Human Factors Engineering: Why Engineers Should Do More of It
Human Factors Engineering: Why Engineers Should Do More of It
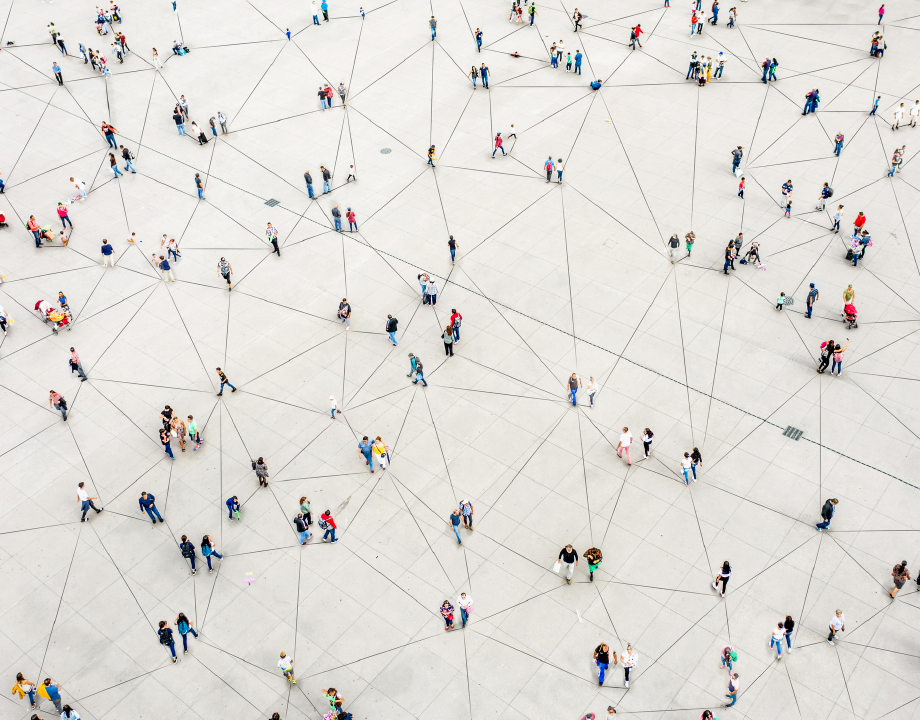
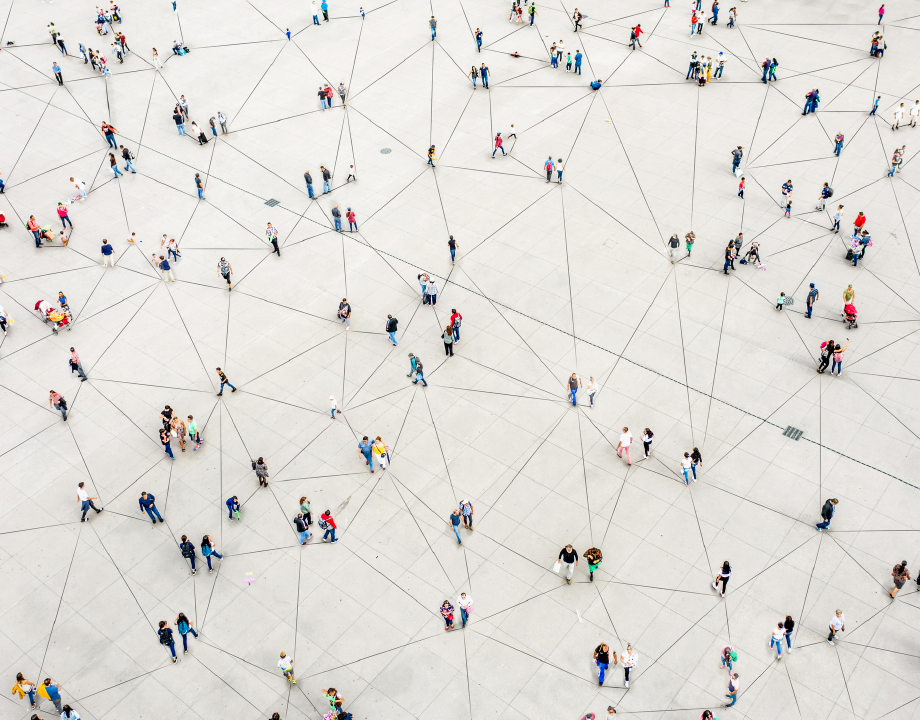
Oregon State’s Onan Demirel talks about the benefits of human factors engineering.
Human factors engineering (HFE) and usability studies during product design almost always improve a product’s performance, but why are these not standard tools that mechanical engineers always use when building new products?
Some engineers feel HFE is an extra step that adds cost to the product and slows down production and time to market, especially for simple, straightforward designs. HFE is sometimes required for regulatory reasons, such as designing medical devices. For other companies, HFE is a cornerstone for a corporate culture focused on quality.
Benefits of HFE include improved product performance and user experience, reduced life cycle costs, safer products, reduced risk and liability, fewer product returns, and stronger brand value and recognition in the marketplace.
Editor's Pick: Five Key Trends in Industrial Connectivity
Despite these benefits, HFE is still not embraced by many mechanical engineers. ASME.org recently discussed the role of HFE in manufacturing with Onan Demirel, an assistant professor at the School of Mechanical, Industrial, and Manufacturing Engineering at Oregon State University in Corvallis, and an HFE expert.
Q1: What do mechanical engineers misunderstand about HFE and its value to product design?
Onan Demirel: There are many reasons why MEs misunderstand or do not understand/apply HFE, but extra cost or time is not the biggest problem. The impacts of market loss due to not considering user interactions, or the compensations associated with injuries due to poor product and process design, are so overwhelming that it is virtually impossible for any engineering firm to ignore human aspects within product design as a high-level goal. However, how one injects HFE throughout the design process, from a high-level goal to an actual design task or implementation, is still problematic for many mechanical engineers because their understanding of HFE design methods is limited.
Q2: What are the roadblocks in understanding HFE design?
O.D: In the past, many MEs tended to think that it was especially challenging to represent human abilities, limitations, and needs systematically within the design process, computationally, since human physiology and psychology are not as predictable or easily modeled as other system components. This school of thought has been slowly disappearing due to advancements in computational HFE tools. However, many MEs still do not get enough exposure to HFE theory and practice, as well as computational ergonomics, primarily due to the lack of HFE-based design courses and a limited number of ME faculty also HFE experts.
Furthermore, conventional design techniques that focus on incorporating HFE principles mostly lack the computational approach, often existing in the form of guidelines or checklists, and do not allow engineers to keep the user’s needs and abilities in the loop. Computational methodologies that can incorporate HFE principles early in design processes are still limited compared to other ME tools such as finite element modeling. As a result, many MEs think of HFE as a cumbersome additional step that must be applied as a check gate or as a post-processing method, that is not part of the core product design activities.
Q3: Why not conduct HFE for every project, if it makes for a better and safer product?
O.D: I can break down the fundamental problems into three categories, where each group addresses a specific HFE-related issue.
1. Poor human factors communication between product designers. In the context of product design, engineers and industrial designers focus on the human element with a mutual interest, but often within a compartmentalized or an isolated environment. Each domain has its field of interest in safety, reliability, and usability attributes of the design process. However, there is a gap between two worlds due to curricular development and field practice, even though the human element is a common interest.
2. Inadequate human factors practice in the product design process. Often, designers consider HFE principles toward the late stages of product design as a post-evaluation method. Not enough fundamental interest is paid to HFE principles, compared to mechanical engineering or software programming. Also, it is still not common to see HFE experts at the core of the design team, who have direct input to design decisions.
3. Lack of human factors awareness in systems engineering. Although systems theory shares a great interest with human well-being and overall system performance, understanding and practicing the HFE design principles within systems engineering has not fully realized. Inside the systems engineering cycle, HFE methods are mostly treated as checkpoints or evaluation steps, rather than core design guidelines. Since the main objective of HFE is to consider the needs, abilities, and limitations of humans, then, systems principles should be integrated early in the design cycle.
Reader's Choice: We Need to Be Real about AM’s Limitations
Q4: How has HFE advanced in recent years?
O.D: Today, computational HFE tools enable engineers to inject ergonomics and check human factors issues early in design. One of the key developments in recent years is digital human modeling (DHM). The theoretical research work in DHM has only become part of the modern computer-aided engineering (CAE) tools in the last 20 to 25 years and has not matured enough to be a mainstream HFE design tool. DHM refers to the development of simulation and analysis techniques and technology integration to create 2D/3D representations of humans, often regarded as computational "mannequins or manikins," within a computer simulation or virtual environment (VE) to facilitate the prediction of safety and comfort.
Complex functions of humans, both physical and cognitive aspects, can now be digitally represented, simulated, and analyzed through DHM tools. These tools, integrated with CAE software, bring the opportunities to represent realistic humans, running "what-if" simulations, and generate digital prototypes before building physical mock-ups and committing resources. This allows the discovery of unseen ergonomics issues and minimizes human factors discrepancies before launching products.
Q5: What do MEs tend to find the most interesting in computational HFE?
O.D: DHM is quite popular. This software technology represents the human size, body proportions, and some of the musculoskeletal and cognitive attributes via biomechanics and ergonomics assessment modules within a CAE or VE platform. For example, one can evaluate the differences between the reach envelopes of a fifth-percentile U.S. male/female and a ninety-fifth-percentile U.S. male/female pilot for a concept cockpit design, computationally. Thus, the DHM-based design approach enables engineers to execute “what-if” scenarios and evaluate concept variants for users from different anthropometric backgrounds without constructing expensive physical prototypes and calling human subjects for data collection. A flexible computational tool that allows generating design exploration is particularly important during the early design, where design decisions are shifting rapidly. Also, designing with DHM is particularly advantageous in evaluating hazardous environments (for example, fire simulation), experiments involve high-risk of injury (crash-testing), or design of assets where physical prototyping is limited and costly (submarine design).
More for You: Bioengineering Blog: Computational Modeling’s Place in Medical Device Testing
Q6: Any final advice for MEs about how to use HFE in their work?
O.D: Considering human needs, abilities, and limitations during the early stages of product design with a system lens will reduce design iterations, lead-time to market, and development costs.
Throughout history, humans, both as individuals and societies, have made progress through design. Unimagined breakthroughs have been attained largely by how we translate scientific discoveries to advancements in engineering through designing products, processes, and environments. Today, sustaining a modern society would be unimaginable without the activity of design. Therefore, good design practices are vital for prosperity since they directly impact our safety, well-being, and quality of life.
We, humans, are at the heart of the design activities both as creators (designers, makers), users (stakeholders, end users), and caregivers (maintenance, recycle). The world is more crowded and resource-limited than ever before, which challenges the efficacy of current engineering methodologies. Economic, socio-political, and ecological considerations will impact human prosperity. Our grand challenges are dynamic, fast-evolving, and cross-disciplinary—it is almost impossible to think MEs who lack HFE theory and practice can provide solutions to such human-centric problems.
Mark Crawford is an independent writer in Corrales, N.M.
Some engineers feel HFE is an extra step that adds cost to the product and slows down production and time to market, especially for simple, straightforward designs. HFE is sometimes required for regulatory reasons, such as designing medical devices. For other companies, HFE is a cornerstone for a corporate culture focused on quality.
Benefits of HFE include improved product performance and user experience, reduced life cycle costs, safer products, reduced risk and liability, fewer product returns, and stronger brand value and recognition in the marketplace.
Editor's Pick: Five Key Trends in Industrial Connectivity
Despite these benefits, HFE is still not embraced by many mechanical engineers. ASME.org recently discussed the role of HFE in manufacturing with Onan Demirel, an assistant professor at the School of Mechanical, Industrial, and Manufacturing Engineering at Oregon State University in Corvallis, and an HFE expert.
Q1: What do mechanical engineers misunderstand about HFE and its value to product design?
Onan Demirel: There are many reasons why MEs misunderstand or do not understand/apply HFE, but extra cost or time is not the biggest problem. The impacts of market loss due to not considering user interactions, or the compensations associated with injuries due to poor product and process design, are so overwhelming that it is virtually impossible for any engineering firm to ignore human aspects within product design as a high-level goal. However, how one injects HFE throughout the design process, from a high-level goal to an actual design task or implementation, is still problematic for many mechanical engineers because their understanding of HFE design methods is limited.
Q2: What are the roadblocks in understanding HFE design?
O.D: In the past, many MEs tended to think that it was especially challenging to represent human abilities, limitations, and needs systematically within the design process, computationally, since human physiology and psychology are not as predictable or easily modeled as other system components. This school of thought has been slowly disappearing due to advancements in computational HFE tools. However, many MEs still do not get enough exposure to HFE theory and practice, as well as computational ergonomics, primarily due to the lack of HFE-based design courses and a limited number of ME faculty also HFE experts.
Furthermore, conventional design techniques that focus on incorporating HFE principles mostly lack the computational approach, often existing in the form of guidelines or checklists, and do not allow engineers to keep the user’s needs and abilities in the loop. Computational methodologies that can incorporate HFE principles early in design processes are still limited compared to other ME tools such as finite element modeling. As a result, many MEs think of HFE as a cumbersome additional step that must be applied as a check gate or as a post-processing method, that is not part of the core product design activities.
Q3: Why not conduct HFE for every project, if it makes for a better and safer product?
O.D: I can break down the fundamental problems into three categories, where each group addresses a specific HFE-related issue.
1. Poor human factors communication between product designers. In the context of product design, engineers and industrial designers focus on the human element with a mutual interest, but often within a compartmentalized or an isolated environment. Each domain has its field of interest in safety, reliability, and usability attributes of the design process. However, there is a gap between two worlds due to curricular development and field practice, even though the human element is a common interest.
2. Inadequate human factors practice in the product design process. Often, designers consider HFE principles toward the late stages of product design as a post-evaluation method. Not enough fundamental interest is paid to HFE principles, compared to mechanical engineering or software programming. Also, it is still not common to see HFE experts at the core of the design team, who have direct input to design decisions.
3. Lack of human factors awareness in systems engineering. Although systems theory shares a great interest with human well-being and overall system performance, understanding and practicing the HFE design principles within systems engineering has not fully realized. Inside the systems engineering cycle, HFE methods are mostly treated as checkpoints or evaluation steps, rather than core design guidelines. Since the main objective of HFE is to consider the needs, abilities, and limitations of humans, then, systems principles should be integrated early in the design cycle.
Reader's Choice: We Need to Be Real about AM’s Limitations
Q4: How has HFE advanced in recent years?
O.D: Today, computational HFE tools enable engineers to inject ergonomics and check human factors issues early in design. One of the key developments in recent years is digital human modeling (DHM). The theoretical research work in DHM has only become part of the modern computer-aided engineering (CAE) tools in the last 20 to 25 years and has not matured enough to be a mainstream HFE design tool. DHM refers to the development of simulation and analysis techniques and technology integration to create 2D/3D representations of humans, often regarded as computational "mannequins or manikins," within a computer simulation or virtual environment (VE) to facilitate the prediction of safety and comfort.
Complex functions of humans, both physical and cognitive aspects, can now be digitally represented, simulated, and analyzed through DHM tools. These tools, integrated with CAE software, bring the opportunities to represent realistic humans, running "what-if" simulations, and generate digital prototypes before building physical mock-ups and committing resources. This allows the discovery of unseen ergonomics issues and minimizes human factors discrepancies before launching products.
Q5: What do MEs tend to find the most interesting in computational HFE?
O.D: DHM is quite popular. This software technology represents the human size, body proportions, and some of the musculoskeletal and cognitive attributes via biomechanics and ergonomics assessment modules within a CAE or VE platform. For example, one can evaluate the differences between the reach envelopes of a fifth-percentile U.S. male/female and a ninety-fifth-percentile U.S. male/female pilot for a concept cockpit design, computationally. Thus, the DHM-based design approach enables engineers to execute “what-if” scenarios and evaluate concept variants for users from different anthropometric backgrounds without constructing expensive physical prototypes and calling human subjects for data collection. A flexible computational tool that allows generating design exploration is particularly important during the early design, where design decisions are shifting rapidly. Also, designing with DHM is particularly advantageous in evaluating hazardous environments (for example, fire simulation), experiments involve high-risk of injury (crash-testing), or design of assets where physical prototyping is limited and costly (submarine design).
More for You: Bioengineering Blog: Computational Modeling’s Place in Medical Device Testing
Q6: Any final advice for MEs about how to use HFE in their work?
O.D: Considering human needs, abilities, and limitations during the early stages of product design with a system lens will reduce design iterations, lead-time to market, and development costs.
Throughout history, humans, both as individuals and societies, have made progress through design. Unimagined breakthroughs have been attained largely by how we translate scientific discoveries to advancements in engineering through designing products, processes, and environments. Today, sustaining a modern society would be unimaginable without the activity of design. Therefore, good design practices are vital for prosperity since they directly impact our safety, well-being, and quality of life.
We, humans, are at the heart of the design activities both as creators (designers, makers), users (stakeholders, end users), and caregivers (maintenance, recycle). The world is more crowded and resource-limited than ever before, which challenges the efficacy of current engineering methodologies. Economic, socio-political, and ecological considerations will impact human prosperity. Our grand challenges are dynamic, fast-evolving, and cross-disciplinary—it is almost impossible to think MEs who lack HFE theory and practice can provide solutions to such human-centric problems.
Mark Crawford is an independent writer in Corrales, N.M.