Metal to Plastic: Design Flexibility
Metal to Plastic: Design Flexibility
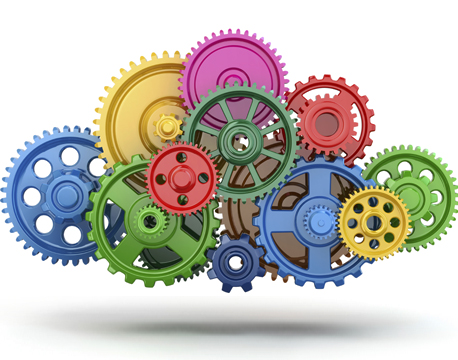
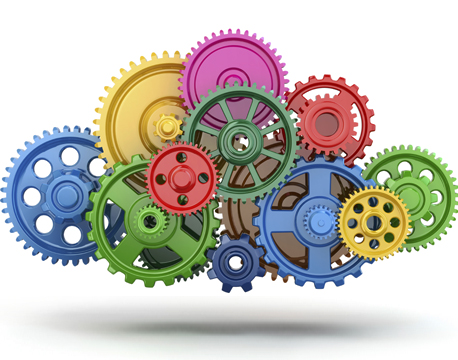
Even though metal-to-plastic conversion has been around since the 1950s, many manufacturers are still not familiar with all the benefits it provides.
Automotive and aerospace companies have been most active in converting existing metal products or parts to plastic, driven by the need to reduce weight and improve fuel efficiency. With proper design, engineered plastics can be just as strong as metal. They can also be more chemical-resistant with exceptional heat resistance, making them good choices for fuel systems, fluid handling systems, and other high-temperature applications.Plastics that are engineered to be thermally and electrically conductive can be used as EMI/RFI shields, or in automotive electronics.
Benefits that conversion to plastic can provide are:- High tensile strength with proper structural design
- Reduced part weight
- Highly repeatable in processing (less scrap)
- Lower manufacturing costs
- Enhanced regulatory compliance
- Greater design flexibility (part consolidation)
- Lower packaging and shipping costs
- Up to six times longer tool life.
Current metal-to-plastic trends focus on reducing weight, improvingstrength and corrosion resistance, and consolidating multiple metal parts into one plastic part.Plastic parts can be just as tough as metal parts and achieve the same tight tolerances, with fewer secondary operations. In general, companies can expect to achieve an overall cost savings of 25% to 50% by converting to plastic parts.
Design Freedom
Converting to plastic parts gives manufacturers more freedom in product design, including greater variety in material selection and being able to create more complex geometries. It is much easier to produce complex shapes out of plastic than metal, due to injection molds allowing for under-cuts, threads, ports, and tight tolerances allowing a net shape to be produced to the finish level specifications.
“Plastics can be made to flow to produce thin-walled parts with uniform wall dimensions, replacing the more costly thicker-walled design features of most die-cast metal parts,” says Ken Glassen, vice president of engineering for Kaysun Corporation, an injection molder in Manitowoc, WI. “Multiple metal parts can be replaced by one injection-molded part made of tough engineered plastic, eliminating the need for fasteners and assembly.”
Plastic parts can actually be stronger than metal parts by using engineering-grade materials with proper structural design. The ability to mold in features for structural strength such as ribs, bosses, and gussets when the part is originally produced (instead of fastening, welding, and gluing afterwards) can increase the total strength of the assembled part as well as reduce additional costs.
“There are many more options available for materials and additives/fillers when using plastic instead of metal,” adds Glassen. “Converting from metal to plastic gives designers the ability to produce final net shape and dimensions, all in one process.”
Material Selection
Polymer science has advanced to the point where vendors can compound a variety of plastic materials with specific fillers and reinforcements that provide a tremendous amount of structural integrity.Plastic can be as strong as metal with proper material selection paired with design optimization, and weigh far less.
Choosing the right plastic can take some time, depending on the project. One of the greatest advantages of plastics is the availability of more than 25,000 engineered materials for manufacturing applications. New, higher-performance blends and hybrids can also be custom-designed to meet very specific performance requirements.
Key considerations for type of plastic are:- Crystalline vs. amorphous: evaluate requirements such as chemical resistance, impact, flow, processing, etc.
- Additives: additives will affect strength, stiffness, temperature performance, appearance, package requirements, and cost.
- Carbon and stainless steel fillersimprove conductive and/or shielding properties.
- Lubricant fillersimprove wear and friction properties.
- Mineral fillersimprove electrical performance, weighted feel, sound dampening, and higher specific gravity and improve dimensional stability.
- Impact modifiersimprove toughness.
Making the Switch
The first step is finding out if the project is suitable for metal-to-plastic conversion. This requires considerable analysis and is not necessarily a quick determination. It is essential to fully understand the end-use application, environmental conditions, material evaluations and analysis, manufacturability, and economic feasibility. The design engineers must be able to accuratelyevaluate the real-world environment that will impact the product, including chemical exposure or contact solutions, temperature ranges, shielding, and forces (including worst-case scenarios). All this information must be analyzed together to make the best material choice.
“With plastic, youcan prove it out using finite element analysis before ever molding a part and investing in tooling,” says Glassen. “With analysis of the entire system up front (system loads, temperatures, chemicals, and UV considerations), you can be sure that plastic is the right choice for your application.”
Mark Crawford is an independent writer.
With plastic, you can prove it out using finite element analysis before ever molding a part and investing in tooling.Ken Glassen, Kaysun Corporation