Portable Factory Builds New Approach to Construction
Portable Factory Builds New Approach to Construction
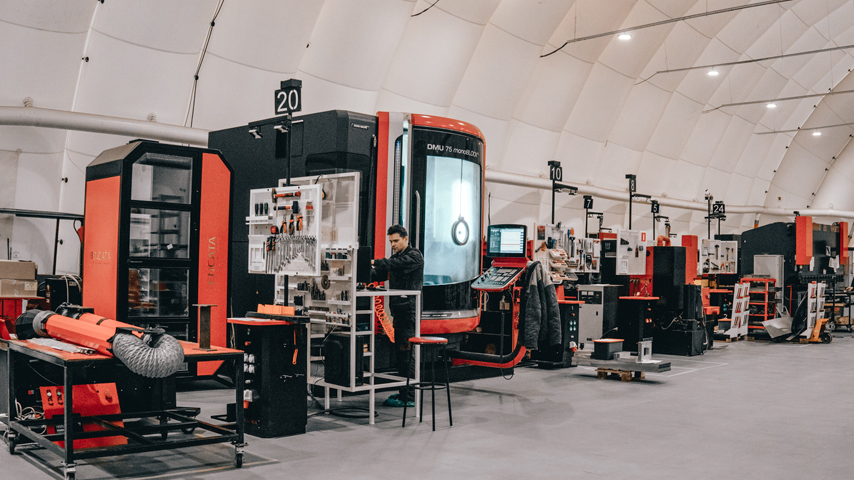
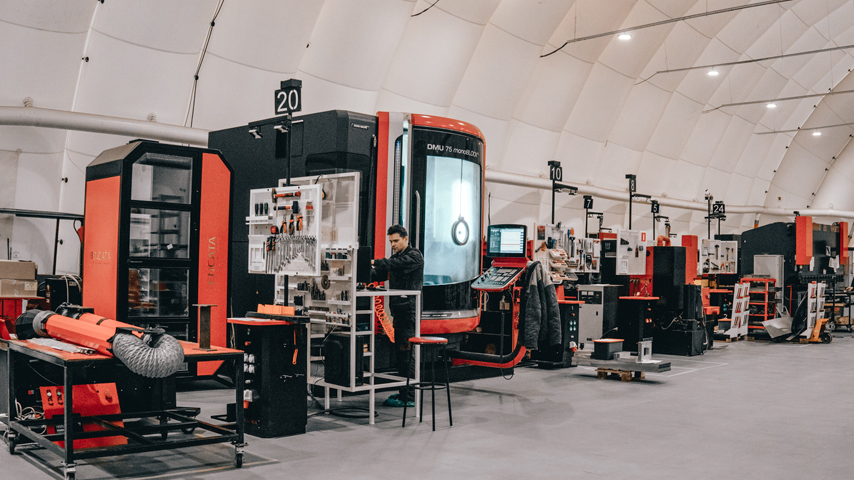
Cuby is hoping to revitalize the sector by applying lean manufacturing processes and by bringing a transportable factory (shown above) to the construction site.
More than a hundred years ago, Henry Ford introduced the moving assembly line to the process of car production and dramatically increased production efficiency. As a result, a model T could be built in 90 minutes.
The construction industry today is at a place where the automotive industry was then, argues Aleh Kandrashou, co-founder of Cuby, a startup headquartered in Wilmington, Del., that streamlines the construction process through turnkey transportable factories operating near the construction site. Part of the startup’s process derives from the relatively new modular concept in construction where a building is broken into component parts, each of which is manufactured elsewhere and then assembled onsite.
Assembly teams then put these component parts together onsite. Traditional “kit of parts” modular construction involves manufacturing component parts elsewhere and then shipping finished goods to the construction site, where it is assembled. With Cuby, the production of constructed components, thanks to the mobile factory, happens near the construction site. The final assembly for both methods still takes place at the construction site.
You Might Also Enjoy: 7 Trends Shaping Construction in 2023
Kandrashou argues that today’s construction methods should be evaluating a parameter called Manufacturing Readiness Level (MRL), which contrasts time spent on the construction site against that spent in manufacturing materials and components. For example, precast concrete has an MRL of 15 percent, which means only 15 percent of the total materials needed to construct a building with the material is made in a factory. The rest has to be done onsite, increasing time and labor costs.
“At Cuby, we have [an] MRL of roughly 75 percent to 85 percent, which means that almost everything is produced in the factory and we only have to assemble it like an IKEA model on the site,” Kandrashou said. “This is a full turkey solution starting from the raw material and ending with the final building and all finishes.”
The system leans on the modular kit-of-parts system so factory-like lean production processes can apply to building construction. It also delivers time and transportation efficiencies in bringing production close to the site. “The big problems in modular construction are transportation, labor, and scalability,” Kandrashou said. “That’s why we developed and designed a mobile factory that moves as close to the construction site and uses local materials and labor as much as possible.”
A Cuby factory can produce roughly 2,000 square feet of components per day, which means “one factory can work with 20 assembly teams and produce 20 houses a month,” Kandrashou said. A typical on-site assembly crew consists of four or five (mostly unskilled) workers. A single-family home can typically take up to 4,000 hours, but a Cuby-assisted home takes about 2,000 hours.
Software allows the portable factory to visualize the end-to-end construction manufacturing process and tweak the mechanics along the way. Cuby’s engineers have maximized workflow efficiencies as well, so when the worker reports to work, “the system gives him the exact task from the pipeline of tasks to do and based on his skills,” Kandrashou said. In turn, the logistics and transportation departments are fine-tuned to deliver the necessary amount of materials needed for any given project for today and tomorrow.
Workers go through training exercises using a virtual reality program called Unreal Engine. “Workers can pass tests and work in our virtual factory before they start in our actual factory,” Kandrashou said. This process enables Cuby to use and train local unskilled labor.
Cuby designs can accommodate close to 60 percent of the buildings constructed around the world, Kandrashou said. The startup offers options to customize buildings depending on the final sale price. “Different types of exterior and interior finishes can help you increase or decrease the level of the building so you can [cater to all categories] of housing,” Kandrashou said.
Become a Member: How to Join ASME
Projects using Cuby portable factories are underway in Europe and the United States, and the company is targeting big developers with its turnkey concept. The startup is focused on “building to help improve the technology and test prototypes,” said Kandrashou, who lives with his family in a Cuby-constructed home in eastern Europe.
The firm’s operating principle is close to what Jim Barrett, chief innovation officer at Turner Construction Company, sees as the future of construction. “By 2050, much less work will be happening on the actual construction site. We will probably have a network of sites where most of the fabrication, assembly, and installation happens,” he said.
Poornima Apte is a technology writer in Walpole, Mass.
The construction industry today is at a place where the automotive industry was then, argues Aleh Kandrashou, co-founder of Cuby, a startup headquartered in Wilmington, Del., that streamlines the construction process through turnkey transportable factories operating near the construction site. Part of the startup’s process derives from the relatively new modular concept in construction where a building is broken into component parts, each of which is manufactured elsewhere and then assembled onsite.
Kit of parts with a twist
Cuby factories incorporate lean manufacturing techniques—Kandrashou has years of experience in the process—to produce a combination of building components like doors and windows, wall units, and more. The startup has 300 SKUs in its library from which to choose.Assembly teams then put these component parts together onsite. Traditional “kit of parts” modular construction involves manufacturing component parts elsewhere and then shipping finished goods to the construction site, where it is assembled. With Cuby, the production of constructed components, thanks to the mobile factory, happens near the construction site. The final assembly for both methods still takes place at the construction site.
You Might Also Enjoy: 7 Trends Shaping Construction in 2023
Kandrashou argues that today’s construction methods should be evaluating a parameter called Manufacturing Readiness Level (MRL), which contrasts time spent on the construction site against that spent in manufacturing materials and components. For example, precast concrete has an MRL of 15 percent, which means only 15 percent of the total materials needed to construct a building with the material is made in a factory. The rest has to be done onsite, increasing time and labor costs.
“At Cuby, we have [an] MRL of roughly 75 percent to 85 percent, which means that almost everything is produced in the factory and we only have to assemble it like an IKEA model on the site,” Kandrashou said. “This is a full turkey solution starting from the raw material and ending with the final building and all finishes.”
Turnkey production efficiencies
Cuby sells the portable factory itself, along with its production machines, which construction companies can then use to manufacture SKUs according to their own designs.The system leans on the modular kit-of-parts system so factory-like lean production processes can apply to building construction. It also delivers time and transportation efficiencies in bringing production close to the site. “The big problems in modular construction are transportation, labor, and scalability,” Kandrashou said. “That’s why we developed and designed a mobile factory that moves as close to the construction site and uses local materials and labor as much as possible.”
A Cuby factory can produce roughly 2,000 square feet of components per day, which means “one factory can work with 20 assembly teams and produce 20 houses a month,” Kandrashou said. A typical on-site assembly crew consists of four or five (mostly unskilled) workers. A single-family home can typically take up to 4,000 hours, but a Cuby-assisted home takes about 2,000 hours.
Software allows the portable factory to visualize the end-to-end construction manufacturing process and tweak the mechanics along the way. Cuby’s engineers have maximized workflow efficiencies as well, so when the worker reports to work, “the system gives him the exact task from the pipeline of tasks to do and based on his skills,” Kandrashou said. In turn, the logistics and transportation departments are fine-tuned to deliver the necessary amount of materials needed for any given project for today and tomorrow.
Workers go through training exercises using a virtual reality program called Unreal Engine. “Workers can pass tests and work in our virtual factory before they start in our actual factory,” Kandrashou said. This process enables Cuby to use and train local unskilled labor.
The future of construction
A conveyor belt process of manufacturing construction parts reduces waste, Kandrashou said. Decreased transportation costs for finished goods also help. He estimates the process reduces carbon emissions by around three times more than traditional equivalents. In addition, Cuby is investing in research and development to make eco panels with silver grass, which shows promise in absorbing more carbon dioxide than what was produced during construction of a building.Cuby designs can accommodate close to 60 percent of the buildings constructed around the world, Kandrashou said. The startup offers options to customize buildings depending on the final sale price. “Different types of exterior and interior finishes can help you increase or decrease the level of the building so you can [cater to all categories] of housing,” Kandrashou said.
Become a Member: How to Join ASME
Projects using Cuby portable factories are underway in Europe and the United States, and the company is targeting big developers with its turnkey concept. The startup is focused on “building to help improve the technology and test prototypes,” said Kandrashou, who lives with his family in a Cuby-constructed home in eastern Europe.
The firm’s operating principle is close to what Jim Barrett, chief innovation officer at Turner Construction Company, sees as the future of construction. “By 2050, much less work will be happening on the actual construction site. We will probably have a network of sites where most of the fabrication, assembly, and installation happens,” he said.
Poornima Apte is a technology writer in Walpole, Mass.