Can Engineers Build Floating Cities to Save Island Nations?
Can Engineers Build Floating Cities to Save Island Nations?
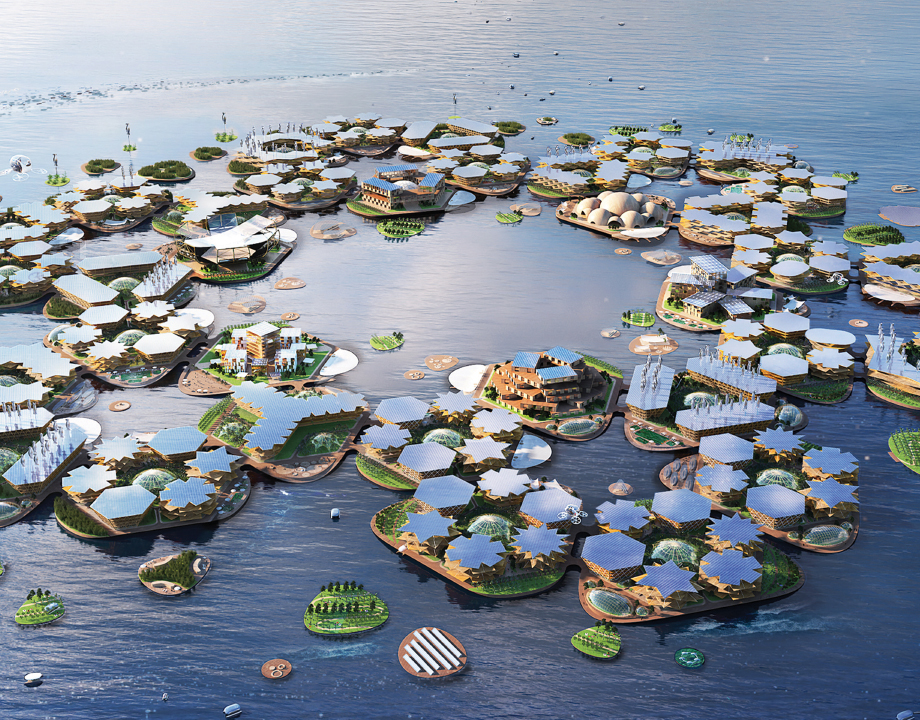
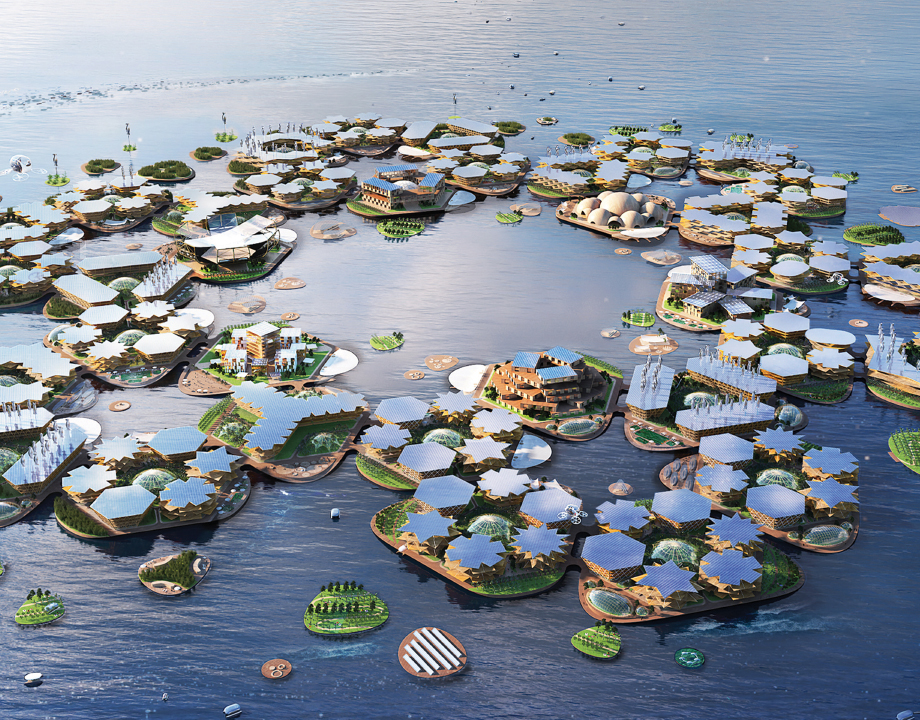
An artist's interpretation of a floating settlement. Image: Oceanix
By some accounts, French Polynesia is heaven on Earth. It’s a collection of 118 tropical islands and atolls spread across a wide expanse of the Pacific. (Perhaps you’ve heard of Tahiti.) And yet, thanks to erosion, land subsidence, and sea level rise, parts of this paradise are threatened with sinking beneath the waves.
“When we looked at it, the options were pretty bad,” said Marc Collins Chen, who in the 2000s was the minister of tourism. “One was to retreat. The other was to build large engineering public works, like dikes and seawalls.”
That’s the choice a lot of low-lying places are facing in the coming century. For some, like Miami or Bangladesh, retreat is at least possible. Island nations, Chen realized, had nowhere to turn and needed another option. Chen had one: “To have entire floating cities.”
Chen took that vision and founded a company called Oceanix to work out the logistics of permanent life at sea. In Oceanix’s vision, floating communities would produce their own electricity, produce their own food, and produce zero waste.
“In Asia three million people a week are migrating to cities,” Chen said. “Most of those cities are coastal and they are growing faster than they can grow infrastructure.”
Cities on the water may sound pie in the sky, to say nothing of expensive. But where the price of real estate is high enough—or the alternatives are national exodus—adventurous new ideas look comparatively less extravagant. And the concept is starting to get serious attention. In April 2019, the United Nations held a “High Level Round Table” on sustainable floating cities. There, Oceanix introduced architectural illustrations of a bright and shiny world of green soft-edged isles arranged in hexagons, hosting dazzling structures topped with glittering solar panels, lush gardens, a diverse and healthy population, all spread over 185 acres in the middle of the ocean.
For decades, engineers have looked at the idea of relocating giant pieces of infrastructure to buoyant buildings, or very large floating structures. Up to now, their proposals have largely been curiosities or technology demonstrations, pushing the limits of what was possible. Now, with waterside cities from New York to Lagos and Jakarta pressed to find more living space while the oceans are eating away at what’s already there, the idea of floating cities on the seas has begun to take on an edge of desperate necessity.
Herodotus in his Histories told of the Persian invasion of Greece in 480 BC. To speed his army across the narrowest part of the Hellespont, Xerxes the Great ordered the construction of a bridge created by laying timbers across 360 boats.
That might be the earliest recorded very large floating structure, but it has not been the last. It isn’t even the last pontoon bridge: The Washington State Department of Transportation opened the 7,710-foot Evergreen Point Floating Bridge in 2016, making it the longest floating bridge in the world and nearly twice as long as Xerxes’s bridge.
Editor's Pick Floating Turbines Harness Offshore Winds
At the turn of this millennium, Japan built a 1,000-meter model airport in Tokyo Bay. Planes successfully landed on it and the airfield was deemed safe, but it was a temporary structure and, according to plan, eventually disassembled. Short on land but surrounded by water, Japan also has two massive floating oil storage “yards,” each covering more than 130,000 square feet and holding together 11 million kiloliters of oil.
Floating cities would be many times larger and several orders of magnitude more complex. Olaf Waals, a naval architect and engineer for MARIN, the Maritime Research Institute of the Netherlands, has produced what is arguably the first piece of solid technology that would make up the ground level of an ocean floating municipality of whatever size.
Waals is quick to point out that the floating communities are not new—houseboats are common on Amsterdam’s placid canals. But Waals wants his communities to stay afloat in waters as violent as those of the North Sea. “What would be required to achieve that goal?” he asked himself not too long ago.
One challenge Waals had to meet was squaring the conflict between size and stress. Making the structure very large was essential to weathering storms, but the stresses on an enormous, solid rigid structure would be unmanageable.
“And if it becomes really large—like two miles across—how do you fabricate that?” Waals asked. “The largest shipping docks in the world are 400 meters long, so you can’t build such a thing with current-day technologies.”
Waals's solution is to create modular, three-sided islands that can work for any size and, eventually, in any kind of weather. Linked together, triangles more easily handle waves, be they rogue or regular, than the squares and rectangles favored by conventional engineers.
“If you make a surface of triangles, it is easier to flex with waves from any direction,” Waals said. The center of this island is made of larger triangles, as the island will do less flexing there. The central rigidity will help it rise and fall with greater stability.
Why not make the whole thing rigid? “Imagine you make a completely rigid island—in theory, yeah, you could make an island that is completely stable,” Waals said. “But there is a price to pay: if you make it really rigid, then the loads inside the island will still be there and you will need to accommodate them.”
You May Also Like: Developing and Verifying Deepwater Offshore Wind Turbines
Whatever the shape, such a platform would have to survive the roughest waters that the weather might toss up in 200-odd years. To test his grid of triangles, Waals pummeled them with the equivalent of 82-foot waves in MARIN’s test pool, one of the largest indoor pools in the world. The platform rode the waves like a magic carpet. The crests did not crash over the island and the front wave-facing end did all the flexing.
“You don’t want to put your houses there,” Waals said.
Without the flexibility, a hinge-free island would need more freeboard—that is, the distance from the water to the deck—which would require much more material. Waals is now at work creating a model that more acutely proves the viability of the concept. “Instead of just a yellow island with a flat surface, this will really be a floating city with buildings that test the design,” he said.
Not every engineer studying very large floating structures is convinced that flexibility is necessary. While Jan van Kessel, senior engineer in floating city development for the Dutch architectural firm Blue21, agrees that the basic elements of a floating city must be modular, he favors rigidity. “A floating city is fairly large, so by definition it has a high stability,” he said. “So it does not react to the waves very much.” Van Kessel has designed a platform that floats on a cushion of air, something like an overturned canoe.
For a floating city to be large, rigid, and modular, the connectors between modules become the weak link. “Technically, this is the biggest challenge,” van Kessel said. “How do you connect the modules so that they survive high waves? We haven’t solved that yet.”
The offshore oil industry has plenty of experience building floating structures. Though putting a city on some kind of massive oil rig would be prohibitively expensive, borrowing ideas from the industry could prove the fastest way to living on the ocean. For instance, instead of sitting right on the water, why not increase the freeboard and rest the platform on multiple spars. “Like a coke can floating upright, with a fair amount of ballast in the bottom, so it’s inherently stable,” said John Halkyard, an ocean engineer who has designed many offshore platforms and author of Design and Analysis of Floating Structures. “Consider that as a building block, have a number of these spars spaced apart, then have beams on them with hinges—the spar is going to roll.”
Semi-submersible rigs already rest on submerged pontoons. Those pontoons do more than keep the structure afloat. “The wave forces on the pontoons are designed to be equal and opposite on columns, so for the worst storm you get wave force cancelling effects,” Halkyard said. “That’s standard practice for pontoon design.” Similarly, to mitigate wave forces and decrease drag, floating cities could use some modified form of the bulbous bow found on tankers under the water line.
“You could put a skirt on it so you get cancellation forces,” Halkyard said. “When a crest is going over, the fluid is accelerating downward—the downward force cancels the upward force on the main spar columns. That would take care of your heaves up and down.”
Whether it’s spars, pontoons, or hinged triangles that keep a floating city afloat, the material it’s made from will be expected to survive for generations. “For oil and gas platforms we usually speak of a life of 20 or 40 years,” said Torgeir Moan, an engineer and professor of marine technology at the Norwegian University of Science and Technology as well as co-author of Stochastic Dynamics of Marine Structures. “Normally, when we talk about infrastructure, we would like to plan for 1,000 years. But it’s not possible to guarantee a maintenance-free system for 100 years.”
Any structure made of steel will have to be painted—and repainted. Ships get hauled out of the water for their touch ups. Not a likely scenario for a city. There are other materials that might better protect steel, but their longevity is not known, and they are prohibitively expensive. Another option is cathodic protection—turning the metal into the cathode of an electrochemical cell. But this option only works for fully submerged structures.
Concrete may be the best alternative, but, the difficulties of using it may outweigh the benefits. Sea-worthy concrete will have to be crack-proof or the metal it’s reinforced with is likely to corrode, a problem that plagued the concrete ships of a century ago. “Concrete floating structures have been built in that past but not to that scale and not that many,” Waals said. “The effects of long-term salt water not known on concrete.”
Very large floating structures have already been built from concrete; the Evergreen Point Floating Bridge, for instance, rests on 77 concrete pontoons. But it will take decades before its long-term performance can be assessed.
Any floating city far from shore will need to produce its own electricity. Wind power is the obvious choice, and the offshore wind industry is already exploring floating structures as it moves into deeper water.
“Once you get to more than 65 or 70 meters of water depth, the economics of fixing structures to the sea bed are such that it’s far more desirable to float,” said Feargal Brennan, a professor of naval architecture and offshore engineering at the University of Strathclyde Offshore Engineering Institute.
While single wind turbines have been tested on spars and triangular semi-submersibles platforms, there’s no real reason to stop at one. “Once we’ve bitten the bullet, then the bigger you get, the better,” Brennan said. “If you consider the cost threshold, by the time you’ve built a large floating foundation, you’ve got to put the largest thing on it possible.”
Brennan and his colleagues are looking at the design of very large floating structures capable of supporting several 150-MW turbines. The first step is building the software tools that would allow designers to create floating islands. The structures would be so large that as they deform under loading, the loading itself changes. “We can’t just use conventional FEA to deal with this,” he said.
Though he’s still at work creating those tools, Brennan has ideas about how best to minimize the effects of waves. One is to change a platform’s hydrodynamic response characteristics by taking on—and jettisoning—ballast water to and from a hull or tank. Crane vessels already use such a system, pumping water at great speed from tank to tank to suppress motion. And hinges, not unlike those conceived by Waals, could aid in that suppression by changing their stiffness to accommodate different wave sizes. They could also add to the energy production of the whole island with every wave induced flex.
A structure large enough to support a small wind farm could do much more. For instance, the electricity from the turbines could power a hydrolysis plant to make hydrogen fuel; that would allow wind farms to be established far beyond the reach of submarine electricity cables. Or the space under the decks could be used for aquaculture.
“For fish stock it’s better to be away from coastal areas,” Brennan said. “You don’t get the pollution from fish farms and the health of the fish is far, far better.”
When engineering experts saw Oceanix’s initial plans for floating cities, they acknowledged that the scope was ambitious. But according to some who looked at the proposal, the engineering was naïve. For instance, Nicholas Makris, a professor of mechanical and ocean engineering at MIT, attended the meeting; when he asked if anyone had ever been on the ocean during a hurricane, no one raised a hand.
“They had thought of a lot of interesting things from the perspective of reinventing the whole urban landscape,” Makris said. “But the thing they really didn’t have down was the naval architecture and the marine engineering side of things. We thought we could help them with that.”
The structures, and the base they were meant to sit on were, simply put, not seaworthy. Rather than go the route of off-shore oil platforms, which survive over deep waters but cost billions, Makris suggested giving up on the idea of living in the middle of the ocean, at least for now.
“If you immediately try to go into high sea states, you are completely going to lose your urban audience. You can move out slowly, and have their life style not change much,” he said. The first baby steps should be taken in naturally protected harbors—the kind that have given rise to major coastal cities from Venice to Manhattan. Where the waves are kept to a minimum by geography, floating communities will need less freeboard.
Makris is now trying to move toward a first prototype. “We’re talking a half a kilometer, just one structure, with some kind of functional establishment on it—we don’t know if it’s going to be a school or a home for the elderly—where there would be some kind of community,” he said. But he’s a long way from putting anything in the water.
“We don’t have the magic wand here, we’re relying on bringing people together.”
Creating a waterborne habitat for our species may not require revolutionary new technology, but uniting proven technologies and testing the heck out of them. “These technologies are out there,” said Oceanix’s Chen. “We just need to put them together. It’s like what William Gibson said about the future: ‘The future is already here—it’s just not very evenly distributed.’ ”
Michael Abrams is a technology writer based in Westfield, N.J.
“When we looked at it, the options were pretty bad,” said Marc Collins Chen, who in the 2000s was the minister of tourism. “One was to retreat. The other was to build large engineering public works, like dikes and seawalls.”
That’s the choice a lot of low-lying places are facing in the coming century. For some, like Miami or Bangladesh, retreat is at least possible. Island nations, Chen realized, had nowhere to turn and needed another option. Chen had one: “To have entire floating cities.”
Chen took that vision and founded a company called Oceanix to work out the logistics of permanent life at sea. In Oceanix’s vision, floating communities would produce their own electricity, produce their own food, and produce zero waste.
“In Asia three million people a week are migrating to cities,” Chen said. “Most of those cities are coastal and they are growing faster than they can grow infrastructure.”
Cities on the water may sound pie in the sky, to say nothing of expensive. But where the price of real estate is high enough—or the alternatives are national exodus—adventurous new ideas look comparatively less extravagant. And the concept is starting to get serious attention. In April 2019, the United Nations held a “High Level Round Table” on sustainable floating cities. There, Oceanix introduced architectural illustrations of a bright and shiny world of green soft-edged isles arranged in hexagons, hosting dazzling structures topped with glittering solar panels, lush gardens, a diverse and healthy population, all spread over 185 acres in the middle of the ocean.
For decades, engineers have looked at the idea of relocating giant pieces of infrastructure to buoyant buildings, or very large floating structures. Up to now, their proposals have largely been curiosities or technology demonstrations, pushing the limits of what was possible. Now, with waterside cities from New York to Lagos and Jakarta pressed to find more living space while the oceans are eating away at what’s already there, the idea of floating cities on the seas has begun to take on an edge of desperate necessity.
Infrastructure Afloat
Herodotus in his Histories told of the Persian invasion of Greece in 480 BC. To speed his army across the narrowest part of the Hellespont, Xerxes the Great ordered the construction of a bridge created by laying timbers across 360 boats.
That might be the earliest recorded very large floating structure, but it has not been the last. It isn’t even the last pontoon bridge: The Washington State Department of Transportation opened the 7,710-foot Evergreen Point Floating Bridge in 2016, making it the longest floating bridge in the world and nearly twice as long as Xerxes’s bridge.
Editor's Pick Floating Turbines Harness Offshore Winds
At the turn of this millennium, Japan built a 1,000-meter model airport in Tokyo Bay. Planes successfully landed on it and the airfield was deemed safe, but it was a temporary structure and, according to plan, eventually disassembled. Short on land but surrounded by water, Japan also has two massive floating oil storage “yards,” each covering more than 130,000 square feet and holding together 11 million kiloliters of oil.
Floating cities would be many times larger and several orders of magnitude more complex. Olaf Waals, a naval architect and engineer for MARIN, the Maritime Research Institute of the Netherlands, has produced what is arguably the first piece of solid technology that would make up the ground level of an ocean floating municipality of whatever size.
Waals is quick to point out that the floating communities are not new—houseboats are common on Amsterdam’s placid canals. But Waals wants his communities to stay afloat in waters as violent as those of the North Sea. “What would be required to achieve that goal?” he asked himself not too long ago.
One challenge Waals had to meet was squaring the conflict between size and stress. Making the structure very large was essential to weathering storms, but the stresses on an enormous, solid rigid structure would be unmanageable.
“And if it becomes really large—like two miles across—how do you fabricate that?” Waals asked. “The largest shipping docks in the world are 400 meters long, so you can’t build such a thing with current-day technologies.”
Waals's solution is to create modular, three-sided islands that can work for any size and, eventually, in any kind of weather. Linked together, triangles more easily handle waves, be they rogue or regular, than the squares and rectangles favored by conventional engineers.
“If you make a surface of triangles, it is easier to flex with waves from any direction,” Waals said. The center of this island is made of larger triangles, as the island will do less flexing there. The central rigidity will help it rise and fall with greater stability.
Why not make the whole thing rigid? “Imagine you make a completely rigid island—in theory, yeah, you could make an island that is completely stable,” Waals said. “But there is a price to pay: if you make it really rigid, then the loads inside the island will still be there and you will need to accommodate them.”
You May Also Like: Developing and Verifying Deepwater Offshore Wind Turbines
Whatever the shape, such a platform would have to survive the roughest waters that the weather might toss up in 200-odd years. To test his grid of triangles, Waals pummeled them with the equivalent of 82-foot waves in MARIN’s test pool, one of the largest indoor pools in the world. The platform rode the waves like a magic carpet. The crests did not crash over the island and the front wave-facing end did all the flexing.
“You don’t want to put your houses there,” Waals said.
Without the flexibility, a hinge-free island would need more freeboard—that is, the distance from the water to the deck—which would require much more material. Waals is now at work creating a model that more acutely proves the viability of the concept. “Instead of just a yellow island with a flat surface, this will really be a floating city with buildings that test the design,” he said.
Mitigating Forces
Not every engineer studying very large floating structures is convinced that flexibility is necessary. While Jan van Kessel, senior engineer in floating city development for the Dutch architectural firm Blue21, agrees that the basic elements of a floating city must be modular, he favors rigidity. “A floating city is fairly large, so by definition it has a high stability,” he said. “So it does not react to the waves very much.” Van Kessel has designed a platform that floats on a cushion of air, something like an overturned canoe.
For a floating city to be large, rigid, and modular, the connectors between modules become the weak link. “Technically, this is the biggest challenge,” van Kessel said. “How do you connect the modules so that they survive high waves? We haven’t solved that yet.”
The offshore oil industry has plenty of experience building floating structures. Though putting a city on some kind of massive oil rig would be prohibitively expensive, borrowing ideas from the industry could prove the fastest way to living on the ocean. For instance, instead of sitting right on the water, why not increase the freeboard and rest the platform on multiple spars. “Like a coke can floating upright, with a fair amount of ballast in the bottom, so it’s inherently stable,” said John Halkyard, an ocean engineer who has designed many offshore platforms and author of Design and Analysis of Floating Structures. “Consider that as a building block, have a number of these spars spaced apart, then have beams on them with hinges—the spar is going to roll.”
Semi-submersible rigs already rest on submerged pontoons. Those pontoons do more than keep the structure afloat. “The wave forces on the pontoons are designed to be equal and opposite on columns, so for the worst storm you get wave force cancelling effects,” Halkyard said. “That’s standard practice for pontoon design.” Similarly, to mitigate wave forces and decrease drag, floating cities could use some modified form of the bulbous bow found on tankers under the water line.
“You could put a skirt on it so you get cancellation forces,” Halkyard said. “When a crest is going over, the fluid is accelerating downward—the downward force cancels the upward force on the main spar columns. That would take care of your heaves up and down.”
Whether it’s spars, pontoons, or hinged triangles that keep a floating city afloat, the material it’s made from will be expected to survive for generations. “For oil and gas platforms we usually speak of a life of 20 or 40 years,” said Torgeir Moan, an engineer and professor of marine technology at the Norwegian University of Science and Technology as well as co-author of Stochastic Dynamics of Marine Structures. “Normally, when we talk about infrastructure, we would like to plan for 1,000 years. But it’s not possible to guarantee a maintenance-free system for 100 years.”
Any structure made of steel will have to be painted—and repainted. Ships get hauled out of the water for their touch ups. Not a likely scenario for a city. There are other materials that might better protect steel, but their longevity is not known, and they are prohibitively expensive. Another option is cathodic protection—turning the metal into the cathode of an electrochemical cell. But this option only works for fully submerged structures.
Concrete may be the best alternative, but, the difficulties of using it may outweigh the benefits. Sea-worthy concrete will have to be crack-proof or the metal it’s reinforced with is likely to corrode, a problem that plagued the concrete ships of a century ago. “Concrete floating structures have been built in that past but not to that scale and not that many,” Waals said. “The effects of long-term salt water not known on concrete.”
Very large floating structures have already been built from concrete; the Evergreen Point Floating Bridge, for instance, rests on 77 concrete pontoons. But it will take decades before its long-term performance can be assessed.
The Largest Thing Possible
Any floating city far from shore will need to produce its own electricity. Wind power is the obvious choice, and the offshore wind industry is already exploring floating structures as it moves into deeper water.
“Once you get to more than 65 or 70 meters of water depth, the economics of fixing structures to the sea bed are such that it’s far more desirable to float,” said Feargal Brennan, a professor of naval architecture and offshore engineering at the University of Strathclyde Offshore Engineering Institute.
While single wind turbines have been tested on spars and triangular semi-submersibles platforms, there’s no real reason to stop at one. “Once we’ve bitten the bullet, then the bigger you get, the better,” Brennan said. “If you consider the cost threshold, by the time you’ve built a large floating foundation, you’ve got to put the largest thing on it possible.”
Brennan and his colleagues are looking at the design of very large floating structures capable of supporting several 150-MW turbines. The first step is building the software tools that would allow designers to create floating islands. The structures would be so large that as they deform under loading, the loading itself changes. “We can’t just use conventional FEA to deal with this,” he said.
Though he’s still at work creating those tools, Brennan has ideas about how best to minimize the effects of waves. One is to change a platform’s hydrodynamic response characteristics by taking on—and jettisoning—ballast water to and from a hull or tank. Crane vessels already use such a system, pumping water at great speed from tank to tank to suppress motion. And hinges, not unlike those conceived by Waals, could aid in that suppression by changing their stiffness to accommodate different wave sizes. They could also add to the energy production of the whole island with every wave induced flex.
A structure large enough to support a small wind farm could do much more. For instance, the electricity from the turbines could power a hydrolysis plant to make hydrogen fuel; that would allow wind farms to be established far beyond the reach of submarine electricity cables. Or the space under the decks could be used for aquaculture.
“For fish stock it’s better to be away from coastal areas,” Brennan said. “You don’t get the pollution from fish farms and the health of the fish is far, far better.”
Wading In
When engineering experts saw Oceanix’s initial plans for floating cities, they acknowledged that the scope was ambitious. But according to some who looked at the proposal, the engineering was naïve. For instance, Nicholas Makris, a professor of mechanical and ocean engineering at MIT, attended the meeting; when he asked if anyone had ever been on the ocean during a hurricane, no one raised a hand.
“They had thought of a lot of interesting things from the perspective of reinventing the whole urban landscape,” Makris said. “But the thing they really didn’t have down was the naval architecture and the marine engineering side of things. We thought we could help them with that.”
The structures, and the base they were meant to sit on were, simply put, not seaworthy. Rather than go the route of off-shore oil platforms, which survive over deep waters but cost billions, Makris suggested giving up on the idea of living in the middle of the ocean, at least for now.
“If you immediately try to go into high sea states, you are completely going to lose your urban audience. You can move out slowly, and have their life style not change much,” he said. The first baby steps should be taken in naturally protected harbors—the kind that have given rise to major coastal cities from Venice to Manhattan. Where the waves are kept to a minimum by geography, floating communities will need less freeboard.
Makris is now trying to move toward a first prototype. “We’re talking a half a kilometer, just one structure, with some kind of functional establishment on it—we don’t know if it’s going to be a school or a home for the elderly—where there would be some kind of community,” he said. But he’s a long way from putting anything in the water.
“We don’t have the magic wand here, we’re relying on bringing people together.”
Creating a waterborne habitat for our species may not require revolutionary new technology, but uniting proven technologies and testing the heck out of them. “These technologies are out there,” said Oceanix’s Chen. “We just need to put them together. It’s like what William Gibson said about the future: ‘The future is already here—it’s just not very evenly distributed.’ ”
Michael Abrams is a technology writer based in Westfield, N.J.