Bioengineering Blog: Tools to Accelerate the Development of Energy-Based Medical Devices
Bioengineering Blog: Tools to Accelerate the Development of Energy-Based Medical Devices
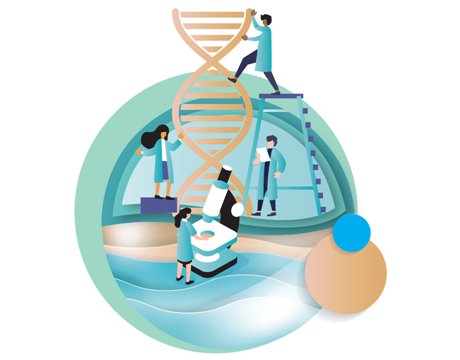
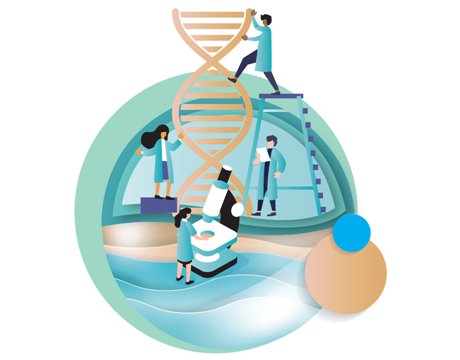
Computational modeling and simulation tools shorten early stage R&D for a medical device platform.
A common challenge when developing a new energy-based medical device platform is the complex design dependencies that change treatment outcomes in unintended ways. The platform itself is a system of interrelated parts each with its own design team working toward compartmentalized goals.
The energy delivery team is tasked with designing a system that delivers the right amount of energy at the right time and incorporates the required sensing and control systems to do it consistently and safely. The hand piece team must deliver the energy to the tissue while positioning the sensors to provide the desired information back to the hardware.
Reminiscent of the chicken and the egg, developing an entire platform often runs into a problem. The hardware side wants to know what the energy and sensing requirements are, but the disposable side wants hardware that can deliver energy before evaluating the prototype that was designed to provide the energy requirements.
The traditional medical device system prototype or test model requires system research tools to be built before evaluating a device prototype.
That is why platform level medical device design has an early stage where "research tools" are developed on the hardware side. To add to the complexity of the problem, the requirements range can be vast, making it difficult to build this first-generation research tool. Delays in the development of the research tool to provide energy as desired with the level of control needed for the device itself are an early project challenge that has long-term effects on the product's actual launch into the marketplace.
Related Bioengineering Blog Post: AI to Predict Kidney Failure in Advance
Once the research tool is decided upon and prototypes are being evaluated, there is always a question whether the testing results are skewed because of the disposable design or the hardware research tool isn't delivering energy in the desired manner. So, all the testing must include measuring the research tool outputs as well as the resulting effect on the tissue, requiring troubleshooting of the entire system at every stage.
Delays in the research tools often extend timelines for prototype evaluation, which can delay the project by months.
Using computational modeling and simulation (CM&S) early in the platform development process can alleviate this problem. Drawing on knowledge of the desired end tissue effect and the physical mechanisms that create it, CM&S can be used to quickly narrow the energy delivery requirements for a hardware research tool. Virtual prototyping can also iterate disposable designs though the evaluation of the end result, allowing faster and cheaper design changes while still meeting the project's timeline.
Related Bioengineering Blog Post: Advanced Design and Manufacturing Tools Empower Personalized Medicine
Using CM&S, early stage research and development for a medical device platform can benefit by:
Use tissue effect simulation to tighten the requirements and make progress on the device while simplifying the research tool, reducing lengthy and costly requirements for both. This translates to faster time to market, an earlier platform launch, and more revenue from the completed system.
Arlen Ward, Ph.D., P.E., is a modeling and simulation principal for System Insight Engineering, a consultancy providing computational modeling and simulation services for medical device companies with a focus on the interaction between energy and tissue.
Opinions expressed are the author’s and do not necessarily reflect the views of ASME.
The energy delivery team is tasked with designing a system that delivers the right amount of energy at the right time and incorporates the required sensing and control systems to do it consistently and safely. The hand piece team must deliver the energy to the tissue while positioning the sensors to provide the desired information back to the hardware.
Reminiscent of the chicken and the egg, developing an entire platform often runs into a problem. The hardware side wants to know what the energy and sensing requirements are, but the disposable side wants hardware that can deliver energy before evaluating the prototype that was designed to provide the energy requirements.
Problem
The traditional medical device system prototype or test model requires system research tools to be built before evaluating a device prototype.
That is why platform level medical device design has an early stage where "research tools" are developed on the hardware side. To add to the complexity of the problem, the requirements range can be vast, making it difficult to build this first-generation research tool. Delays in the development of the research tool to provide energy as desired with the level of control needed for the device itself are an early project challenge that has long-term effects on the product's actual launch into the marketplace.
Related Bioengineering Blog Post: AI to Predict Kidney Failure in Advance
Once the research tool is decided upon and prototypes are being evaluated, there is always a question whether the testing results are skewed because of the disposable design or the hardware research tool isn't delivering energy in the desired manner. So, all the testing must include measuring the research tool outputs as well as the resulting effect on the tissue, requiring troubleshooting of the entire system at every stage.
Result
Delays in the research tools often extend timelines for prototype evaluation, which can delay the project by months.
Using computational modeling and simulation (CM&S) early in the platform development process can alleviate this problem. Drawing on knowledge of the desired end tissue effect and the physical mechanisms that create it, CM&S can be used to quickly narrow the energy delivery requirements for a hardware research tool. Virtual prototyping can also iterate disposable designs though the evaluation of the end result, allowing faster and cheaper design changes while still meeting the project's timeline.
Related Bioengineering Blog Post: Advanced Design and Manufacturing Tools Empower Personalized Medicine
Using CM&S, early stage research and development for a medical device platform can benefit by:
- reducing the requirements range for the research tool, resulting in easier design and less expensive components.
- facilitating the disposable design iterations through virtual prototyping, allowing for intelligent design decisions before the research tool is available.
- significantly fewer physical prototype iterations mean a shorter time to market, positively impacting the ROI for the project.
Solution
Use tissue effect simulation to tighten the requirements and make progress on the device while simplifying the research tool, reducing lengthy and costly requirements for both. This translates to faster time to market, an earlier platform launch, and more revenue from the completed system.
Arlen Ward, Ph.D., P.E., is a modeling and simulation principal for System Insight Engineering, a consultancy providing computational modeling and simulation services for medical device companies with a focus on the interaction between energy and tissue.
Opinions expressed are the author’s and do not necessarily reflect the views of ASME.
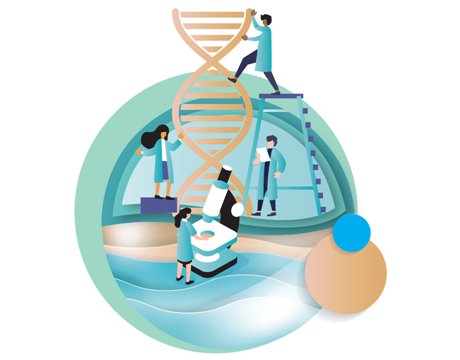
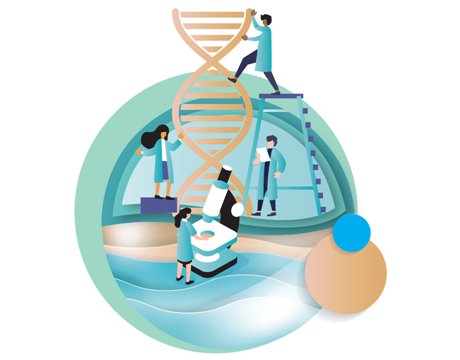