Building the Factory of the Future: Leveraging New Technologies for the Engineering Workforce
Building the Factory of the Future: Leveraging New Technologies for the Engineering Workforce
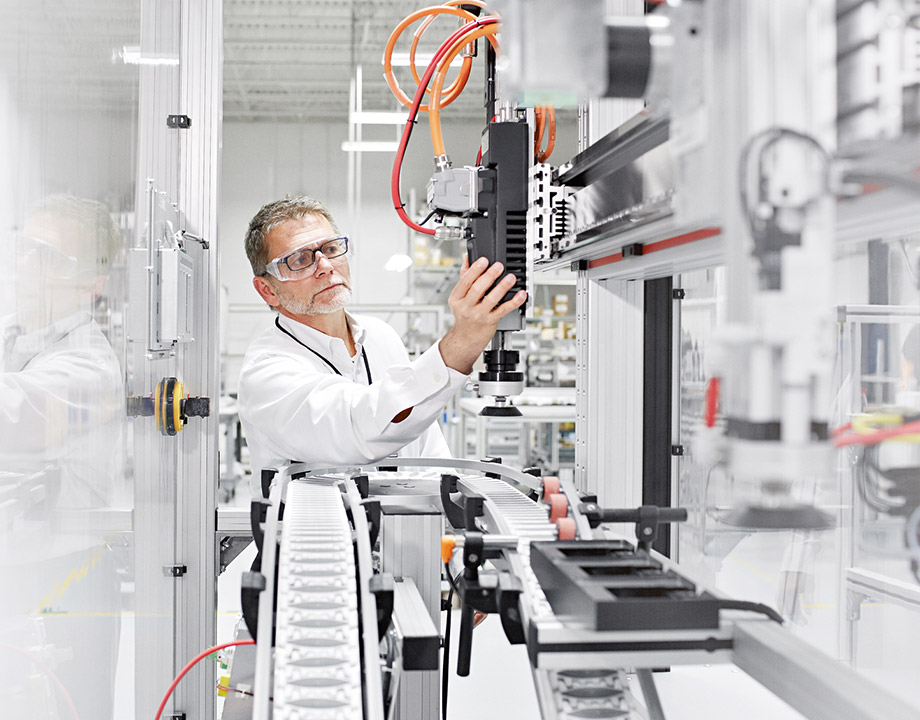
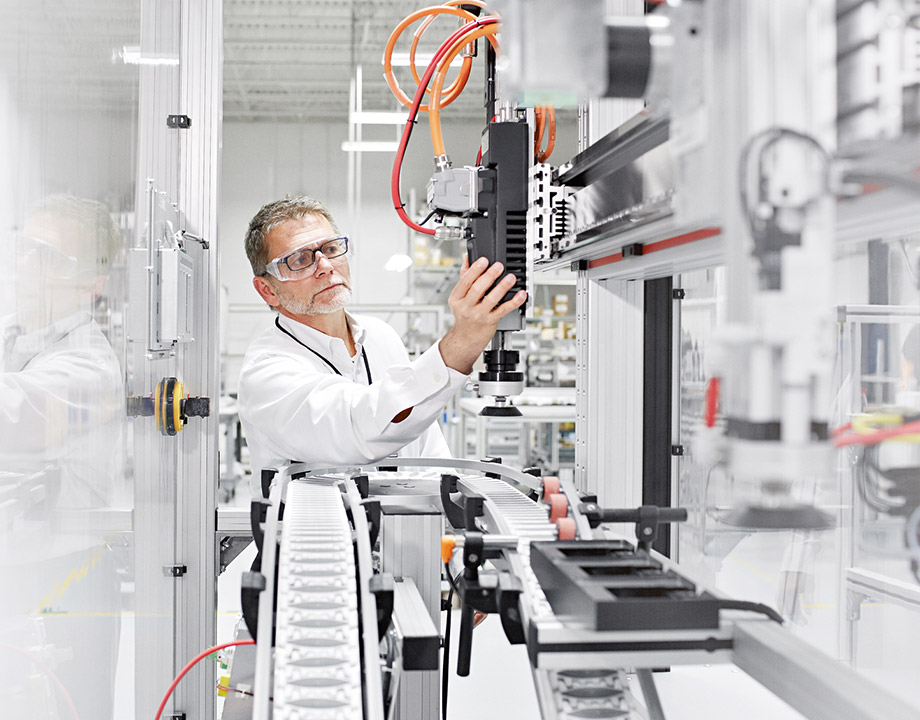
Today’s manufacturing and automation engineers, whether they are young or seasoned veterans, can make full use of IoT technology by building a step-by-step approach toward the Factory of the Future.
Today’s manufacturing and automation industry segments are constantly leveraging new technologies and processes to help them become more agile, more responsive to fast-changing global markets, and more innovative in the products and solutions they offer.
These new technologies are often grouped into the concept of the Internet of Things (IoT). Or, depending on the industry and location, they can also be referred to as Industry 4.0, Industrial IoT, or the Factory of the Future. Whatever the name, they all offer the potential to revolutionize global manufacturing operations, and their rapid adoption is already having a significant impact on many industries.
There’s also another “new” element to consider in current manufacturing environments: a new generation of engineers, many of whom are entering the industrial workplace with skills, backgrounds, and experiences that are significantly different from previous cohorts of manufacturing engineers.
Whether they’re experienced engineers or part of a newer generation that just launched their professional careers, today’s manufacturing and automation engineers can make full use of IoT technology by targeting key productivity, throughput or quality issues and building a step-by-step approach to make smart, incremental investments to move forward on the path to the Factory of the Future.
IoT technologies are already impacting major areas of industrial production and operations:
In the Factory of the Future, everything is connected, from the individual machine components with embedded sensors and intelligence up through machine-level and plant-level communications architectures to a cloud-based solution. Sophisticated software collects, transfers, and processes data in ways to provide both production transparency and actionable answers to inefficient workflows, including bottlenecks and equipment downtime.
Learn More About: The State of American Manufacturing 2019
Many manufacturing plants contain a mix of new and legacy equipment with little or no intelligent controls, sensors, or communications capabilities to state-of-the-art systems fully equipped for IoT operation. To transform production systems — for both existing equipment and new hardware — unifying them under one connected network and the collection of data play a crucial role.
You may begin by asking, "Where is my value? Where can I gain the most in productivity?” Start by focusing on production bottlenecks and quality issues. For example, a production part consistently has quality issues and high scrap rates.
Improving connectivity between production units and upgrading sensors can help provide the data. Many plants today have island productions, where the production steps are isolated from one another. Connecting the islands via a unified data link can improve productivity.
To decide what sensors to install and what type of data to collect, start by applying lean principles. Mapping the value stream, identifying where time is wasted and scrap is created are key metrics to analyze. Senior engineers have long-standing experience with lean manufacturing programs, and key help indicates key areas of data collection for IoT sensors.
On the manufacturing floor, lean principles can be used to point to where initial investments in sensor and data-collecting technologies can have the greatest impact. By applying simple sensors and simple data storage for these targeted, high-level, high-volume areas, you collect historical data and start visualizing it. It also provides the right framework for capturing and analyzing historical and trending production data for a more detailed and comprehensive approach to understanding how to improve operations.
Find Out What’s New: Infographic on The Evolution of the Modern Factory
There is a new generation of tools now available for managing and improving how that data, once captured, is managed and analyzed in real-time. Production performance software is designed to help users visualize data in real time and can track many different sensors installed in production lines to measure data such as temperature, flow, pressure, vibrations, torque, sounds, and other operating characteristics.
For example, smart servo drives can capture feedback data on motion characteristics, such as torque and velocity. This data can be integrated with data from other devices and sensors to assess whether the load or resistance on a particular axis matches established parameters, or whether there are mechanical issues that need to be addressed.
That information is needed to apply continuous improvement process (CIP) tools that will gain value and correct your quality, cost, or wasted time and effort issues. This approach can be applied to a range of production systems, not just the legacy ones with minimal sensors and connectivity. You can begin with sensors, but many machines also have smart motion drives and controls to deepen and enrich the data you’re capturing.
As manufacturers augment sensors, data collection, and connectivity, machine by machine or production cell by production cell, there is the risk of “too much data, not enough insight.” One reason some companies resist investing in IoT technology is the fear that they will be overwhelmed by a mountain of data and not know how to extract the right insights to improve their performance.
It’s a legitimate concern. With the massive amount of data collected, configuring how information is captured and channeled is just as important. A logical step to consider is embedding an intelligent “edge” or gateway that collects the right data from the factory floor.
These gateways normalize the data streams to give you a coherent and actionable portrait of your production in real-time. For example, an IoT Gateway is a combined software/hardware platform that makes it easy to perform real-time monitoring of process data, such as temperature, pressure, vibration, power consumption, or other parameters. It is designed for easier setup without intervening in the automation logic.
Recommended for You: Making Sense of Real-Time Factory Data
Data can be centralized at the plant level with local machine state monitoring systems and eventually scale up to using the gateway to connect all production locations through the cloud and utilizing cloud-based analytical tools. With these tools, it is now possible to have much more data-driven solutions to help companies improve several critical productivity tools and strategic programs. These include predictive maintenance with better insight into machine service, data analytics for smarter use of production data and decision making, and visualization and notification of production data in real-time for production planning and quality data management.
Using the data from across the enterprise better quantifies the overall equipment effectiveness (OEE) and compares different production platforms to help guide investments in future equipment
Ultimately, solid historical data and better insight from cloud-based analytical tools lead to better business intelligence and enterprise-wide strategic planning; addressing long-range investments in new production systems, plants, personnel, and markets.
The current generation of engineers entering manufacturing operations have backgrounds and experiences that differ in many ways from those engineers who have 20 to 30 years on the job. Mechanical engineers fresh out of school grew up surrounded by and interacting with digital information technologies.
They are much more used to having in-depth data on hand to make decisions. They use computer-aided design tools, 3D simulations of systems, and virtual prototypes of components or devices before even fabricating an actual prototype. They most likely have also taken basic programming classes and have experience with commercial programming languages and designing and programming user interfaces, as opposed to standard PLC programming methods using ladder logic.
They also tend to be much more experienced with thinking about and designing systems that are networked and highly connected. That means they may assume that technology incorporates the ability to connect with other systems and share data horizontally and vertically, including the use of cloud-based applications and artificial intelligence-type systems.
In contrast, there are large segments of today’s manufacturing systems that are less networked and data-rich than the new generation of engineers might expect. The older engineering staff in these operations draw more on their experience designing, building, and running these systems to a significant degree, compensating for the comparative dearth of information. These more experienced engineers know their machines: how they sound, how products move through the equipment, and where potential choke points, common areas of stress and potential breakdowns are located.
Combining the skills and expertise of both veteran and new engineers can help companies implement IoT technologies more effectively as they seek to build the Factory of the Future. The older generation of engineers can contribute their experience and insights about how existing manufacturing systems perform, while the newer generation can contribute their skills at organizing and analyzing data and optimizing how digital technology like sensors, visualization systems, and controls can be leveraged to the maximum value.
Editors’ Pick: Experience Faster Internet at AT&T’s 5G Manufacturing Zone
It’s important to appreciate that the Factory of the Future is already being built. Seasoned engineers and the new generation just joining today’s manufacturing companies both have important contributions to make. Together they can chart a scalable, step-by-step approach that adds the layers of sensors, intelligence, and connectivity to existing manufacturing platforms that can yield actionable insights to solve current issues. They can also collaborate with forward-looking OEMs and technology suppliers to determine the best way to incorporate IoT technology into the next generation of production platforms.
Peter Fischbach is industry segment manager for Bosch Rexroth U.S.
Opinions expressed are the author’s and do not necessarily reflect the views of ASME.
These new technologies are often grouped into the concept of the Internet of Things (IoT). Or, depending on the industry and location, they can also be referred to as Industry 4.0, Industrial IoT, or the Factory of the Future. Whatever the name, they all offer the potential to revolutionize global manufacturing operations, and their rapid adoption is already having a significant impact on many industries.
There’s also another “new” element to consider in current manufacturing environments: a new generation of engineers, many of whom are entering the industrial workplace with skills, backgrounds, and experiences that are significantly different from previous cohorts of manufacturing engineers.
Whether they’re experienced engineers or part of a newer generation that just launched their professional careers, today’s manufacturing and automation engineers can make full use of IoT technology by targeting key productivity, throughput or quality issues and building a step-by-step approach to make smart, incremental investments to move forward on the path to the Factory of the Future.
Starting the Factory of the Future Journey
IoT technologies are already impacting major areas of industrial production and operations:
- $28 billion is the amount of expected cost reduction in the automotive sector between 2016 and 2020 due to IoT technologies, representing a 3.9% reduction in annual costs.
- A 2.6% estimated annual reduction in inventory levels due to smart, connected IoT factory material management systems able to track inventory levels in real-time using embedded sensors and other systems.
- A 30% estimated increase in productivity could be realized by early adopters of IoT technologies, by providing real-time data to plan and manage predictive maintenance programs and intervene faster when machine sensors detect performance issues that fall outside of established thresholds.
In the Factory of the Future, everything is connected, from the individual machine components with embedded sensors and intelligence up through machine-level and plant-level communications architectures to a cloud-based solution. Sophisticated software collects, transfers, and processes data in ways to provide both production transparency and actionable answers to inefficient workflows, including bottlenecks and equipment downtime.
Learn More About: The State of American Manufacturing 2019
Many manufacturing plants contain a mix of new and legacy equipment with little or no intelligent controls, sensors, or communications capabilities to state-of-the-art systems fully equipped for IoT operation. To transform production systems — for both existing equipment and new hardware — unifying them under one connected network and the collection of data play a crucial role.
You may begin by asking, "Where is my value? Where can I gain the most in productivity?” Start by focusing on production bottlenecks and quality issues. For example, a production part consistently has quality issues and high scrap rates.
Improving connectivity between production units and upgrading sensors can help provide the data. Many plants today have island productions, where the production steps are isolated from one another. Connecting the islands via a unified data link can improve productivity.
To decide what sensors to install and what type of data to collect, start by applying lean principles. Mapping the value stream, identifying where time is wasted and scrap is created are key metrics to analyze. Senior engineers have long-standing experience with lean manufacturing programs, and key help indicates key areas of data collection for IoT sensors.
On the manufacturing floor, lean principles can be used to point to where initial investments in sensor and data-collecting technologies can have the greatest impact. By applying simple sensors and simple data storage for these targeted, high-level, high-volume areas, you collect historical data and start visualizing it. It also provides the right framework for capturing and analyzing historical and trending production data for a more detailed and comprehensive approach to understanding how to improve operations.
Find Out What’s New: Infographic on The Evolution of the Modern Factory
There is a new generation of tools now available for managing and improving how that data, once captured, is managed and analyzed in real-time. Production performance software is designed to help users visualize data in real time and can track many different sensors installed in production lines to measure data such as temperature, flow, pressure, vibrations, torque, sounds, and other operating characteristics.
For example, smart servo drives can capture feedback data on motion characteristics, such as torque and velocity. This data can be integrated with data from other devices and sensors to assess whether the load or resistance on a particular axis matches established parameters, or whether there are mechanical issues that need to be addressed.
That information is needed to apply continuous improvement process (CIP) tools that will gain value and correct your quality, cost, or wasted time and effort issues. This approach can be applied to a range of production systems, not just the legacy ones with minimal sensors and connectivity. You can begin with sensors, but many machines also have smart motion drives and controls to deepen and enrich the data you’re capturing.
Making Smart Use of the Data
As manufacturers augment sensors, data collection, and connectivity, machine by machine or production cell by production cell, there is the risk of “too much data, not enough insight.” One reason some companies resist investing in IoT technology is the fear that they will be overwhelmed by a mountain of data and not know how to extract the right insights to improve their performance.
It’s a legitimate concern. With the massive amount of data collected, configuring how information is captured and channeled is just as important. A logical step to consider is embedding an intelligent “edge” or gateway that collects the right data from the factory floor.
These gateways normalize the data streams to give you a coherent and actionable portrait of your production in real-time. For example, an IoT Gateway is a combined software/hardware platform that makes it easy to perform real-time monitoring of process data, such as temperature, pressure, vibration, power consumption, or other parameters. It is designed for easier setup without intervening in the automation logic.
Recommended for You: Making Sense of Real-Time Factory Data
Data can be centralized at the plant level with local machine state monitoring systems and eventually scale up to using the gateway to connect all production locations through the cloud and utilizing cloud-based analytical tools. With these tools, it is now possible to have much more data-driven solutions to help companies improve several critical productivity tools and strategic programs. These include predictive maintenance with better insight into machine service, data analytics for smarter use of production data and decision making, and visualization and notification of production data in real-time for production planning and quality data management.
Using the data from across the enterprise better quantifies the overall equipment effectiveness (OEE) and compares different production platforms to help guide investments in future equipment
Ultimately, solid historical data and better insight from cloud-based analytical tools lead to better business intelligence and enterprise-wide strategic planning; addressing long-range investments in new production systems, plants, personnel, and markets.
Combining Innovation With Experience
The current generation of engineers entering manufacturing operations have backgrounds and experiences that differ in many ways from those engineers who have 20 to 30 years on the job. Mechanical engineers fresh out of school grew up surrounded by and interacting with digital information technologies.
They are much more used to having in-depth data on hand to make decisions. They use computer-aided design tools, 3D simulations of systems, and virtual prototypes of components or devices before even fabricating an actual prototype. They most likely have also taken basic programming classes and have experience with commercial programming languages and designing and programming user interfaces, as opposed to standard PLC programming methods using ladder logic.
They also tend to be much more experienced with thinking about and designing systems that are networked and highly connected. That means they may assume that technology incorporates the ability to connect with other systems and share data horizontally and vertically, including the use of cloud-based applications and artificial intelligence-type systems.
In contrast, there are large segments of today’s manufacturing systems that are less networked and data-rich than the new generation of engineers might expect. The older engineering staff in these operations draw more on their experience designing, building, and running these systems to a significant degree, compensating for the comparative dearth of information. These more experienced engineers know their machines: how they sound, how products move through the equipment, and where potential choke points, common areas of stress and potential breakdowns are located.
Combining the skills and expertise of both veteran and new engineers can help companies implement IoT technologies more effectively as they seek to build the Factory of the Future. The older generation of engineers can contribute their experience and insights about how existing manufacturing systems perform, while the newer generation can contribute their skills at organizing and analyzing data and optimizing how digital technology like sensors, visualization systems, and controls can be leveraged to the maximum value.
Editors’ Pick: Experience Faster Internet at AT&T’s 5G Manufacturing Zone
It’s important to appreciate that the Factory of the Future is already being built. Seasoned engineers and the new generation just joining today’s manufacturing companies both have important contributions to make. Together they can chart a scalable, step-by-step approach that adds the layers of sensors, intelligence, and connectivity to existing manufacturing platforms that can yield actionable insights to solve current issues. They can also collaborate with forward-looking OEMs and technology suppliers to determine the best way to incorporate IoT technology into the next generation of production platforms.
Peter Fischbach is industry segment manager for Bosch Rexroth U.S.
Opinions expressed are the author’s and do not necessarily reflect the views of ASME.