We Need to Be Real About AM’s Limitations
We Need to Be Real About AM’s Limitations
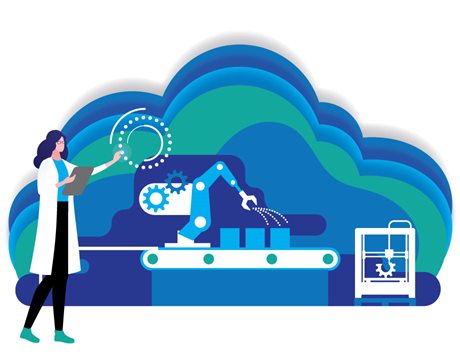
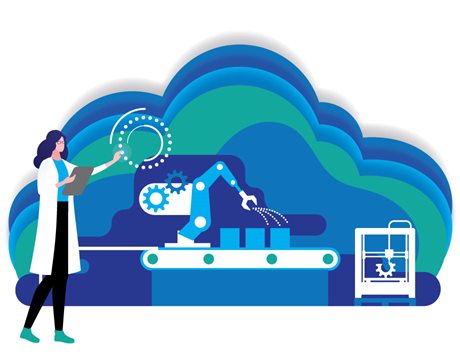
3D printers filled the supply chain gap during the pandemic. But they aren’t ready to replace conventional manufacturing.
When the coronavirus pandemic swept the globe and disrupted conventional supply chains, additive manufacturing stepped up to meet demand. Tales of AM’s deployment were heart-warming: Homes, libraries, and businesses of every size powered up 3D printers to churn out parts.
While this emergent action reignited awareness of AM’s potential to digitize and localize production and fueled predictions of a new normal for manufacturing, the response also revealed the technology’s shortcomings. If companies want to use AM as a supply chain fix, they need to leverage the advantages and mitigate the limitations.
Additive manufacturing’s advantages–chiefly responsiveness and flexibility–have been well chronicled. Armed with little more than a printer, raw material, and a digital part definition, AM can begin manufacturing in minutes. Should the need arise, there is no barrier to switching to a different part with each print run.
The elimination of tooling also makes distributed manufacturing feasible while dramatically reducing startup costs. Fold in the insensitivity to design complexities, and AM becomes a production tool that anyone can use to build whatever they need, when they need it, from any location.
Editors' pick: Manufacturing Blog: Should You Design for Additive Manufacturing?
AM may seem like an ideal solution to prevent or overcome supply chain disruption—if we ignore its shortfalls.
The technology’s most glaring limitation is throughput, which falls far short of typical, high-volume manufacturing processes. AM output, for example, could not meet the demands of medical professionals for face shields and ventilators. Compounding this limitation is the lack of automation for the complete workflow, especially for post-processing and quality assurance.
In times of need, cost takes a backseat to delivery. During the pandemic, AM’s high per-unit cost for protective gear was not a significant factor in purchasing decisions. When less costly alternatives appeared, however, their lower unit cost often trumped any advantages AM offered.
Business also faces an AM integration challenge: AM software solutions for planning, scheduling, and monitoring do not play nice with the established management execution systems systems that run factories. Lack of seamless integration makes AM operations an island in a sea of manufacturing processes.
The final challenge illuminated by the pandemic is lack of guidance, such as standards, certifications, protocols, and best practices. For example, in their rush to make nasal swabs and ventilator splitters, AM practitioners had no playbook from FDA and other regulatory agencies. This issue goes beyond medical compliance. For the most part, additive manufacturers are left to their own devices to characterize and qualify parts and establish best practices.
Considering both strengths and weaknesses, AM proved a viable stopgap solution for needed supplies during the pandemic. Yet its performance is not a watershed moment that alters the future of manufacturing. Instead, the pandemic reignited interest and curiosity in AM as a supply chain alternative, which will give it a bit of momentum going forward.
More About Manufacturing: Engineers Needed to Fill AI Tool Gaps
The pandemic will also stimulate AM suppliers to address their weaknesses and improve their total solution. COVID-19 has shined a light on the advances needed to elevate AM from a stopgap solution to a true manufacturing alternative.
Those stopgap solutions might be needed. Shutdowns, lockdowns, and stay-at-home orders exposed the fragility of existing supply chains and the broad impact of their disruption. This is a lesson all businesses should take to heart. To emerge stronger, companies should evaluate the possible failure modes of their existing supply chain structures, then map out plans to prevent or recover from disruptions.
Manufacturers may find that AM is a supply chain alternative to use as a backup in case of emergency; a bridge during production ramp-up; a supplement for existing supplies—or a primary delivery vehicle for products where AM’s advantages outweigh any limitations.
Todd Grimm is president of T. A. Grimm & Associates, an additive manufacturing consulting and communications company, and a 30-year industry veteran.
While this emergent action reignited awareness of AM’s potential to digitize and localize production and fueled predictions of a new normal for manufacturing, the response also revealed the technology’s shortcomings. If companies want to use AM as a supply chain fix, they need to leverage the advantages and mitigate the limitations.
Additive manufacturing’s advantages–chiefly responsiveness and flexibility–have been well chronicled. Armed with little more than a printer, raw material, and a digital part definition, AM can begin manufacturing in minutes. Should the need arise, there is no barrier to switching to a different part with each print run.
The elimination of tooling also makes distributed manufacturing feasible while dramatically reducing startup costs. Fold in the insensitivity to design complexities, and AM becomes a production tool that anyone can use to build whatever they need, when they need it, from any location.
Editors' pick: Manufacturing Blog: Should You Design for Additive Manufacturing?
AM may seem like an ideal solution to prevent or overcome supply chain disruption—if we ignore its shortfalls.
The technology’s most glaring limitation is throughput, which falls far short of typical, high-volume manufacturing processes. AM output, for example, could not meet the demands of medical professionals for face shields and ventilators. Compounding this limitation is the lack of automation for the complete workflow, especially for post-processing and quality assurance.
In times of need, cost takes a backseat to delivery. During the pandemic, AM’s high per-unit cost for protective gear was not a significant factor in purchasing decisions. When less costly alternatives appeared, however, their lower unit cost often trumped any advantages AM offered.
Business also faces an AM integration challenge: AM software solutions for planning, scheduling, and monitoring do not play nice with the established management execution systems systems that run factories. Lack of seamless integration makes AM operations an island in a sea of manufacturing processes.
The final challenge illuminated by the pandemic is lack of guidance, such as standards, certifications, protocols, and best practices. For example, in their rush to make nasal swabs and ventilator splitters, AM practitioners had no playbook from FDA and other regulatory agencies. This issue goes beyond medical compliance. For the most part, additive manufacturers are left to their own devices to characterize and qualify parts and establish best practices.
Considering both strengths and weaknesses, AM proved a viable stopgap solution for needed supplies during the pandemic. Yet its performance is not a watershed moment that alters the future of manufacturing. Instead, the pandemic reignited interest and curiosity in AM as a supply chain alternative, which will give it a bit of momentum going forward.
More About Manufacturing: Engineers Needed to Fill AI Tool Gaps
The pandemic will also stimulate AM suppliers to address their weaknesses and improve their total solution. COVID-19 has shined a light on the advances needed to elevate AM from a stopgap solution to a true manufacturing alternative.
Those stopgap solutions might be needed. Shutdowns, lockdowns, and stay-at-home orders exposed the fragility of existing supply chains and the broad impact of their disruption. This is a lesson all businesses should take to heart. To emerge stronger, companies should evaluate the possible failure modes of their existing supply chain structures, then map out plans to prevent or recover from disruptions.
Manufacturers may find that AM is a supply chain alternative to use as a backup in case of emergency; a bridge during production ramp-up; a supplement for existing supplies—or a primary delivery vehicle for products where AM’s advantages outweigh any limitations.
Todd Grimm is president of T. A. Grimm & Associates, an additive manufacturing consulting and communications company, and a 30-year industry veteran.