Innovative Fiber Offers New Textile Possibilities
Innovative Fiber Offers New Textile Possibilities
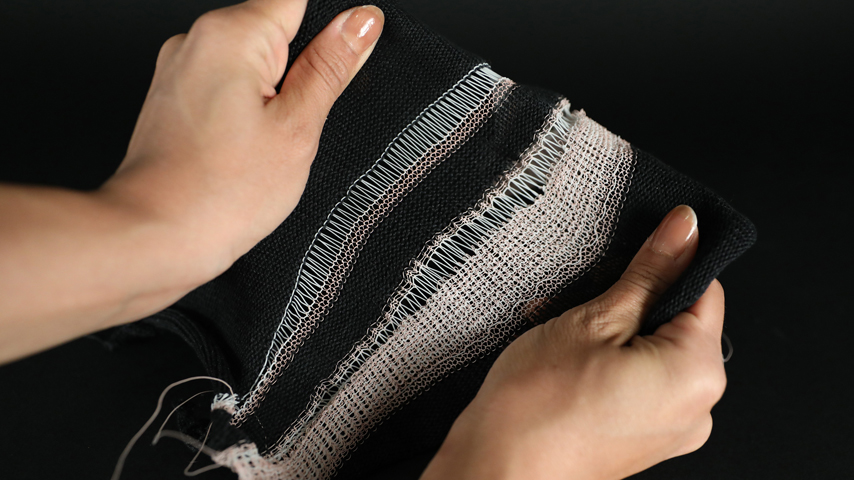
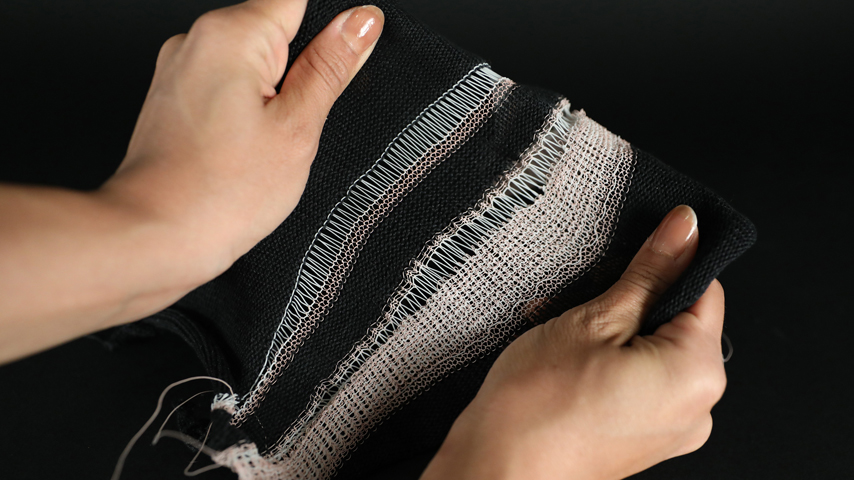
FibeRobo is a shape-changing fiber based on liquid crystal elastomers.
There have been several advances in fiber actuation over the past decade, but existing fibers faced limitations in contraction capacity, actuation speed, and shape reversal capability. But the most significant challenge was compatibility with textile machinery. Among current fibers, some could only contract by 5 percent over a five-minute period, some lacked self-reversibility, and required user intervention for restoration to their original shape, and none were compatible with industrial machines.
Now, a team of researchers at the Massachusetts Institute of Technology (MIT) have created a material called FibeRobo that is capable of actuating through heat or electric current, shrinking by up to 40 percent, and reverting to its initial shape upon source removal. It’s also compatible with industrial textile machines used in knitting, embroidery, weaving, and sewing.
“The reason we're drawn to textiles for this project is that we already had massive infrastructure of weaving and knitting and beautiful machines that could do very complex fiber-to-fabric assembly," explained Jack Forman, a Ph.D. student at MIT’s Media Lab and Center for Bits and Atoms. “Making a fiber that is compatible with different fabrication processes allows us to tap into the full functionality of complex multi-fiber structures and be able to do that at scale and very quickly.”
Textile Innovations: Self-Decontaminating Material Destroys Viruses Without Burning Skin
To make an impact on the textile industry, a shape-shifting fabric would need to align with industrial machinery, allowing for large scale manufacturing without substantial costs. The fiber would also have to be compatible with various techniques, maintain consistent size and shape to prevent machine jamming, and possess adequate strength to avoid breakage. Ideally, it would seamlessly integrate into industrial machines with minimal process alterations.
The team—comprised of materials and biomedical engineers, interactive designers, a roboticist, and fashion experts—conducted successful tests on FibeRobo using a range of knitting techniques, including plain knit, inlay, plain weave, floats, sewing, and embroidery. This offered an opportunity for “4-dimensional knitting, where a 3D fabric changes shape over time, with the fourth dimension being time,” Forman said.
Each year, the textile industry manufactures 17 million tons of textiles, with only 14.7 percent of that being recycled. As a result, the team aimed to address FibeRobo’s recyclability and biodegradability throughout the research process. Offering textiles for multiple uses could potentially reduce textile consumption, thereby decreasing overall waste.
Become a Member: How to Join ASME
FibeRobo originated from liquid crystal elastomer extruded through a 3D nozzle, which was then stretched and cured on both sides with UV lights. To prevent fiber fusion, the fiber was dipped in mineral oil to establish a protective barrier, followed by another round of UV curing, then the fibers were spun onto a spindle. The researchers found that adjusting the intensity of the UV lights and reducing curing time enhanced the rate of production. With a production cost of $0.20/meter, FibeRobo is 30 to 60 times less expensive than other shape-memory fabrics currently available. Scaling this process to industrial fabrication has the potential to further reduce the cost per meter.
By synthesizing the liquid crystal elastomer in different compositions, the research team successfully created one fiber actuating at 65 °C and another at 47 °C. The researchers tested various applications, including an adaptive sports bra that contracts for additional support as the wearer’s body temperature rises and loosens as it cools. Another test involved a knitted shirt for a dog, contracting from a remote signal to simulate a hug from the pet’s owner. Through testing, “samples were actuated hundreds of times and still worked the same as the first time. In our testing we have yet to see any visible decay in actuation after hundreds of cycles,” Forman explained.
Thanks to its fabrication technique and chemical composition, the fiber is self-reversing at or slightly above body temperature. Possible applications range from medical devices and athletic wear to transforming fashion “garments that could allow someone to look like they owned seven different dresses,” for example, Forman explained. “So one dress lasting the same aesthetic configurations of seven dresses without seven times as much material waste.”
Nicole Imeson is an engineer and writer in Calgary, Alberta.
Now, a team of researchers at the Massachusetts Institute of Technology (MIT) have created a material called FibeRobo that is capable of actuating through heat or electric current, shrinking by up to 40 percent, and reverting to its initial shape upon source removal. It’s also compatible with industrial textile machines used in knitting, embroidery, weaving, and sewing.
“The reason we're drawn to textiles for this project is that we already had massive infrastructure of weaving and knitting and beautiful machines that could do very complex fiber-to-fabric assembly," explained Jack Forman, a Ph.D. student at MIT’s Media Lab and Center for Bits and Atoms. “Making a fiber that is compatible with different fabrication processes allows us to tap into the full functionality of complex multi-fiber structures and be able to do that at scale and very quickly.”
Textile Innovations: Self-Decontaminating Material Destroys Viruses Without Burning Skin
To make an impact on the textile industry, a shape-shifting fabric would need to align with industrial machinery, allowing for large scale manufacturing without substantial costs. The fiber would also have to be compatible with various techniques, maintain consistent size and shape to prevent machine jamming, and possess adequate strength to avoid breakage. Ideally, it would seamlessly integrate into industrial machines with minimal process alterations.
The team—comprised of materials and biomedical engineers, interactive designers, a roboticist, and fashion experts—conducted successful tests on FibeRobo using a range of knitting techniques, including plain knit, inlay, plain weave, floats, sewing, and embroidery. This offered an opportunity for “4-dimensional knitting, where a 3D fabric changes shape over time, with the fourth dimension being time,” Forman said.
Each year, the textile industry manufactures 17 million tons of textiles, with only 14.7 percent of that being recycled. As a result, the team aimed to address FibeRobo’s recyclability and biodegradability throughout the research process. Offering textiles for multiple uses could potentially reduce textile consumption, thereby decreasing overall waste.
Become a Member: How to Join ASME
FibeRobo originated from liquid crystal elastomer extruded through a 3D nozzle, which was then stretched and cured on both sides with UV lights. To prevent fiber fusion, the fiber was dipped in mineral oil to establish a protective barrier, followed by another round of UV curing, then the fibers were spun onto a spindle. The researchers found that adjusting the intensity of the UV lights and reducing curing time enhanced the rate of production. With a production cost of $0.20/meter, FibeRobo is 30 to 60 times less expensive than other shape-memory fabrics currently available. Scaling this process to industrial fabrication has the potential to further reduce the cost per meter.
By synthesizing the liquid crystal elastomer in different compositions, the research team successfully created one fiber actuating at 65 °C and another at 47 °C. The researchers tested various applications, including an adaptive sports bra that contracts for additional support as the wearer’s body temperature rises and loosens as it cools. Another test involved a knitted shirt for a dog, contracting from a remote signal to simulate a hug from the pet’s owner. Through testing, “samples were actuated hundreds of times and still worked the same as the first time. In our testing we have yet to see any visible decay in actuation after hundreds of cycles,” Forman explained.
Thanks to its fabrication technique and chemical composition, the fiber is self-reversing at or slightly above body temperature. Possible applications range from medical devices and athletic wear to transforming fashion “garments that could allow someone to look like they owned seven different dresses,” for example, Forman explained. “So one dress lasting the same aesthetic configurations of seven dresses without seven times as much material waste.”
Nicole Imeson is an engineer and writer in Calgary, Alberta.