Knock on Super Wood
Knock on Super Wood
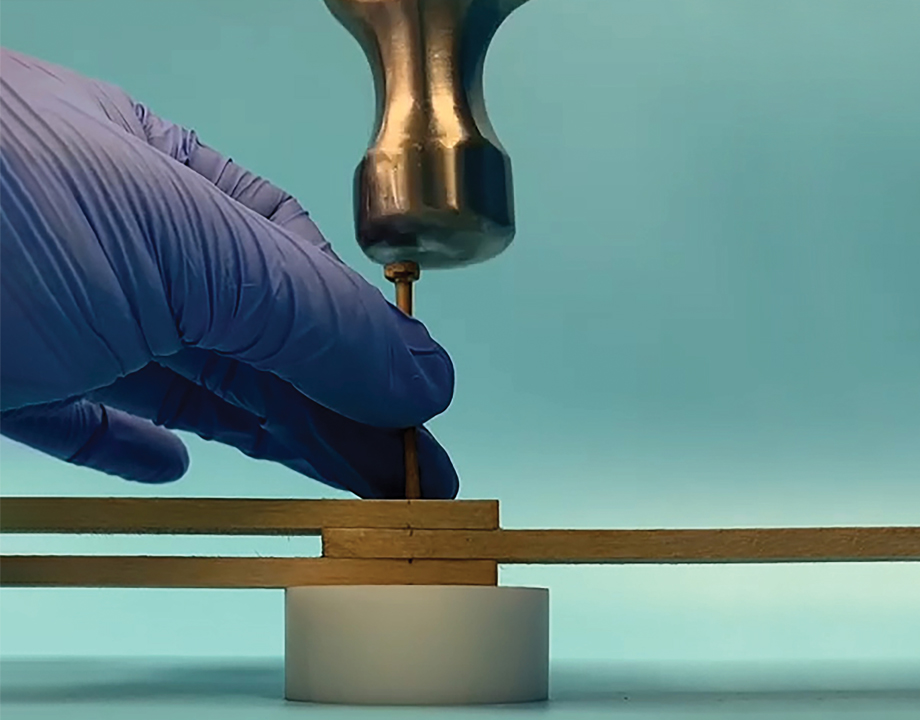
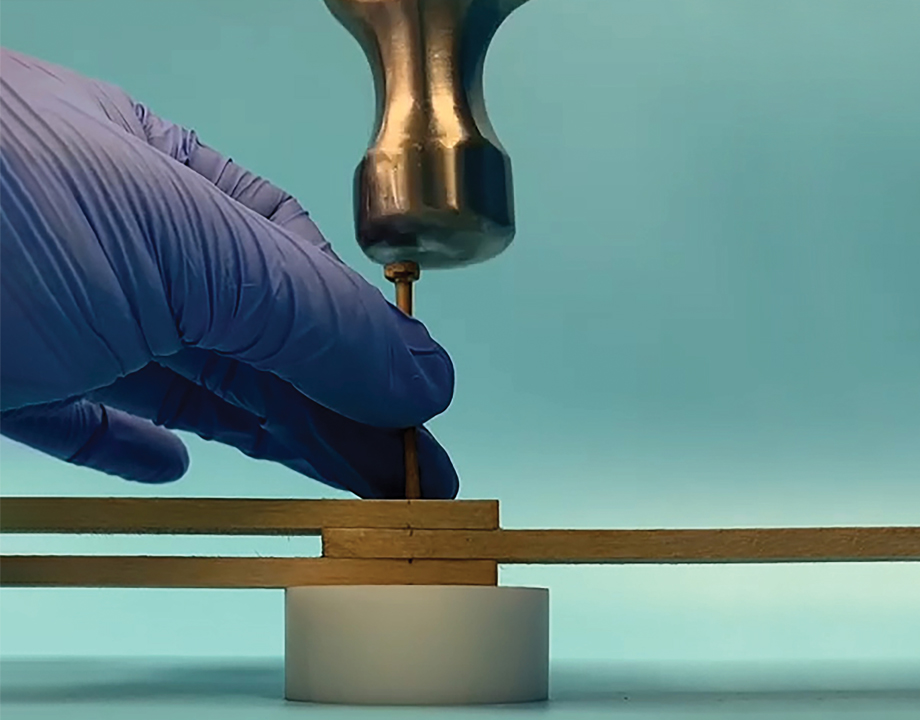
Researchers have engineered everyday wood to become stronger and tougher than steel. Is super wood destined to become this century’s favorite material?
Archaeologists divide human history by the favored materials of the time. Hence the Stone Ages, a Bronze Age, and an Iron Age. Civilizations have even been named after the pottery shards they left behind. And once archaeologists get around to naming the 20th century, they will have their choice among steel, concrete, and plastic, all of which blossomed over the past century as scientists, engineers, and manufacturers learned how best to make use of these materials.
One constant but overlooked material throughout history has been wood. For thousands of years, wood has been used in construction and in building furniture, tools, and weapons. Although lightweight, abundant, and self-renewing, wood’s reputation has suffered when compared to other materials. In its natural state, wood can’t compete with the strength of steel, for example. While wood is strong along its grains, it can be brittle in directions perpendicular to the grain. Wood is also rigid with poor formability compared to metals or plastics, making it difficult to mold into different shapes.
In the 21st century, however, materials are being reconsidered based on the size of their carbon footprints. The manufacture of steel, concrete, and plastic results in large amounts of carbon emissions. Wood, on the other hand, is made from carbon drawn from the atmosphere.
“We know carbon emission, or carbon neutralization, is really something the whole world needs to work on,” said Teng Li, Keystone professor of mechanical engineering at the University of Maryland in College Park. “If you are using wood to replace steel, you can reduce the manufacturing cost and have a light carbon footprint.”
Wood also lasts for a long time, and can essentially trap and store the carbon so that it can’t escape into the atmosphere as carbon dioxide.
Li and his colleagues, who had been busy conducting research on cellulose, a major component of wood, knew that wood had the potential to replace steel in modern uses in everything from construction to vehicles to aerospace. But first, they had to find a way to use what they understood about the properties of wood to make it both more moldable and stronger.
More on Materials: Low-Carbon Concrete Can Fight Global Warming
By combining two modification processes, the team discovered they could radically improve the qualities of wood. Over the past few years, the team from Maryland has published a series of papers outlining the results of their modification: Hardened wood tough enough to use as nails, sharpened wood that can cut through well-done steak, and thin sheets of wood treated to be transparent enough to use as windows.
Crushing It
Natural wood is composed of a network of cellulose, lignin, and hemicellulose. Unlike many engineering processes where another material with different properties is added to create a stronger substance, the researchers in Li’s lab take the opposite approach.
Using chemicals, they dissolve and wash away lignin, which gives wood its rigidity and brownish hue. The process leaves behind a soft and spongy delignified wood that is easily moldable into a desired shape. To go from spongy to hard as steel requires another step. Other labs have tried their hand at re-engineering wood to make it stronger, with only marginal success.
“Traditional approaches of making wood stronger tend to focus on filling the pores with another material or making it more hydrophobic,” said Ping Liu, a professor of nanoengineering and director of the Sustainable Power and Energy Center at the University of California, San Diego, who was not involved with the research. “The residual porosities put a limit on the ultimate strength and hardness.”
Instead of filling in the pores, the Maryland team squashed them. They took samples of the shaped, delignified wood and placed them in a mechanical press for about a day while heating them to 150° F. The mechanical process collapsed the individual cell walls and tightly packed the cellulose fibers, creating strong hydrogen bonds, and crushed any holes or knots.
“The UMD process of partially removing lignin to collapse the pores for compression is unique,” Liu said.
Materials for Manufacturing: 9 Material Discoveries that Could Transform Manufacturing
The resulting densified wood is five times thinner, but 12 times stronger and 10 times tougher than it was before the processing: Try stabbing super wood and you’ll be hard pressed to get the knife in. Conversely, as the team demonstrated in video clips, nails made of super wood can be pounded through multiple boards to hold them together. In another clip, an unassuming knife that looks more at home in a picnic set than a restaurant sliced through a thick slab of beef.
Typically, it’s difficult to achieve both higher tensile strength and increased toughness in a material. But Li and his colleagues found the treated wood to have improved resistance to breaking under tension and better ability to absorb energy without fracturing.
“Of outstanding interest is the fact that wood densification leads to both increased strength and toughness, two properties that usually offset each other,” said Orlando J. Rojas, a professor at Aalto University in Finland, in a press statement.
Despite its strengths, super wood comes with its own weaknesses.
The most obvious of these is wood’s vulnerability to water. Trees continually transport water and nutrition from their roots all the way to their leaves. So natural wood itself works with water all the time. In cut wood, however, as water content increases, strength and stiffness decrease.
“It’s sort of a double-edged sword,” Li said. “You want [it to be] high strength; meanwhile, you want it to be biodegradable. So, this water absorption and liquidation of the material is something far more accommodating to its high mechanical performance.”
One common way to counter water absorption is via a surface coating that has anti-water properties, such as those containing oil. This has been done with furniture, buildings, and hardwood floors for years and similar techniques could be used to further protect super wood from moisture.
“Wood is particularly appealing as a steel replacement if the exposure to water is not extensive,” said Liu, who also explains that in objects like nails, wood would not suffer the galvanic corrosion that is seen in metals. Further, wood is potentially very easily accepted by consumers, as it’s more biodegradable.
Environmental Impact
Beyond its ability to break down via natural processes, what really are the environmental impacts of super wood? To better understand its carbon footprint, the team compared 3D-molded wood with traditional metal and polymer-based structural materials. Specifically, they calculated the ratio of environmental impact per volume of material to tensile strength and stiffness. The researchers looked at different categories like impact on ecosystem, global warming, fossil fuel usage, and human health, among others.
“The 3D-molded wood shows substantial reductions (59 percent to 99 percent) across all environmental impact categories, even compared with (aluminum) alloy with a high recycled content of 73.9 percent,” the team reported in a 2021 paper published in Science. “Additionally, on the basis of the specific tensile strength measured in this study, 3D-molded wood only needs 21 percent to 23 percent of the mass of Al alloy to fulfill the same strength requirements.”
With such results, the case for utilizing the treated wood to replace steel and other carbon-intensive materials seems obvious: Use a material that requires less energy than alternatives and literally grows on trees. And with three trillion mature trees on Earth, there seems to be an abundance of available material.
Editor's Choice: Rebuilding with Recycled Concrete
But what would be the environmental impact of cutting enough trees to replace commercially used steel and plastics with wood? A mature tree absorbs upward of 48 pounds of carbon dioxide each year from the atmosphere. Felled trees not only cease to continue absorbing this greenhouse gas but also can start releasing the carbon they’ve been storing into the atmosphere.
The solution to offset any trees cut for super wood, according to Li, is reforestation. Potentially, each tree cut could be replaced by a newly planted sapling, especially one from a fast-growing species like poplar. Additionally, Li believes we need to reassess our value system when it comes to the reasons why we cut trees in the first place.
“When people cut trees, they’re trying to get the higher value of either the material or the land,” he said. “For example, if they cut the trees for construction of buildings, that generates more value for the land use instead of leaving forest over there. However, if you can get more value, or more potential, from the trees or the woods, then people will realize that, ‘OK, if I have more trees then these trees will generate more value.’”
Once industry changes its relationship to this low-cost and abundant material, it can use wood in applications such as vehicles, building material, airplanes, and wind turbines—instead of steel, plastics, carbon fiber, or even Kevlar. Li even points to potential use in the aerospace industry.
“Even a single ounce of saved weight will save a lot of energy to fly and launch,” he said.
Moving to a future made of wood could also reduce the net burden on the environment.
“The current materials all have major environmental impacts: Steel is very energy intensive to make and will eventually rust; plastic is not biodegradable and is a major environmental hazard,” Liu said.
Engineering Materials: Using Muscle to Spin Fiber
Also, strength and toughness are not the only attributes that can be engineered into wood. For instance, tweaking the process laid out by Li and colleagues can create wood that’s transparent while retaining its resistance to transmitting heat. Such material could in theory replace glass while providing better thermal insulation. These possibilities were highlighted in the 2023 Annual Review of Materials Research.
“There is actually still a lot of potential to be explored and so we’ve only scratched the surface here,” said Li. They also need to examine how to scale such a product for manufacturing, while lowering the cost enough so that people are willing to make the switch when it hits the market. Because he says that when people are buying a new product, they typically ask two questions: “Is it better than what we have? And is it cheap enough?”
What’s clear, however, is that Li and his fellow researchers “are excited and enthusiastic to work with other experts to push this forward,” he said.
And exciting additional developments have already come to the fore. Fellow University of Maryland researchers, for one, published a study in 2024 in the journal, Matter, outlining how they edited a single gene called 4CL1 out of live polar trees to grow wood that doesn’t require chemical processing to make it stronger. Using a technology called base editing, the researchers were able to grow poplars with 12.8% lower lignin content.
So while it’s too soon to know whether super wood will one day come to rival, or replace, steel or plastic, it’s clear that human ingenuity is making the Age of Super Wood a possibility.
Sara Goudarzi is a science writer based in Brooklyn, N.Y. Her novel, The Almond in the Apricot, was published in February 2022.
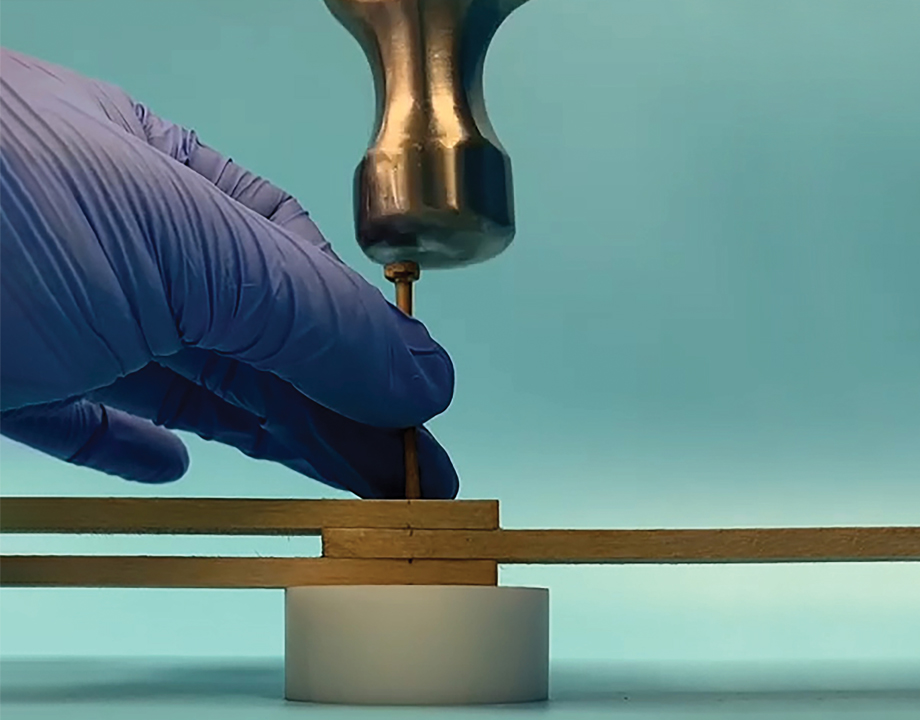
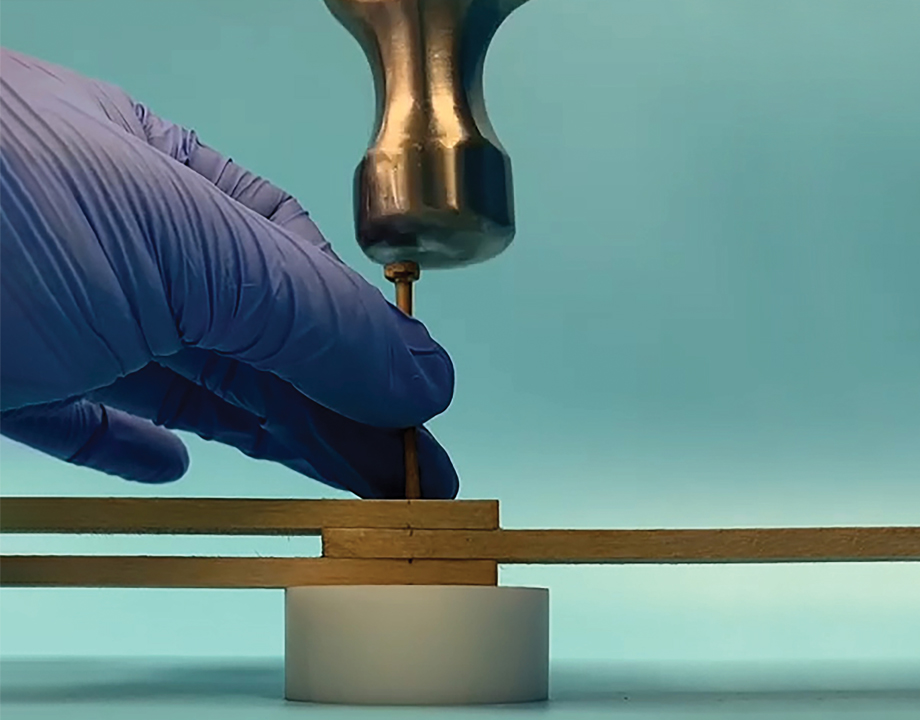