Top 5 Nanoscale Manufacturing Processes
Top 5 Nanoscale Manufacturing Processes
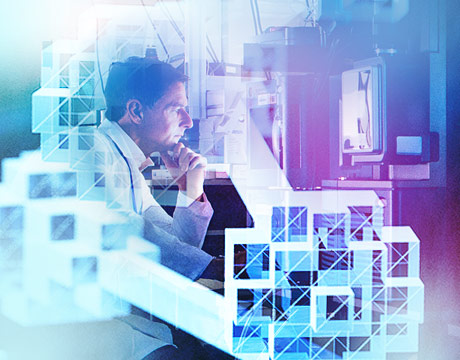
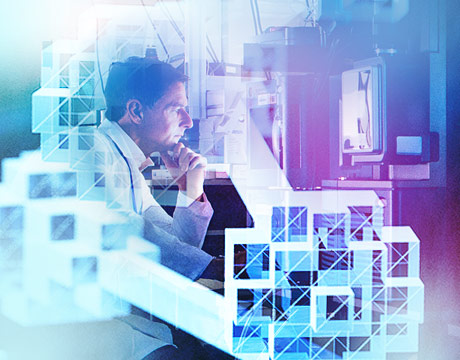
While there is much excitement reported around developments in new manufacturing technologies in the areas of robotics and 3D printing, there is a lot more going on in the nation’s research labs in advanced manufacturing than literally meets the naked eye.
Breakthroughs in nanotechnology and other small-scale work are contributing to improvements in many technology and industry sectors. Many of the benefits come from the ability to create new materials at very small scales to exhibit certain properties, such as stronger, lighter, better electrical conduction and more.
For instance, the Advanced Multi-Scale Manufacturing Lab at Arizona State University, directed by Assistant Professor Keng Hsu, focuses on new manufacturing processes at the nanoscale, microscale and mesoscale levels, aiming to bring theoretical materials to reality. Having studied and harnessed material-energy interaction to create new manufacturing processes for a number of years, Hsu, who holds bachelor’s, master’s and a doctorate in mechanical engineering, the latter from the University of Illinois, is now also working with additive manufacturing. “I’ve seen lots of things come and go,” he says.
Today, he is encouraged by work that he believes offers the most promise for innovative manufacturing technologies based on new hybrid materials and nanotechnology, particularly processes that allow the generation of very, very small features in very large surface areas as well as some other related processes.
1. Printing Integrated 3D Solid Materials
The main technology for basic 3D printing today involves melting metals or plastics and applying it layer by layer to create an object.Because different materials have varying melting points, only one type of material or class of materials can easily be printed at a time.
Researchers are working with “sound,” or vibrations, in a frequency above human hearing to manipulate material properties instead of heating and melting. When the material vibrates, the interaction with the material harnesses a property change and that allows metals to be processed on the same platform as polymers and ceramics.
“What that means is we will be able to construct an entire system … with the push of a button on a relatively inexpensive 3D printer and it will spit out the [entire] product,” Hsu says.
2. New Process for Semiconductor PatterningSemiconductors, so important for the rapidly growing fields of consumer and industrial electronics and optical sensing among others, have presented an interesting challenge for researchers. Both miniaturization and high-volume processing are important in producing affordable yet complex circuits used in many devices.
“When you want to generate very, very small features in the material, it’s not possible to create small features over a very large area in a cost-effective way,” Hsu says. Typicallydone with various photolithography techniques, these are “very powerful but very expensive and the maximum size today is only about a meter or so,” he says. Additionally, when functionally graded semiconductor materials are produced this way, they are not scalable.
Researchers are now studying contact-controlled chemical etching to produce nanoscale-to-microscale size features. Not only can the semiconductor be selectively patterned, the pre-patterned stamp can be reused multiple times, and the resulting material is also highly scalable, lowering costs.
3. Microscale Assembly forNanostructured Metamaterials
Currently, there is no way to assemble components across multiple-size scales. “We can make these very tiny features and can harness the features to tap into nanotechnologies, but when things get that small it is very hard to assemble them,” Hsu says, because there is no physical way of holding the device.
Researchers are using modulated surface energy to control the adhesion of flexible tools to manipulate assembly. They are developing a set of tools with varying sizes of different soft contact tabs that can pick up very small devices and then reposition them. The traditional method is to place the devices in very high-end equipment where tiny robotic arms do the assembly, one by one. “It takes days to make one device,” Hsu says, and thus is very costly.
4. 3D Printing of Customized Shape Memory Polymers
To some extent, 3D-printed active devices have been limited by the lack of small and lightweight actuator systems that have reliable mechanical properties. Researchers are working with shape-memory polymers that can serve as actuators because they respond to external stimuli by expanding or contracting.
“This is a very easy way to achieve actuation purely from using the material’s response to its environment as opposed to putting mechanical components physically in the material,” Hsu says. “A big application would be space missions or anything launched into space – where every single gram of material is very important.”
5. Scalable Nanomanufacturing of Polymer 2D Materials
As with semiconductors, a large-scale photolithography method for high-density small patterns on polymers, used primarily in microelectronics processing, does not exist.Current photolithography methods, while effective, are extremely expensive. Researchers are working on an optical process that avoids the expensive methods available. The process works by partially using the material’s response to light while also controlling the light interacting with the material. “By combining these, you can create very sharp features that are very small,” Hsu says. “It is low-cost, scalable and once developed can have a large impact in how electronic components are made and how much they cost.”
Nancy S. Giges is an independent writer
“When you want to generate very, very small features in the material, it’s not possible to create small features over a very large area in a cost-effective way.Keng Hsu, Director, Advanced Multi-Scale Manufacturing Lab, Arizona State University