existing mechanical recycling efforts.
In combination with mechanical recycling methods, chemical recycling may help lead to a circular economy for plastics, in which used plastics are repurposed rather than disposed, keeping plastics out of the environment and harnessing their inherent value to create new products. It may be beyond the scope of the technology to eliminate virgin feedstocks entirely, but a robust chemical recycling sector would be able to substantially reduce the volume of new material necessary to support the plastics industry.
Virtually every stakeholder, whether they are manufacturers, consumers, or nongovernmental organizations, recognizes that plastic waste in the environment is a huge problem. Chemical recycling does offer a net-positive solution to this problem by effectively diverting plastics from the environment and creating new and valuable products that displace virgin materials. It has some additional benefits, such as reducing net greenhouse gas emissions.
The technology is now available, but not at the scale or level of development needed to meet the challenge of waste plastics pollution today. Chemical recycling cannot develop quickly enough without initial capital investment.
However, public incentives can help catalyze the quick development of these processes and technologies that might otherwise take years to develop and mature. This would be a worthwhile public investment: Chemical recycling companies can extract value from a resource which would otherwise simply end in a landfill or our oceans, and by doing so, create jobs and bring tax revenues to communities. It is absolutely logical to explore public policies and incentives that encourage these technologies to develop more quickly.
Marco J. Castaldi is an ASME Fellow and a professor of chemical engineering at the City College of New York. He is also director of CCNY’s Earth System Science and Environmental Engineering program and the Earth Engineering Center.
Plastic is manufactured as a direct result of demand by businesses and consumers. Because plastics are produced in large volumes—an October 2020 paper in Science Advances estimated global production in 2016 to be 422 million tons—management of plastic waste and litter is becoming a serious problem. The same October 2020 paper estimated that the United States produced 42 million tons of plastic waste in 2016, or 130 kg per capita. While some of that waste is recycled or combusted with energy recovery, the Environmental Protection Agency reports that around three-quarters of plastic waste is simply buried in landfills; an unknown fraction escapes into the wider environment and is washed into the oceans.
Policymakers are reviewing proposals to minimize plastic waste and litter, from bans on single-use plastic bags to deposits on plastic beverage bottles. Often, the policy solution is to step up recycling. It is important for policymakers to understand, however, that traditional mechanical recycling will not by itself achieve the time-restricted goals set by most municipalities and environmental organizations.
According to a 2017 study that some colleagues and I published in Waste and Biomass Valorization, even in an ideal scenario where a municipal recycling center receives an uncontaminated polypropylene (PP) and high-density polyethylene (HDPE) stream, the best recycling rate will be 73 percent due to technology inefficiencies. In a real-world illustration of the limits of recycling, New York has one of the best curbside collection and citizen participation rates in the United States for plastic recovery but still achieves a recycling rate of only 48 percent of plastic placed in the blue bins. These are just two of many examples which clearly indicate mechanical recycling cannot be expected to manage all the plastics which enter the waste stream.
To meet the ambitious targets ahead of us, all possible processes and technologies must be considered to ensure end-of-life plastics are not disposed in landfills. A set of technologies worth investigating are some relatively new ones that repurpose used plastics into new products, including new plastics, industrial products, and transportation fuels.
Technologies that break down used plastics into their chemical building blocks to create new products are broadly referred to as “chemical recycling” and complement current mechanical recycling efforts. In addition to creating new products, these technologies keep these plastic materials circulating within the existing infrastructure and economy. The process of breaking down the plastics into their building blocks is basically reversing the assembly process. This can help to decontaminate some plastics, making their recycling more valuable.
More about Materials: Making a Greener Catalyst
There has been much public discourse about the promise, merit, and drawbacks of chemical recycling—however, it can only be fully understood through careful analysis of the results from scientific studies. Some organizations are concerned that the promise of chemical recycling is a myth and may actually exacerbate environmental impacts. The body of knowledge and evidence developed by engineers, scientists, and practitioners demonstrates that these concerns not supported.
Sorting It Out
What most people think of as plastic recycling is mechanical recycling. Mechanical processes, such as grinding, regranulating, and compounding, are used to reprocess the materials; the polymers stay intact. This works well for specific resins and forms like bottles and containers (think of resin identification code numbers 1 and 2), and it is well-suited to produce plastics for new durable uses such as pipe, railroad ties, lawn furniture, and pallets.
However, other plastics (such as multi-layer food packaging) are difficult to sort and impossible to process in today’s mechanical recycling facilities. When those streams are processed through a mechanical recycling facility, a huge amount of waste is generated at the end of the process, and this would typically be landfilled or combusted for energy.
Chemical recycling offers an alternative for those waste streams and offers a second life for the plastic as a renewed useful end product. In chemical recycling, the plastic material undergoes a set of changes at the molecular level that affects the polymer structure. The processes are varied; such as decomposition of mixed plastics into fuels via pyrolysis and other processes, depolymerization of single polymers into their monomers and raw materials, or the repolymerization of decomposed polymers to produce essentially virgin materials. Although processes such as repolymerization are technically challenging, they are achievable, and since they use “waste” plastics as the feedstock, the processes simultaneously reduce the use of petrochemicals and divert used plastics from the environment.
Among the end products for chemical recycling processes are feedstocks for new plastics, which can be utilized in a multitude of plastic manufacturing applications; chemicals such as methanol found in windshield wiper fluid; and valuable products such as wax that can be utilized in roofing and candles. The recycled plastics can also be converted into fuels for jets, diesel trucks, heating units, and any other machine that consumes petroleum-derived fuels.
Neither mechanical recycling or chemical recycling is “better” than the other; instead, each has a unique use-case depending on the plastic waste stream and the output needed. For instance, it is challenging to use mechanically recycled plastics in food-contact applications and packaging, whereas chemical recycling allows for added purification making waste plastics suitable for food contact.
Green Technology: 5 Ways to Make Roads More Sustainable
Chemical recycling does require an energy input and is competing against the plastics industry with ready access to raw petrochemicals. Many observers will bring up economics: Is chemical recycling a viable business? It is, as long as the business model contains three important elements. The first two are a suitable technology and access to an untapped waste stream of used plastics—both of which exist. There are quite a few examples of chemical recycling technologies that have been deployed economically in various industrial processes, including the production of industrial waxes, and more processes continue to come online.
The third element is more uncertain: Is there a demand for the end products of the process at a price that covers all costs? That third element is rapidly developing as today’s business climate demands materials made from recycled content to help meet sustainability goals. Mechanical recycling will allow for a portion of that demand to be met, but not all. Remaking plastics from used plastics (repolymerization) will help businesses to meet their recycled content goals and to reduce their dependence on virgin material.
Today’s chemical recycling businesses vary in their maturity, but all have demonstrated practical viability. Recent studies have demonstrated great opportunities for chemical recycling, both at home and abroad. For example, a 2019 report by the Closed Loop Partners, an organization that invests in the development of the circular economy, found there is tremendous demand for the products of chemical recycling. So, while many chemical recycling companies are young, they are maturing quickly as the growth in demand for their outputs continues.
Environmental Impact
As is common with relatively new technologies, especially ones involving industrial processes, there is some skepticism concerning chemical recycling beyond its economic viability. Specifically, environmental factors are often raised when assessing chemical recycling, with the statement that the advantages over other forms of recycling or disposal are actually a form of what is called “greenwashing.”
Greenwashing refers to efforts to obscure environmental realities by painting a misleading picture. In this instance, the charge is that the term “chemical recycling” uses an environmentally friendly term (recycling) to describe a polluting industrial process. In this instance, however, the chemicals actually are being recycled—there is no sleight of hand in the description—although the term doesn’t fully describe the wide variety of technologies, processes, and end products involved. It is a term that differentiates the technology from the more widely known recycling processes that use mechanical technologies to recycle used plastics. Others use the terms “advanced recycling and recovery” or “transformational technologies” interchangeably with chemical recycling; it’s all the same.
Another issue that many cite is that converting used plastics into fuel damages the environment. Converting plastics to fuel is just one of the processes defined by chemical recycling. Since plastics contain a certain inherent energy the capturing and usage of that energy is environmentally beneficial compared to the alternative of landfilling. The process allows the energy captured in the original petroleum and natural gas hydrocarbons to have two uses: first as the plastic product, and then fuel. Therefore, converting used plastics into valuable transportation fuels reduces the need to extract natural resources to create “virgin” fuels and avoids the associated environmental impacts.
Effectively, this process takes back the inherent energy that was used to make the product and repurposes it in a beneficial use.
Emissions release is an important facet of fuel production from plastics. Yet, all facilities (manufacturing facilities, restaurants, factories, homes, hospitals, government offices, and more) produce emissions. Chemical recycling is a manufacturing process: raw materials (waste plastics) are processed to make new products. Like all manufacturing processes, there is a potential for emissions, so the process is monitored and controlled to ensure emissions are below the U.S. EPA and state regulatory limits. These processes are monitored not only by the manufacturer, but also by state and federal authorities.
Interestingly, emissions from facilities that use a common chemical recycling technology (pyrolysis) were typically found to be lower compared to many industrial and commercial facilities, such as food manufacturing, hospitals, and universities. Pyrolysis results in a non-hazardous solid byproduct that can be managed similarly to other solid waste, resulting in waste reduction of approximately 90 percent.
Another important consideration about chemical recycling is that it allows for avoidance of emissions that would be generated if new plastic material or fuels needed to be manufactured from extraction of natural resources.
(The production of fuels from chemicals should not be confused with incineration of plastics. Incineration refers to destroying waste materials by burning, without any provision for recovering energy or materials. This is a separate process. There are facilities that can recover the energy and materials through combustion called waste-to-energy [WTE].)
Editor's Choice: How Are Robots Helping Us to Recycle Better
It is important not to make broad assumptions about chemical recycling technologies, processes, costs, efficiencies, and environmental profiles. Each technology is different and has advantages and challenges just as mechanical recycling does. Instead, keep in mind that the ultimate goal is to ensure that plastics are properly collected and managed after they have gone through their useful life.
Worthwhile Investments
Plastic manufacturers produce materials to meet customers’ demands. They can easily produce plastics from virgin feedstocks or renewed plastic feedstocks that result from chemical recycling. Many of these manufacturers have committed to increase the amount of recycled plastics they use, to meet their customers’ demands and sustainability pledges. These companies also realize that mechanical recycling is useful but obviously cannot handle all the plastic waste. So, these companies promote chemical recycling to complement existing mechanical recycling efforts.
In combination with mechanical recycling methods, chemical recycling may help lead to a circular economy for plastics, in which used plastics are repurposed rather than disposed, keeping plastics out of the environment and harnessing their inherent value to create new products. It may be beyond the scope of the technology to eliminate virgin feedstocks entirely, but a robust chemical recycling sector would be able to substantially reduce the volume of new material necessary to support the plastics industry.
Virtually every stakeholder, whether they are manufacturers, consumers, or nongovernmental organizations, recognizes that plastic waste in the environment is a huge problem. Chemical recycling does offer a net-positive solution to this problem by effectively diverting plastics from the environment and creating new and valuable products that displace virgin materials. It has some additional benefits, such as reducing net greenhouse gas emissions.
The technology is now available, but not at the scale or level of development needed to meet the challenge of waste plastics pollution today. Chemical recycling cannot develop quickly enough without initial capital investment.
However, public incentives can help catalyze the quick development of these processes and technologies that might otherwise take years to develop and mature. This would be a worthwhile public investment: Chemical recycling companies can extract value from a resource which would otherwise simply end in a landfill or our oceans, and by doing so, create jobs and bring tax revenues to communities. It is absolutely logical to explore public policies and incentives that encourage these technologies to develop more quickly.
Marco J. Castaldi is an ASME Fellow and a professor of chemical engineering at the City College of New York. He is also director of CCNY’s Earth System Science and Environmental Engineering program and the Earth Engineering Center.