Building Tough 3D Nanomaterials
Building Tough 3D Nanomaterials
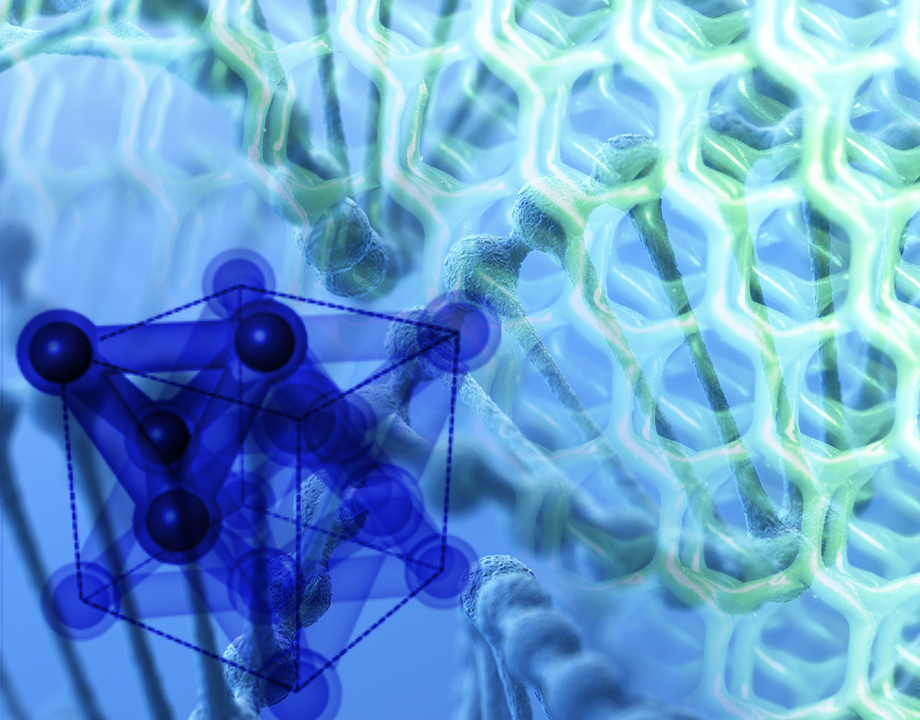
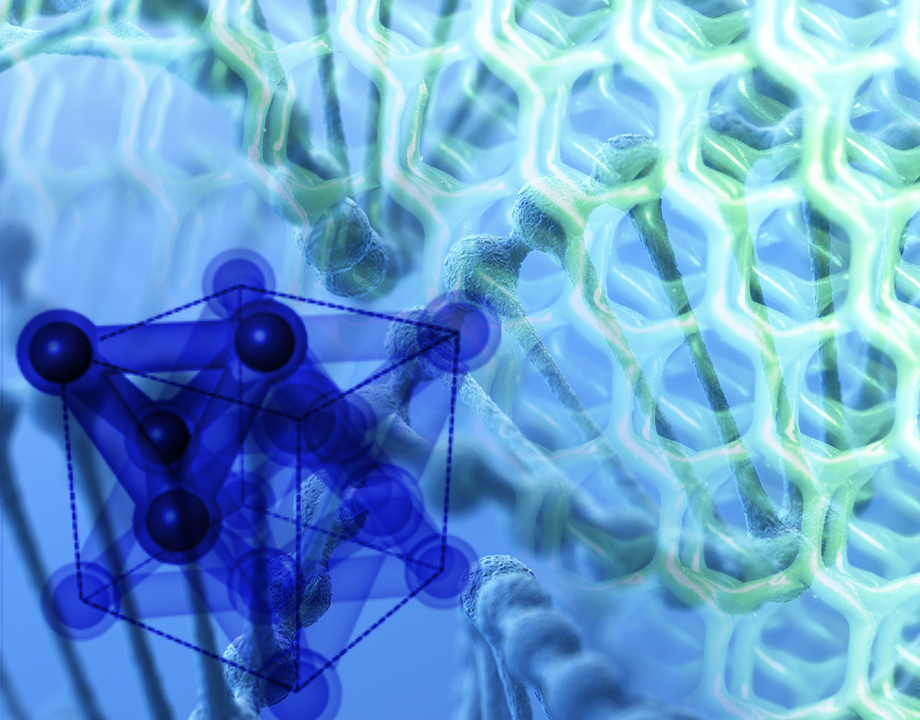
Mineralization of 3D lattice formed by DNA tetrahedra (about 30 nm) and gold nanoparticle into all-inorganic 3D silica-Au replicas with preserved architecture. Image: Oleg Gang/Columbia Engineering
Using DNA nanotechnology, a research team at Columbia University has created hardy nanoparticle-based materials that can be processed using conventional nanofabrication methods. Pliable, 3D DNA-nanoparticle-based structures are converted from a liquid state to a rigid solid state by using a silicification process that uniformly reinforces the DNA structure.
“Specifically designed DNA can be assembled into three-dimensional nanostructured scaffolds that serve to organize inorganic nanoscale matter,” said lead researcher Oleg Gang, professor of chemical engineering and of applied physics and materials science at Columbia University. “However, these scaffolds are delicate structures that can exist only in a narrow range of environmental conditions, which limits their applications for generating novel materials that can be subjected to manufacturing stresses or need to operate in a broad range of environmental conditions.”
To make these structures stronger and more viable for potential engineering and manufacturing applications, Gang and his team created a process that makes robust replicas of the 3D DNA-based nano-architectures by mineralizing them with silica.
The new system was built in collaboration with Brookhaven National Laboratory. Gang, who is also group leader of the Soft and Bio Nanomaterials Group at Brookhaven Lab’s Center for Functional Nanomaterials, is one of the world’s leading experts DNA nanotechnology.
Editor’s Pick: Virtual Technology at the Nanoscale
DNA can be folded into two and three-dimensional nanostructures, which can then become building blocks when they are programmed via Watson-Crick interactions to self-assemble into specific 3D architectures. These can then be integrated with nanoparticles to have very specific chemical and mechanical characteristics. The “blocks” are then mineralized with a silica coating (as thin as 5 nm) to add strength and rigidity.
Gang’s process was specifically devised to yield a conformal coating for the 3D nanoscale structure, thus preserving the entire 3D architecture. “In our approach, the reaction conditions are optimized to achieve uniform silication within the 3D DNA-nano-particle frameworks, thus templating results in an inorganic replica of the entire architecture with the ability to control its structurally defined porosity through the degree of silica coating,” he said. “The nanoscale silica provides stability while also preserving the architecture.”
To test the hardiness of the silica-coated structures, the team subjected them high temperatures above 1,0000˚C and high mechanical stresses over 8 Gpa, as well as exposed them to high doses of radiation and focused ion beams. They monitored the structure changes under these conditions using x-ray scattering and electron microscopy methods.
To their delight, the researchers discovered the new nanomaterial withstood all these extremes, without altering its properties or architecture. “It can withstand a high pressure, a high temperature, and a high radiation and also be processed by conventional nanofabrication methods,” said Gang. “The in-situ characterizations reveal that nano-architecture is preserved under the extreme environmental conditions. We were surprised by how stable the structures were and how difficult they were to break—we did not expect this!”
“Our analysis of the applicability of these structures to couple with traditional nanofabrication techniques demonstrates a truly robust platform for generating resilient nanomaterials via DNA-based approaches for discovering their novel properties,” said Gang. “This is a big step forward. No alternative methods exist today to create architectured 3D nanomaterials on such small scales.”
More for You: Infographic: 10 Applications of Nanotechnology
Gang’s approach permits creating organized 3D nanoarchitectures in a designed way. He believes that his approach for creating 3D DNA scaffolds, with or without nanoparticles, and their templating into inorganics, opens a door for a conceptually different approach for creating prescribed structured nanomaterials.
“This allows generation of robust materials and harvesting their nanoparticle functions, such as optical, chemical, etc.,” said Gang. “We can envision that materials with tuned and enhanced mechanical properties can be formed rationally. They could also be combined with different known classes—for example, nanocomposites.”
This integration of novel and conventional nanofabrication methods will likely lead to advances in mechanics, electronics, plasmonics, photonics, superconductivity, energy, and other industries. What is the next step for Gang and his team? “First, we need to do more fundamental studies to reveal nanomechanical properties and to understand what key parameters control them,” he said. “After that we plan to explore how to build materials rationally with specific desired mechanical properties.”
Mark Crawford is a technology writer based in Corrales, N.M.
“Specifically designed DNA can be assembled into three-dimensional nanostructured scaffolds that serve to organize inorganic nanoscale matter,” said lead researcher Oleg Gang, professor of chemical engineering and of applied physics and materials science at Columbia University. “However, these scaffolds are delicate structures that can exist only in a narrow range of environmental conditions, which limits their applications for generating novel materials that can be subjected to manufacturing stresses or need to operate in a broad range of environmental conditions.”
To make these structures stronger and more viable for potential engineering and manufacturing applications, Gang and his team created a process that makes robust replicas of the 3D DNA-based nano-architectures by mineralizing them with silica.
How It Works
The new system was built in collaboration with Brookhaven National Laboratory. Gang, who is also group leader of the Soft and Bio Nanomaterials Group at Brookhaven Lab’s Center for Functional Nanomaterials, is one of the world’s leading experts DNA nanotechnology.
Editor’s Pick: Virtual Technology at the Nanoscale
DNA can be folded into two and three-dimensional nanostructures, which can then become building blocks when they are programmed via Watson-Crick interactions to self-assemble into specific 3D architectures. These can then be integrated with nanoparticles to have very specific chemical and mechanical characteristics. The “blocks” are then mineralized with a silica coating (as thin as 5 nm) to add strength and rigidity.
Gang’s process was specifically devised to yield a conformal coating for the 3D nanoscale structure, thus preserving the entire 3D architecture. “In our approach, the reaction conditions are optimized to achieve uniform silication within the 3D DNA-nano-particle frameworks, thus templating results in an inorganic replica of the entire architecture with the ability to control its structurally defined porosity through the degree of silica coating,” he said. “The nanoscale silica provides stability while also preserving the architecture.”
To test the hardiness of the silica-coated structures, the team subjected them high temperatures above 1,0000˚C and high mechanical stresses over 8 Gpa, as well as exposed them to high doses of radiation and focused ion beams. They monitored the structure changes under these conditions using x-ray scattering and electron microscopy methods.
To their delight, the researchers discovered the new nanomaterial withstood all these extremes, without altering its properties or architecture. “It can withstand a high pressure, a high temperature, and a high radiation and also be processed by conventional nanofabrication methods,” said Gang. “The in-situ characterizations reveal that nano-architecture is preserved under the extreme environmental conditions. We were surprised by how stable the structures were and how difficult they were to break—we did not expect this!”
Moving Forward
“Our analysis of the applicability of these structures to couple with traditional nanofabrication techniques demonstrates a truly robust platform for generating resilient nanomaterials via DNA-based approaches for discovering their novel properties,” said Gang. “This is a big step forward. No alternative methods exist today to create architectured 3D nanomaterials on such small scales.”
More for You: Infographic: 10 Applications of Nanotechnology
Gang’s approach permits creating organized 3D nanoarchitectures in a designed way. He believes that his approach for creating 3D DNA scaffolds, with or without nanoparticles, and their templating into inorganics, opens a door for a conceptually different approach for creating prescribed structured nanomaterials.
“This allows generation of robust materials and harvesting their nanoparticle functions, such as optical, chemical, etc.,” said Gang. “We can envision that materials with tuned and enhanced mechanical properties can be formed rationally. They could also be combined with different known classes—for example, nanocomposites.”
This integration of novel and conventional nanofabrication methods will likely lead to advances in mechanics, electronics, plasmonics, photonics, superconductivity, energy, and other industries. What is the next step for Gang and his team? “First, we need to do more fundamental studies to reveal nanomechanical properties and to understand what key parameters control them,” he said. “After that we plan to explore how to build materials rationally with specific desired mechanical properties.”
Mark Crawford is a technology writer based in Corrales, N.M.
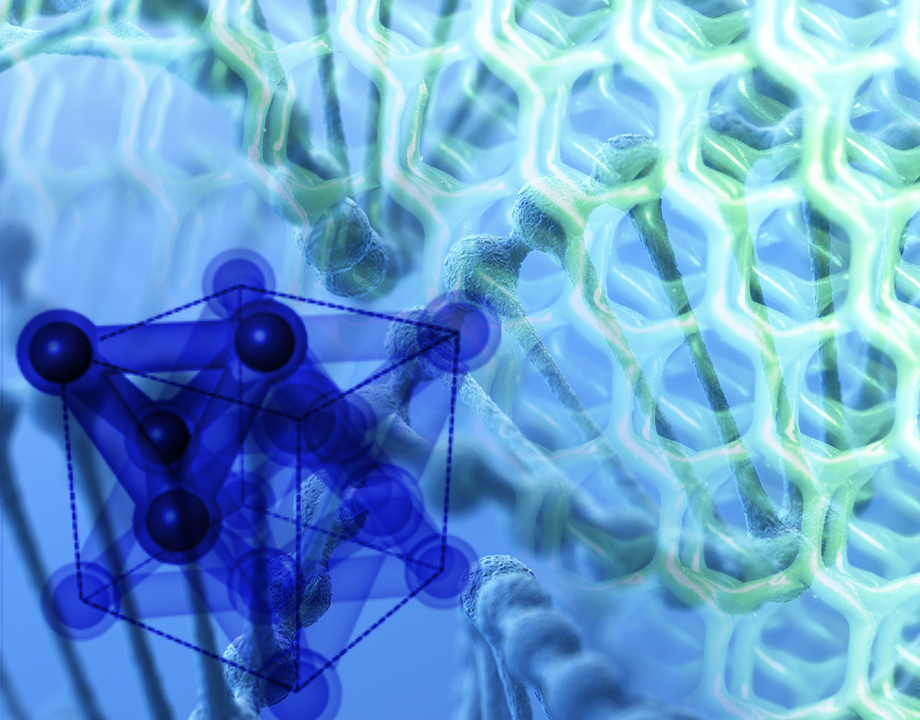
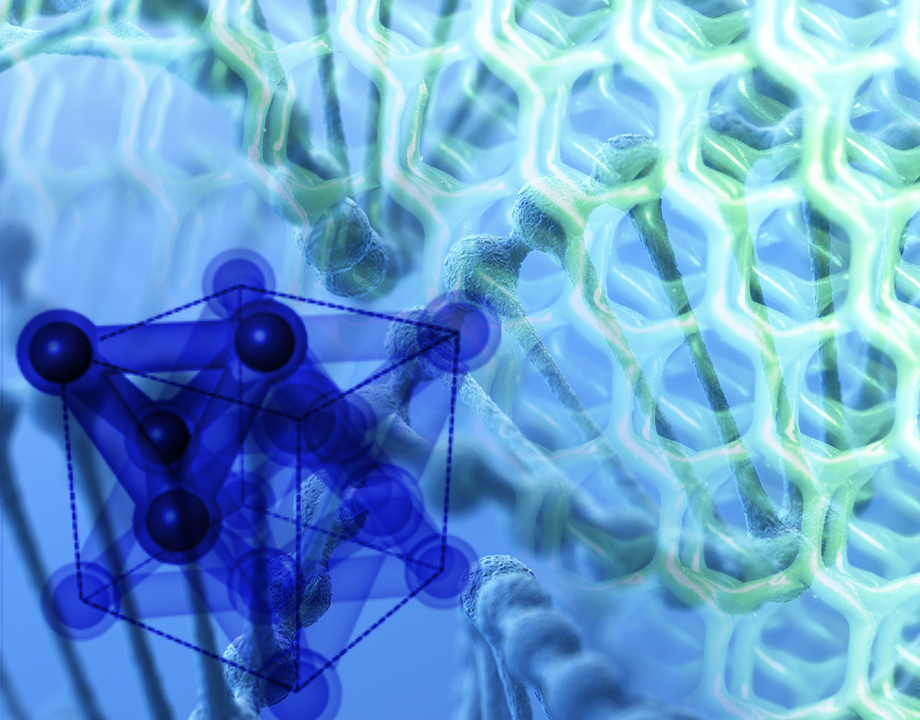