Training the Next Generation of Engineers
Training the Next Generation of Engineers
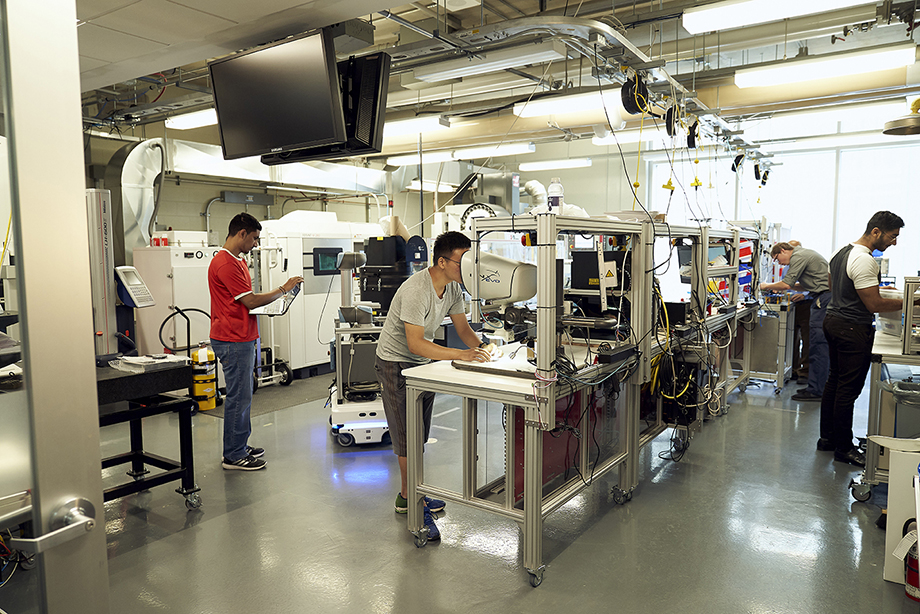
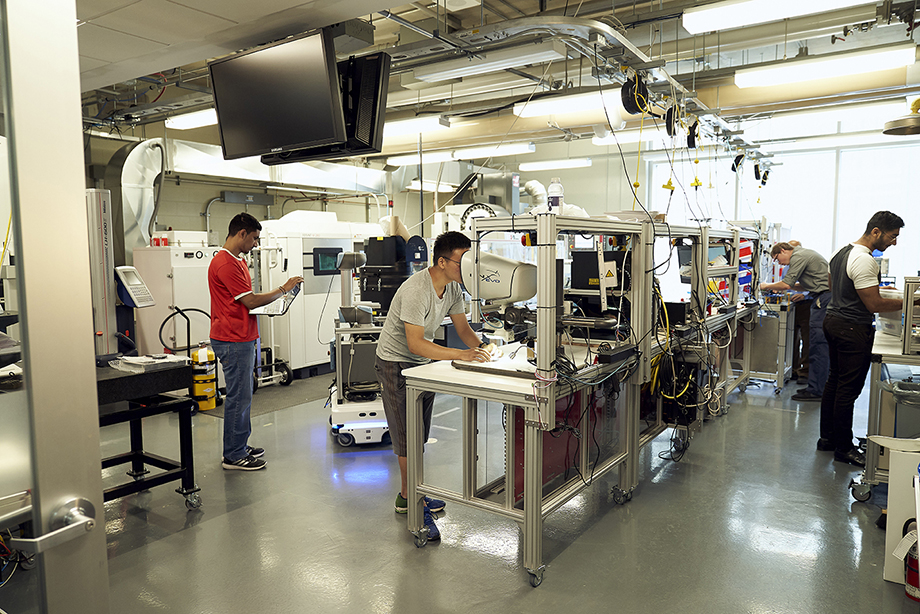
As we move toward Industry 4.0, the field is relying on “learning factories” to give mechanical and industrial engineers hands-on experience in emerging technologies. Photo: McMaster University
When Pennsylvania State University opened the Bernard M. Gordon Learning Factory more than a quarter-century ago, it was primarily a machine shop to support mechanical and industrial engineering students as they worked on their senior Capstone projects. Today, however, it provides unique, hands-on training opportunities for both students and manufacturing workers–offering a foundation in the automation and “smart” manufacturing methods that underlie Industry 4.0.
“These innovative technologies require a deepened engagement across different disciplines,” said Matthew Parkinson, a mechanical engineering professor and director of Penn State’s Learning Factory. “Manufacturing, as an industry, is looking for engineers who can work in this kind of multidisciplinary space, yet, historically, it was a challenge to find ways for mechanical engineering, industrial engineering, and computer science to work together. Industry 4.0 is just a natural way to build those kinds of collaborations, so our students are ready to work with these technologies.”
As more manufacturing organizations become interested in integrating machine learning, cloud computing, the Internet of Things (IoT), embedded software systems, and other next-generation technologies on to the factory floor, they are finding a lack of skilled engineers to help them do so.
Manufacturing Blog: Engineers Needed to Fill AI Tool Gaps
Grant Richards, assistant professor of practice in the School of Engineering Technology, who, with professor of engineering technology, Ragu Athinarayanan, is leading the development of a new learning factory at Purdue University, said they are hoping to fill that gap by getting undergraduates into their “cyber-physical manufacturing environment” on day one. The new facility is expected to open in August 2022 and start welcoming students the following spring semester.
“We are generating a new workforce that understands what’s involved in transitioning from Industry 3.0 to Industry 4.0,” he explained. “With our new facility, we hope to not only introduce the technology to our students–but produce change agents that can go out into the manufacturing world and really help usher in these new processes.”
Keeping up with Industry 4.0
To date, large manufacturing companies like Siemens and Pratt & Whitney have created small learning factories within their own operations to train their workforce, as well as a few choice engineering interns each summer. Yet, having such large-scale facilities at prominent engineering universities, supported by vital industry partnerships, allows both academia and industry to keep up with the latest and greatest technologies and grow into Industry 4.0 in a rather symbiotic way. Industry players often sponsor specific projects to test innovative ideas, devices, and automation processes before committing to any big changes. It’s a win-win: Manufacturers can try new things and students get the opportunity to do hands-on work with different “smart” technologies before matriculating.
Listen to a Podcast on Preparing the Workforce for Digital Transformation
“One of the largest benefits of a learning factory is that it is a safe environment to do testing of new technologies,” said Dan Centea, professor of mechanical engineering and head of McMaster University’s Learning Factory in Canada. “You can’t go into a real-world factory and try a new automation system with disrupting production. You can’t do research into new methods or embedded systems in a working factory. But you can test and try new things here–and learn what works and what doesn’t work for a particular manufacturing problem without any risks to real-life production.”
Centea added that many traditional manufacturing outfits, especially smaller organizations, are intrigued by the potential of Industry 4.0 yet wary of large investments into these newer technologies.
“Too often, manufacturers do not have the knowledge to effectively implement many of these technologies,” he said. “They do not realize the benefits of them–or understand where they might be useful. They also don’t have the people with the right skill sets to answer their questions about Industry 4.0 or implement the technologies. So, when we can train students and train people already working in manufacturing in these areas, we not only increase awareness but also help manufacturing companies, big or small, move into Industry 4.0.”
A Multidisciplinary Approach
Most learning factories don’t just educate students, they also offer workshops and seminars for engineers, plant managers, and key manufacturing workers to help them stay abreast of the latest advances. That combination of education, research, and training is of benefit to the entire industry, as seen by the innovations fueled by government-funded learning factories in Germany and other European countries.
Editors' Pick: 10 Innovative Engineering Institutes
Dan Spillane, a graduate student in engineering design at Penn State, said working in the learning factory has helped him understand the nuances of applying “smart” technologies to traditional manufacturing processes as well as how to better work with students from other disciplines to solve challenging design problems.
“The learning factory is a great way to get in the door and integrate these typically software-heavy IoT and automation processes in a way that you can really understand what it takes to put these devices in the manufacturing space,” he said. “I’ve now worked on several projects and having the combination of computer science and computer engineering with industrial and mechanical engineering really is indispensable to understanding how it all can and should work.”
Kayt Sukel is a freelance writer and author in Houston, Tex.
“These innovative technologies require a deepened engagement across different disciplines,” said Matthew Parkinson, a mechanical engineering professor and director of Penn State’s Learning Factory. “Manufacturing, as an industry, is looking for engineers who can work in this kind of multidisciplinary space, yet, historically, it was a challenge to find ways for mechanical engineering, industrial engineering, and computer science to work together. Industry 4.0 is just a natural way to build those kinds of collaborations, so our students are ready to work with these technologies.”
As more manufacturing organizations become interested in integrating machine learning, cloud computing, the Internet of Things (IoT), embedded software systems, and other next-generation technologies on to the factory floor, they are finding a lack of skilled engineers to help them do so.
Manufacturing Blog: Engineers Needed to Fill AI Tool Gaps
Grant Richards, assistant professor of practice in the School of Engineering Technology, who, with professor of engineering technology, Ragu Athinarayanan, is leading the development of a new learning factory at Purdue University, said they are hoping to fill that gap by getting undergraduates into their “cyber-physical manufacturing environment” on day one. The new facility is expected to open in August 2022 and start welcoming students the following spring semester.
“We are generating a new workforce that understands what’s involved in transitioning from Industry 3.0 to Industry 4.0,” he explained. “With our new facility, we hope to not only introduce the technology to our students–but produce change agents that can go out into the manufacturing world and really help usher in these new processes.”
Keeping up with Industry 4.0
To date, large manufacturing companies like Siemens and Pratt & Whitney have created small learning factories within their own operations to train their workforce, as well as a few choice engineering interns each summer. Yet, having such large-scale facilities at prominent engineering universities, supported by vital industry partnerships, allows both academia and industry to keep up with the latest and greatest technologies and grow into Industry 4.0 in a rather symbiotic way. Industry players often sponsor specific projects to test innovative ideas, devices, and automation processes before committing to any big changes. It’s a win-win: Manufacturers can try new things and students get the opportunity to do hands-on work with different “smart” technologies before matriculating.
Listen to a Podcast on Preparing the Workforce for Digital Transformation
“One of the largest benefits of a learning factory is that it is a safe environment to do testing of new technologies,” said Dan Centea, professor of mechanical engineering and head of McMaster University’s Learning Factory in Canada. “You can’t go into a real-world factory and try a new automation system with disrupting production. You can’t do research into new methods or embedded systems in a working factory. But you can test and try new things here–and learn what works and what doesn’t work for a particular manufacturing problem without any risks to real-life production.”
Centea added that many traditional manufacturing outfits, especially smaller organizations, are intrigued by the potential of Industry 4.0 yet wary of large investments into these newer technologies.
“Too often, manufacturers do not have the knowledge to effectively implement many of these technologies,” he said. “They do not realize the benefits of them–or understand where they might be useful. They also don’t have the people with the right skill sets to answer their questions about Industry 4.0 or implement the technologies. So, when we can train students and train people already working in manufacturing in these areas, we not only increase awareness but also help manufacturing companies, big or small, move into Industry 4.0.”
A Multidisciplinary Approach
Most learning factories don’t just educate students, they also offer workshops and seminars for engineers, plant managers, and key manufacturing workers to help them stay abreast of the latest advances. That combination of education, research, and training is of benefit to the entire industry, as seen by the innovations fueled by government-funded learning factories in Germany and other European countries.
Editors' Pick: 10 Innovative Engineering Institutes
Dan Spillane, a graduate student in engineering design at Penn State, said working in the learning factory has helped him understand the nuances of applying “smart” technologies to traditional manufacturing processes as well as how to better work with students from other disciplines to solve challenging design problems.
“The learning factory is a great way to get in the door and integrate these typically software-heavy IoT and automation processes in a way that you can really understand what it takes to put these devices in the manufacturing space,” he said. “I’ve now worked on several projects and having the combination of computer science and computer engineering with industrial and mechanical engineering really is indispensable to understanding how it all can and should work.”
Kayt Sukel is a freelance writer and author in Houston, Tex.
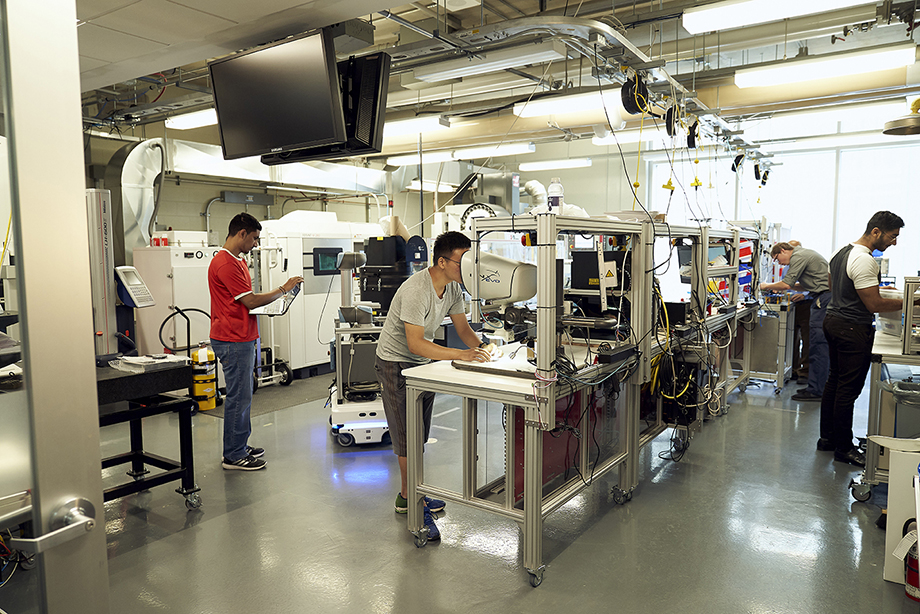
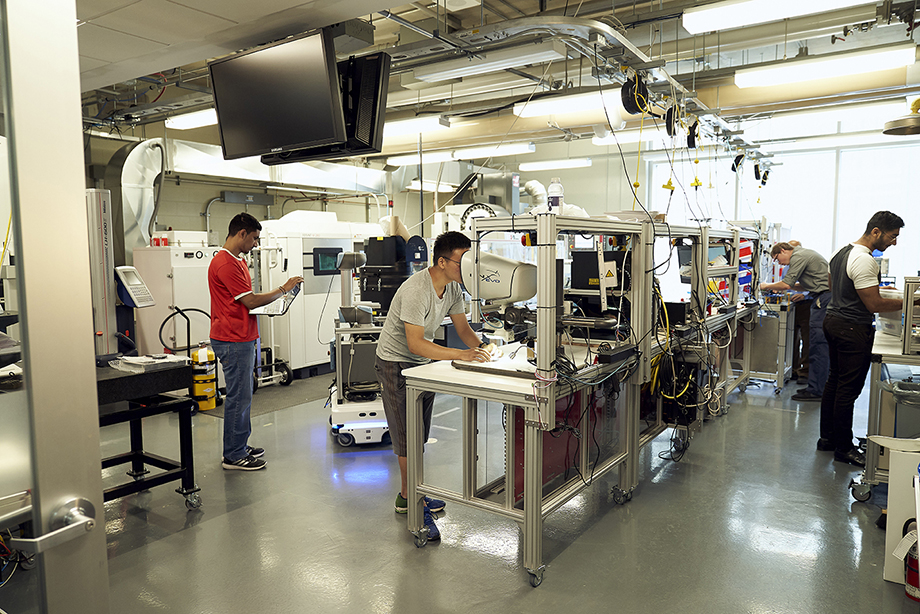