Manufacturing Blog: Rebuilding the Medical Device Supply Chain
Manufacturing Blog: Rebuilding the Medical Device Supply Chain
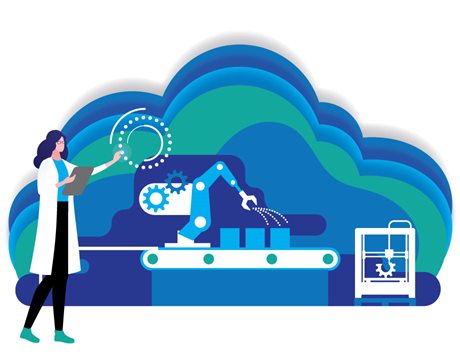
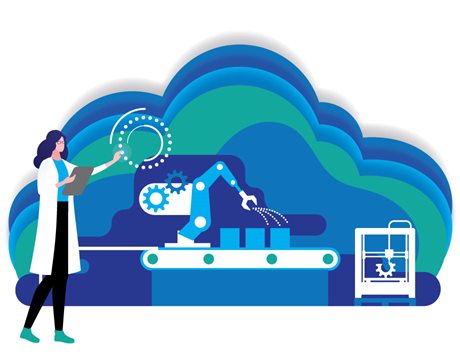
The global supply chain and manufacturing production are a couple examples of mundane, day-to-day issues and processes that most people take for granted, until something happens to throw the system into disarray. That something, of course, is COVID-19, and the pandemic that shut down economies of the major industrial countries. There are plenty of examples of sudden shortages of products, goods and services brought by closures, but the most critical were in healthcare. Hospitals and medical providers suddenly had to deal with shortages of critical goods, from sophisticated medical devices and their parts to basic personal protection equipment. Just like that, everyone rediscovered the supply chain that now was broken.
China and politics again came front and center, and the vulnerabilities of producing so many products in one region were exposed. So what happens now? Some manufacturers are diversifying their supply chains, moving operations to even cheaper hubs in Southeast Asia or Mexico. There is an effort to reshore some work back to the U.S. But a large volume of work will still remain in China.
Editor's Pick: Robotics Blog: Making Robots Ubiquitous Post-Pandemic
“What we have seen, what we think will continue to happen will be a regionalization,” said Terry Haber, managing director of St. Onge, a supply change strategy and logistics firm. Haber is one of three industry representatives who are dealing with the issue and participated in Mechanical Engineering’s sixth webinar on how to move forward after the pandemic, “Rebuilding the Medical Device Supply Chain.” In other words, manufacturers may continue to source parts and product in one region, but expand the number of vendors they use; or continue to work in one country, but find other suppliers in neighboring countries.
Drugs and pharmaceuticals are another key component of the healthcare market, one which has seen much manufacturing concentrated in China and India. B. Frank Gupton is the chair and professor of chemical and life science engineering at Virginia Commonwealth University, and founder of its Medicines for All Institute. Its goal is to improve global access to needed medicine by rethinking manufacturing processes to lower production costs. He recently secured a $354-million grant from the federal government to form a consortium with Phlow Corp. and build a pharmaceutical manufacturing chain in the U.S.
“There's been a migration of pharmaceutical main and manufacturing outside of the U.S. When you start looking at the platforms are being used to produce these drugs, they've the characteristic of having a lot of flexibility and they're using batch manufacturing techniques to be able to produce the active ingredients as well as a formulated products,” he said. “As a result of that, these are very fairly labor-intensive procedures as opposed to a assembly line or continuous type manufacturing operation. That manufacturing element has migrated to countries that have lower labor costs so that they can produce [product] using batch manufacturing and have lower overall cost. What we're looking at doing is applying some basic principles of continuous manufacturing to be able to make these things much more cost-competitive and reduce the labor costs.”
Reader's Choice: Workforce Blog: Engineering the New Workforce after the Pandemic
Many device manufacturers were caught without a supply of raw materials or parts, a product of lean manufacturing philosophy that works on just-in-time delivery. That saves money but can hurt in times of distress when the materials are unavailable.
“We're starting to see a shift of people's thoughts, where they're going, it's nice to have [supply] outside of the U.S. But what do we have also for internal resources because if we don't have that something like that and this happens again, we're going to find ourselves with an even bigger issue,” noted Adam Callahan, XCentric’s northeast sales manager. XCentric supports injection molding in the medical equipment industry with rapid manufacturing and Callahan pointed to clients and customers who had to shut down when raw materials became unavailable.
More for You: Bioengineering Blog: Simulation Does Not Replace Physical Testing
All of these experiences may fuel changes in how manufacturers source and produce their products. Global manufacturing consulting firm Kearney recently released its seventh annual Reshoring Index, and it showed a “dramatic reversal” of a five-year trend: Domestic U.S. manufacturing in 2019 held a significantly greater share versus 14 Asian exporters tracked in the study. Manufacturing imports from China were the hardest hit, and some companies and their Chinese partners were moving manufacturing plants to other southeast Asian countries to avoid tariffs.
Where else could the supply chain move? It depends. India is becoming an alternative and Mexico is finding itself more popular too. But no one is counting out China, at least not yet. The market is huge and the industrial infrastructure is there, even if labor costs may rise.
Watch the full video and tune in to more conversations about the role engineers will play in rebooting our society after the pandemic on go.asme.org/PostCOVED-19.
John Kosowatz is senior editor.
China and politics again came front and center, and the vulnerabilities of producing so many products in one region were exposed. So what happens now? Some manufacturers are diversifying their supply chains, moving operations to even cheaper hubs in Southeast Asia or Mexico. There is an effort to reshore some work back to the U.S. But a large volume of work will still remain in China.
Editor's Pick: Robotics Blog: Making Robots Ubiquitous Post-Pandemic
“What we have seen, what we think will continue to happen will be a regionalization,” said Terry Haber, managing director of St. Onge, a supply change strategy and logistics firm. Haber is one of three industry representatives who are dealing with the issue and participated in Mechanical Engineering’s sixth webinar on how to move forward after the pandemic, “Rebuilding the Medical Device Supply Chain.” In other words, manufacturers may continue to source parts and product in one region, but expand the number of vendors they use; or continue to work in one country, but find other suppliers in neighboring countries.
Drugs and pharmaceuticals are another key component of the healthcare market, one which has seen much manufacturing concentrated in China and India. B. Frank Gupton is the chair and professor of chemical and life science engineering at Virginia Commonwealth University, and founder of its Medicines for All Institute. Its goal is to improve global access to needed medicine by rethinking manufacturing processes to lower production costs. He recently secured a $354-million grant from the federal government to form a consortium with Phlow Corp. and build a pharmaceutical manufacturing chain in the U.S.
“There's been a migration of pharmaceutical main and manufacturing outside of the U.S. When you start looking at the platforms are being used to produce these drugs, they've the characteristic of having a lot of flexibility and they're using batch manufacturing techniques to be able to produce the active ingredients as well as a formulated products,” he said. “As a result of that, these are very fairly labor-intensive procedures as opposed to a assembly line or continuous type manufacturing operation. That manufacturing element has migrated to countries that have lower labor costs so that they can produce [product] using batch manufacturing and have lower overall cost. What we're looking at doing is applying some basic principles of continuous manufacturing to be able to make these things much more cost-competitive and reduce the labor costs.”
Reader's Choice: Workforce Blog: Engineering the New Workforce after the Pandemic
Many device manufacturers were caught without a supply of raw materials or parts, a product of lean manufacturing philosophy that works on just-in-time delivery. That saves money but can hurt in times of distress when the materials are unavailable.
“We're starting to see a shift of people's thoughts, where they're going, it's nice to have [supply] outside of the U.S. But what do we have also for internal resources because if we don't have that something like that and this happens again, we're going to find ourselves with an even bigger issue,” noted Adam Callahan, XCentric’s northeast sales manager. XCentric supports injection molding in the medical equipment industry with rapid manufacturing and Callahan pointed to clients and customers who had to shut down when raw materials became unavailable.
More for You: Bioengineering Blog: Simulation Does Not Replace Physical Testing
All of these experiences may fuel changes in how manufacturers source and produce their products. Global manufacturing consulting firm Kearney recently released its seventh annual Reshoring Index, and it showed a “dramatic reversal” of a five-year trend: Domestic U.S. manufacturing in 2019 held a significantly greater share versus 14 Asian exporters tracked in the study. Manufacturing imports from China were the hardest hit, and some companies and their Chinese partners were moving manufacturing plants to other southeast Asian countries to avoid tariffs.
Where else could the supply chain move? It depends. India is becoming an alternative and Mexico is finding itself more popular too. But no one is counting out China, at least not yet. The market is huge and the industrial infrastructure is there, even if labor costs may rise.
Watch the full video and tune in to more conversations about the role engineers will play in rebooting our society after the pandemic on go.asme.org/PostCOVED-19.
John Kosowatz is senior editor.