Shaking Up Ore to Release Valuable Lithium
Shaking Up Ore to Release Valuable Lithium
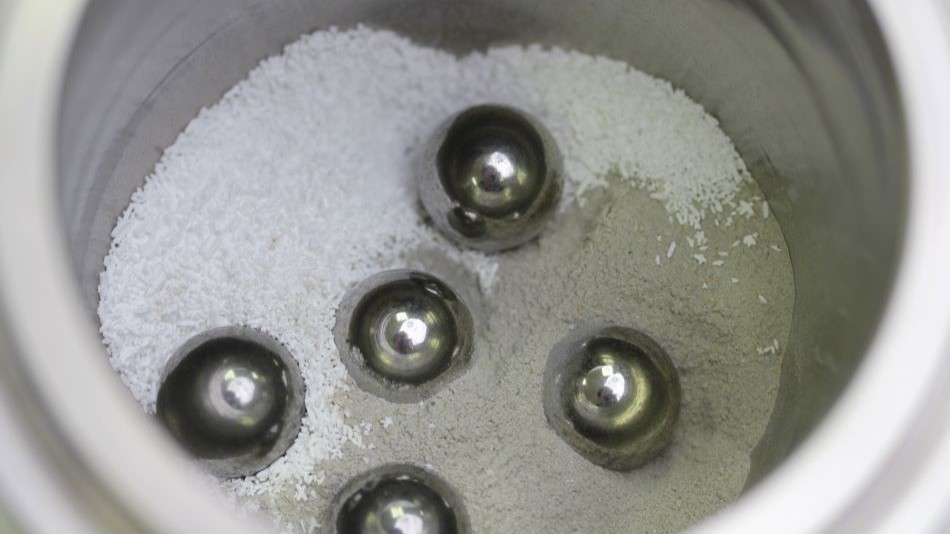
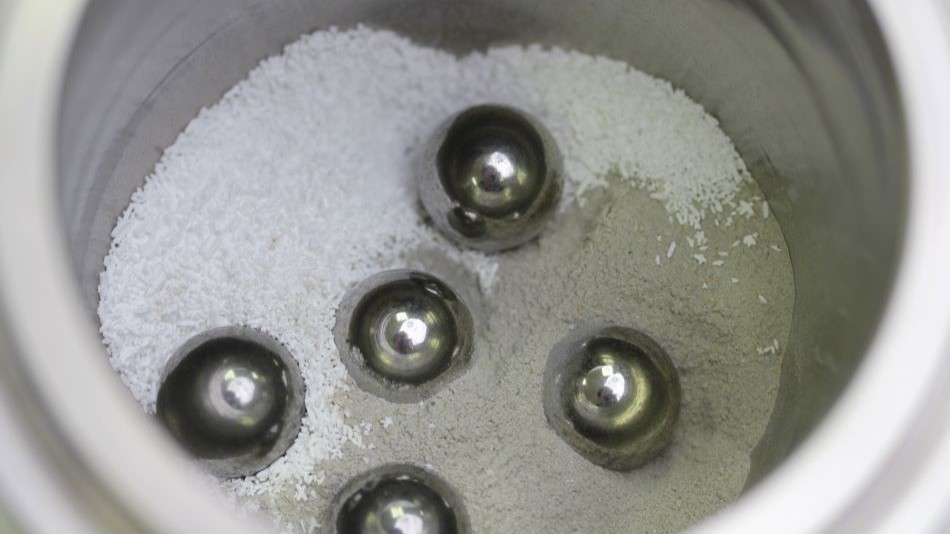
Mechanochemistry promises a low-temperature way to access lithium tied up in rocks.
The United States gets most of its lithium-ion batteries from China, which has led at times to supply chain challenges. But it doesn’t have to be that way. The U.S. is sitting on some of the biggest lithium deposits in the world—at least 14 million tons, according to the U.S. Geological Survey.
Given that demand for the metal is forecast to increase by a factor of five or even 10 times, addressing local availability is a key challenge to energy security. Ihor Hlova, a scientist at the Critical Materials Innovation (CMI) Hub at Ames National Laboratory, is leading research to address the problem.
One of the issues said, Hlova, is that the lithium in the United States is tied up in a rock-hard mineral called spodumene, lithium aluminum inosilicate, LiAl(SiO₃)₂. Extraction of lithium from spodumene involves a series of expensive and energy-intensive steps that emit unwanted greenhouse gases and result in hazardous waste streams. The two-step process involves heating the mineral ore twice. First, spodumene is roasted at 1,050 °C (1,976 °F) to convert it into a state suitable for chemical processing. Then it is heated along with chemicals to a temperature of around 250 °C to a form suitable for Li-ion battery production.
(Lithium brines, salt groundwater containing lithium, are an alternative to spodumene; up to now the easiest way to access the mineral is to let the brines evaporate from shallow ponds over the course of a couple years.)
“When you extract lithium from spodumene you need to convert the tightly packed alpha spodumene to an open structure that is more easily susceptible to chemical attacks by acids, facilitating Li leaching,” Hlova said.
But the process requires a lot of harsh conditions. “This conversion step is done at temperatures around 1,050 °C, which requires a lot of energy and generates substantial greenhouse emissions,” Hlova said. “What we propose is to eliminate this conversion from alpha to beta, and then use some milder conditions to extract lithium,” he said.
Hlova’s approach is to use mechanochemistry, which harnesses kinetic energy to cause chemical reactions and get at the lithium. Called Mechanochemical Extraction of Lithium at Low Temperatures (MELLT), the process involves ball milling.
Hlova and his colleagues used steel balls as grinding media to cause a reaction between solid spodumene pieces and a solid reactant chemical such as sodium bicarbonate. Moving the chamber rapidly enough caused shear and impact stresses on the materials, triggering a reaction.
More about Minerals: California Looks to Develop Its Lithium Valley
“If you use mechanochemistry, [repeated stresses] on the structure can amorphize it,” Hlova said. “You don’t need high temperatures or harsh chemicals to extract the lithium, just water will do.”
However, mechanochemistry is not recommended for all reactions, especially in those instances where the crystalline structure of the final product needs to be preserved. The process also introduces around a small but significant percentage of impurities, which might not be allowable for all applications. (In the ball milling of spodumene, a small amount of iron makes its way into the final product but it can be filtered out using water).
New Energy Economy: Iron Flow Battery Could Aid Electric Grid
“Right now, we are not extracting lithium from our spodumene reserves as much as we could, because the technology is quite expensive,” Hlova said. “If we could develop and scale this green method for extraction, that would prove very helpful to extract lithium from the deposit that we have in the U.S.” Hlova said, “and we would have our own steady source of lithium, which is a critical strategic material.”
As part of next steps, Hlova and his team will work with the Colorado School of Mines to scale up the laboratory experiments. “We will then have baseline data to perform techno-economical analysis and life cycle assessment,” Hlova said, “which will show us how commercially viable this approach is and what impact it has on the environment.”
Poornima Apte is a technology writer in Walpole, Mass.
Given that demand for the metal is forecast to increase by a factor of five or even 10 times, addressing local availability is a key challenge to energy security. Ihor Hlova, a scientist at the Critical Materials Innovation (CMI) Hub at Ames National Laboratory, is leading research to address the problem.
One of the issues said, Hlova, is that the lithium in the United States is tied up in a rock-hard mineral called spodumene, lithium aluminum inosilicate, LiAl(SiO₃)₂. Extraction of lithium from spodumene involves a series of expensive and energy-intensive steps that emit unwanted greenhouse gases and result in hazardous waste streams. The two-step process involves heating the mineral ore twice. First, spodumene is roasted at 1,050 °C (1,976 °F) to convert it into a state suitable for chemical processing. Then it is heated along with chemicals to a temperature of around 250 °C to a form suitable for Li-ion battery production.
(Lithium brines, salt groundwater containing lithium, are an alternative to spodumene; up to now the easiest way to access the mineral is to let the brines evaporate from shallow ponds over the course of a couple years.)
The alternative: mechanochemistry
Hlova suggests an alternative to one of the methods used to extract lithium: the processing of spodumene.“When you extract lithium from spodumene you need to convert the tightly packed alpha spodumene to an open structure that is more easily susceptible to chemical attacks by acids, facilitating Li leaching,” Hlova said.
But the process requires a lot of harsh conditions. “This conversion step is done at temperatures around 1,050 °C, which requires a lot of energy and generates substantial greenhouse emissions,” Hlova said. “What we propose is to eliminate this conversion from alpha to beta, and then use some milder conditions to extract lithium,” he said.
Hlova’s approach is to use mechanochemistry, which harnesses kinetic energy to cause chemical reactions and get at the lithium. Called Mechanochemical Extraction of Lithium at Low Temperatures (MELLT), the process involves ball milling.
Hlova and his colleagues used steel balls as grinding media to cause a reaction between solid spodumene pieces and a solid reactant chemical such as sodium bicarbonate. Moving the chamber rapidly enough caused shear and impact stresses on the materials, triggering a reaction.
More about Minerals: California Looks to Develop Its Lithium Valley
“If you use mechanochemistry, [repeated stresses] on the structure can amorphize it,” Hlova said. “You don’t need high temperatures or harsh chemicals to extract the lithium, just water will do.”
The role of mechanochemistry
If mechanochemistry can extract lithium in an environmentally friendly manner, wouldn’t it work for a wider range of processes? The technique is used for a few cases like making aluminum hydride, used for hydrogen storage. It’s also used to decrease the resistance of chemicals to conversion, breaking down minerals so they can be processed in one heat treatment instead of a multi-step process.However, mechanochemistry is not recommended for all reactions, especially in those instances where the crystalline structure of the final product needs to be preserved. The process also introduces around a small but significant percentage of impurities, which might not be allowable for all applications. (In the ball milling of spodumene, a small amount of iron makes its way into the final product but it can be filtered out using water).
New Energy Economy: Iron Flow Battery Could Aid Electric Grid
“Right now, we are not extracting lithium from our spodumene reserves as much as we could, because the technology is quite expensive,” Hlova said. “If we could develop and scale this green method for extraction, that would prove very helpful to extract lithium from the deposit that we have in the U.S.” Hlova said, “and we would have our own steady source of lithium, which is a critical strategic material.”
As part of next steps, Hlova and his team will work with the Colorado School of Mines to scale up the laboratory experiments. “We will then have baseline data to perform techno-economical analysis and life cycle assessment,” Hlova said, “which will show us how commercially viable this approach is and what impact it has on the environment.”
Poornima Apte is a technology writer in Walpole, Mass.
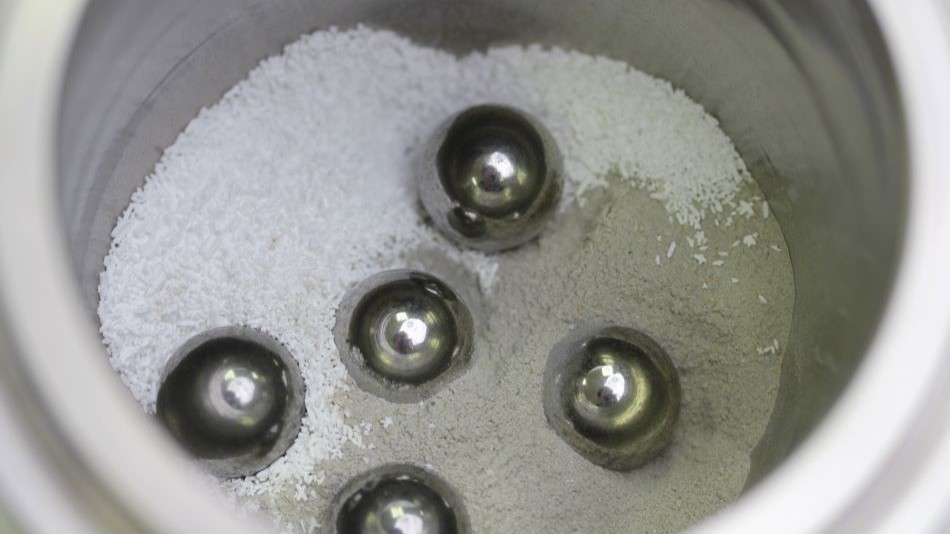
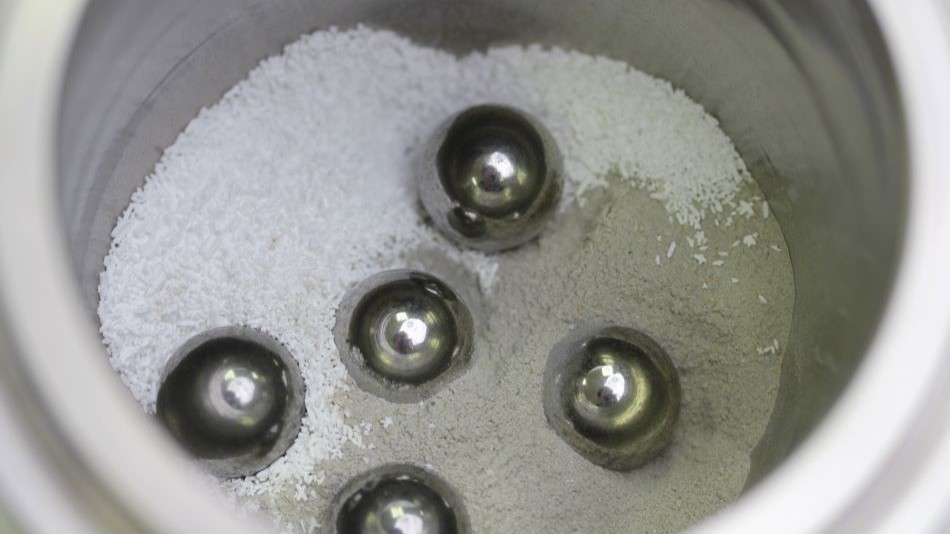