Bioengineering Blog: Simulation at the Crossroads of Engineering and Biology
Bioengineering Blog: Simulation at the Crossroads of Engineering and Biology
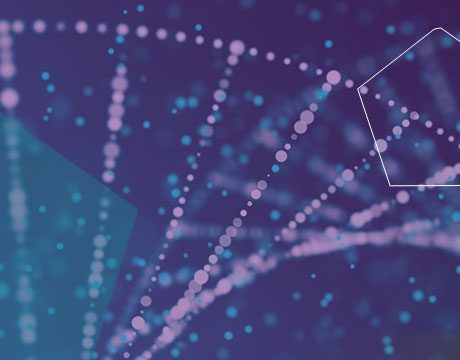
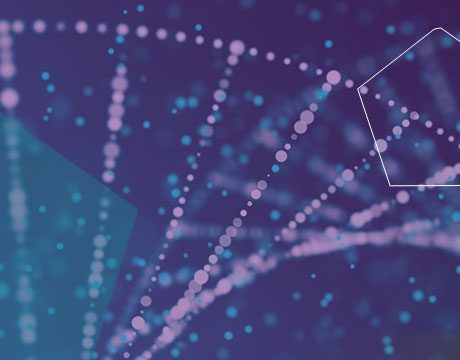
Designing medical devices is complicated, but computational modeling and simulation promises to provide shorter development time and safer treatments.
What sets computational modeling and simulation of medical devices apart from other analyses? It is the same thing that makes them medical— their interaction with biology. When running a stress analysis on a device mechanism or a thermal analysis on enclosed electronics, the modeling is the same for medical devices as for other products. But when questioning the interaction with biological tissue, simulations start to take on elements that are unique to medical devices.
Consider the following inquiries:
What laser wavelength and power provide the desired surgical result for our new device concept?
How does bone remodeling affect loading of a hip implant over the months and years after surgery?
How much more power do we have to supply at the electrosurgery generator if we increase the size of our deployable electrode by 20 percent?
What are the performance expectations in human trials for our device developed using porcine models?
Is our sensor placement optimized for the physiological parameter we want to measure?
If we change our surgical tool design/manufacturing method/algorithm in order to improve manufacturability, will it change the surgical effect in unintended ways?
In order to analyze with simulation tools, every one of these scenarios requires a computational model for its biological materials. Tissue models range from simple to complex; from static and isotropic defined materials on one end to nonlinear and partially reversible multiscale linked physical mechanisms accounting for anisotropy in tissue layers and induced biological response (like heat-shock or healing) on the other. Understanding the material science of biological tissue is key as the need for accurate and timely simulations is at the forefront of device design.
Another complicating factor for device design is the variability of material parameters seen not only between but also within patients. Things like age, hydration, disease state, or scar tissue all play a role in tissue variability, and quickly outstrip the relevance of static material properties. The ability of computational modeling and simulation to provide insight into the sensitivity of the result to the expected variability of the multitude of system inputs provides a powerful tool to know if any new design will likely be effective across a wide range of patient populations.
As simulation data is included more and more in 510(k) and PMA submissions to the Food and Drug Administration and other regulatory bodies, knowledge of key sensitive inputs for the device system will be the new expectation.
Defining mathematical models for biological materials and their interaction with medical device designs provides many engineering challenges, but the advantages are well worth it for both medical device companies as well as patients. As computational modeling and simulation are further incorporated into medical device development, the benefit will be safer and more effective treatments, as well as shorter development times.
Arlen Ward, Ph.D., P.E., is a Principal Modeling and Simulation Engineer with System Insight Engineering LLC, a medical device simulation consultancy.
Opinions expressed are the author’s and do not necessarily reflect the views of ASME.
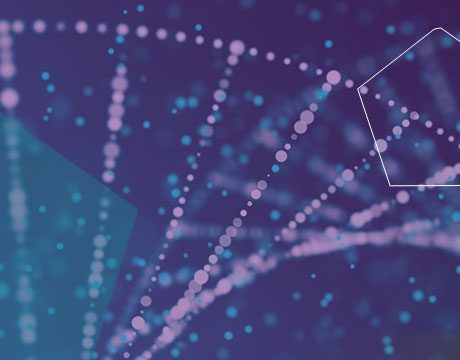
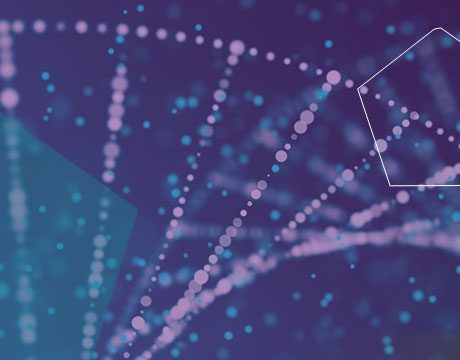