Microscale Hydraulic Gripper Features Soft Touch
Microscale Hydraulic Gripper Features Soft Touch
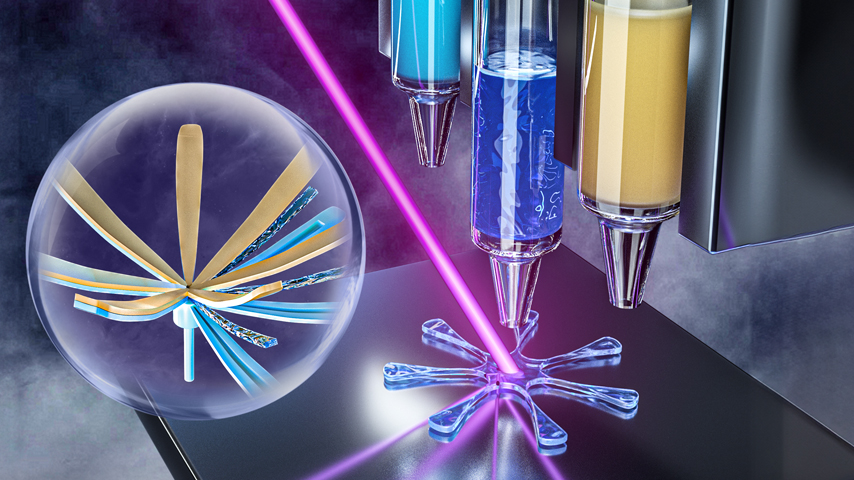
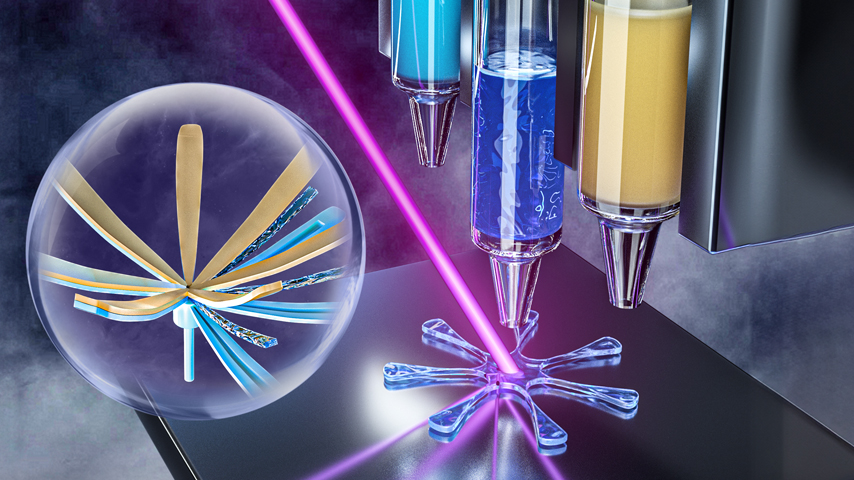
A shape memory polymer allows the gripper to be more efficient than a purely hydraulic system. Roboticists may soon create miniature tools for minimally invasive surgery.
Hydraulics has for some thousands of years been an exclusively macro phenomenon. Excavators, elevators, and flight simulators all use fluid power to move large, heavy components. But a team of researchers at North Carolina State University have created a set of soft hydraulic grippers that work on the opposite end of the scale.
The team 3D-printed “miniature soft hydraulic actuators” using a novel method that creates tiny channels for fluid. The shape memory polymer that makes up the gripper allows it to be more efficient than a purely hydraulic system. Using their method, roboticists may soon create miniature tools for minimally invasive surgery.
Developing hydraulics at the micro scale has been nearly impossible till now because of the difficulty of creating sub-millimeter sized channels.
“Shrinking down to this size is kind of challenging,” said Yinding Chi, who worked on the project as a doctoral student at the university, and is co-first author of the paper “Fully 3D-Printed Miniature Soft Hydraulic Actuators with Shape Memory Effect for Morphing and Manipulation,” which appeared in Advanced Materials this spring. “Usually, people have the supporting material filled inside all the channels, but it's very hard to remove it if everything is solid.”
To overcome this hurdle, Chi and his colleagues used a conventional 3D-printer (a Stratasys Objet260 Connex3) but swapped the usual supporting material with cleaning fluid.
“Our idea is very unique,” said Haitao Qing, another doctoral student at the university and co-first author of the paper. “We printed the microfluidic channels in the soft materials in one single step by replacing the supporting material with non-curing fluid.”
At the micro scale, lines of fluid stay organized and there were no defects of liquid pattern. After being sandwiched in elastomers, the fluid is simply squeezed out.
The successful creation of the channels is only one part of what makes these mini hydraulic grippers remarkable. In addition to the sandwiching elastomer, there is a layer of shape memory polymer. This allows the assembled slab of soft material—a mere half a millimeter thick—to hold its shape when heated. In short, fluid is first pumped into the actuator so that it changes shape, then it’s heated, locking the shape into place; after cooling, the memory aspect of the polymer kicks in and the fluid can be removed. This eliminates the energy needed to keep constant hydraulic pressure in other systems.
“It’s a huge improvement for soft robotics,” Chi said. “You don’t have to continuously pump hydraulic pressure into, but it can still fix that changed shape and hold the object.”
Simply reheat the gripper and it can return to its original shape.
Renew Your ASME Membership ... and Enjoy the Benefits
The researchers have created a handful of grippers, including a flower-shaped gripper whose petals curl in to clutch whatever is at its center, a leaf-like pad that can softly cradle a tiny object, and a wrapping ribbon that can curl around a cylinder. With a two-pronged pincher has they have successfully grabbed a human hair, lifted an ant, and plucked a tiny shrimp from a vessel of water, transferring it to another. The ant and shrimp were unharmed after having been moved.
At the moment, it takes about two minutes to heat the polymer so that it retains its shape. That heating could be done with water, infrared light, or electricity. And its response is likely to be made faster by altering the composition of the shape-memory polymer. Also, at the moment, the interaction between the non-curable fluid and the solid creates an unstable material. But that too will likely be fixed with a little tinkering.
“I think in the future we can change the recipe of materials to make it more efficient and more applicable,” Qing said.
Michael Abrams is a technology writer in Westfield, N.J.
The team 3D-printed “miniature soft hydraulic actuators” using a novel method that creates tiny channels for fluid. The shape memory polymer that makes up the gripper allows it to be more efficient than a purely hydraulic system. Using their method, roboticists may soon create miniature tools for minimally invasive surgery.
Developing hydraulics at the micro scale has been nearly impossible till now because of the difficulty of creating sub-millimeter sized channels.
“Shrinking down to this size is kind of challenging,” said Yinding Chi, who worked on the project as a doctoral student at the university, and is co-first author of the paper “Fully 3D-Printed Miniature Soft Hydraulic Actuators with Shape Memory Effect for Morphing and Manipulation,” which appeared in Advanced Materials this spring. “Usually, people have the supporting material filled inside all the channels, but it's very hard to remove it if everything is solid.”
To overcome this hurdle, Chi and his colleagues used a conventional 3D-printer (a Stratasys Objet260 Connex3) but swapped the usual supporting material with cleaning fluid.
“Our idea is very unique,” said Haitao Qing, another doctoral student at the university and co-first author of the paper. “We printed the microfluidic channels in the soft materials in one single step by replacing the supporting material with non-curing fluid.”
At the micro scale, lines of fluid stay organized and there were no defects of liquid pattern. After being sandwiched in elastomers, the fluid is simply squeezed out.
The successful creation of the channels is only one part of what makes these mini hydraulic grippers remarkable. In addition to the sandwiching elastomer, there is a layer of shape memory polymer. This allows the assembled slab of soft material—a mere half a millimeter thick—to hold its shape when heated. In short, fluid is first pumped into the actuator so that it changes shape, then it’s heated, locking the shape into place; after cooling, the memory aspect of the polymer kicks in and the fluid can be removed. This eliminates the energy needed to keep constant hydraulic pressure in other systems.
“It’s a huge improvement for soft robotics,” Chi said. “You don’t have to continuously pump hydraulic pressure into, but it can still fix that changed shape and hold the object.”
Simply reheat the gripper and it can return to its original shape.
Renew Your ASME Membership ... and Enjoy the Benefits
The researchers have created a handful of grippers, including a flower-shaped gripper whose petals curl in to clutch whatever is at its center, a leaf-like pad that can softly cradle a tiny object, and a wrapping ribbon that can curl around a cylinder. With a two-pronged pincher has they have successfully grabbed a human hair, lifted an ant, and plucked a tiny shrimp from a vessel of water, transferring it to another. The ant and shrimp were unharmed after having been moved.
At the moment, it takes about two minutes to heat the polymer so that it retains its shape. That heating could be done with water, infrared light, or electricity. And its response is likely to be made faster by altering the composition of the shape-memory polymer. Also, at the moment, the interaction between the non-curable fluid and the solid creates an unstable material. But that too will likely be fixed with a little tinkering.
“I think in the future we can change the recipe of materials to make it more efficient and more applicable,” Qing said.
Michael Abrams is a technology writer in Westfield, N.J.