Metal Injection Molding or Metal Additive Manufacturing: Which One is Best for Your Project?
Metal Injection Molding or Metal Additive Manufacturing: Which One is Best for Your Project?
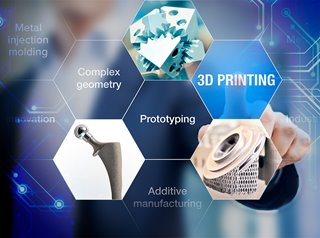
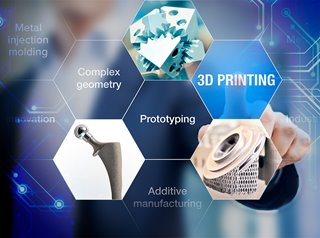
Both metal injection molding and metal additive manufacturing have unique attributes that can make either one the best choice for a project.
Metal injection molding (MIM) and metal additive manufacturing (metal AM) are two manufacturing techniques for making metal products and components. Based on the design, complexity, material, and production volume required for the part, each process has unique attributes that can make them the best choice for a project. Both processes are an alternative to traditional machining and provide engineers with a wider range of options for designing complex, high-quality metal components.
For projects that involve metals, engineers should consider MIM and metal AM as an alternative to standard CNC machining, especially for creating smaller and more complex parts. Depending on the project, they can also complement each other to achieve the highest tolerances and production speed, with the least amount of secondary processing steps.
Metal injection molding (MIM) combines plastic injection molding with metal powder fusion. A fine metal powder is mixed with a binder and injected into a mold—when the part is finished the binder is removed, leaving a metal part or structure that is then sintered into its final form.
MIM is often selected for small, complex parts with unique geometries that cannot be efficiently manufactured using other manufacturing methods—for example, medical devices and components.
A wide variety of metals can be processed with MIM, including stainless steel, steel alloys, iron-nickel alloys, cobalt alloys, tungsten alloys, and ceramics. Alloys can be customized for highly specific functions—for example, nickel and cobalt concentrations in carbon steel formulas can be modified for high-temperature automotive applications.
Because making a part with MIM requires only a single mold, the process is highly repeatable and produces parts consistent in size, shape, and strength. The process can also be easily automated for high-volume production and even higher quality. Most finishes on MIM parts are inferior compared to standard CNC machining and require secondary processes for smoother finishes and tight tolerances.
You May Also Like: How to Ride the Wave of Additive Manufacturing News
MIM is used frequently in the medical device, aerospace, automotive, and electronics fields. MIM can create dense, lightweight parts, or a single part that replaces multiple parts, to make a product that is lighter in weight (for example, automotive parts that will help meet tighter MPG or emission regulations in vehicles).
Overall, MIM is a cost-effective process, especially when producing complex or unusually shaped parts at high volumes (which helps offset the expense of making the mold).
Manufacturers often use metal AM to create complex, customized components that require specific mechanical characteristics or have intricate design features, for one-off or low-volume production—for example, patient-specific implants. The most popular metal AM processes are powder bed fusion technologies, which weld thin layers of metal powder together using a high energy source, such as a laser or electron beam. Titanium is the metal of choice for most AM applications, although new metal alloys are continuously coming into the AM market, including precious metals like gold and platinum.
An advantage of metal AM compared to MIM is that it does not require a mold, which provides engineers with more creative design possibilities. Metal AM is often used to produce complex lattice and porous structures—applications include aerospace parts (strong yet much lighter in weight—for example, turbine blades) and medical implants (open porosity into which bone can grow). However, metal AM can cost more per part compared to MIM and is not suited for high-volume production.
There are several ways MIM and metal AM can be combined to produce parts. For example, metal AM can be used to make prototypes, jigs, fixtures, and tooling for the metal injection molding process, streamlining production and reducing downtime.
Listen to This: The AI Evolution of Generative Computer-Aided Design
In a breakthrough development, Mitsubishi Chemical Advanced Materials has developed a new process called freeform injection molding that combines MIM and metal AM, which allows injection molders to make the same types of products as metal AM can, but stronger. The thermoplastic is injected into a 3D-printed mold made from a proprietary 3D printable liquid photopolymer resin that can be dissolved completely, revealing the completed injection-molded part. This process does not require a metal mold, which saves considerable time and cost.
Engineers can become too process-focused when they design new products; by combining technologies (CNC machining, laser machining, AM, and MIM), they can create hybrid, complementary manufacturing processes that not only enable the creation of one-of-a-kind products, but also optimize quality, save production time, reduce costs, and speed up time to market.
Mark Crawford is a technology writer based in Corrales, N.M.
For projects that involve metals, engineers should consider MIM and metal AM as an alternative to standard CNC machining, especially for creating smaller and more complex parts. Depending on the project, they can also complement each other to achieve the highest tolerances and production speed, with the least amount of secondary processing steps.
Metal Injection Molding (MIM)
Metal injection molding (MIM) combines plastic injection molding with metal powder fusion. A fine metal powder is mixed with a binder and injected into a mold—when the part is finished the binder is removed, leaving a metal part or structure that is then sintered into its final form.
MIM is often selected for small, complex parts with unique geometries that cannot be efficiently manufactured using other manufacturing methods—for example, medical devices and components.
A wide variety of metals can be processed with MIM, including stainless steel, steel alloys, iron-nickel alloys, cobalt alloys, tungsten alloys, and ceramics. Alloys can be customized for highly specific functions—for example, nickel and cobalt concentrations in carbon steel formulas can be modified for high-temperature automotive applications.
Because making a part with MIM requires only a single mold, the process is highly repeatable and produces parts consistent in size, shape, and strength. The process can also be easily automated for high-volume production and even higher quality. Most finishes on MIM parts are inferior compared to standard CNC machining and require secondary processes for smoother finishes and tight tolerances.
You May Also Like: How to Ride the Wave of Additive Manufacturing News
MIM is used frequently in the medical device, aerospace, automotive, and electronics fields. MIM can create dense, lightweight parts, or a single part that replaces multiple parts, to make a product that is lighter in weight (for example, automotive parts that will help meet tighter MPG or emission regulations in vehicles).
Overall, MIM is a cost-effective process, especially when producing complex or unusually shaped parts at high volumes (which helps offset the expense of making the mold).
Metal Additive Manufacturing (Metal AM)
Manufacturers often use metal AM to create complex, customized components that require specific mechanical characteristics or have intricate design features, for one-off or low-volume production—for example, patient-specific implants. The most popular metal AM processes are powder bed fusion technologies, which weld thin layers of metal powder together using a high energy source, such as a laser or electron beam. Titanium is the metal of choice for most AM applications, although new metal alloys are continuously coming into the AM market, including precious metals like gold and platinum.
An advantage of metal AM compared to MIM is that it does not require a mold, which provides engineers with more creative design possibilities. Metal AM is often used to produce complex lattice and porous structures—applications include aerospace parts (strong yet much lighter in weight—for example, turbine blades) and medical implants (open porosity into which bone can grow). However, metal AM can cost more per part compared to MIM and is not suited for high-volume production.
MIM + Metal AM
There are several ways MIM and metal AM can be combined to produce parts. For example, metal AM can be used to make prototypes, jigs, fixtures, and tooling for the metal injection molding process, streamlining production and reducing downtime.
Listen to This: The AI Evolution of Generative Computer-Aided Design
In a breakthrough development, Mitsubishi Chemical Advanced Materials has developed a new process called freeform injection molding that combines MIM and metal AM, which allows injection molders to make the same types of products as metal AM can, but stronger. The thermoplastic is injected into a 3D-printed mold made from a proprietary 3D printable liquid photopolymer resin that can be dissolved completely, revealing the completed injection-molded part. This process does not require a metal mold, which saves considerable time and cost.
Engineers can become too process-focused when they design new products; by combining technologies (CNC machining, laser machining, AM, and MIM), they can create hybrid, complementary manufacturing processes that not only enable the creation of one-of-a-kind products, but also optimize quality, save production time, reduce costs, and speed up time to market.
Mark Crawford is a technology writer based in Corrales, N.M.