Tiny 3D Printed Lens to Transform Optics
Tiny 3D Printed Lens to Transform Optics
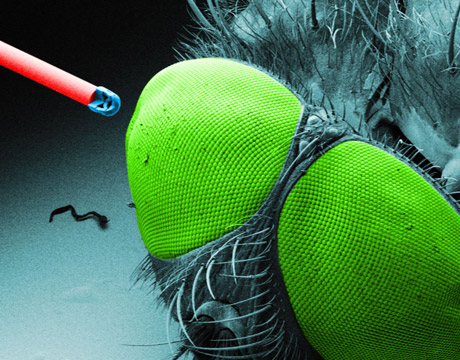
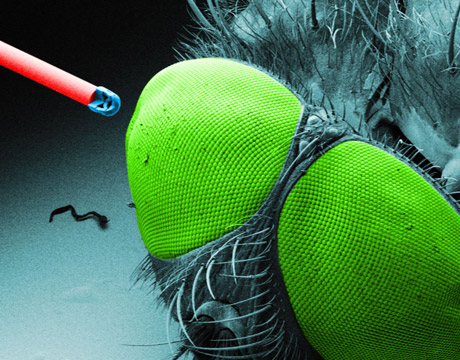
The complex 3D printed lens on an optical fiber next to a fly. Image: Stuttgart University
Researchers at Stuttgart University in Germany have 3D printed a tiny, high-performance optical lens about the size of a grain of salt. At 100 microns across, the lens fits inside a syringe needle and can be printed on the tip of an optical fiber. The technology holds great promise for transforming microscale and nanoscale optical applications in medicine, aerospace, surveillance, and other fields.
“Current lens systems are restricted in size, shape, and dimensions by limitations of manufacturing,” states Tim Gissibl, a researcher at Stuttgart University and lead author of a recent paper in Nature Photonics that describes this work. “Multi-lens elements with non-spherical shapes are required for high optical performance and to correct for aberrations when imaging at wide angles and large fields. Our system overcomes all the aforementioned difficulties and opens a new field of 3D printed micro-optics and nano-optics with complex lens designs.”
How the Process Works
Gissibl and his colleagues used a 3D printing technique called two-photon direct laser writing. A femtosecond laser, with a pulse duration of less than 100 femtoseconds, was focused by means of a microscope into a liquid photoresist which has previously been applied, for example, to a glass plate or to a glass fiber.Two photons of the red laser beam with a wavelength of 785 nm were simultaneously absorbed at the focal point and exposed.This caused the polymers to crosslink and solidify to build up a transparent element on the surface.
The laser beam was directed with the aid of a scanner or through a process of the substrate in all three spatial directions to create the desired shape.In this way, optical freeform surfaces can be produced with sub-micrometer accuracy.Only the material in the small 3D area where the laser light was focused hardens. When the 3D structure is completed, any unhardened material is then washed away, revealing the optical element that was just been created.
Optical elements as small as 4.4 microns were printed onto the exact center of an optical fiber only 125 microns in diameter, just slightly thicker than the diameter of a human hair. This high precision makes it possible to produce not only spherical lenses, but also multi-lens lenses for high-quality images. The multi-lens systems feature multiple singlet (simple) lenses that are combined into a compound lens within a supporting shell. The systems can be printed at a rate of centimeters per second.
Future Applications
A major advancement for optics, this new system allows for accurate manufacturing of lenses at sizes about one order of magnitude smaller than before. This breakthrough will likely transform the design of optical equipment in the fields of medicine, aerospace, and surveillance. For example, high-quality imaging elements could be printed directly on semiconductor chips to create tiny sensors for self-propelled cars, autonomous robots, or industrial machines 4.0.Even the smallest body sensors and all-round cameras for mobile phones are possible.
“The unprecedented flexibility of our method paves the way towards printed optical miniature instruments such as endoscopes, fiber-imaging systems for cell biology, new illumination systems, miniature optical fiber traps, integrated quantum emitters and detectors, and miniature drones and robots with autonomous vision,” says Gissibl.
He is hopeful his team’s breakthrough will fundamentally change how optics are manufactured. "The time from the idea, the optics design, and a CAD model, to the finished, 3D printed micro-objectives, will take less than a day,” says Gissibl. “We are going to open potentials just like computer-aided design and computer-integrated manufacturing did in mechanical engineering a few years ago.”
Mark Crawford is an independent writer.
Our system opens a new field of 3D printed micro-optics and nano-optics with complex lens designs.Tim Gissibl, researcher, Stuttgart University