What’s the Deal with Graphene?
What’s the Deal with Graphene?
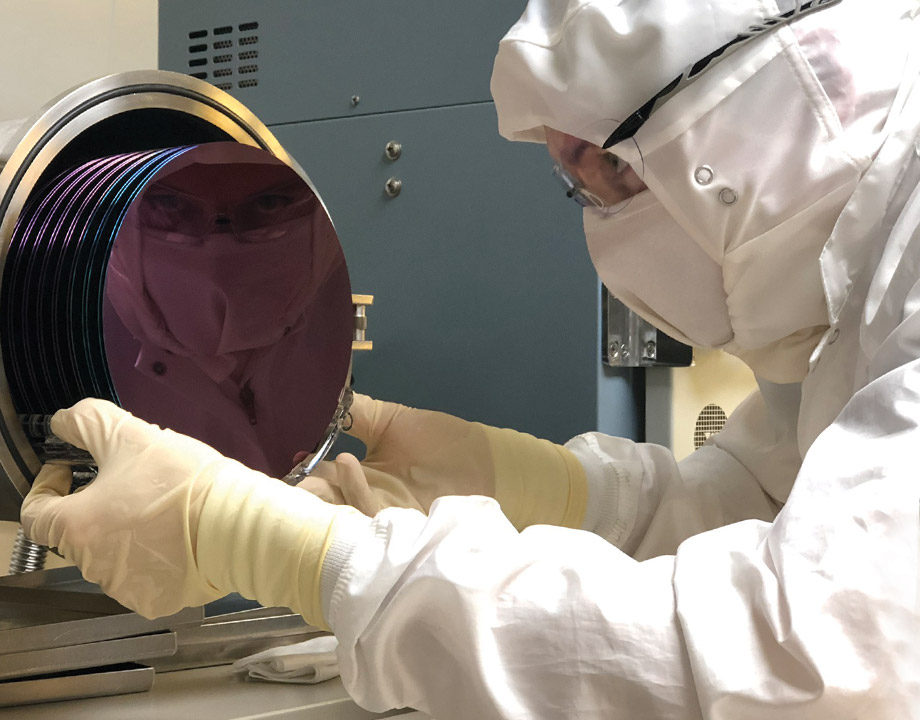
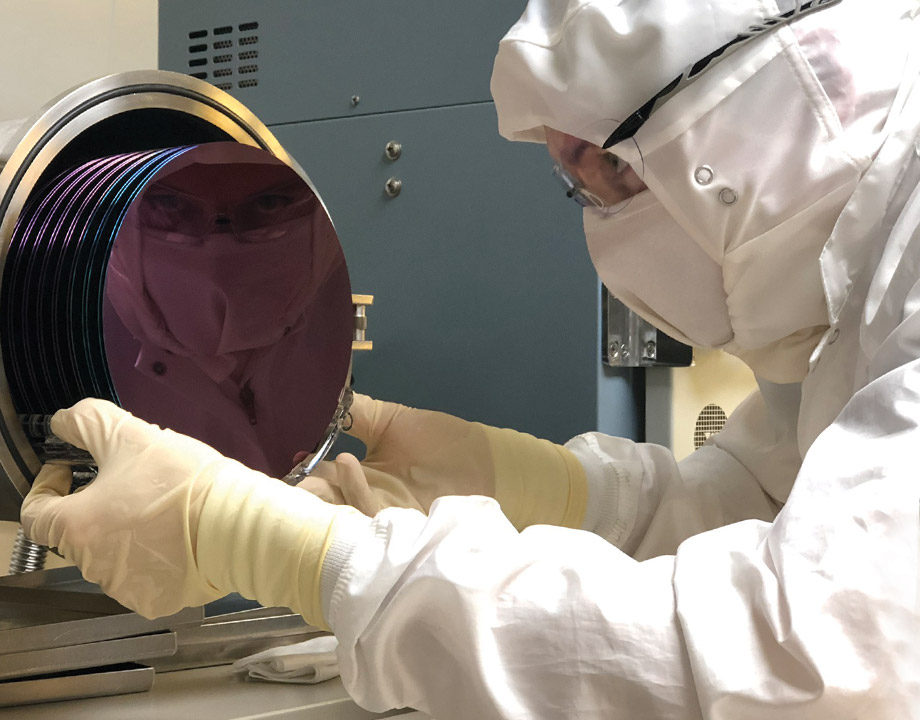
San Diego-based manufacturer Grolltex says its graphene plant can produce up to 30,000 eight-inch wafers per year. The company says it could make much more if demand warranted. Photo: Grolltex
Jeffrey Draa is selling a material lighter than a feather, hundreds of times stronger than steel, and ten times more conductive than copper. Like the maker of the proverbial better mousetrap, he might expect the world to beat a path to his door.
That hasn’t been Draa’s experience. According to Draa, co-founder and CEO of Grolltex in San Diego, Calif., his company has found a way to mass produce high-quality graphene, the one-atom-thick molecular form of carbon that’s been touted as the next great thing. Earlier this year Grolltex completed an expansion of its fabrication facility and can now produce the equivalent of 30,000 eight-inch wafers per year.
He could make more, much more. “I am ready to ramp up a factory today, to make miles and miles of sheet graphene,” Draa said. “However, I don’t have anybody knocking on my door saying that they want miles and miles of it.”
In spite of its wondrous laboratory-scale properties, engineers have been hesitant to incorporate graphene into their mission-critical designs. There is still a lot that is not known about this material, including how much of an environmental and health risk will it pose. A number of products and prototypes have failed to meet expectations. Then there is the question of a supply chain being developed at scale where there is none today.
But up to now, there’s also been the first-mover problem, with manufacturers, investors, and developers each waiting for the other to make a move. Why produce graphene at scale when there’s no market? And why design graphene-enabled products when there’s no supply?
But that stalemate looks to change soon. In addition to Grolltex, other manufacturers are starting to produce graphene at scale. And manufacturers are edging into limited uses for the material in applications as diverse as touch screens and auto parts.
For now, people can still ask, “If graphene is really so great, why aren’t we seeing more of it being used today?” But soon, there may be a ready reply: It’s all around us.
Impossibly Thin
Graphene is a term that’s been thrown around somewhat indiscriminately to describe a range of materials. The basis of any graphene is a single-atom-thick sheet of carbon, but the term has been extended to encompass materials derived from graphene—such as graphene oxide, which has oxygen atoms attached to the edges—or two-dimensional sheets made from other material, such as borophene, in which boron atoms take the place of carbons.
Scientists have realized that impossibly thin sheets of carbon could in theory be produced since the work of English chemist Benjamin Collins Brodie in 1859, and in the late 1940s, Canadian physicist P.R. Wallace recognized that pure, defect-free graphene would have impressive material properties. Graphene was at that point an imaginary molecule—it had never been seen in the laboratory and no one was sure that isolating a single sheet of graphene was even possible.
Recommended for You 3D Printing in Space
When scientists finally produced single sheets of pure graphene in 2004, they did it without high-tech equipment. Andre Geim and Konstantin Novoselov at the University of Manchester in England rubbed adhesive tape over a block of graphite and then peeled off layers of graphene. Their work, which earned them the Nobel Prize in Chemistry in 2010, touched off a rush to confirm the extraordinary properties of graphene and figure out how to produce the material in bulk.
Graphene’s remarkable properties derive from the hexagonal lattice structure that the atoms form, which Joseph Meany, co-author of the book Graphene: The Superstrong, Superthin, and Superversatile Material That Will Revolutionize the World, describes as “a chicken wire fence.” Each carbon atom, with its four electrons in the outer shell is bonded to three other carbon atoms. This structure allows it to lay perfectly flat, providing amazing strength, fantastic conductivity (electrical and thermal), while remaining porous and optically transparent.
To put some numbers around this, graphene has an ultimate tensile strength of 130 GPa—that’s 325 times greater than structural steel. At the same time, a single sheet of graphene weighs a mere 770 micrograms per square meter. According to Spanish manufacturer Graphenea, that means that a sheet big enough to cover an entire football field would weigh less than a gram.
Those are theoretical material limits and apply to pure graphene that is entirely free of imperfections. Real-world testing of actual manufactured samples yield results that are less magical but still impressive. For instance, sheets of graphene between 2 and 8 Nm thick were tested and found to have a Young's Modulus of 500 GPa and thermal conductivity ranging between 3,500 and 5,000 W/m2. Electron mobility has been demonstrated at 15,000 cm2·V−1·s−1 with a theoretical limit as high as 200,000. Both electrical and thermal conductivity are roughly ten times that of copper.
Once tests seemed to confirm some of graphene’s predicted properties, the material became the latest carbon construct—following on the heels of buckminsterfullerene and carbon nanotubes—to become hyped. “One of the challenges,” Meany said, “is getting designers and developers to understand that you can't necessarily say that just because they are going to slap some graphene flakes into a composite that you should expect it to magically become super-strong and super-hard.”
Where are the Wonder Products?
Some materials incorporating graphene do display a breathtaking range of useful properties. One manufacturer, Directa Plus, describes items containing their G+ graphene additive as “stronger, more absorbent, able to conduct heat and electricity, or enjoy properties such as a barrier effect, low friction and better resistance to wear.”
Consider graphene-based apparel as an example of how versatile graphene can be. Super-strong graphene polymer fibers can be made into safety gloves. Adding graphene to textiles can provide exceptional durability, heat-dissipation, bacteriostatic properties, and electrical conductivity for smart wearables as well as for energy harvesting.
Top Story: State of American Manufacturing 2019
Other protective gear, such as a motorcycle helmet already on the market, incorporate a graphene coating that allows for better distribution of impact force. An extremely light and thin bullet-proof vest can locally produce a super-hard diamond-like structure upon impact.
The combination of high electrical conductivity and strength make graphene an ideal candidate for battery electrodes and solar cells. Bicycle tires containing graphene are stiff when rolling in a straight line but become flexible when cornering. European researchers have demonstrated how graphene can enable low-power, ultra-wide bandwidth optical communications with the potential to exceed the bandwidth demands for 5G, the Internet of Things, and Industry 4.0.
In spite of all that, a quick look through the sporting goods aisles and electronics shops betrays a decided lack of graphene-based wonder products. Where are they?
One of the factors holding back graphene applications until recently has been a lack of mass production. To be sure, chemists have progressed far past the pulling-sheets-from-pencils method used by Geim and Novoselov, but it is still very much a work in progress and the subject of considerable research.
There are dozens of ways to make graphene, but the most common approaches fall into two primary camps. The first, which can trace its roots back to Manchester, is called “exfoliated” or solution graphene. This approach now employs more sophisticated methods for removing the super-thin layers from graphite using some combination of mechanical and chemical action. The result is graphene flakes, or “nano-platelets” as they are sometimes called, consisting of between three and 20 layers.
XG Science of Lansing, Mich., makes four grades of graphene nanoplatelets by starting with graphite and breaking it down, using two different exfoliation processes, one mechanical and one chemical. The company specializes in formulating various materials for composites, films, and coatings by mixing in different grades of graphene nanoplatelets to obtain desired functional characteristics.
“Our larger platelets are really good for electrical conductivity, thermal conductivity and barrier properties,” said Bamidele Ali, XG's chief commercial officer, “while the high surface area graphene is typically good for mechanical properties: flexural, impact, shear strength, tensile strength, and things of that nature.”
XG Science recently signed a deal to supply Ford Motor Co., in conjunction with the auto parts supplier Eagle Industries, with graphene-based foam material to be used on 10 different components in the F-150 pickup. These include fuel rail covers, pump covers, and front engine covers. The primary functional goal of these foam materials is noise reduction.
Test results, according to Eagle Industries CEO John Bull, showed “about a 17 percent reduction in noise, a 20 percent improvement in mechanical properties, and a 30 percent improvement in heat endurance properties, compared with that of the foam used without graphene.”
Exfoliation is fast and relatively cheap, but it suffers from quality control issues. A recent paper published by researchers at RMIT in Australia revealed that under careful examination, much of the exfoliated graphene being used today is highly contaminated with silicon, which significantly hampers its performance. Fortunately, while silicon is nearly impossible to remove from the graphene, the graphite from which it is produced can be purified using well-known techniques.
Along similar lines, a paper co-authored by Novoselov and published in Advanced Materials scrutinized samples of graphene from 60 producers. The quality of those samples, they found, was “rather poor, not optimal for most applications.”
While using graphene flakes can often work well for improving mechanical properties, realizing the significant potential of graphene in electronic and optical applications will require single layer sheets. This requires a more bottom-up approach, building graphene atom by atoms rather than pulling ready-made sheets from existing graphite.
The most common way to accomplish that is via chemical vapor deposition (CVD). The process begins with a furnace filled with an inert gas; a carbon source is vaporized, and as the atoms cool, they settle as a single layer on a copper foil sheet. It’s a more energy-intensive approach than the exfoliation methods, but it produces purer single-layer graphene sheets. These pure sheets are typically used in high-value electronic and optical applications that can justify the higher cost.
In the News: NASA Reveals Shape-Shifting Wing Design
While graphene has been produced using CVD on copper since 2010, it's been difficult to cleanly remove the graphene from the copper. According to Jeffrey Draa of Grolltex, his company has solved that problem by using nickel sprayed onto the graphene. The adhesion of nickel to graphene is as much as 10 times stronger than that of graphene to copper, so the graphene can be cleanly pulled off the copper by simply grabbing onto the nickel.
One example application is its use as a conductive transparent layer for touch screen displays such as those used in cellphones. Single layer graphene coatings can directly substitute for indium tin oxide at a considerably lower cost.
The leading-edge use case though, according to Draa, is sensors: bio-sensing, strain sensing, among others. For example, Nanomedical Diagnostics makes a device that utilizes a silicon chip with a layer of graphene on which a drop of blood is placed. The chip can immediately determine the presence of Zika virus, Lyme disease, and other pathogens.
Managing Expectations
Even with the advances in manufacturing, it will take time for engineers to catch up with the potential of graphene. To help speed the transition, the United Kingdom has launched its National Graphene Institute in Manchester. Recent work there includes using graphene to strengthen natural fibers.
Another initiative, Graphene Flagship, coordinates activities between companies and universities in the European Union and provides a platform for sharing information. Flagship, which launched in 2013 under the coordination of Chalmers University of Technology based in Gothenburg, Sweden, has a research budget of €1 billion and has been a powerful force in advancing graphene technology with recent achievements ranging from high-speed opto-electronic communications to super-light, strong, and thermally stable aerospace composites.
The United States does not have that kind of coordinated effort. The National Graphene Association, which started two years ago, has taken on the role of convener, advocate, educator, and connector, looking into issues such as health and safety and standardization.
“The world is not going to be the same. It's not about what we've accomplished right now, it's about what is the possibility of accomplishing in the next few decades,” said Zina Cinker, NGA’s executive director. “That being said, we need to be very realistic about what to expect from graphene.”
When formulating graphene into composites, Bamdele Ali pointed out, “You can't just drop it in and expect for it to work. How well it's dispersed, the morphology of the graphene, the adhesion to the matrix you're putting it into, the platelet orientation—all these things determine how it's going to perform, whether you're going to just get a clump of plastics, or if you're going to get a clump of plastic that's really, really tough.”
While the course of future products may well be altered and improved by the use of graphene, the graphene revolution will not be plug and play. It's going to require skilled engineers and scientists at every step, at least until that next level of understanding is achieved.
R.P. Siegel is a technology writer based in Rochester, N.Y.
That hasn’t been Draa’s experience. According to Draa, co-founder and CEO of Grolltex in San Diego, Calif., his company has found a way to mass produce high-quality graphene, the one-atom-thick molecular form of carbon that’s been touted as the next great thing. Earlier this year Grolltex completed an expansion of its fabrication facility and can now produce the equivalent of 30,000 eight-inch wafers per year.
He could make more, much more. “I am ready to ramp up a factory today, to make miles and miles of sheet graphene,” Draa said. “However, I don’t have anybody knocking on my door saying that they want miles and miles of it.”
In spite of its wondrous laboratory-scale properties, engineers have been hesitant to incorporate graphene into their mission-critical designs. There is still a lot that is not known about this material, including how much of an environmental and health risk will it pose. A number of products and prototypes have failed to meet expectations. Then there is the question of a supply chain being developed at scale where there is none today.
But up to now, there’s also been the first-mover problem, with manufacturers, investors, and developers each waiting for the other to make a move. Why produce graphene at scale when there’s no market? And why design graphene-enabled products when there’s no supply?
But that stalemate looks to change soon. In addition to Grolltex, other manufacturers are starting to produce graphene at scale. And manufacturers are edging into limited uses for the material in applications as diverse as touch screens and auto parts.
For now, people can still ask, “If graphene is really so great, why aren’t we seeing more of it being used today?” But soon, there may be a ready reply: It’s all around us.
Impossibly Thin
Graphene is a term that’s been thrown around somewhat indiscriminately to describe a range of materials. The basis of any graphene is a single-atom-thick sheet of carbon, but the term has been extended to encompass materials derived from graphene—such as graphene oxide, which has oxygen atoms attached to the edges—or two-dimensional sheets made from other material, such as borophene, in which boron atoms take the place of carbons.
Scientists have realized that impossibly thin sheets of carbon could in theory be produced since the work of English chemist Benjamin Collins Brodie in 1859, and in the late 1940s, Canadian physicist P.R. Wallace recognized that pure, defect-free graphene would have impressive material properties. Graphene was at that point an imaginary molecule—it had never been seen in the laboratory and no one was sure that isolating a single sheet of graphene was even possible.
Recommended for You 3D Printing in Space
When scientists finally produced single sheets of pure graphene in 2004, they did it without high-tech equipment. Andre Geim and Konstantin Novoselov at the University of Manchester in England rubbed adhesive tape over a block of graphite and then peeled off layers of graphene. Their work, which earned them the Nobel Prize in Chemistry in 2010, touched off a rush to confirm the extraordinary properties of graphene and figure out how to produce the material in bulk.
Graphene’s remarkable properties derive from the hexagonal lattice structure that the atoms form, which Joseph Meany, co-author of the book Graphene: The Superstrong, Superthin, and Superversatile Material That Will Revolutionize the World, describes as “a chicken wire fence.” Each carbon atom, with its four electrons in the outer shell is bonded to three other carbon atoms. This structure allows it to lay perfectly flat, providing amazing strength, fantastic conductivity (electrical and thermal), while remaining porous and optically transparent.
To put some numbers around this, graphene has an ultimate tensile strength of 130 GPa—that’s 325 times greater than structural steel. At the same time, a single sheet of graphene weighs a mere 770 micrograms per square meter. According to Spanish manufacturer Graphenea, that means that a sheet big enough to cover an entire football field would weigh less than a gram.
Those are theoretical material limits and apply to pure graphene that is entirely free of imperfections. Real-world testing of actual manufactured samples yield results that are less magical but still impressive. For instance, sheets of graphene between 2 and 8 Nm thick were tested and found to have a Young's Modulus of 500 GPa and thermal conductivity ranging between 3,500 and 5,000 W/m2. Electron mobility has been demonstrated at 15,000 cm2·V−1·s−1 with a theoretical limit as high as 200,000. Both electrical and thermal conductivity are roughly ten times that of copper.
Once tests seemed to confirm some of graphene’s predicted properties, the material became the latest carbon construct—following on the heels of buckminsterfullerene and carbon nanotubes—to become hyped. “One of the challenges,” Meany said, “is getting designers and developers to understand that you can't necessarily say that just because they are going to slap some graphene flakes into a composite that you should expect it to magically become super-strong and super-hard.”
Where are the Wonder Products?
Some materials incorporating graphene do display a breathtaking range of useful properties. One manufacturer, Directa Plus, describes items containing their G+ graphene additive as “stronger, more absorbent, able to conduct heat and electricity, or enjoy properties such as a barrier effect, low friction and better resistance to wear.”
Consider graphene-based apparel as an example of how versatile graphene can be. Super-strong graphene polymer fibers can be made into safety gloves. Adding graphene to textiles can provide exceptional durability, heat-dissipation, bacteriostatic properties, and electrical conductivity for smart wearables as well as for energy harvesting.
Top Story: State of American Manufacturing 2019
Other protective gear, such as a motorcycle helmet already on the market, incorporate a graphene coating that allows for better distribution of impact force. An extremely light and thin bullet-proof vest can locally produce a super-hard diamond-like structure upon impact.
The combination of high electrical conductivity and strength make graphene an ideal candidate for battery electrodes and solar cells. Bicycle tires containing graphene are stiff when rolling in a straight line but become flexible when cornering. European researchers have demonstrated how graphene can enable low-power, ultra-wide bandwidth optical communications with the potential to exceed the bandwidth demands for 5G, the Internet of Things, and Industry 4.0.
In spite of all that, a quick look through the sporting goods aisles and electronics shops betrays a decided lack of graphene-based wonder products. Where are they?
One of the factors holding back graphene applications until recently has been a lack of mass production. To be sure, chemists have progressed far past the pulling-sheets-from-pencils method used by Geim and Novoselov, but it is still very much a work in progress and the subject of considerable research.
There are dozens of ways to make graphene, but the most common approaches fall into two primary camps. The first, which can trace its roots back to Manchester, is called “exfoliated” or solution graphene. This approach now employs more sophisticated methods for removing the super-thin layers from graphite using some combination of mechanical and chemical action. The result is graphene flakes, or “nano-platelets” as they are sometimes called, consisting of between three and 20 layers.
XG Science of Lansing, Mich., makes four grades of graphene nanoplatelets by starting with graphite and breaking it down, using two different exfoliation processes, one mechanical and one chemical. The company specializes in formulating various materials for composites, films, and coatings by mixing in different grades of graphene nanoplatelets to obtain desired functional characteristics.
“Our larger platelets are really good for electrical conductivity, thermal conductivity and barrier properties,” said Bamidele Ali, XG's chief commercial officer, “while the high surface area graphene is typically good for mechanical properties: flexural, impact, shear strength, tensile strength, and things of that nature.”
XG Science recently signed a deal to supply Ford Motor Co., in conjunction with the auto parts supplier Eagle Industries, with graphene-based foam material to be used on 10 different components in the F-150 pickup. These include fuel rail covers, pump covers, and front engine covers. The primary functional goal of these foam materials is noise reduction.
Test results, according to Eagle Industries CEO John Bull, showed “about a 17 percent reduction in noise, a 20 percent improvement in mechanical properties, and a 30 percent improvement in heat endurance properties, compared with that of the foam used without graphene.”
Exfoliation is fast and relatively cheap, but it suffers from quality control issues. A recent paper published by researchers at RMIT in Australia revealed that under careful examination, much of the exfoliated graphene being used today is highly contaminated with silicon, which significantly hampers its performance. Fortunately, while silicon is nearly impossible to remove from the graphene, the graphite from which it is produced can be purified using well-known techniques.
Along similar lines, a paper co-authored by Novoselov and published in Advanced Materials scrutinized samples of graphene from 60 producers. The quality of those samples, they found, was “rather poor, not optimal for most applications.”
While using graphene flakes can often work well for improving mechanical properties, realizing the significant potential of graphene in electronic and optical applications will require single layer sheets. This requires a more bottom-up approach, building graphene atom by atoms rather than pulling ready-made sheets from existing graphite.
The most common way to accomplish that is via chemical vapor deposition (CVD). The process begins with a furnace filled with an inert gas; a carbon source is vaporized, and as the atoms cool, they settle as a single layer on a copper foil sheet. It’s a more energy-intensive approach than the exfoliation methods, but it produces purer single-layer graphene sheets. These pure sheets are typically used in high-value electronic and optical applications that can justify the higher cost.
In the News: NASA Reveals Shape-Shifting Wing Design
While graphene has been produced using CVD on copper since 2010, it's been difficult to cleanly remove the graphene from the copper. According to Jeffrey Draa of Grolltex, his company has solved that problem by using nickel sprayed onto the graphene. The adhesion of nickel to graphene is as much as 10 times stronger than that of graphene to copper, so the graphene can be cleanly pulled off the copper by simply grabbing onto the nickel.
One example application is its use as a conductive transparent layer for touch screen displays such as those used in cellphones. Single layer graphene coatings can directly substitute for indium tin oxide at a considerably lower cost.
The leading-edge use case though, according to Draa, is sensors: bio-sensing, strain sensing, among others. For example, Nanomedical Diagnostics makes a device that utilizes a silicon chip with a layer of graphene on which a drop of blood is placed. The chip can immediately determine the presence of Zika virus, Lyme disease, and other pathogens.
Managing Expectations
Even with the advances in manufacturing, it will take time for engineers to catch up with the potential of graphene. To help speed the transition, the United Kingdom has launched its National Graphene Institute in Manchester. Recent work there includes using graphene to strengthen natural fibers.
Another initiative, Graphene Flagship, coordinates activities between companies and universities in the European Union and provides a platform for sharing information. Flagship, which launched in 2013 under the coordination of Chalmers University of Technology based in Gothenburg, Sweden, has a research budget of €1 billion and has been a powerful force in advancing graphene technology with recent achievements ranging from high-speed opto-electronic communications to super-light, strong, and thermally stable aerospace composites.
The United States does not have that kind of coordinated effort. The National Graphene Association, which started two years ago, has taken on the role of convener, advocate, educator, and connector, looking into issues such as health and safety and standardization.
“The world is not going to be the same. It's not about what we've accomplished right now, it's about what is the possibility of accomplishing in the next few decades,” said Zina Cinker, NGA’s executive director. “That being said, we need to be very realistic about what to expect from graphene.”
When formulating graphene into composites, Bamdele Ali pointed out, “You can't just drop it in and expect for it to work. How well it's dispersed, the morphology of the graphene, the adhesion to the matrix you're putting it into, the platelet orientation—all these things determine how it's going to perform, whether you're going to just get a clump of plastics, or if you're going to get a clump of plastic that's really, really tough.”
While the course of future products may well be altered and improved by the use of graphene, the graphene revolution will not be plug and play. It's going to require skilled engineers and scientists at every step, at least until that next level of understanding is achieved.
R.P. Siegel is a technology writer based in Rochester, N.Y.