Designing the Most Effective Heat Exchanger
Designing the Most Effective Heat Exchanger
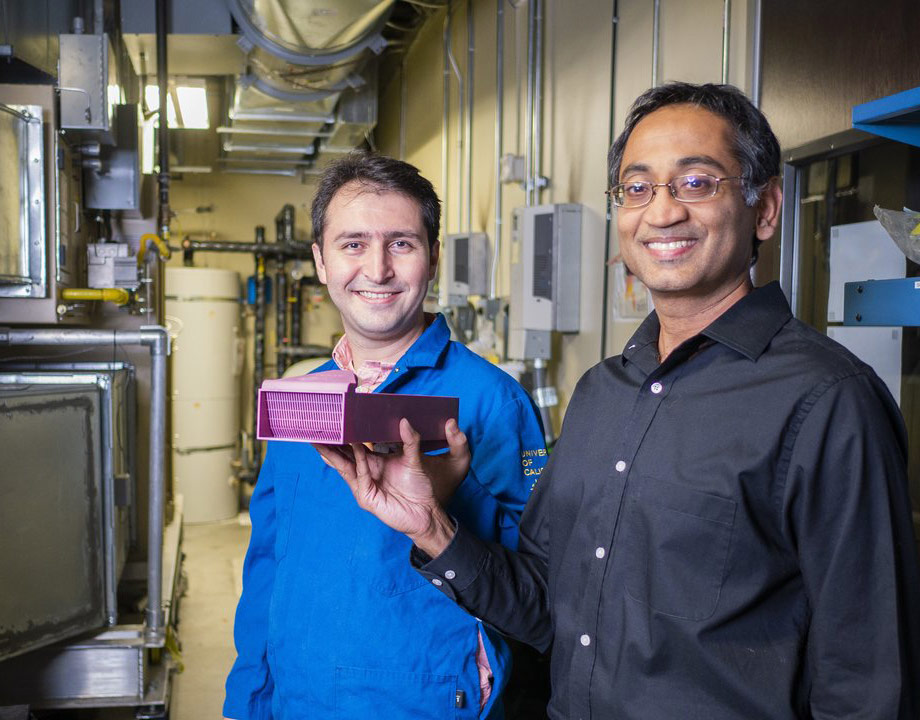
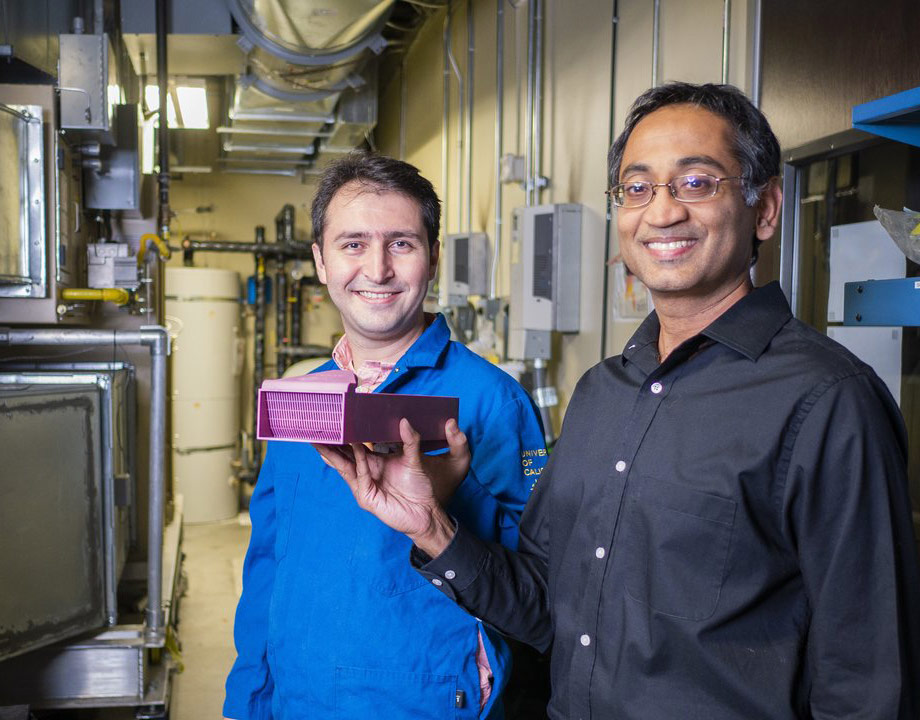
Western Cooling Efficiency Center R&D engineer Erfan Rasouli and Vinod Narayanan (right) show off a 3D-printed heat exchanger. Photo: Paul Fortunato, UC Davis
High-temperature heat exchangers could reduce the amount of fuel needed to power many industrial processes, reducing costs and improving energy efficiency along the way. But first, researchers need to find the best way to create those high-temperature, high-pressure, efficient, and compact heat exchangers.
Three-dimensional printing is the best answer, but it does bring challenges, said Andrew Rollett, a Carnegie Mellon University professor of materials science and engineering.
“We have to be able to print these heat exchangers because the only way to make them efficient enough and modular enough, is through 3D printing,” he said.
Further Reading: Supercritical Power
To look at how high-temperature heat exchangers could be 3D printed, Rollett’s lab is partnering with the energy efficiency expert Vinod Narayanan, a mechanical and aerospace engineering professor at the University of California, Davis, and the associate director of the Western Cooling Efficiency Center (WCEC).
At the WCEC, Narayanan leads a group called the Solar/Supercritical CO2 Thermal Energy Enhancement Laboratory (STEEL), a facility specifically established to research and test advanced heat exchangers working with high pressure and high temperature fluids.
Most heat exchangers today are limited in performance and efficiency because their structure limits maximum heat transfer rates—the way in which the thermal energy moves from the hot side to the cold side of the exchanger. New exchanger designs, new materials, and new manufacturing techniques could raise the performance while keeping manufacturing and operating costs low, according to the U.S. Department of Energy’s Advance Research Projects Agency for Energy (ARPA-E) that provided a grant for the Rollett and Narayanan teams’ research.
Heat exchangers transfer heat from one fluid to another while keeping the fluids from coming into contact with each other. They are widely used in power generation, space heating, refrigeration, air conditioning, and transportation, and can advance development of high-efficiency modular power systems. However, most are extremely large and expensive.
The team is developing high-temperature heat exchangers that must pass strength requirements while operating at 850 °C. The exchangers must operate at these high temperatures and pressures because they’re using supercritical carbon dioxide as a fluid, Rollett said.
Carbon dioxide is becoming more widely used in heat exchangers found in refrigerators, heat pumps, and in other power-producing devices. Compared with other fluids, it’s more chemically stable and is noncorrosive. And due to its relatively high working pressure, the carbon dioxide system is more compact than the system operating with other working fluids.
Learn More About: 6 Innovative Ways to Use 3D Printing
A typical heat exchanger is made with metal and has a rectangular architecture composed of right angles, straight lines, and stacks. These are the types of shapes most easily manufactured using traditional techniques, but they aren’t the best shapes for maximizing heat exchange in a small space.
And they certainly aren’t the best suited for high-temperature and high-pressure heat exchangers.
“There are very few materials and even fewer fabrication methods that can handle those pressures and temperatures,” Narayanan said.
Printing could cut costs and manufacturing methods while bringing other benefits to the table, Rollett said.
The 3D-printing method is ideal for high-temperature, high-pressure heat exchangers because the exchanger itself is composed of a single block—there are no welded or brazed joints that can fail, Narayanan said.
In addition to maintaining strength, a 3D-printed exchanger must resist gas corrosion, meaning material choice is important.
“We're trying to introduce alloys that can be 3D printed that have significantly higher temperature capability compared to the standard ones that everybody knows about,” Rollett said.
His team will use machine learning to find potential materials options. The computer algorithms will track the many potential alloys along with their composition, properties, and how they perform. Over time, the algorithms will learn to recognize the best alloys for experimentation.
“Instead of picking some alloy and saying, ‘this looks as if it might do the job,’ and then perhaps discovering that we can't print it, I'd rather try to put it into some systematic format and a database of some kind,” Rollett said. “So, if something doesn't work out, I can take a look at the next candidate.”
Editors' Pick: Heated Volcanic Rocks Store Energy
Rollett’s team is focusing on printing the 3D exchanger and studying the materials to characterize them and understand their microstructure, strength, and creep. They will then send a sample design to Narayanan’s lab for pressure testing and thermal characterization to see if it’s capable of withstanding high temperatures between 800 °C and 850 °C.
If the tests are successful, Narayanan will develop numerical models of what a large-scale version of the technology might look like.
The teams will then work with their manufacturing partners to look at cost modeling and potential markets for the technology, Narayanan said.
Jean Thilmany is an engineering writer based in St. Paul, Minn.
Three-dimensional printing is the best answer, but it does bring challenges, said Andrew Rollett, a Carnegie Mellon University professor of materials science and engineering.
“We have to be able to print these heat exchangers because the only way to make them efficient enough and modular enough, is through 3D printing,” he said.
Further Reading: Supercritical Power
To look at how high-temperature heat exchangers could be 3D printed, Rollett’s lab is partnering with the energy efficiency expert Vinod Narayanan, a mechanical and aerospace engineering professor at the University of California, Davis, and the associate director of the Western Cooling Efficiency Center (WCEC).
At the WCEC, Narayanan leads a group called the Solar/Supercritical CO2 Thermal Energy Enhancement Laboratory (STEEL), a facility specifically established to research and test advanced heat exchangers working with high pressure and high temperature fluids.
High-Effeciency Power: Supercritical CO2
Most heat exchangers today are limited in performance and efficiency because their structure limits maximum heat transfer rates—the way in which the thermal energy moves from the hot side to the cold side of the exchanger. New exchanger designs, new materials, and new manufacturing techniques could raise the performance while keeping manufacturing and operating costs low, according to the U.S. Department of Energy’s Advance Research Projects Agency for Energy (ARPA-E) that provided a grant for the Rollett and Narayanan teams’ research.
Heat exchangers transfer heat from one fluid to another while keeping the fluids from coming into contact with each other. They are widely used in power generation, space heating, refrigeration, air conditioning, and transportation, and can advance development of high-efficiency modular power systems. However, most are extremely large and expensive.
The team is developing high-temperature heat exchangers that must pass strength requirements while operating at 850 °C. The exchangers must operate at these high temperatures and pressures because they’re using supercritical carbon dioxide as a fluid, Rollett said.
Carbon dioxide is becoming more widely used in heat exchangers found in refrigerators, heat pumps, and in other power-producing devices. Compared with other fluids, it’s more chemically stable and is noncorrosive. And due to its relatively high working pressure, the carbon dioxide system is more compact than the system operating with other working fluids.
Learn More About: 6 Innovative Ways to Use 3D Printing
A typical heat exchanger is made with metal and has a rectangular architecture composed of right angles, straight lines, and stacks. These are the types of shapes most easily manufactured using traditional techniques, but they aren’t the best shapes for maximizing heat exchange in a small space.
And they certainly aren’t the best suited for high-temperature and high-pressure heat exchangers.
“There are very few materials and even fewer fabrication methods that can handle those pressures and temperatures,” Narayanan said.
ML to Find Suitable 3D-Printing Material
Printing could cut costs and manufacturing methods while bringing other benefits to the table, Rollett said.
The 3D-printing method is ideal for high-temperature, high-pressure heat exchangers because the exchanger itself is composed of a single block—there are no welded or brazed joints that can fail, Narayanan said.
In addition to maintaining strength, a 3D-printed exchanger must resist gas corrosion, meaning material choice is important.
“We're trying to introduce alloys that can be 3D printed that have significantly higher temperature capability compared to the standard ones that everybody knows about,” Rollett said.
His team will use machine learning to find potential materials options. The computer algorithms will track the many potential alloys along with their composition, properties, and how they perform. Over time, the algorithms will learn to recognize the best alloys for experimentation.
“Instead of picking some alloy and saying, ‘this looks as if it might do the job,’ and then perhaps discovering that we can't print it, I'd rather try to put it into some systematic format and a database of some kind,” Rollett said. “So, if something doesn't work out, I can take a look at the next candidate.”
Editors' Pick: Heated Volcanic Rocks Store Energy
Rollett’s team is focusing on printing the 3D exchanger and studying the materials to characterize them and understand their microstructure, strength, and creep. They will then send a sample design to Narayanan’s lab for pressure testing and thermal characterization to see if it’s capable of withstanding high temperatures between 800 °C and 850 °C.
If the tests are successful, Narayanan will develop numerical models of what a large-scale version of the technology might look like.
The teams will then work with their manufacturing partners to look at cost modeling and potential markets for the technology, Narayanan said.
Jean Thilmany is an engineering writer based in St. Paul, Minn.