Engineering Musical Drums
Engineering Musical Drums
By Soren Maloney
What are musical steel drums?
The steel drum is the only acoustic instrument developed in the last century. In the United States the instrument is known as the steel drum whereas throughout most of the Caribbean, the instrument is commonly referred to as the steelpan or pan. The steelpan has its roots in the drumming traditions of the two largest ethnic groups in Trinidad and Tobago – Afro and Indo Trinidadians, and was invented around the Second World War. Prior to the invention of the steelpan, islander's fashioned musical instruments from biscuit pans, paint tins, grease barrels, wooden buckets and bamboo poles. The expanding oil industry and the American Naval bases in Trinidad during World War II provided an abundance of oil drums which gave.
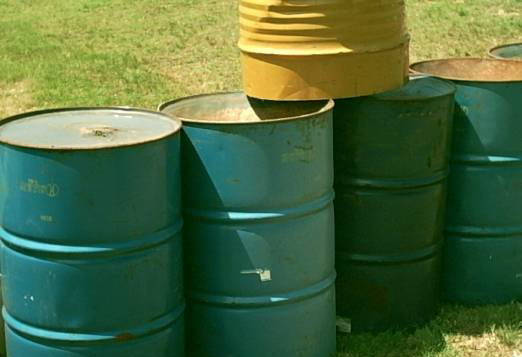
Figure 1: Used 55 gallon oil drums
Every steelpan consists of two regions: the playing surface on which the note regions are located and the side commonly referred to as the skirt (see figure 2). In music, note refers to the sign used in musical notation or to the pitch of a sound. The word 'note' with respect to the steelpan is also used when referring to the physical space or the region allocated to a musical note on the pan's surface as seen in figure 2. Over the decades, steelpans have evolved into a range of instruments with different pan types. The present playing range of the family of steelpans extends approximately five octaves
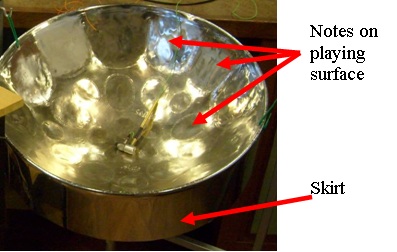
The first step in the traditional pan making process makes use of a sledgehammer or a heavy metal ball to achieve a dished surface that forms the playing surface on which the note regions are created. After dishing, the note regions are formed on the playing surface and the side of the drum is cut to length depending on the pan type in production. In the case of bass pans the entire drum side is retained. Note regions are typically arranged so that adjacent notes share a consonant musical relationship such that when played simultaneously sounds pleasing to the human ear. Before tuning note regions, the playing surface is heated to provide a form of stress relief from the dishing and note-creating operations. This heating is believed to provide some surface hardening through the effect of strain ageing of the steel. Pan tuning, the final stage, is considered to be one of the most sophisticated steps of the entire steelpan production process. During tuning the pan maker hand-tunes two or three modes in each note region to frequencies on the Western twelve tone equal temperament scale. These mode frequencies are tuned to have a consonant musical relationship. Steelpan tuning remains a skill that takes many years to master and there are only a handful of master pan tuners. The steelpan is chrome plated or painted to provide corrosion protection and a final fine tuning is done to compensate for the detuning caused by the coating process.
Mechanized dish forming processes
Several problems associated with sinking by hand have lead pan makers to search for mechanized alternatives to dish forming. Some of these problems range from high noise intensity levels, material wastage due to splitting of the drum during the sinking process, and problems experienced by pan builders which include noise induced hearing loss and exposure to hand-arm vibrations. Some of the mechanized processes applied to dishing by pan makers include, pneumatic hammering, conventional spinning and hydroforming.
Pneumatic hammering has become popular among pan makers owing to its relatively low cost and high speed. It is also less energy demanding when compared with traditional hand sinking but requires just as much skill on the part of the pan maker to avoid splitting the drum surface. However, this technique also exposes the pan builders to high noise levels ~ 100dB and problems connected with hand arm vibrations.
Conventional lathe spinning has also been successfully used and involves the progressive shaping of a rotating metal blank over a rotating mandrel in the shape of the dish to be formed as illustrated in figure 3.
Spinning unlike traditional handcrafting and pneumatic hammering makes it possible to produce pan dishes with a relatively good degree of consistency since the same mandrel is used repeatedly. The finished dish is subsequently attached to a cylindrical side. Manual spinning can also be physically challenging and requires dexterity as control of the process is highly dependent on the competence of the operator. However, spinning of pans can take advantage of programmable numerical control (PNC) which uses playback technology. Here, the pan dish is spun manually by an experienced operator while his motion is recorded and played back to form subsequent dishes. This capitalizes on both operator skill and the repeatability given by the computer.
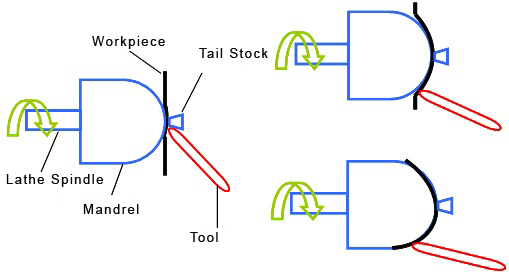
Figure 3: Spin forming of a pan dish
Hydroforming is another sheet metal forming process that has been applied to pan dishing. The time savings achieved by this process is phenomenal but the relatively high capital outlay requires the production of a large volume of pans in order to recoup capital and tooling costs. Hydroforming does not expose pan makers to high noise and vibration levels and delivers pans with superior geometrical accuracy, tolerance and repeatability but has poor flexibility as dedicated tools will be required for each pan type.
Metal alloy alternatives to low-carbon steel
Other pan makers have experimented with metal alloys such as alpha-brass (70%Cu/30%Zn), 304 stainless steel and aluminum 6061 (T0 and T6 heat treatable grades). These metal alloys were suitable because of their high formability and exceptional corrosion resistant properties. The use of aluminum provides the opportunity for light-weight pans which can be hard coated and colored through the anodizing process. However, very few pan makers produce pans from these materials in-spite of their attractive properties. The principal drawback is the relatively high cost of these materials while another drawback is related to the careful control and sophisticated equipment required to provide heat treatment to these alloys. For instance, pans made from stainless steels may require intermittent solution treatment annealing during the dishing stage due to the rapid work hardening of stainless steel. Solution treatment involves heating the steel to between 1010°C and 1120°C before cooling rapidly. If the stainless steel is not cooled rapidly, particularly between 500°C and 850°C, there is a risk of sensitization in which chromium carbides precipitates from the steel thereby undermining its corrosion protection capability.
Vibration behavior
The steelpan like most percussion instruments is a pitched percussion instrument in which there are two distinctive features. Firstly, the first mode in each steelpan note is tuned to have a dominant fundamental tone and secondly, some of the natural frequencies of the higher modes are tuned into a harmonic relationship with the fundamental. Numerous modal testing studies have been performed on steelpans, and the unique vibration behavior of steelpan notes in which vibrations are predominantly localized within the boundaries of excited notes is well documented (see figure 4).
However, unlike several other percussion instruments such as the timpani, marimba, xylophone and Indian drums, there is no analytical or numerical model that adequately describes the vibration behavior of steelpan note regions. Even with advances in computational capabilities, the modeling of steelpan notes remains a formidable challenge. The challenge may be in part due to the difficulty of modeling the residual stresses brought on by the heating and forming cycles experienced by the pan surface.
The steelpan is a new instrument that is continuing to evolve, with opportunities for further innovation in the application of metal forming techniques, materials selection and modeling of vibration behavior. Hand and pneumatic sinking although very cheap exposes pan makers to high noise and vibration levels, which is a direct threat to their health and longevity as craftsmen.
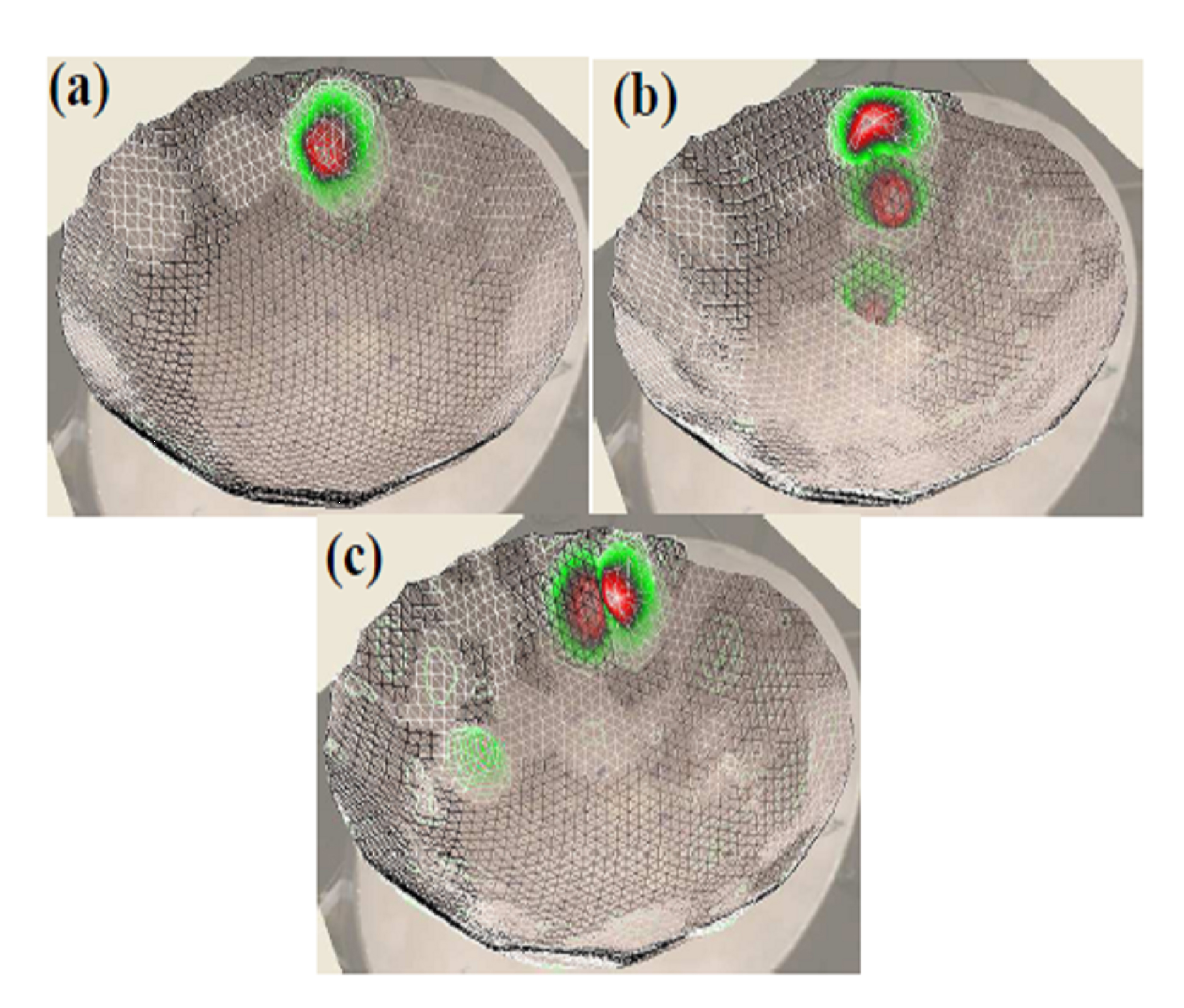
Figure 4: Vibration mode shapes of first three natural frequencies of a steelpan note (a) first mode, (b) second mode and (c) third mode
Hydroforming while relatively quiet, skill independent and fast, is inflexible, require significant capital outlay, and large volumes of dishes would be required to break even on investment. The spinning technology is also very attractive provided that it can be fully automated. Although the poor corrosion properties and heavy weight of low-carbon steel are significant disadvantages to its usage in pan production, its low cost, abundant availability, ease of forming and recyclability will continue to see low-carbon steel as the de-facto material for pan making. Although alpha-brass, stainless steel and aluminum offer attractive benefits, pan makers may long remain hesitant to change as current production and tuning techniques have evolved around more than seven decades of using low-carbon steel.
References
- Maloney, S.E., Acoustics and Manufacture of Caribbean Steelpans. Ph.D. Thesis, University of Cambridge, 2011
- Blake, F.I.R., The Trinidad and Tobago Steel Pan: History and Evolution. 1st ed. 1995, Port of Spain: Speeds Printery.
- Kronman, U., Steelpan Tuning: A handbook for steelpan making and tuning. 1991, Stockholm, Sweden: Musikmuseet.
- Murr, L.E., S.M. Gaytan, M.I. Lopez, D.E. Bujanda, E.Y. Martinez, G. Whitmyre, and H.Price, Metallurgical and acoustical characterization of a hydroformed, 304 stainless steel, Caribbean-style musical pan. Materials Characterization, 2008. 59(3): p. 321 -328.
- Barlow, C.Y., B.E. Richardson, J. Woodhouse, and J. Zarek, The Caribbean Steel Drum. Proceedings of the Institute of Acoustics, 1988: p. 193-198.