How Manufacturers Can Attract and Engage Young Talent?
How Manufacturers Can Attract and Engage Young Talent?
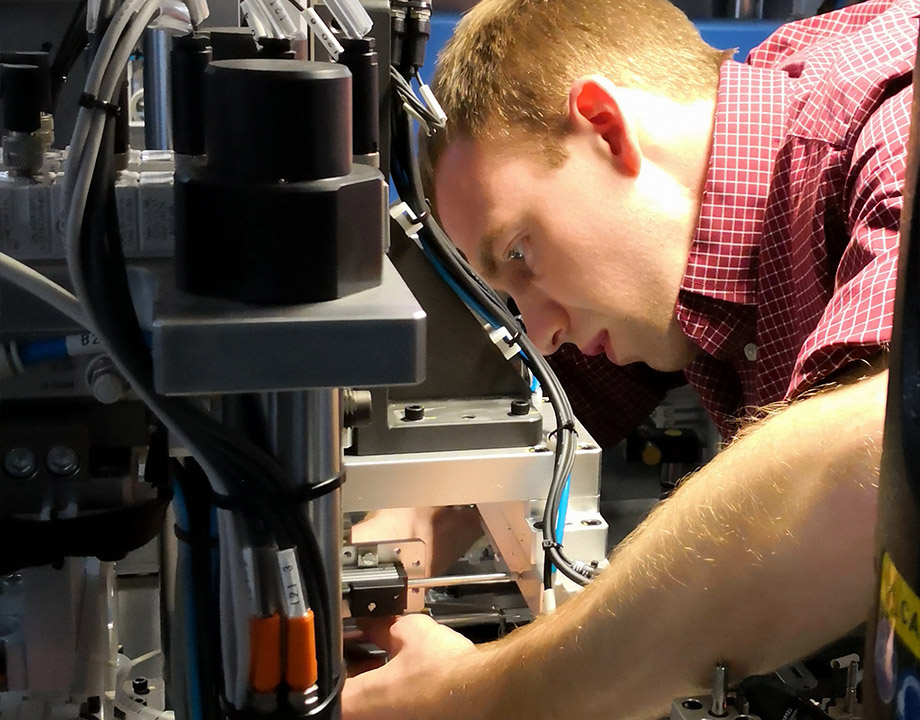
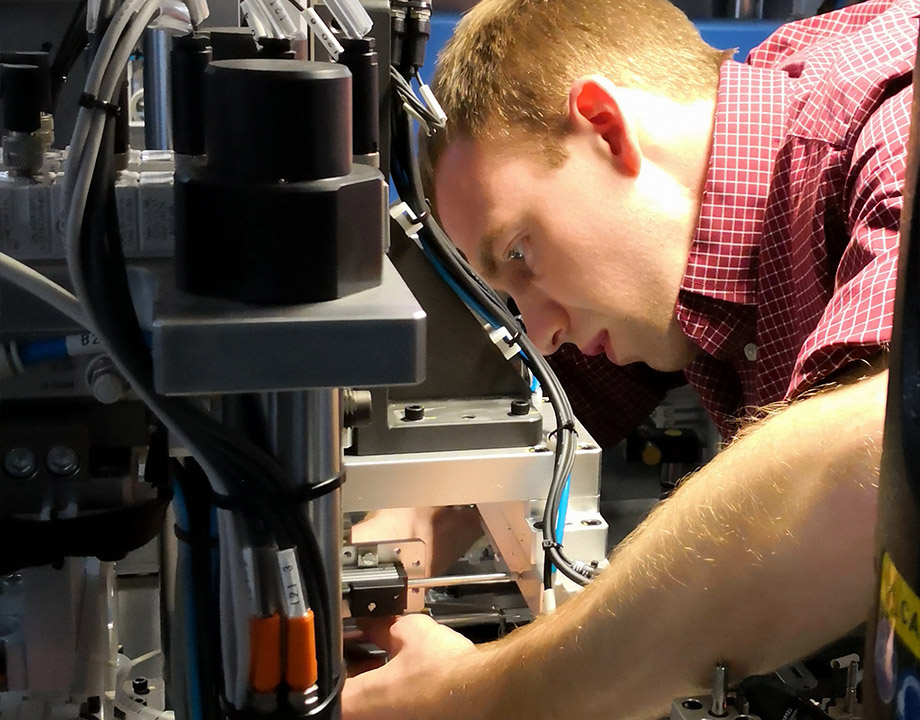
For young engineers like Mitch Engleka, an internship is an important stepping stone to becoming a full-time engineer. Photo: Southco
The future of manufacturing is in the hands of the younger generation.
The U.S. Department of Labor Bureau projects that by the year 2020, about 25 percent of the workforce will be composed of older workers (ages 55 and over). As that generation begins retiring, it is vital for manufacturing to identify ways to attract new, young people to careers in the manufacturing-related science, technology, engineering, and math (STEM) professions.
Over the next decade, according to a study by the Manufacturing Institute and Deloitte, an estimated 3.5 million manufacturing jobs will need to be filled, and the skills gap could potentially result in 2 million of those jobs going unfilled.
There are many reasons for young people choosing to pursue careers in industries outside of manufacturing. Manufacturers need to understand the factors contributing to the shortage of skilled workers and ways to take a proactive role in STEM outreach, educating the next generation about the available opportunities in manufacturing and engineering.
There are several societal factors that make it difficult to attract young people to careers in manufacturing.
One challenge is longstanding impressions about U.S. manufacturing that bear little resemblance to current realities. Kids entering high school or college may only know the manufacturing industry from what they see in their textbooks: Photos from the middle of the twentieth-century showing steel mills and other industrial sites as dirty, dark, unattractive places to spend a lifetime career. It’s no surprise that many people have developed a negative perception of what it means to work in manufacturing.
Unfortunately, it is no longer common practice to bring schoolchildren or vocational-technical students to tour factories and provide a first-hand look at what modern factories are like. So, unless a young person’s family is working in these evolved facilities, it may be difficult to overcome stereotypical impressions.
You May Also Like: Infographic: Changing What’s Made in the USA
In the past 20-30 years many manufacturing plants closed or moved overseas. Although U.S.-based manufacturing has seen growth in recent years, young people whose parents and grandparents have experienced plant closures and layoffs will be even more reluctant to consider manufacturing careers.
Another challenge manufacturing faces is the competition, i.e. the Silicon Valley. Young women and men with strong math and computer skills often envision their future developing the next big app or inventing the next Facebook.
Also contributing to the shortage of a skilled workforce is a gradual decline of technical education programs in high schools.
Other factors include loss of knowledge due to experienced workers leaving the workforce. Many of the skilled tradespeople such as tool and die makers, manufacturing technicians, maintenance mechanics, and production technicians have gained skills over decades of work, with many of the skills self-taught. Unless a sufficient number of young people with a basic set of technical skills are brought onboard manufacturing operations, those skills could be lost.
You May Also Like: Infographic: The Future Engineering Workforce
One significant new skills challenge that manufacturers need to consider is the growth of digital manufacturing and Industry 4.0. Engineers working in these environments need a broader skill set than just expertise in mechanical systems or pneumatic systems.
Cutting-edge companies need personnel with backgrounds and capabilities that combine electrical engineering, mechanical engineering, computer systems, and networking, plus backgrounds in production data analytics.
Manufacturing companies of different sizes and across every industry segment are responding to these challenges with specific programs and investments. They fall into two categories: supporting STEM education programs and engaging in early outreach.
Outreach—the earlier, the better—has proven to be a valuable and effective approach to developing future engineers and technical production staff. The start can be relatively small and simple: arranging “show and tells” at local schools (on career day, for example) to explain what a company manufactures, with sample products and exciting videos that show off what goes on within the local factory’s walls.
At some companies, these initial outreach efforts have evolved into scheduling visits to a local factory or engineering facility. These types of activities can be targeted to high schools and local colleges; participation in college job fairs is also productive.
Companies can also benefit by encouraging existing engineering personnel to participate in industry advisory boards at local universities and community colleges, particularly ones with engineering and technical programs. By doing so, the company has the opportunity to build relationships with faculty and potential student hires, promote internships and co-op programs and contribute advice on the school’s curriculum and the types of equipment the schools purchase to equip their labs.
Another popular way to build relationships and cultivate talent is to sponsor and support robotics teams and robotics competitions at local educational institutions. These have become increasingly popular in recent years, and by supplying engineers who act as advisors to teams, as well as supporting the events and prizes, manufacturers and engineering companies can raise their profile and contribute to building a stronger public profile for STEM education and careers.
Internships, co-op programs, and part-time work opportunities for college and technical students are all effective tools for attracting engineering talent.
These types of programs do require investments of time and resources, but the payoff can be significant: With the right program, it’s much easier to turn interns into full-time engineers who will be dedicated to the company from day one.
Further Reading: How to Bring Engineering and Manufacturing Jobs Back to America
Many manufacturers have found that the key to successful internships is giving the students real-world challenges. One of the benefits of this approach is it gives current students the sense that their skills and creativity can truly be applied in a manufacturing or engineering setting and leads to tangible results.
If possible, internships should be paid; moreover, many companies are discovering that the best way to secure interns for long-term employment after graduation is through offering opportunities for part-time employment after the internship is completed.
Also, word-of-mouth is valuable: Once a student-turned-part-time-employee tells other students about their positive experience, attracting other interns will be easier.
Internships can evolve into full-time positions and are often the best way to attract young engineers to manufacturing.
Mitch Engleka was an undergraduate engineering student at Pennsylvania State University. As part of his multidisciplinary engineering design program he took a field trip to Southco, a manufacturing company that creates access hardware for the transportation and electronics industries.
The Multidisciplinary Engineering Design (MDE) program at Penn State is very hands-on: there are guest lectures, field trips to engineering and manufacturing companies, and a required internship.
“While I was visiting the Southco factory, I dropped off my resume for a summer internship,” Engleka said. “The tour showed me how clean, dynamic, and cutting-edge the company was, in terms of manufacturing operation, so seeing it and the kind of work they did really appealed to me.”
Further Reading: 8 Time-Management Tips for Engineers
His internship was successful, and in his senior year Engleka only needed to go to school part-time to complete his degree. “Southco was very supportive and offered me the opportunity to work three days a week while I went to school for two days,” he said. “I got the chance to have extra experience working in a manufacturing environment that I wasn’t able to get during the internship.”
During his last semester, Southco partnered with Penn State to sponsor a team of students, including Engleka, to work on a senior “capstone” project: Automating the quality inspection process for a sliding cabinet latch. For the project, the team built an attachment for the production equipment that would test the strength of the latch, relying on cameras and sensors to perform the audit.
“It’s rewarding to work on a project that you know a company will use,” said Engleka, who is now employed with Southco full-time as a manufacturing engineer. “The capstone assignment—along with my internship—prepared me for a career in manufacturing. In fact, on the Monday after graduation, I started working full-time.”
To be successful, companies need to strongly encourage engineering and professional staff to take the time to support internships and outreach to STEM students and programs in the community. Developing a network of professionals, for example, those who can devote 5% of their time every month to these efforts and spreading out the responsibility rather than saddling a few individuals will help ensure that outreach efforts are productive. Plus, getting managers and engineering staff out of the office and interacting with the next generation of production workers and engineers can be very rewarding.
You May Also Like: QUIZ: How Much Do New College Graduates Earn?
For companies that ask, “All this STEM outreach seems like a lot of effort … what’s in it for our company?” the payback can be immediate and substantial. If a company has strong STEM outreach and internship programs, talent can be developed in-house, and their abilities and value accurately assessed, saving time and money when bringing them onboard.
Al Frattarola is the global director of engineering and technology at Southco.
Opinions expressed are the author’s and do not necessarily reflect the views of ASME.
The U.S. Department of Labor Bureau projects that by the year 2020, about 25 percent of the workforce will be composed of older workers (ages 55 and over). As that generation begins retiring, it is vital for manufacturing to identify ways to attract new, young people to careers in the manufacturing-related science, technology, engineering, and math (STEM) professions.
Over the next decade, according to a study by the Manufacturing Institute and Deloitte, an estimated 3.5 million manufacturing jobs will need to be filled, and the skills gap could potentially result in 2 million of those jobs going unfilled.
There are many reasons for young people choosing to pursue careers in industries outside of manufacturing. Manufacturers need to understand the factors contributing to the shortage of skilled workers and ways to take a proactive role in STEM outreach, educating the next generation about the available opportunities in manufacturing and engineering.
Counteracting Manufacturing Stereotypes
There are several societal factors that make it difficult to attract young people to careers in manufacturing.
One challenge is longstanding impressions about U.S. manufacturing that bear little resemblance to current realities. Kids entering high school or college may only know the manufacturing industry from what they see in their textbooks: Photos from the middle of the twentieth-century showing steel mills and other industrial sites as dirty, dark, unattractive places to spend a lifetime career. It’s no surprise that many people have developed a negative perception of what it means to work in manufacturing.
Unfortunately, it is no longer common practice to bring schoolchildren or vocational-technical students to tour factories and provide a first-hand look at what modern factories are like. So, unless a young person’s family is working in these evolved facilities, it may be difficult to overcome stereotypical impressions.
You May Also Like: Infographic: Changing What’s Made in the USA
In the past 20-30 years many manufacturing plants closed or moved overseas. Although U.S.-based manufacturing has seen growth in recent years, young people whose parents and grandparents have experienced plant closures and layoffs will be even more reluctant to consider manufacturing careers.
Another challenge manufacturing faces is the competition, i.e. the Silicon Valley. Young women and men with strong math and computer skills often envision their future developing the next big app or inventing the next Facebook.
Challenge of Sustaining a Skilled Workforce
Also contributing to the shortage of a skilled workforce is a gradual decline of technical education programs in high schools.
Other factors include loss of knowledge due to experienced workers leaving the workforce. Many of the skilled tradespeople such as tool and die makers, manufacturing technicians, maintenance mechanics, and production technicians have gained skills over decades of work, with many of the skills self-taught. Unless a sufficient number of young people with a basic set of technical skills are brought onboard manufacturing operations, those skills could be lost.
You May Also Like: Infographic: The Future Engineering Workforce
One significant new skills challenge that manufacturers need to consider is the growth of digital manufacturing and Industry 4.0. Engineers working in these environments need a broader skill set than just expertise in mechanical systems or pneumatic systems.
Cutting-edge companies need personnel with backgrounds and capabilities that combine electrical engineering, mechanical engineering, computer systems, and networking, plus backgrounds in production data analytics.
Investing in Student Outreach, Education, and Support
Manufacturing companies of different sizes and across every industry segment are responding to these challenges with specific programs and investments. They fall into two categories: supporting STEM education programs and engaging in early outreach.
Outreach—the earlier, the better—has proven to be a valuable and effective approach to developing future engineers and technical production staff. The start can be relatively small and simple: arranging “show and tells” at local schools (on career day, for example) to explain what a company manufactures, with sample products and exciting videos that show off what goes on within the local factory’s walls.
At some companies, these initial outreach efforts have evolved into scheduling visits to a local factory or engineering facility. These types of activities can be targeted to high schools and local colleges; participation in college job fairs is also productive.
Companies can also benefit by encouraging existing engineering personnel to participate in industry advisory boards at local universities and community colleges, particularly ones with engineering and technical programs. By doing so, the company has the opportunity to build relationships with faculty and potential student hires, promote internships and co-op programs and contribute advice on the school’s curriculum and the types of equipment the schools purchase to equip their labs.
Another popular way to build relationships and cultivate talent is to sponsor and support robotics teams and robotics competitions at local educational institutions. These have become increasingly popular in recent years, and by supplying engineers who act as advisors to teams, as well as supporting the events and prizes, manufacturers and engineering companies can raise their profile and contribute to building a stronger public profile for STEM education and careers.
Building Effective Internships and Co-op Programs
Internships, co-op programs, and part-time work opportunities for college and technical students are all effective tools for attracting engineering talent.
These types of programs do require investments of time and resources, but the payoff can be significant: With the right program, it’s much easier to turn interns into full-time engineers who will be dedicated to the company from day one.
Further Reading: How to Bring Engineering and Manufacturing Jobs Back to America
Many manufacturers have found that the key to successful internships is giving the students real-world challenges. One of the benefits of this approach is it gives current students the sense that their skills and creativity can truly be applied in a manufacturing or engineering setting and leads to tangible results.
If possible, internships should be paid; moreover, many companies are discovering that the best way to secure interns for long-term employment after graduation is through offering opportunities for part-time employment after the internship is completed.
Also, word-of-mouth is valuable: Once a student-turned-part-time-employee tells other students about their positive experience, attracting other interns will be easier.
From Summer Intern to Full-time Engineer
Internships can evolve into full-time positions and are often the best way to attract young engineers to manufacturing.
Mitch Engleka was an undergraduate engineering student at Pennsylvania State University. As part of his multidisciplinary engineering design program he took a field trip to Southco, a manufacturing company that creates access hardware for the transportation and electronics industries.
The Multidisciplinary Engineering Design (MDE) program at Penn State is very hands-on: there are guest lectures, field trips to engineering and manufacturing companies, and a required internship.
“While I was visiting the Southco factory, I dropped off my resume for a summer internship,” Engleka said. “The tour showed me how clean, dynamic, and cutting-edge the company was, in terms of manufacturing operation, so seeing it and the kind of work they did really appealed to me.”
Further Reading: 8 Time-Management Tips for Engineers
His internship was successful, and in his senior year Engleka only needed to go to school part-time to complete his degree. “Southco was very supportive and offered me the opportunity to work three days a week while I went to school for two days,” he said. “I got the chance to have extra experience working in a manufacturing environment that I wasn’t able to get during the internship.”
During his last semester, Southco partnered with Penn State to sponsor a team of students, including Engleka, to work on a senior “capstone” project: Automating the quality inspection process for a sliding cabinet latch. For the project, the team built an attachment for the production equipment that would test the strength of the latch, relying on cameras and sensors to perform the audit.
“It’s rewarding to work on a project that you know a company will use,” said Engleka, who is now employed with Southco full-time as a manufacturing engineer. “The capstone assignment—along with my internship—prepared me for a career in manufacturing. In fact, on the Monday after graduation, I started working full-time.”
Investing in STEM Outreach Pays Dividends
To be successful, companies need to strongly encourage engineering and professional staff to take the time to support internships and outreach to STEM students and programs in the community. Developing a network of professionals, for example, those who can devote 5% of their time every month to these efforts and spreading out the responsibility rather than saddling a few individuals will help ensure that outreach efforts are productive. Plus, getting managers and engineering staff out of the office and interacting with the next generation of production workers and engineers can be very rewarding.
You May Also Like: QUIZ: How Much Do New College Graduates Earn?
For companies that ask, “All this STEM outreach seems like a lot of effort … what’s in it for our company?” the payback can be immediate and substantial. If a company has strong STEM outreach and internship programs, talent can be developed in-house, and their abilities and value accurately assessed, saving time and money when bringing them onboard.
Al Frattarola is the global director of engineering and technology at Southco.
Opinions expressed are the author’s and do not necessarily reflect the views of ASME.