7 Digital Twin Applications for Manufacturing
7 Digital Twin Applications for Manufacturing
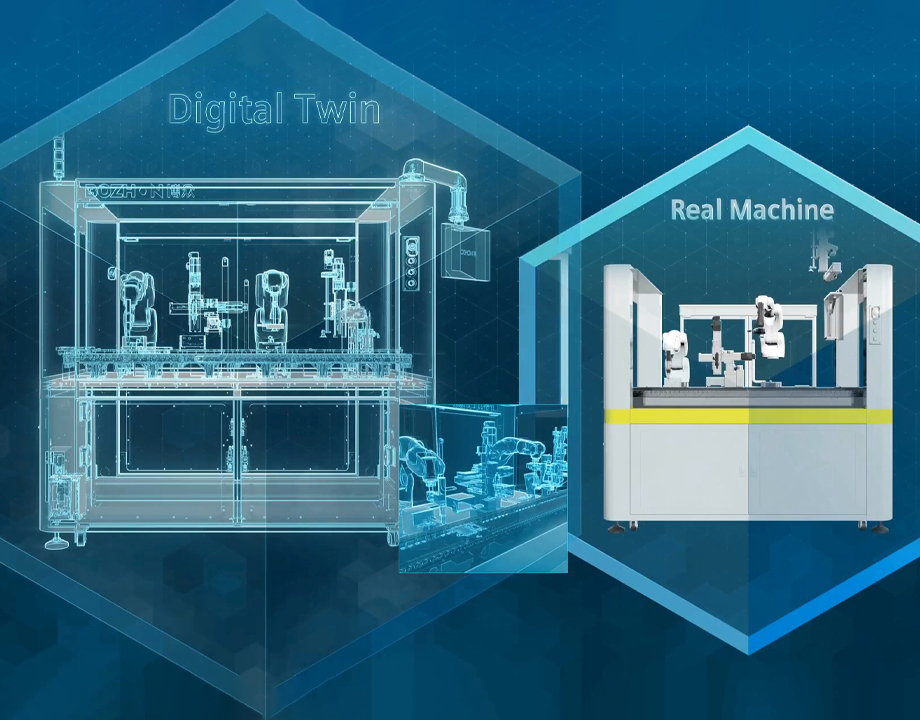
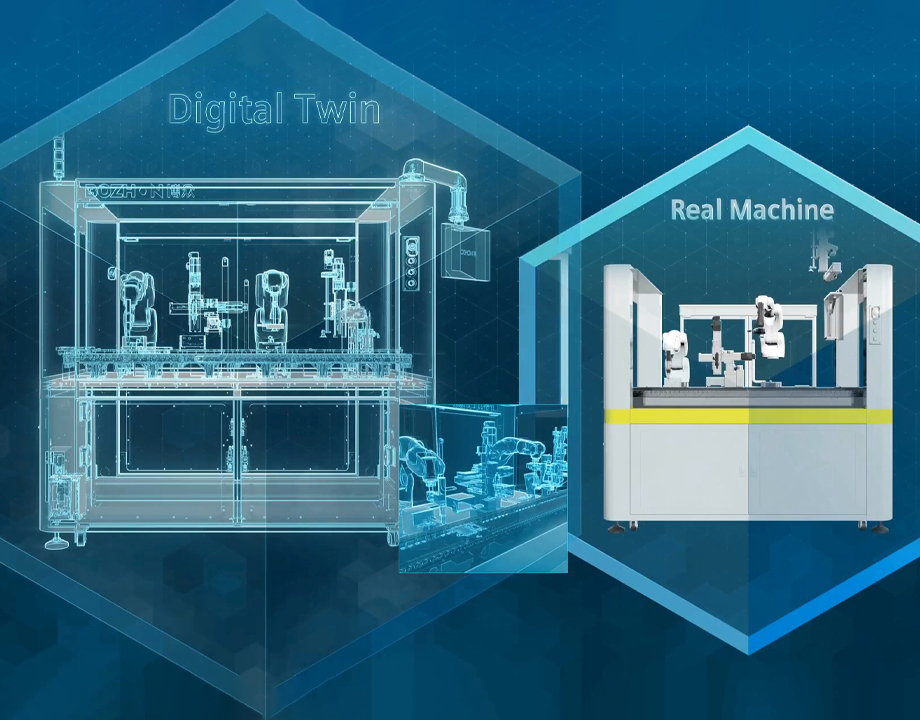
The role of digital twins is expanding into manufacturing for quality management, supply chain management, predictive maintenance, and customer experience.
A digital twin is an exact virtual copy of an object, product, piece of equipment, person, process, supply chain, or even a complete business ecosystem. It is created using data derived from the Internet of Things (IoT) sensor technologies that are attached to or embedded in the original object. This cloud-connected data allows for both structural and operational views of what happens to the object in real-time, allowing engineers to monitor systems and model systems dynamics. Adjustments can be made to the digital twin to see how the system would change in real life before making any changes to the original system.
“More than a blueprint or schematic, a digital twin combines a real-time simulation of system dynamics with a set of executive controls,” said technology consultant and advisor Daniel Araya. Serving as both an interactive simulation and a set of administrative tools, digital twins manage facilities, systems, and machines, while gathering data to drive performance.”
As more companies embrace IoT and big data, digital twin technology is becoming more popular. Deloitte estimates that the digital twins’ global market will grow at a 38% compound annual growth rate to reach $16 billion by 2023.
Below are seven ways that digital twins are used to improve manufacturing operations.
Explore the Infographic: Urban Digital Twins Reflect Smart Cities
Recommended for You: Smart Cities Look for Digital Twins
You May Also Like: Engineers Learn to Work with AI
Digital twins will only get more popular as companies learn how to use them to improve productivity and reduce costs. A 2020 study by Research and Markets indicates:
Mark Crawford is technology writer based in Corrales, N.M.
Learn More at ASME's Digital Twin Summit
“More than a blueprint or schematic, a digital twin combines a real-time simulation of system dynamics with a set of executive controls,” said technology consultant and advisor Daniel Araya. Serving as both an interactive simulation and a set of administrative tools, digital twins manage facilities, systems, and machines, while gathering data to drive performance.”
As more companies embrace IoT and big data, digital twin technology is becoming more popular. Deloitte estimates that the digital twins’ global market will grow at a 38% compound annual growth rate to reach $16 billion by 2023.
Below are seven ways that digital twins are used to improve manufacturing operations.
Digital twins can be virtual prototypes during the design phase and be adjusted to test different simulations or designs before investing in a solid prototype. This saves time and cost by reducing the number of iterations required to get the product into production. 1. Product Design
Explore the Infographic: Urban Digital Twins Reflect Smart Cities
2. Process Optimization
Sensors on a manufacturing line can be used to create a digital twin of the process and analyze important performance indicators. Adjustments to the digital twin can identify new ways to optimize production, reduce variances, and help with root-cause analysis.3. Quality Management
Monitoring and responding to data from IoT sensors during production is essential for maintaining top quality and eliminating rework. The digital twin can model every part of the production process to identify where variances occur, or if better materials or processes can be used.Supply chains and logistics/distribution firms rely on digital twins to track and analyze key performance indicators, such as packaging performance, fleet management, and route efficiency. They are especially useful for optimizing just-in-time or just-in-sequence production and analyzing distribution routes. 4. Supply Chain Management
Recommended for You: Smart Cities Look for Digital Twins
5. Predictive Maintenance
Digital twins for individual equipment or manufacturing processes can identify variances that indicate the need for preventative repairs or maintenance before a serious problem occurs. They can also help optimize load levels, tool calibration, and cycle times.The ready availability of operational data from digital twins makes it easy to share across disciplines, enabling collaboration, improved communication, and faster decision-making. Engineering, production, sales, and marketing can all work together, using the same data, to make more informed decisions. 6. Cross-Discipline Collaboration
You May Also Like: Engineers Learn to Work with AI
7. Analyze the Customer Experience
Digital twins are often used to collect data over time that deliver insights into product performance, distribution, and end-user experience. This data can be used to help engineers and designers improve the customer response to the product, especially through customization and ease of use.Digital Twins and the Future of Manufacturing
Digital twins will only get more popular as companies learn how to use them to improve productivity and reduce costs. A 2020 study by Research and Markets indicates:
- Up to 89% of all IoT platforms will include digital twins by 2025
- Digital twinning will be a standard IoT feature by 2027
- Nearly 36% of executives across a variety of industries understand the benefits of digital twinning, with about half of them planning to use it in their operations by 2028
Mark Crawford is technology writer based in Corrales, N.M.
Learn More at ASME's Digital Twin Summit