Bioengineering Blog: Simulation Does Not Replace Physical Testing
Bioengineering Blog: Simulation Does Not Replace Physical Testing
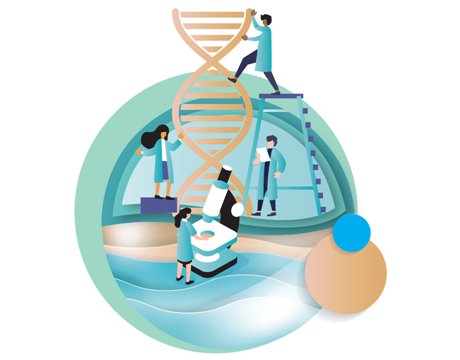
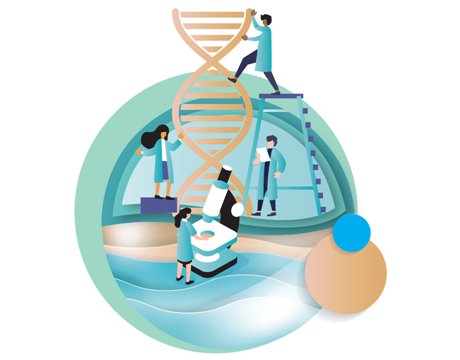
When simulation and experiments are used together, principles are verified faster and more efficiently than in isolation.
When talking with medical device companies about incorporating computational modeling and simulation into their research and development processes, it is often necessary to highlight that simulation is not meant to be a replacement for all physical testing. Prototypes, bench tests, preclinical labs and clinical studies are not replaced by modeling and simulation, but when used side by side they become more efficient at reaching project goals. When simulation and experiments are used together, insights are highlighted faster, experimental design is more effective, and underlying physical principles are verified all at a time and cost efficiency not seen with either in isolation.
As an enhancement for physical testing, simulation is a force multiplier for the benefits in laboratory work. When used alongside experimental tests on prototypes or alongside data collection in clinical studies simulation provides a window into things that would be otherwise difficult or impossible to measure and validation for theories on underlying processes.
Editor's Choice: Remote Modeling and Simulation for Medical Design
For example, with temperature measurements it is difficult to physically measure an entire temperature field simultaneously and experimentalists are limited to choosing individual points or at best an array of measured points to characterize the entire field. When coupled with modeling and simulation, it is possible to visualize the entire predicted temperature field in a volume of tissue and determine the optimal positioning of measurement probes in the experimental setup.
For MRI interactions with human bodies it is not possible to measure the electromagnetic fields inside the tissue, but computational modeling and simulation provide visualizations and insight into the interaction– informing decisions that will impact patient safety and treatment efficacy.
More for You: Computational Lung Model May Guide How Ventilators Are Used
On the opposite site of the coin, computational modeling and simulation can be used to verify an engineer’s understanding of the underlying physical principles for their medical device project. Through simulation, the physical mechanisms that effect device performance are linked through the multiphysics interactions and the resulting prediction is compared to the associated experimental scenario. Even through the process of model validation, the R&D team’s understanding of how the device works is put to the test by linking the model to observed physical measurements. When the model predictions agree with the observable experiment across the range of use, the engineering team can be confident they have captured the relevant physics for their application.
The complementary aspects of simulation and experiment provide unique information through both efforts that accelerate the understanding needed to make great products. As medical device companies continue to align their development processes to both computation modeling and experimental efforts the time and cost savings will be joined with more successful outcomes through improved patient safety and more effective medical interventions.
Arlen Ward, Ph.D., P.E., is a principal modeling and simulation engineer with System Insight Engineering, a medical device simulation consultancy.
Opinions expressed are the author’s and do not necessarily reflect the views of ASME.
As an enhancement for physical testing, simulation is a force multiplier for the benefits in laboratory work. When used alongside experimental tests on prototypes or alongside data collection in clinical studies simulation provides a window into things that would be otherwise difficult or impossible to measure and validation for theories on underlying processes.
Editor's Choice: Remote Modeling and Simulation for Medical Design
For example, with temperature measurements it is difficult to physically measure an entire temperature field simultaneously and experimentalists are limited to choosing individual points or at best an array of measured points to characterize the entire field. When coupled with modeling and simulation, it is possible to visualize the entire predicted temperature field in a volume of tissue and determine the optimal positioning of measurement probes in the experimental setup.
For MRI interactions with human bodies it is not possible to measure the electromagnetic fields inside the tissue, but computational modeling and simulation provide visualizations and insight into the interaction– informing decisions that will impact patient safety and treatment efficacy.
More for You: Computational Lung Model May Guide How Ventilators Are Used
On the opposite site of the coin, computational modeling and simulation can be used to verify an engineer’s understanding of the underlying physical principles for their medical device project. Through simulation, the physical mechanisms that effect device performance are linked through the multiphysics interactions and the resulting prediction is compared to the associated experimental scenario. Even through the process of model validation, the R&D team’s understanding of how the device works is put to the test by linking the model to observed physical measurements. When the model predictions agree with the observable experiment across the range of use, the engineering team can be confident they have captured the relevant physics for their application.
The complementary aspects of simulation and experiment provide unique information through both efforts that accelerate the understanding needed to make great products. As medical device companies continue to align their development processes to both computation modeling and experimental efforts the time and cost savings will be joined with more successful outcomes through improved patient safety and more effective medical interventions.
Arlen Ward, Ph.D., P.E., is a principal modeling and simulation engineer with System Insight Engineering, a medical device simulation consultancy.
Opinions expressed are the author’s and do not necessarily reflect the views of ASME.